What is Metallization?
Metallization is the process of coating a non-metallic substrate, such as plastic, ceramic, or glass, with a thin layer of metal. The Metallization Process involves depositing a thin film of metal onto the surface of the substrate material to give it metallic properties such as conductivity, reflectivity, and a metallic appearance.
Metallization is widely used in various industries, including electronics, automotive, aerospace, and consumer goods. It enables non-metallic materials to have desirable metallic characteristics while retaining the advantageous properties of the substrate, such as light weight, durability, and low cost.
Metallization Techniques
There are several techniques used for metallization, each with its own advantages and limitations. The choice of metallization technique depends on factors such as the substrate material, the desired metal coating, the required adhesion strength, and the intended application. Some common metallization techniques include:
Physical Vapor Deposition (PVD)
PVD is a vacuum deposition method that involves vaporizing a solid metal source and condensing it onto the substrate surface. The two main PVD processes are evaporation and sputtering.
Evaporation
In evaporation, the metal source is heated in a vacuum chamber until it evaporates. The metal vapor then condenses on the cooler substrate surface, forming a thin film. Evaporation is suitable for depositing pure metal films and is often used for decorative coatings and electronics applications.
Sputtering
Sputtering involves bombarding a metal target with high-energy ions, typically argon, in a vacuum chamber. The ion bombardment causes metal atoms to be ejected from the target and deposited onto the substrate. Sputtering can deposit a wider range of materials, including alloys and compounds, and provides better adhesion and uniformity compared to evaporation.
Chemical Vapor Deposition (CVD)
CVD is a process in which a volatile precursor compound of the desired metal is introduced into a reaction chamber and decomposed on the heated substrate surface, resulting in the deposition of a thin metal film. CVD can produce high-purity, uniform coatings with excellent conformal coverage and is widely used in the semiconductor industry for depositing thin films of metals, oxides, and nitrides.
Electroplating
Electroplating is a process that uses an electrical current to reduce dissolved metal cations and deposit them onto a conductive substrate. The substrate is immersed in an electrolyte solution containing the desired metal ions and connected to the negative terminal (cathode) of a power supply. A metal anode is connected to the positive terminal. When an electric current is applied, the metal ions are reduced at the cathode and deposited onto the substrate surface. Electroplating is commonly used for depositing thick, uniform metal coatings for corrosion protection, wear resistance, and decorative purposes.
Electroless Plating
Electroless plating, also known as autocatalytic plating, is a chemical reduction process that deposits a metal coating without the use of an external electrical current. The substrate is immersed in a plating solution containing a metal salt, a reducing agent, and a catalyst. The catalyst, typically palladium or tin, initiates the reduction of the metal ions on the substrate surface, leading to the deposition of a metal film. Electroless plating is often used for coating non-conductive substrates and provides uniform coverage, even on complex geometries.
Metallization Process Steps
The metallization process typically involves the following steps:
-
Substrate Preparation: The substrate surface is cleaned and treated to remove contaminants and improve adhesion. This may involve degreasing, etching, or applying a surface treatment such as plasma or chemical modification.
-
Seed Layer Deposition: In some cases, a thin seed layer of a conductive material, such as titanium or chromium, is deposited onto the substrate to promote adhesion and facilitate the subsequent metal deposition.
-
Metal Deposition: The desired metal is deposited onto the substrate using one of the metallization techniques described earlier, such as PVD, CVD, electroplating, or electroless plating.
-
Post-Treatment: After metal deposition, the coated substrate may undergo additional treatments to improve the properties of the metal film, such as annealing, passivation, or applying a protective top coat.
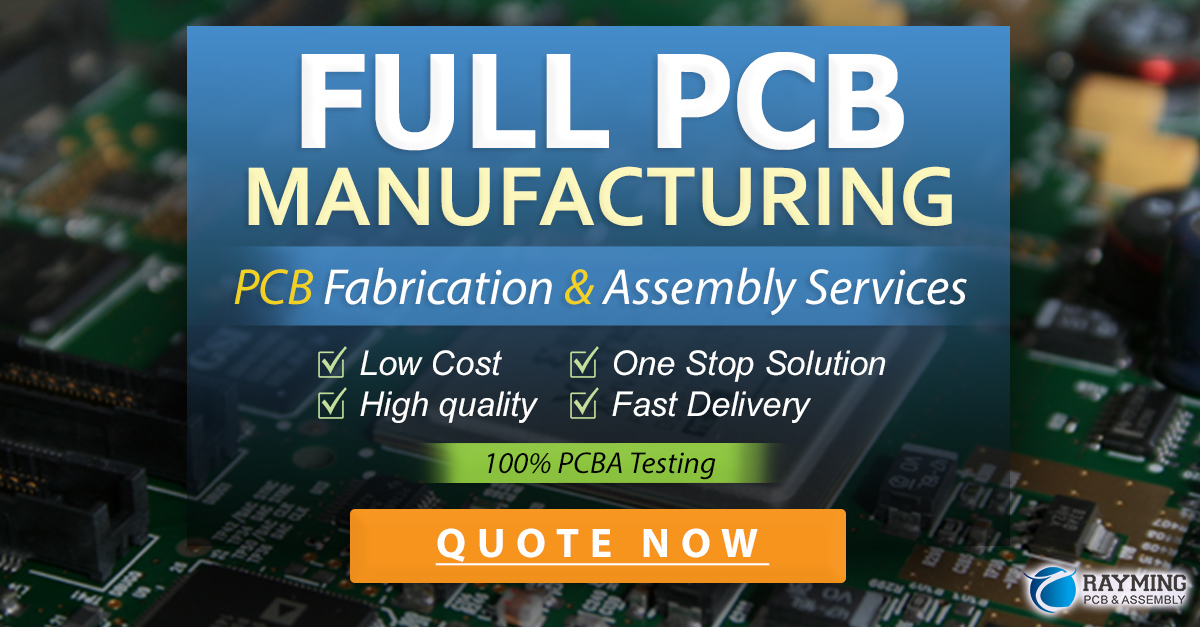
Metallization Materials
Various metals can be used for metallization, depending on the desired properties and applications. Some common metallization materials include:
Metal | Properties | Applications |
---|---|---|
Aluminum | – Good electrical and thermal conductivity – Reflective – Lightweight |
– Electronics – Solar cells – Reflectors |
Copper | – Excellent electrical and thermal conductivity – Good ductility |
– Electronics – Heat exchangers – Decorative coatings |
Gold | – Excellent electrical conductivity – Corrosion resistant – Biocompatible |
– Electronics – Biomedical devices – Decorative coatings |
Silver | – Highest electrical and thermal conductivity – Reflective |
– Electronics – Solar cells – Mirrors |
Nickel | – Good corrosion resistance – Hard and wear-resistant |
– Corrosion protection – Wear-resistant coatings |
Chromium | – Hard and wear-resistant – Corrosion resistant – Decorative |
– Wear-resistant coatings – Decorative finishes |
Titanium | – High strength-to-weight ratio – Corrosion resistant – Biocompatible |
– Aerospace – Biomedical devices – Decorative coatings |
Advantages of Metallization
Metallization offers several advantages, including:
-
Enhanced Electrical and Thermal Conductivity: Metallization can impart electrical and thermal conductivity to non-conductive substrates, enabling their use in electronic and thermal management applications.
-
Improved Corrosion and Wear Resistance: Metal coatings can protect the substrate from corrosion and wear, extending the life of the component and reducing maintenance costs.
-
Decorative Finishes: Metallization can provide attractive, metallic finishes to non-metallic substrates, enhancing their aesthetic appeal for consumer products and decorative applications.
-
Lightweight Components: By using metallized non-metallic substrates, lightweight components with metallic properties can be produced, which is particularly advantageous in aerospace and automotive applications.
-
Cost-Effective: Metallization allows the use of low-cost, lightweight substrate materials while providing the desired metallic properties, resulting in cost savings compared to using solid metal components.
Challenges in Metallization
Despite its numerous advantages, metallization also presents some challenges:
-
Adhesion: Ensuring strong adhesion between the metal coating and the substrate is critical for the durability and performance of the metallized component. Poor adhesion can lead to delamination, flaking, or peeling of the metal film.
-
Thermal Expansion Mismatch: Differences in the thermal expansion coefficients of the metal coating and the substrate can cause stress and delamination during thermal cycling, particularly for high-temperature applications.
-
Uniform Coverage: Achieving uniform metal coverage on complex geometries or porous substrates can be challenging, especially with line-of-sight deposition techniques like PVD.
-
Process Control: Metallization processes often involve multiple variables, such as temperature, pressure, gas flow rates, and chemical compositions, which must be carefully controlled to ensure consistent and high-quality metal coatings.
-
Environmental Concerns: Some metallization processes, particularly those involving hazardous chemicals or high energy consumption, may have environmental impacts that need to be addressed and mitigated.
Frequently Asked Questions (FAQ)
1. What is the difference between PVD and CVD metallization?
PVD (Physical Vapor Deposition) and CVD (Chemical Vapor Deposition) are both metallization techniques, but they differ in their deposition mechanisms. PVD involves the physical vaporization and condensation of a metal source onto the substrate, while CVD uses chemical reactions of volatile precursors to deposit a metal film on the heated substrate. PVD is typically used for depositing pure metal films, while CVD can deposit a wider range of materials, including metals, oxides, and nitrides.
2. Can metallization be applied to any substrate material?
Metallization can be applied to a wide range of non-metallic substrates, including plastics, ceramics, glass, and composites. However, the choice of substrate material and its surface properties can affect the adhesion, uniformity, and performance of the metal coating. Some substrates may require surface treatments or modifications to improve the compatibility with the metallization process.
3. How does surface preparation affect the quality of metallization?
Surface preparation is a critical step in the metallization process, as it directly influences the adhesion and quality of the metal coating. Proper surface preparation involves cleaning the substrate to remove contaminants, such as oils, dust, or oxides, and modifying the surface to improve its wettability and reactivity. Common surface preparation techniques include degreasing, etching, plasma treatment, and chemical modification. Inadequate surface preparation can lead to poor adhesion, non-uniformity, and defects in the metal coating.
4. What are the factors that influence the choice of metallization technique?
The choice of metallization technique depends on several factors, including:
- Substrate material and its properties
- Desired metal coating and its thickness
- Required adhesion strength and durability
- Intended application and performance requirements
- Production scale and cost considerations
For example, PVD is often used for depositing thin, pure metal films for electronics applications, while electroplating is suitable for producing thick, uniform coatings for corrosion protection and decorative purposes.
5. How can the durability of metallized components be improved?
The durability of metallized components can be improved through various strategies, such as:
- Optimizing the surface preparation to ensure strong adhesion between the metal coating and the substrate
- Selecting metallization materials and techniques that are compatible with the substrate and the intended application
- Applying post-treatment processes, such as annealing or passivation, to enhance the mechanical and chemical stability of the metal coating
- Using intermediate layers, such as adhesion promoters or diffusion barriers, to improve the interfacial properties
- Designing the component to minimize stress concentrations and thermal expansion mismatches
- Implementing quality control measures to ensure consistent and defect-free metal coatings
By addressing these aspects, the durability and performance of metallized components can be significantly enhanced, extending their service life and reliability in demanding applications.
Conclusion
Metallization is a versatile process that enables the deposition of thin metal films onto non-metallic substrates, imparting desirable metallic properties while retaining the advantages of the substrate material. With a wide range of metallization techniques and materials available, it finds applications in diverse industries, from electronics and automotive to aerospace and consumer goods.
The success of the metallization process depends on careful selection of the substrate material, surface preparation, metallization technique, and post-treatment processes. Overcoming challenges related to adhesion, uniformity, and process control is crucial for achieving high-quality and durable metal coatings.
As technology advances, new metallization techniques and materials are being developed to meet the ever-increasing demands for performance, efficiency, and sustainability. Continued research and innovation in this field will undoubtedly lead to the development of novel metallized products and applications that push the boundaries of what is possible with non-metallic materials.
Leave a Reply