Introduction to Flexible PCBs
Flexible PCBs, also known as flex circuits, have gained significant popularity in recent years due to their versatility and ability to conform to various shapes and sizes. These circuits are made from flexible materials, such as polyimide or polyester, which allow them to bend, twist, and fold without breaking or losing their electrical properties. Flexible PCBs have opened up new opportunities in various industries, including consumer electronics, medical devices, automotive, aerospace, and wearable technology.
Advantages of Flexible PCBs
- Space-saving design: Flexible PCBs can be bent and folded to fit into tight spaces, reducing the overall size and weight of electronic devices.
- Increased reliability: The flexible nature of these circuits allows them to withstand stress, vibration, and shock better than rigid PCBs.
- Improved signal integrity: Flexible PCBs can be designed with shorter signal paths, reducing electromagnetic interference (EMI) and signal loss.
- Enhanced thermal management: The thin profile of flexible PCBs allows for better heat dissipation, preventing overheating and improving device performance.
- Cost-effective: Flexible PCBs can reduce the number of connectors and cables needed, lowering manufacturing costs and simplifying assembly processes.
Opportunities in Flexible PCB Applications
Wearable Technology
Flexible PCBs have become essential components in wearable technology, such as smartwatches, fitness trackers, and medical monitoring devices. These circuits enable the creation of lightweight, comfortable, and ergonomic devices that can conform to the human body.
Medical Devices
The medical industry has embraced flexible PCBs for their ability to integrate into various devices, such as hearing aids, pacemakers, and implantable sensors. Flex circuits offer the necessary flexibility and biocompatibility required for medical applications.
Automotive Electronics
As vehicles become more advanced and connected, flexible PCBs play a crucial role in integrating electronics into limited spaces. Flex circuits are used in applications such as dashboard displays, lighting systems, and sensor networks, improving reliability and reducing weight.
Consumer Electronics
Flexible PCBs have enabled the development of thinner, lighter, and more compact consumer electronics, such as smartphones, tablets, and laptops. These circuits allow for innovative designs and improved user experiences.
Challenges in Flexible PCB Design and Manufacturing
Material Selection
Choosing the right materials for flexible PCBs is critical to ensure the desired flexibility, durability, and electrical performance. Designers must consider factors such as the dielectric constant, thermal stability, and chemical resistance of the materials.
Mechanical Stress
Flexible PCBs are subjected to various types of mechanical stress, such as bending, twisting, and stretching. Designers must account for these stresses and incorporate appropriate reinforcement techniques to prevent damage and ensure long-term reliability.
Signal Integrity
Maintaining signal integrity in flexible PCBs can be challenging due to the dynamic nature of the circuits. Designers must carefully consider factors such as impedance matching, crosstalk, and EMI to ensure proper signal transmission and minimize signal loss.
Manufacturing Processes
Manufacturing flexible PCBs requires specialized equipment and processes compared to rigid PCBs. Challenges include ensuring proper alignment of layers, controlling the application of adhesives, and managing the curing process to achieve the desired flexibility and reliability.
Testing and Qualification
Testing and qualifying flexible PCBs can be more complex than rigid PCBs due to their dynamic nature. Designers must develop appropriate test methods and qualification procedures to ensure the circuits meet the required performance and reliability standards.
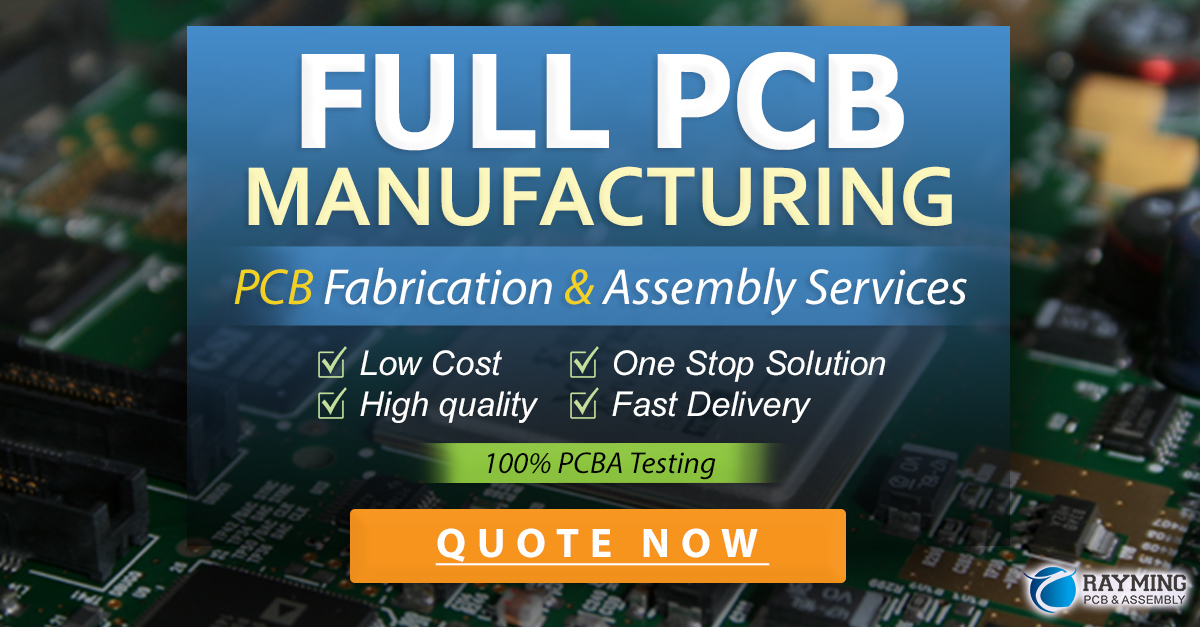
Best Practices for Flexible PCB Design
Use Appropriate Layer Stackup
Designing the appropriate layer stackup is crucial for achieving the desired flexibility and electrical performance. Designers should consider factors such as the number of layers, layer thickness, and the placement of components and traces.
Incorporate Strain Relief Features
Incorporating strain relief features, such as curved traces, tear drops, and stiffeners, can help minimize mechanical stress and improve the reliability of flexible PCBs. These features distribute stress evenly and prevent damage to the circuits.
Optimize Trace Routing
Optimizing trace routing is essential for maintaining signal integrity and reducing EMI. Designers should follow guidelines such as keeping trace lengths as short as possible, using appropriate trace widths and spacing, and avoiding sharp corners or angles.
Consider Component Placement
Component placement on flexible PCBs requires careful consideration to ensure proper functionality and reliability. Designers should place components in areas with minimal bending or flexing and use appropriate mounting techniques, such as adhesives or mechanical fasteners.
Collaborate with Manufacturers
Collaborating closely with flexible PCB manufacturers is essential for ensuring the successful production of the circuits. Designers should communicate their requirements clearly, provide detailed documentation, and work with manufacturers to optimize the design for manufacturability.
Future Trends in Flexible PCBs
Increased Adoption in IoT Devices
As the Internet of Things (IoT) continues to grow, flexible PCBs will play a crucial role in enabling the development of compact, lightweight, and connected devices. Flex circuits will be essential for integrating sensors, antennas, and other components into various IoT applications.
Advancements in Materials and Manufacturing
Ongoing research and development in materials science and manufacturing technologies will drive further advancements in flexible PCBs. New materials with improved flexibility, thermal stability, and electrical properties will enable the creation of more advanced and reliable flex circuits.
Integration with Printed Electronics
The integration of flexible PCBs with printed electronics technologies, such as conductive inks and organic semiconductors, will open up new possibilities for creating low-cost, lightweight, and disposable electronic devices. This combination will enable the development of novel applications in areas such as smart packaging, wearable sensors, and medical diagnostics.
Frequently Asked Questions (FAQ)
-
Q: What are the main advantages of using flexible PCBs over rigid PCBs?
A: Flexible PCBs offer several advantages, including space-saving design, increased reliability, improved signal integrity, enhanced thermal management, and cost-effectiveness. -
Q: What industries commonly use flexible PCBs?
A: Flexible PCBs are used in various industries, such as consumer electronics, medical devices, automotive, aerospace, and wearable technology. -
Q: What are the key challenges in designing and manufacturing flexible PCBs?
A: The main challenges include material selection, managing mechanical stress, maintaining signal integrity, specialized manufacturing processes, and complex testing and qualification procedures. -
Q: How can designers optimize flexible PCB designs for reliability?
A: Designers can optimize flexible PCB designs by using appropriate layer stackups, incorporating strain relief features, optimizing trace routing, considering component placement, and collaborating closely with manufacturers. -
Q: What are some future trends in flexible PCBs?
A: Future trends in flexible PCBs include increased adoption in IoT devices, advancements in materials and manufacturing technologies, and integration with printed electronics.
Conclusion
Flexible PCBs have revolutionized the electronics industry by enabling the development of compact, lightweight, and reliable devices across various sectors. While designing and manufacturing flexible PCBs present unique challenges, adopting best practices and staying informed about the latest trends and technologies can help designers and manufacturers capitalize on the opportunities offered by these versatile circuits. As the demand for flexible and wearable electronics continues to grow, flexible PCBs will play an increasingly vital role in shaping the future of the electronics industry.
Leave a Reply