Introduction to MOSFETs and the Need for Protection
Metal-Oxide-Semiconductor Field-Effect Transistors, or MOSFETs, are widely used semiconductor devices that have revolutionized the electronics industry. They are essential components in various applications, ranging from power electronics to high-frequency circuits. However, despite their numerous advantages, MOSFETs are susceptible to damage caused by electrical overstress (EOS) and electrostatic discharge (ESD). To ensure the reliable operation and longevity of MOSFETs, it is crucial to implement proper protection techniques.
In this comprehensive article, we will delve into the world of MOSFET Protection, exploring the various methods and best practices for safeguarding these critical devices. We will discuss the common causes of MOSFET failure, the importance of ESD and EOS protection, and the different protection circuits and techniques available. By the end of this article, you will have a solid understanding of how to effectively protect MOSFETs in your designs, ensuring optimal performance and reliability.
Understanding MOSFET Vulnerabilities
Common Causes of MOSFET Failure
Before we dive into the protection techniques, it’s essential to understand the common causes of MOSFET failure. MOSFETs are sensitive devices that can be damaged by various factors, including:
- Electrical Overstress (EOS)
- Electrostatic Discharge (ESD)
- Overheating
- Overcurrent
- Gate Oxide Breakdown
Electrical Overstress (EOS)
Electrical Overstress (EOS) refers to the condition where a MOSFET is subjected to voltage or current levels that exceed its maximum ratings. EOS can occur due to transient events, such as voltage spikes or inductive kickback, or due to sustained overvoltage or overcurrent conditions. When a MOSFET experiences EOS, it can suffer permanent damage to its internal structure, leading to degraded performance or complete failure.
Electrostatic Discharge (ESD)
Electrostatic Discharge (ESD) is a sudden and intense transfer of static charge between two objects. MOSFETs are particularly sensitive to ESD events due to their high input impedance and thin gate oxide. ESD can occur during handling, assembly, or even in the field, and it can cause immediate or latent damage to the MOSFET. Proper ESD protection is crucial to prevent device failure and ensure long-term reliability.
Overheating
MOSFETs generate heat during operation due to their internal resistance and switching losses. If the heat generated is not effectively dissipated, it can lead to overheating, which can cause thermal runaway and permanent damage to the device. Proper thermal management, including heatsinks and airflow, is essential to prevent MOSFET overheating.
Overcurrent
Overcurrent occurs when the current flowing through a MOSFET exceeds its maximum rated value. This can happen due to short circuits, excessive load, or improper gate drive. Overcurrent can cause localized heating and damage to the MOSFET’s internal structure, leading to reduced performance or complete failure. Current limiting and short-circuit protection are crucial to prevent overcurrent damage.
Gate Oxide Breakdown
The gate oxide is a thin insulating layer between the gate and the channel of a MOSFET. It is susceptible to breakdown if subjected to high electric fields or excessive voltage stress. Gate oxide breakdown can occur due to EOS, ESD, or even during normal operation if the gate voltage exceeds the maximum rating. Once the gate oxide breaks down, the MOSFET loses its ability to control the current flow and becomes permanently damaged.
Importance of ESD and EOS Protection
Given the sensitivity of MOSFETs to ESD and EOS events, implementing proper protection measures is of utmost importance. ESD and EOS protection help to:
- Prevent device failure and ensure reliability
- Improve system robustness and longevity
- Reduce maintenance and replacement costs
- Comply with industry standards and regulations
Without adequate ESD and EOS protection, MOSFETs are at risk of premature failure, leading to system downtime, increased maintenance costs, and potential safety hazards. Therefore, designers must prioritize ESD and EOS protection in their MOSFET-based circuits to ensure optimal performance and reliability.
MOSFET Protection Techniques
Now that we understand the vulnerabilities of MOSFETs and the importance of protection, let’s explore the various techniques available to safeguard these devices.
ESD Protection Techniques
ESD protection is crucial to prevent damage to MOSFETs during handling, assembly, and operation. Here are some commonly used ESD protection techniques:
ESD Protection Diodes
ESD protection diodes are one of the most effective methods to protect MOSFETs from ESD events. These diodes are connected between the MOSFET’s gate and source terminals, as well as between the drain and source terminals. When an ESD event occurs, the diodes provide a low-impedance path for the ESD current to flow, redirecting it away from the sensitive MOSFET.
There are two main types of ESD protection diodes:
-
Zener Diodes: Zener diodes are designed to break down at a specific voltage, providing a clamping effect to limit the voltage across the MOSFET. They are often used in conjunction with series resistors to limit the current during an ESD event.
-
Transient Voltage Suppressor (TVS) Diodes: Tvs Diodes are specifically designed for ESD protection and offer fast response times and high power handling capabilities. They are connected in parallel with the MOSFET and provide a low-impedance path for the ESD current when activated.
When selecting ESD protection diodes, consider factors such as breakdown voltage, clamping voltage, response time, and power handling capability to ensure adequate protection for your specific application.
ESD Protection Circuits
In addition to ESD protection diodes, various ESD protection circuits can be implemented to provide comprehensive protection for MOSFETs. These circuits typically combine diodes, resistors, and other components to create a robust ESD protection scheme.
Some common ESD protection circuits include:
-
RC Snubber Circuits: RC snubber circuits consist of a resistor and a capacitor connected in series across the MOSFET. They help to suppress voltage transients and reduce the rate of voltage change during an ESD event.
-
Diode Clamp Circuits: Diode clamp circuits use a combination of diodes and resistors to limit the voltage across the MOSFET during an ESD event. They provide a low-impedance path for the ESD current and help to dissipate the energy safely.
-
Active Clamp Circuits: Active clamp circuits employ active components, such as transistors or MOSFETs, to provide dynamic ESD protection. They can sense the ESD event and actively clamp the voltage across the protected MOSFET, providing fast and effective protection.
When designing ESD protection circuits, consider the specific requirements of your application, such as the expected ESD voltage levels, the MOSFET’s maximum ratings, and the circuit’s operating conditions. Simulations and testing can help to validate the effectiveness of the protection circuit and ensure optimal performance.
EOS Protection Techniques
Electrical Overstress (EOS) protection is essential to prevent damage to MOSFETs due to voltage or current levels exceeding their maximum ratings. Here are some techniques to protect MOSFETs from EOS events:
Voltage Clamping
Voltage clamping is a technique used to limit the voltage across a MOSFET to a safe level. This can be achieved using various components, such as:
-
Zener Diodes: Zener diodes can be connected in parallel with the MOSFET to clamp the voltage at a specific level. When the voltage exceeds the zener diode’s breakdown voltage, it conducts and prevents further voltage rise.
-
Transient Voltage Suppressors (TVS): TVS diodes, as mentioned earlier for ESD protection, can also be used for voltage clamping. They provide fast response times and can handle high power levels, making them suitable for EOS protection.
-
Metal Oxide Varistors (MOVs): MOVs are voltage-dependent resistors that exhibit a high resistance at low voltages and a low resistance at high voltages. They can be connected in parallel with the MOSFET to provide voltage clamping and suppress transient overvoltage events.
When selecting voltage clamping components, consider factors such as the clamping voltage, power handling capability, and response time to ensure adequate protection for your specific application.
Current Limiting
Current limiting is a technique used to restrict the current flowing through a MOSFET to a safe level. This can be achieved using various methods, such as:
-
Current Limiting Resistors: Current limiting resistors can be placed in series with the MOSFET to limit the current flow. The value of the resistor is chosen based on the maximum allowable current and the expected operating conditions.
-
Active Current Limiting: Active current limiting circuits use sensing and control mechanisms to dynamically limit the current. They can employ current sense resistors, comparators, and control circuits to detect overcurrent conditions and take corrective actions, such as shutting down the MOSFET or reducing the gate drive.
-
Fuses and Circuit Breakers: Fuses and circuit breakers can be used as a last resort to protect MOSFETs from sustained overcurrent conditions. When the current exceeds a predetermined threshold, the fuse blows or the circuit breaker trips, disconnecting the MOSFET from the power source.
When implementing current limiting techniques, consider the MOSFET’s maximum current rating, the expected load conditions, and the impact of the current limiting on the overall system performance.
Thermal Protection
Thermal protection is crucial to prevent MOSFET overheating and ensure reliable operation. Here are some techniques for thermal protection:
-
Heatsinks: Heatsinks are commonly used to dissipate heat generated by MOSFETs. They provide a large surface area for heat transfer and help to keep the MOSFET’s temperature within safe limits. Proper heatsink selection and mounting are essential for effective thermal management.
-
Thermal Shutdown Circuits: Thermal shutdown circuits monitor the MOSFET’s temperature and automatically shut down the device if it exceeds a predetermined threshold. These circuits typically use temperature sensors, such as thermistors or integrated temperature sensors, along with control circuits to detect overheating and initiate protective actions.
-
Airflow and Cooling: Adequate airflow and cooling are essential to prevent MOSFET overheating. This can be achieved through the use of fans, air ducts, or other cooling mechanisms. Proper layout and component placement also play a role in ensuring effective heat dissipation.
When designing thermal protection for MOSFETs, consider factors such as the MOSFET’s power dissipation, the expected operating conditions, and the available cooling methods. Thermal simulations and testing can help to validate the effectiveness of the thermal management strategy.
Gate Drive Protection
The gate drive circuit is responsible for controlling the MOSFET’s switching behavior and ensuring reliable operation. Proper gate drive protection is essential to prevent damage to the MOSFET due to excessive gate voltage or current. Here are some techniques for gate drive protection:
-
Gate Resistors: Gate resistors can be placed in series with the MOSFET’s gate to limit the gate current and reduce the rate of voltage change during switching. This helps to minimize voltage overshoots and ringing, which can cause gate oxide stress.
-
Zener Diodes: Zener diodes can be connected between the gate and source terminals to clamp the gate voltage at a safe level. If the gate voltage exceeds the zener diode’s breakdown voltage, it conducts and prevents further voltage rise, protecting the gate oxide.
-
Active Voltage Clamping: Active voltage Clamping Circuits use active components, such as transistors or MOSFETs, to dynamically clamp the gate voltage. They can sense the gate voltage and actively limit it to a safe level, providing fast and effective protection.
-
Gate Drive Transformers: Gate drive transformers can be used to provide isolation between the control circuitry and the MOSFET’s gate. They help to protect the MOSFET from common-mode noise and voltage transients that may be present on the control side.
When designing gate drive protection, consider the MOSFET’s gate characteristics, such as the maximum gate voltage and current ratings, as well as the expected switching speeds and operating conditions. Proper layout and component selection are crucial to ensure effective gate drive protection.
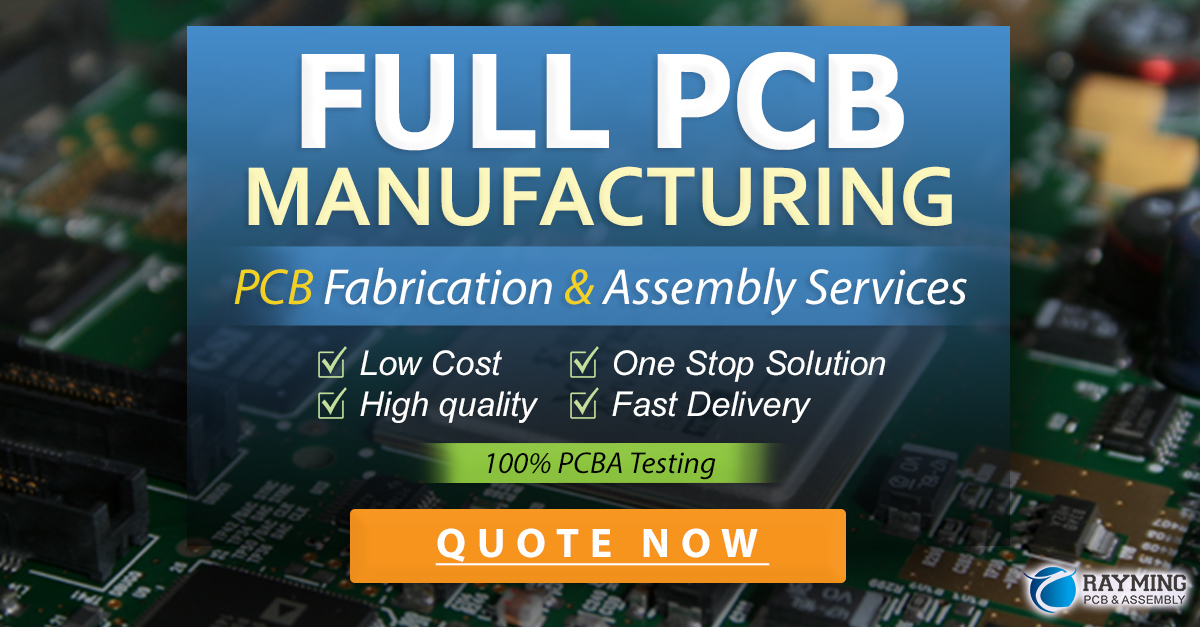
MOSFET Protection Best Practices
In addition to implementing specific protection techniques, following best practices can help to ensure optimal MOSFET protection and reliability. Here are some key best practices to consider:
-
Proper Device Selection: Choose MOSFETs with appropriate voltage and current ratings for your application. Consider factors such as the maximum drain-to-source voltage (VDSS), the maximum continuous drain current (ID), and the power dissipation (PD) when selecting devices.
-
Adequate Margin and Derating: Provide adequate margin and derating when designing MOSFET-based circuits. This means operating the MOSFET well below its maximum ratings to account for variations in operating conditions and component tolerances. A good rule of thumb is to derate the voltage and current ratings by at least 20-30%.
-
Proper Layout and Grounding: Proper PCB layout and grounding are crucial for MOSFET protection. Minimize the loop areas and trace lengths to reduce parasitic inductances and capacitances. Use a solid ground plane and provide low-impedance paths for ESD and transient currents. Keep sensitive traces away from noisy traces to minimize crosstalk and interference.
-
Transient Suppression: Implement transient suppression techniques to protect MOSFETs from voltage spikes and transients. This can include the use of snubber circuits, voltage clamping devices, and proper power supply decoupling. Consider the expected transient levels and the MOSFET’s maximum ratings when designing transient suppression.
-
Thermal Management: Ensure adequate thermal management to prevent MOSFET overheating. Use appropriate heatsinks, thermal interface materials, and cooling methods to dissipate heat effectively. Monitor the MOSFET’s temperature during operation and implement thermal shutdown circuits if necessary.
-
ESD Handling Precautions: Follow proper ESD handling precautions during assembly, testing, and field service. This includes using ESD-safe workstations, wearing ESD-protective gear, and handling MOSFETs in ESD-safe packaging. Regularly train personnel on ESD awareness and best practices.
-
Testing and Validation: Perform thorough testing and validation of MOSFET protection circuits to ensure their effectiveness. This can include ESD and EOS testing, as well as thermal and electrical characterization. Use industry-standard test methods and equipment to validate the protection performance.
By following these best practices and implementing appropriate protection techniques, designers can significantly improve the reliability and longevity of MOSFET-based circuits.
Frequently Asked Questions (FAQ)
-
Q: What is the difference between ESD and EOS protection for MOSFETs?
A: ESD protection focuses on protecting MOSFETs from sudden and intense electrostatic discharge events, typically of short duration and high voltage. EOS protection, on the other hand, addresses overvoltage or overcurrent conditions that exceed the MOSFET’s maximum ratings, which can be of longer duration and cause permanent damage. -
Q: Can a single protection device provide both ESD and EOS protection for MOSFETs?
A: While some devices, such as transient voltage suppressors (TVS), can offer protection against both ESD and EOS events to a certain extent, it is often recommended to use dedicated protection techniques for each type of event. This ensures optimal protection performance and allows for tailoring the protection to the specific requirements of the application. -
Q: How do I select the appropriate voltage rating for ESD protection diodes?
A: When selecting ESD protection diodes, consider the maximum expected ESD voltage levels in your application. The diode’s breakdown voltage should be higher than the maximum operating voltage of the MOSFET but lower than its maximum voltage rating. It’s also important to consider the diode’s clamping voltage and power handling capability to ensure effective protection. -
Q: What are the consequences of not providing adequate thermal protection for MOSFETs?
A: Inadequate thermal protection can lead to MOSFET overheating, which can cause permanent damage to the device. Overheating can result in reduced performance, increased leakage current, and even complete failure of the MOSFET. In extreme cases, overheating can also pose safety hazards, such as fire or explosion. -
Q: How can I validate the effectiveness of my MOSFET protection design?
A: To validate the effectiveness of your MOSFET protection design, perform thorough testing and characterization. This can include ESD and EOS testing using industry-standard methods, such as the human body model (HBM) or the charged device model (CDM). Additionally, perform thermal characterization to ensure adequate heat dissipation and monitor the MOSFET’s temperature during operation. Electrical characterization, including voltage and current measurements, can help to verify the protection circuit’s performance.
Conclusion
Protecting MOSFETs is crucial to ensure their reliable operation and longevity in various applications. By understanding the common causes of MOSFET failure, such as ESD, EOS, overheating, overcurrent, and gate oxide
Leave a Reply