Introduction
Printed Circuit Board (PCB) design is a critical aspect of electronics manufacturing. It involves the layout and routing of electronic components on a board to create a functional circuit. However, designing a PCB is not an easy task, and even experienced designers can make mistakes that can lead to costly delays and redesigns. In this article, we will discuss the top 5 mistakes to avoid in PCB design.
Mistake 1: Not Following Design Rules
One of the most common mistakes in PCB design is not following the design rules. Design rules are a set of guidelines that specify the minimum and maximum values for various parameters such as trace width, spacing, and hole size. These rules are put in place to ensure that the PCB can be manufactured reliably and consistently.
Failing to follow these rules can lead to a variety of problems, such as:
- Short circuits
- Open circuits
- Signal integrity issues
- Manufacturing defects
To avoid these issues, it is important to carefully review the design rules provided by the PCB manufacturer and ensure that your design complies with them. Most PCB design software packages have built-in design rule checks (DRC) that can help you identify and fix any violations.
Tips for Following Design Rules
- Review the design rules provided by the PCB manufacturer
- Use PCB design software with built-in DRC
- Double-check your design before sending it for manufacturing
- Consult with the PCB manufacturer if you have any questions or concerns
Mistake 2: Poor Component Placement
Another common mistake in PCB design is poor component placement. The placement of components on the board can have a significant impact on the performance and reliability of the circuit. Poor placement can lead to issues such as:
- Signal integrity problems
- Thermal issues
- Mechanical stress
- Manufacturability issues
To avoid these issues, it is important to carefully consider the placement of each component on the board. Some factors to consider include:
- Signal routing
- Power distribution
- Thermal management
- Mechanical stress
- Manufacturability
Tips for Optimal Component Placement
- Group related components together
- Place sensitive components away from sources of noise and interference
- Consider the thermal requirements of each component
- Minimize the distance between components to reduce signal loss
- Leave enough space for routing and manufacturing
Component Type | Placement Considerations |
---|---|
Power Components | Place near power input and away from sensitive components |
High-Speed Components | Place close to connectors and away from sources of noise |
Analog Components | Place away from digital components and power supply |
Connectors | Place near edge of board for easy access |
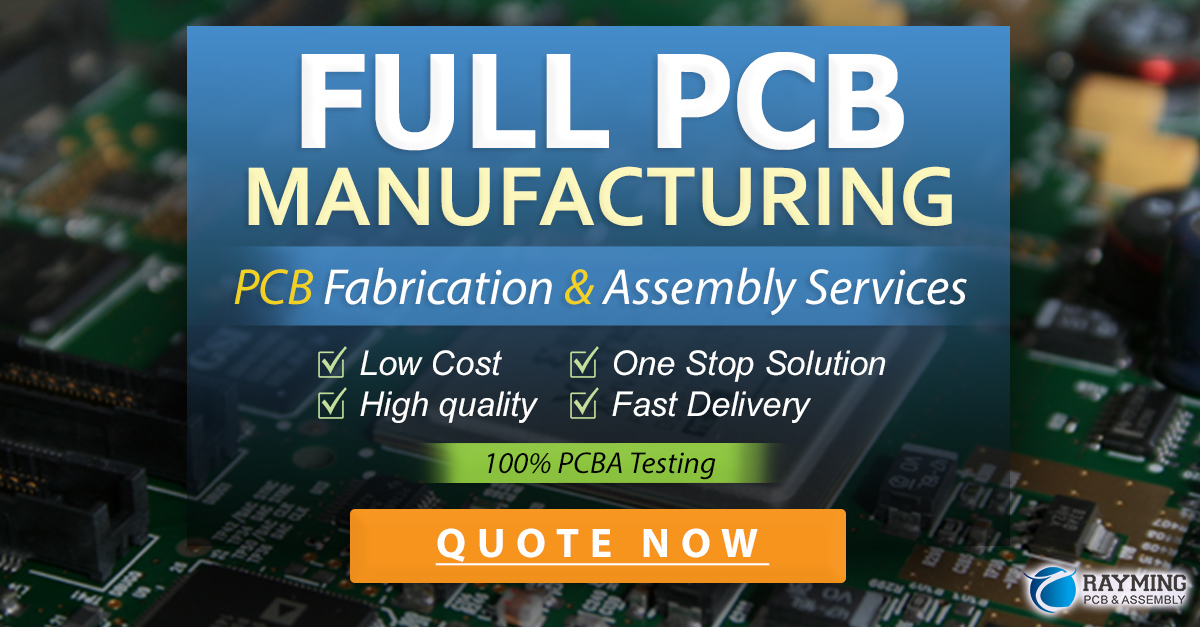
Mistake 3: Incorrect Trace Routing
Trace routing is the process of connecting components on the PCB with conductive traces. Incorrect trace routing can lead to a variety of issues, such as:
- Signal integrity problems
- Crosstalk
- Electromagnetic interference (EMI)
- Manufacturing defects
To avoid these issues, it is important to follow best practices for trace routing. Some tips include:
- Keep traces as short and direct as possible
- Avoid sharp angles and use curved traces instead
- Maintain consistent trace width and spacing
- Use ground planes to reduce EMI and improve signal integrity
- Follow the manufacturer’s guidelines for trace width and spacing
Tips for Optimal Trace Routing
- Use a grid system to keep traces aligned
- Route critical signals first
- Use differential pairs for high-speed signals
- Avoid crossing split planes with signals
- Use vias sparingly and place them carefully
Mistake 4: Forgetting About Manufacturability
Another common mistake in PCB design is forgetting about manufacturability. While it is important to focus on the functionality and performance of the circuit, it is equally important to consider how the board will be manufactured. Failing to consider manufacturability can lead to issues such as:
- Increased manufacturing costs
- Longer lead times
- Lower yields
- Quality issues
To avoid these issues, it is important to design with manufacturability in mind. Some factors to consider include:
- Minimum hole size and spacing
- Minimum trace width and spacing
- Soldermask and silkscreen requirements
- Panelization and routing requirements
- Test point accessibility
Tips for Designing for Manufacturability
- Consult with the PCB manufacturer early in the design process
- Use standard component sizes and packages
- Avoid using non-standard materials or finishes
- Include fiducial marks and tooling holes for alignment
- Use a consistent grid system for component placement and routing
Manufacturing Consideration | Recommendation |
---|---|
Minimum Hole Size | 0.2mm |
Minimum Trace Width/Spacing | 0.1mm |
Soldermask Clearance | 0.05mm |
Silkscreen Width | 0.15mm |
Panelization Spacing | 2mm |
Mistake 5: Not Considering Signal Integrity
Finally, a common mistake in PCB design is not considering signal integrity. Signal integrity refers to the quality of the signals transmitted through the PCB. Poor signal integrity can lead to a variety of issues, such as:
- Distortion
- Attenuation
- Reflections
- Crosstalk
To avoid these issues, it is important to design with signal integrity in mind. Some factors to consider include:
- Impedance matching
- Termination
- Shielding
- Grounding
- Filtering
Tips for Improving Signal Integrity
- Use controlled impedance traces for critical signals
- Terminate long traces to prevent reflections
- Use ground planes to provide shielding and reduce EMI
- Use decoupling capacitors to reduce power supply noise
- Use differential pairs for high-speed signals
Conclusion
PCB design is a complex process that requires careful attention to detail and a thorough understanding of the various factors that can impact the performance and reliability of the circuit. By avoiding these common mistakes and following best practices for PCB design, you can ensure that your board will be manufactured reliably and perform as expected.
FAQ
- What is the most common mistake in PCB design?
-
Not following design rules is one of the most common mistakes in PCB design. Failing to follow these rules can lead to a variety of problems, such as short circuits, open circuits, signal integrity issues, and manufacturing defects.
-
How can I ensure that my PCB design is manufacturable?
-
To ensure that your PCB design is manufacturable, it is important to consult with the PCB manufacturer early in the design process, use standard component sizes and packages, avoid using non-standard materials or finishes, include fiducial marks and tooling holes for alignment, and use a consistent grid system for component placement and routing.
-
What is signal integrity and why is it important in PCB design?
-
Signal integrity refers to the quality of the signals transmitted through the PCB. Poor signal integrity can lead to issues such as distortion, attenuation, reflections, and crosstalk. To ensure good signal integrity, it is important to use controlled impedance traces for critical signals, terminate long traces to prevent reflections, use ground planes to provide shielding and reduce EMI, use decoupling capacitors to reduce power supply noise, and use differential pairs for high-speed signals.
-
What are some tips for optimal component placement on a PCB?
-
Some tips for optimal component placement include grouping related components together, placing sensitive components away from sources of noise and interference, considering the thermal requirements of each component, minimizing the distance between components to reduce signal loss, and leaving enough space for routing and manufacturing.
-
How can I avoid issues with trace routing on my PCB?
- To avoid issues with trace routing, it is important to keep traces as short and direct as possible, avoid sharp angles and use curved traces instead, maintain consistent trace width and spacing, use ground planes to reduce EMI and improve signal integrity, and follow the manufacturer’s guidelines for trace width and spacing. Additionally, using a grid system to keep traces aligned, routing critical signals first, using differential pairs for high-speed signals, avoiding crossing split planes with signals, and using vias sparingly and placing them carefully can help optimize trace routing on your PCB.
Leave a Reply