Introduction to PCBs
Printed Circuit Boards (PCBs) are the backbone of modern electronics. They provide a platform for electronic components to be mounted and interconnected, enabling the creation of complex electronic devices. PCBs come in various types, each with its own unique characteristics and applications. Two of the most common types of PCBs are Rigid PCBs and Flex PCBs. In this article, we will explore the differences between these two types of PCBs, their advantages and disadvantages, and their applications.
What is a Rigid PCB?
A Rigid PCB is a type of printed circuit board that is made from a solid, non-flexible material, typically a glass-reinforced epoxy laminate. The board is composed of multiple layers of copper foil separated by insulating layers, with each layer interconnected through drilled holes known as vias. Rigid PCBs are the most common type of PCB and are used in a wide range of electronic devices, from consumer electronics to industrial equipment.
Advantages of Rigid PCBs
-
Durability: Rigid PCBs are made from sturdy materials that can withstand harsh environments and physical stress, making them ideal for applications that require a high level of reliability.
-
Cost-effective: Due to their widespread use and standardized manufacturing processes, Rigid PCBs are generally more cost-effective than other types of PCBs, especially for high-volume production.
-
Excellent thermal management: The solid structure of Rigid PCBs allows for efficient heat dissipation, which is crucial for electronic components that generate a significant amount of heat.
-
Ease of assembly: Rigid PCBs provide a stable platform for surface-mount and through-hole components, simplifying the assembly process and reducing the risk of errors.
Disadvantages of Rigid PCBs
-
Limited flexibility: As the name suggests, Rigid PCBs are not flexible, which can limit their use in applications that require the board to conform to irregular shapes or withstand repeated bending.
-
Larger size and weight: Compared to Flex PCBs, Rigid PCBs are generally thicker and heavier, which can be a drawback in space-constrained or weight-sensitive applications.
-
Reduced design freedom: The rigid nature of these PCBs can restrict the placement of components and the routing of traces, potentially leading to larger board sizes or increased layer counts.
What is a Flex PCB?
A Flex PCB, also known as a Flexible PCB, is a type of printed circuit board that is made from a thin, flexible substrate, typically a polyimide film. Like Rigid PCBs, Flex PCBs are composed of conductive traces and insulating layers, but the flexible substrate allows the board to bend, twist, and conform to various shapes. Flex PCBs are increasingly popular in applications that require compact, lightweight, and flexible electronic assemblies.
Advantages of Flex PCBs
-
Flexibility: The most significant advantage of Flex PCBs is their ability to bend and flex without damaging the circuitry, enabling their use in applications that require conformity to irregular shapes or repeated bending.
-
Compact and lightweight: Flex PCBs are thinner and lighter than Rigid PCBs, making them ideal for space-constrained and weight-sensitive applications, such as wearable devices and aerospace systems.
-
Increased reliability: By eliminating the need for connectors and cables between multiple Rigid PCBs, Flex PCBs can improve the overall reliability of the electronic assembly by reducing the number of potential failure points.
-
Enhanced design freedom: The flexible nature of Flex PCBs allows for greater freedom in component placement and trace routing, enabling more compact and efficient designs.
Disadvantages of Flex PCBs
-
Higher cost: Due to the specialized materials and manufacturing processes involved, Flex PCBs are generally more expensive than Rigid PCBs, especially for low-volume production.
-
Limited power handling: The thin and flexible nature of Flex PCBs can limit their ability to handle high power levels, as the reduced copper thickness can lead to increased current density and heat generation.
-
Challenging assembly: The flexibility of Flex PCBs can make the assembly process more challenging, as the board may require specialized fixtures or techniques to ensure proper component placement and soldering.
-
Reduced thermal management: The thin and flexible structure of Flex PCBs can hinder efficient heat dissipation, which may be a concern for applications with high-power components.
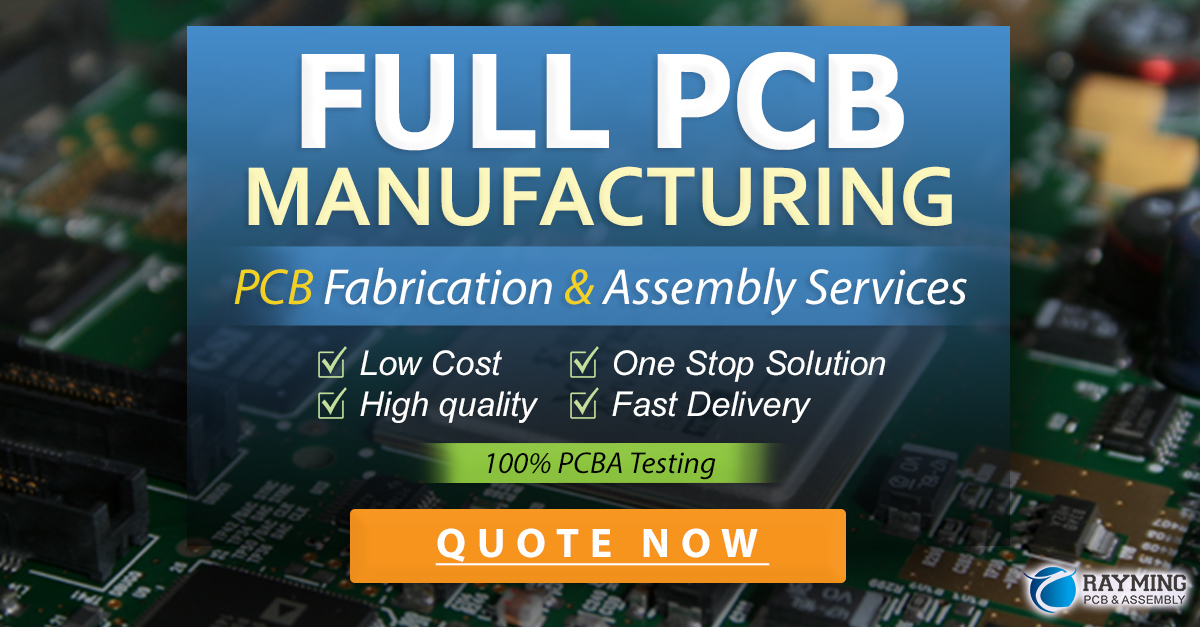
What is a Rigid-Flex PCB?
A Rigid-Flex PCB is a hybrid PCB that combines the benefits of both Rigid and Flex PCBs. It consists of one or more rigid sections connected by flexible sections, allowing the board to be folded or bent into a desired shape. Rigid-Flex PCBs offer the best of both worlds, providing the stability and durability of Rigid PCBs in areas that require it, while also offering the flexibility and conformity of Flex PCBs where needed.
Advantages of Rigid-Flex PCBs
-
Space savings: By combining multiple Rigid PCBs and the interconnects between them into a single Rigid-Flex PCB, designers can significantly reduce the overall size and weight of the electronic assembly.
-
Increased reliability: Rigid-Flex PCBs eliminate the need for connectors and cables between rigid sections, reducing the number of potential failure points and improving overall system reliability.
-
Enhanced design flexibility: The combination of rigid and flexible sections allows for greater design freedom, enabling the creation of complex, three-dimensional electronic assemblies that would be difficult or impossible to achieve with Rigid PCBs alone.
-
Improved signal integrity: By reducing the number of interconnects and keeping signal traces on a single board, Rigid-Flex PCBs can minimize signal degradation and improve overall signal integrity.
Disadvantages of Rigid-Flex PCBs
-
High cost: Rigid-Flex PCBs are typically the most expensive type of PCB, due to the specialized materials, design considerations, and manufacturing processes involved.
-
Complex design and manufacturing: Designing and manufacturing Rigid-Flex PCBs requires specialized expertise and tools, as the combination of rigid and flexible sections introduces unique challenges in terms of material selection, layer stackup, and mechanical stress management.
-
Longer lead times: Due to the complexity of the design and manufacturing process, Rigid-Flex PCBs often have longer lead times compared to Rigid or Flex PCBs.
Applications of Rigid, Flex, and Rigid-Flex PCBs
Rigid PCB Applications
- Consumer electronics (e.g., smartphones, tablets, laptops)
- Industrial equipment (e.g., process control systems, automation machinery)
- Medical devices (e.g., diagnostic equipment, patient monitoring systems)
- Automotive electronics (e.g., engine control units, infotainment systems)
Flex PCB Applications
- Wearable devices (e.g., smartwatches, fitness trackers)
- Medical implants (e.g., pacemakers, hearing aids)
- Aerospace and military systems (e.g., satellites, unmanned aerial vehicles)
- Automotive electronics (e.g., dashboard displays, sensor modules)
Rigid-Flex PCB Applications
- Aerospace and military systems (e.g., avionics, missile guidance systems)
- Medical devices (e.g., endoscopes, surgical instruments)
- Industrial robotics and automation
- High-end consumer electronics (e.g., VR/AR headsets, gaming devices)
Comparison Table: Rigid PCB vs. Flex PCB vs. Rigid-Flex PCB
Feature | Rigid PCB | Flex PCB | Rigid-Flex PCB |
---|---|---|---|
Flexibility | No | Yes | Partial |
Durability | High | Moderate | High |
Cost | Low to Moderate | Moderate to High | High |
Size and Weight | Larger and heavier | Compact and lightweight | Compact and lightweight |
Design Freedom | Limited | High | High |
Thermal Management | Excellent | Limited | Good |
Assembly Complexity | Low | Moderate | High |
Reliability | High | Moderate to High | High |
Typical Applications | Consumer electronics, industrial equipment, medical devices | Wearable devices, medical implants, aerospace systems | Aerospace systems, medical devices, industrial robotics |
Frequently Asked Questions (FAQ)
-
Q: Can Flex PCBs be used in high-temperature environments?
A: Flex PCBs can be designed to withstand high temperatures by using specialized materials, such as polyimide films with high glass transition temperatures. However, the maximum operating temperature will depend on the specific materials used and the design of the PCB. -
Q: Are Rigid-Flex PCBs more durable than Flex PCBs?
A: Yes, Rigid-Flex PCBs are generally more durable than Flex PCBs, as the rigid sections provide additional support and protection for the flexible sections. The rigid sections also help to distribute mechanical stress more evenly, reducing the risk of damage to the flexible portions of the board. -
Q: Can Rigid PCBs be used in applications that require bending or flexing?
A: While Rigid PCBs are not designed to bend or flex, they can be used in applications that require a small amount of bending or flexing by using thinner boards or by incorporating strain relief features. However, for applications that require significant or repeated bending, Flex PCBs or Rigid-Flex PCBs are more suitable. -
Q: How do the costs of Rigid, Flex, and Rigid-Flex PCBs compare?
A: In general, Rigid PCBs are the most cost-effective, followed by Flex PCBs, with Rigid-Flex PCBs being the most expensive. The cost difference is primarily due to the specialized materials, design considerations, and manufacturing processes required for Flex and Rigid-Flex PCBs. -
Q: Can Rigid-Flex PCBs be repaired if damaged?
A: Repairing Rigid-Flex PCBs can be challenging due to their complex structure and the use of specialized materials. In many cases, it may be more cost-effective to replace the entire board rather than attempting a repair. However, minor repairs, such as replacing damaged components or repairing broken traces, may be possible depending on the extent of the damage and the accessibility of the affected area.
Conclusion
Rigid PCBs and Flex PCBs are two distinct types of printed circuit boards, each with its own unique characteristics, advantages, and disadvantages. Rigid PCBs offer durability, cost-effectiveness, and excellent thermal management, making them suitable for a wide range of applications. Flex PCBs, on the other hand, provide flexibility, compact size, and enhanced design freedom, making them ideal for applications that require conformity or space savings.
Rigid-Flex PCBs combine the benefits of both Rigid and Flex PCBs, offering a hybrid solution that provides the stability and durability of Rigid PCBs while also incorporating the flexibility and conformity of Flex PCBs. Although Rigid-Flex PCBs are more expensive and complex to design and manufacture, they enable the creation of highly integrated, reliable, and space-efficient electronic assemblies.
When choosing between Rigid, Flex, and Rigid-Flex PCBs, designers must consider factors such as the application requirements, operating environment, space constraints, and budget. By understanding the differences between these PCB Types and their respective advantages and disadvantages, designers can make informed decisions and select the most appropriate PCB technology for their specific needs.
Leave a Reply