Introduction to PCB Basics
Printed Circuit Boards (PCBs) are the backbone of modern electronics. They are used in almost every electronic device, from smartphones and computers to industrial equipment and medical devices. PCBs provide a platform for electronic components to be mounted and connected, allowing for the creation of complex circuits in a compact and efficient manner.
In this article, we will cover the basics of PCBs, including their history, types, manufacturing process, design considerations, and more. Whether you are an electronics enthusiast, a student, or a professional, understanding PCB basics is essential for anyone working with electronic devices.
What is a PCB?
A PCB is a flat board made of insulating material, such as fiberglass or plastic, with conductive tracks, pads, and other features etched or printed onto its surface. These conductive elements are typically made of copper and are used to electrically connect various components mounted on the board.
PCBs come in various sizes, shapes, and layers, depending on the complexity of the circuit and the intended application. They can be single-sided (with components and tracks on one side), double-sided (with components and tracks on both sides), or multi-layered (with multiple layers of tracks and insulation).
Advantages of using PCBs
Using PCBs offers several advantages over other methods of circuit construction, such as point-to-point wiring or wire-wrap. Some of the key benefits include:
-
Compact size: PCBs allow for the creation of complex circuits in a small form factor, making them ideal for use in portable devices and space-constrained applications.
-
Reliability: PCBs provide a stable and reliable platform for electronic components, reducing the risk of loose connections or short circuits.
-
Mass production: PCBs can be manufactured in large quantities using automated processes, making them cost-effective for mass production.
-
Consistency: PCBs ensure consistent electrical characteristics across multiple boards, which is essential for maintaining product quality and performance.
History of PCBs
The concept of printed circuits dates back to the early 20th century, with the first patent for a printed wire being filed by Albert Hanson in 1903. However, it wasn’t until the 1940s that PCBs began to gain widespread adoption.
Key milestones in PCB History
Year | Milestone |
---|---|
1936 | Paul Eisler develops the first printed circuit board for a radio set |
1943 | The U.S. military begins using PCBs in proximity fuzes during World War II |
1948 | The U.S. Bureau of Engraving and Printing begins using PCBs for currency production |
1950s | PCBs become widely adopted in consumer electronics, such as radios and televisions |
1960s | Multi-layer PCBs are developed, enabling more complex circuit designs |
1980s | Surface-mount technology (SMT) becomes popular, allowing for smaller and more densely packed PCBs |
1990s | High-density interconnect (HDI) PCBs are introduced, enabling even greater circuit density and complexity |
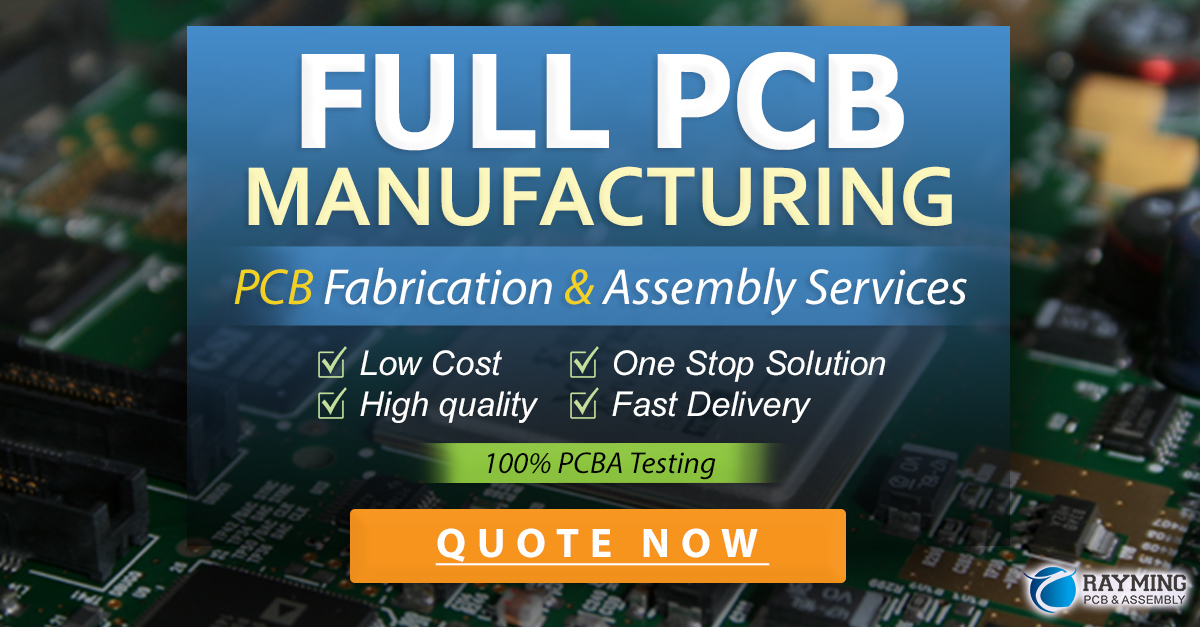
Types of PCBs
There are several types of PCBs, each with its own characteristics and applications. Some of the most common types include:
Single-sided PCBs
Single-sided PCBs have components and conductive tracks on one side of the board. They are the simplest and most cost-effective type of PCB but are limited in terms of circuit complexity and density.
Double-sided PCBs
Double-sided PCBs have components and tracks on both sides of the board, with conductive vias connecting the two sides. They offer greater circuit density and complexity than single-sided PCBs but are more expensive to manufacture.
Multi-layer PCBs
Multi-layer PCBs consist of multiple layers of conductive tracks and insulation, with vias connecting the layers. They offer the highest level of circuit density and complexity but are also the most expensive to manufacture. Multi-layer PCBs are commonly used in high-performance applications, such as smartphones, computers, and aerospace systems.
Flexible PCBs
Flexible PCBs are made of flexible insulating material, such as polyimide, with conductive tracks printed or etched onto the surface. They are designed to bend and flex, making them ideal for applications where the PCB needs to conform to a specific shape or withstand repeated bending.
Rigid-Flex PCBs
Rigid-flex PCBs combine the benefits of both rigid and flexible PCBs. They consist of rigid PCB sections connected by flexible PCB sections, allowing for greater design flexibility and improved reliability in applications where the PCB is subject to mechanical stress or vibration.
PCB Manufacturing Process
The PCB manufacturing process involves several steps, each of which is critical to ensuring the quality and reliability of the final product. The main steps in the PCB manufacturing process are:
-
PCB Design: The PCB design is created using electronic design automation (EDA) software, which generates the necessary files for manufacturing, such as Gerber files and drill files.
-
PCB Fabrication: The PCB fabrication process begins with the creation of a copper-clad laminate, which is then drilled and plated to create the conductive vias. The outer layers of the PCB are then patterned and etched to create the conductive tracks and pads.
-
Solder Mask Application: A solder mask is applied to the PCB to protect the conductive tracks and prevent short circuits during the soldering process.
-
Silkscreen Printing: A silkscreen layer is printed onto the PCB to provide labels, logos, and other identifying information.
-
Surface Finish Application: A surface finish, such as HASL (Hot Air Solder Leveling), ENIG (Electroless Nickel Immersion Gold), or OSP (Organic Solderability Preservative), is applied to the PCB to protect the exposed copper and improve solderability.
-
PCB Assembly: The electronic components are mounted onto the PCB using either through-hole or surface-mount technology (SMT). The components are then soldered to the PCB using wave soldering, reflow soldering, or hand soldering.
-
Testing and Inspection: The assembled PCB is tested and inspected to ensure that it meets the required specifications and functions as intended. This may involve visual inspection, automated optical inspection (AOI), in-circuit testing (ICT), or functional testing.
PCB Design Considerations
Designing a PCB requires careful consideration of several factors to ensure optimal performance, reliability, and manufacturability. Some of the key design considerations include:
Component placement
The placement of components on the PCB should be optimized for signal integrity, thermal management, and manufacturing efficiency. Components should be placed to minimize the length of critical signal paths and to ensure adequate spacing for heat dissipation and soldering.
Signal integrity
Signal integrity refers to the quality of the electrical signals transmitted through the PCB. It is affected by factors such as trace width, trace spacing, dielectric constant of the PCB material, and the presence of ground and power planes. Proper signal integrity design is essential for ensuring reliable operation and minimizing electromagnetic interference (EMI).
Power distribution
A well-designed power distribution network is critical for ensuring stable and reliable power delivery to all components on the PCB. This involves the use of appropriate trace widths, via sizes, and the placement of decoupling capacitors to minimize voltage droops and transients.
Thermal management
Proper thermal management is essential for ensuring the long-term reliability and performance of the PCB and its components. This may involve the use of thermal vias, heatsinks, and other cooling methods to dissipate heat generated by components.
Manufacturability
PCB design should also consider manufacturability, including factors such as minimum trace widths, minimum drill sizes, and the use of standard component footprints. Designing for manufacturability helps to ensure that the PCB can be produced efficiently and cost-effectively.
PCB Testing and Inspection
Testing and inspection are critical steps in the PCB manufacturing process, ensuring that the final product meets the required quality and performance standards. Some of the common testing and inspection methods include:
Visual inspection
Visual inspection involves the use of the human eye or automated optical inspection (AOI) systems to check for defects such as missing components, solder bridges, or incorrect component placement.
In-circuit testing (ICT)
ICT involves the use of specialized test fixtures to verify the electrical connectivity and functionality of individual components on the PCB. This helps to identify defects such as open circuits, short circuits, or incorrect component values.
Functional testing
Functional testing involves testing the PCB under real-world operating conditions to ensure that it performs as intended. This may involve the use of specialized test equipment or software to simulate the PCB’s intended application.
Boundary scan testing
Boundary scan testing, also known as JTAG testing, involves the use of a special test access port (TAP) to test the interconnections between components on the PCB. This helps to identify defects such as open circuits, short circuits, or stuck-at faults.
PCB Industry Trends and Future Developments
The PCB industry is constantly evolving, driven by advances in technology and changing market demands. Some of the key trends and future developments in the PCB industry include:
Miniaturization
The trend towards miniaturization continues, with smaller and more complex PCBs being developed to meet the demands of increasingly compact and portable electronic devices.
High-speed designs
As data rates and signal frequencies continue to increase, PCB designers are faced with the challenge of maintaining signal integrity and minimizing EMI in high-speed designs.
Advanced materials
New PCB materials, such as low-loss dielectrics and high-thermal conductivity substrates, are being developed to meet the demands of high-performance applications.
Embedded components
The use of embedded components, such as resistors, capacitors, and inductors, is becoming more common as a way to reduce PCB Size and improve performance.
3D printing
3D printing technology is being explored as a potential method for rapid prototyping and low-volume production of PCBs.
Frequently Asked Questions (FAQ)
- What is the difference between a PCB and a PCBA?
-
A PCB (Printed Circuit Board) is the bare board without any components mounted on it, while a PCBA (Printed Circuit Board Assembly) is a PCB with all the necessary components soldered onto it, ready for use in an electronic device.
-
What are the most common PCB materials?
-
The most common PCB materials are FR-4 (a type of fiberglass), polyimide (for flexible PCBs), and high-frequency laminates (such as Rogers or Isola materials) for high-speed and RF applications.
-
What is the difference between through-hole and surface-mount components?
-
Through-hole components have leads that are inserted into holes drilled in the PCB and soldered on the opposite side, while surface-mount components are soldered directly onto pads on the surface of the PCB. Surface-mount components are generally smaller and better suited for high-density designs.
-
What is the purpose of a solder mask on a PCB?
-
A solder mask is a protective layer applied to the PCB that covers the copper traces and pads, leaving only the areas to be soldered exposed. It helps to prevent short circuits, protects the copper from oxidation, and provides electrical insulation.
-
What is the typical turnaround time for PCB manufacturing?
- The turnaround time for PCB manufacturing varies depending on the complexity of the design, the PCB manufacturer, and the order quantity. For standard PCBs, the turnaround time can range from a few days to a few weeks. Rush services are often available for an additional cost, providing faster turnaround times.
Conclusion
PCBs are essential components in modern electronics, providing a reliable and efficient platform for circuit construction. Understanding PCB basics, including their types, manufacturing process, design considerations, and testing methods, is crucial for anyone working with electronic devices.
As technology continues to advance, the PCB industry will face new challenges and opportunities, driven by trends such as miniaturization, high-speed designs, advanced materials, embedded components, and 3D printing. By staying informed about these developments and adhering to best practices in PCB design and manufacturing, engineers and manufacturers can create PCBs that meet the ever-increasing demands of the electronics industry.
Leave a Reply