What are Metal Oxide Varistors?
Metal oxide varistors (MOVs) are voltage-dependent resistors commonly used to protect electronic circuits against voltage spikes caused by electrostatic discharge, lightning strikes, or power surges. They are made from a ceramic material, typically zinc oxide, combined with other metal oxides such as bismuth, cobalt, or manganese.
MOVs have a non-linear current-voltage characteristic, which means their resistance varies with the applied voltage. Under normal operating conditions, varistors have a high resistance and allow only a small leakage current to flow. However, when the voltage across the varistor exceeds a certain threshold, its resistance dramatically decreases, allowing a large current to flow and effectively shunting the excess energy away from the protected circuit.
Key Features of Metal Oxide Varistors
- Non-linear current-voltage characteristic
- Fast response time (typically nanoseconds)
- High energy absorption capability
- Compact size and low cost
- Wide operating voltage range (from a few volts to several kilovolts)
How Do Metal Oxide Varistors Work?
The unique behavior of metal oxide varistors is attributed to their microstructure, which consists of conductive zinc oxide grains separated by grain boundaries that act as potential barriers. These grain boundaries are responsible for the non-linear current-voltage characteristic of the varistor.
Equivalent Circuit Model
The electrical behavior of a metal oxide varistor can be represented by an equivalent circuit model consisting of a network of series and parallel-connected resistors and capacitors. This model helps to understand the various conduction mechanisms within the varistor.
Conduction Mechanisms
There are three main conduction mechanisms in a metal oxide varistor:
-
Grain boundary conduction: At low voltages, the current flows through the grain boundaries, which have a high resistance due to the potential barriers. This results in a small leakage current.
-
Grain conduction: As the voltage increases, the potential barriers at the grain boundaries are lowered, allowing current to flow through the conductive zinc oxide grains. This leads to a significant decrease in the varistor’s resistance.
-
Avalanche breakdown: At very high voltages, the electric field across the grain boundaries becomes large enough to cause avalanche breakdown, resulting in a rapid increase in current flow.
Types of Metal Oxide Varistors
Metal oxide varistors are available in various sizes, voltage ratings, and energy absorption capabilities to suit different applications. Some common types of MOVs include:
-
Disc varistors: These are the most common type of MOVs, with a round disc shape and radial leads. They are available in diameters ranging from a few millimeters to several centimeters.
-
SMD varistors: Surface-mount device (SMD) varistors are designed for automated assembly on printed circuit boards. They come in various package sizes, such as 0402, 0603, and 1206.
-
High-energy varistors: These MOVs are designed to handle very high energy surges, such as those caused by lightning strikes. They are typically larger in size and have higher voltage and energy ratings compared to standard varistors.
-
Thermally protected varistors: These varistors incorporate a thermal disconnect mechanism that removes the varistor from the circuit in case of overheating due to prolonged overvoltage conditions, preventing damage to the protected equipment.
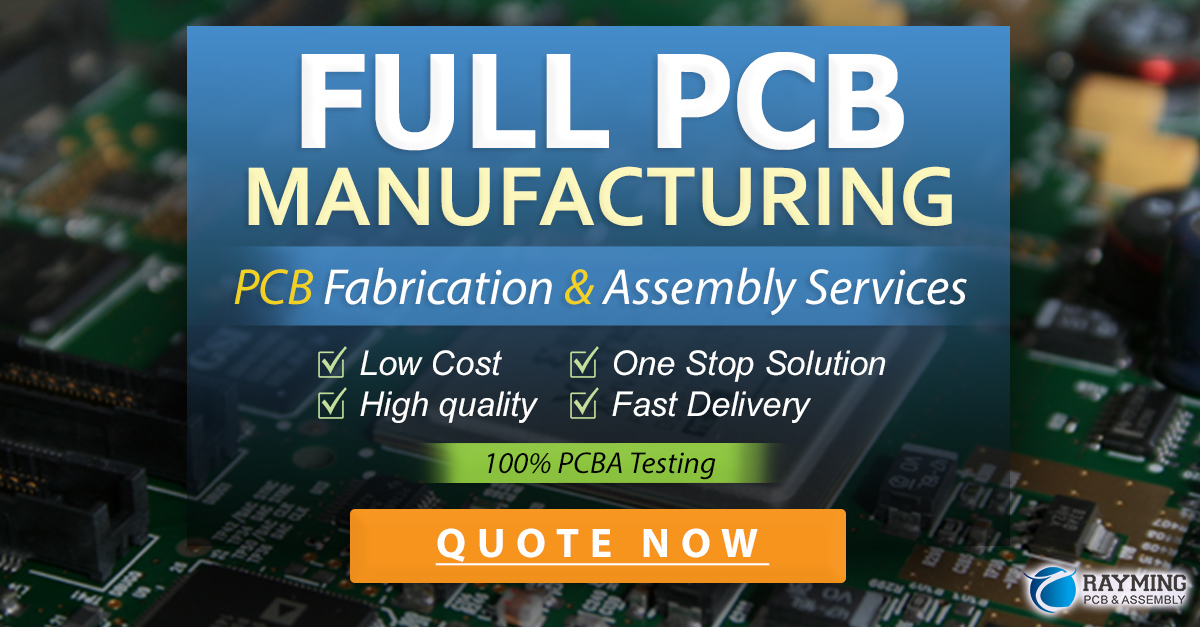
Applications of Metal Oxide Varistors
Metal oxide varistors are widely used in various industries for overvoltage protection, including:
-
Power supply protection: MOVs are commonly used in switch-mode power supplies, uninterruptible power supplies (UPS), and power distribution systems to protect against voltage spikes and transients.
-
Telecommunications: Varistors protect sensitive telecommunication equipment, such as modems, routers, and switches, from voltage surges caused by lightning or power line disturbances.
-
Automotive electronics: In automotive applications, MOVs protect electronic control units (ECUs), sensors, and other electronic components from voltage spikes caused by load dumps, ignition noise, or electrostatic discharge.
-
Industrial equipment: Varistors are used to protect industrial automation systems, process control equipment, and motors from voltage surges and transients.
-
Consumer electronics: MOVs are found in a wide range of consumer electronic devices, such as televisions, computers, home appliances, and surge protector power strips, to provide overvoltage protection.
Selecting the Right Metal Oxide Varistor
When choosing a metal oxide varistor for a specific application, several key parameters should be considered:
-
Continuous operating voltage (Vc): This is the maximum voltage that can be continuously applied to the varistor without causing degradation or damage. The selected MOV should have a Vc rating higher than the expected normal operating voltage of the protected circuit.
-
Clamping voltage (Vclamp): The clamping voltage is the peak voltage that appears across the varistor when subjected to a specified surge current. A lower clamping voltage provides better protection for the connected equipment.
-
Energy absorption capability: This is the maximum amount of energy the varistor can absorb without failing. The energy rating should be selected based on the expected surge energy in the application.
-
Response time: MOVs have a very fast response time, typically in the nanosecond range. However, some applications may require even faster response times, such as in high-speed digital circuits.
-
Package size and mounting options: Varistors are available in various package sizes and mounting options, such as through-hole, surface-mount, and bolt-down. The selected package should be compatible with the circuit layout and assembly process.
Varistor Specifications and Ratings
Varistor datasheets provide essential information about the device’s characteristics and performance. Some key specifications and ratings include:
-
Varistor voltage (V1mA): This is the voltage at which the varistor conducts a specified leakage current, typically 1 mA. It is used to define the nominal operating voltage of the varistor.
-
Maximum continuous operating voltage (MCOV): This is the maximum voltage that can be continuously applied to the varistor without causing degradation or damage.
-
Peak current (Ipeak): The maximum instantaneous current the varistor can withstand without failing.
-
Energy absorption (Wmax): The maximum energy the varistor can absorb in a single surge event without failing.
-
Capacitance (C): The capacitance of the varistor at a specified frequency, typically 1 kHz. This parameter is important for high-frequency applications.
-
Response time (tresponse): The time it takes for the varistor to begin conducting after the voltage exceeds the clamping voltage.
Varistor Protection Circuit Design Considerations
When designing a varistor protection circuit, several factors should be taken into account to ensure optimal performance and reliability:
-
Voltage rating: The varistor’s continuous operating voltage should be selected based on the normal operating voltage of the protected circuit, with sufficient margin to account for voltage fluctuations.
-
Energy absorption: The varistor’s energy absorption capability should be chosen based on the expected surge energy in the application. In some cases, multiple varistors may need to be connected in parallel to increase the total energy absorption capacity.
-
Series impedance: A series impedance, such as an inductance or resistance, can be added to limit the peak current through the varistor during a surge event. This helps to reduce the stress on the varistor and improve its lifespan.
-
Thermal management: In applications with frequent or prolonged surge events, the varistor may generate significant heat. Proper thermal management, such as heat sinks or thermal fuses, should be implemented to prevent overheating and failure.
-
Coordination with other protection devices: When using varistors in conjunction with other overvoltage protection devices, such as gas discharge tubes (GDTs) or transient voltage suppression (TVS) diodes, the protection circuit should be designed to ensure proper coordination and avoid interference between the devices.
Varistor Failure Modes and Precautions
Metal oxide varistors are reliable devices, but they can fail under certain conditions. The most common failure modes include:
-
Thermal runaway: If the varistor is subjected to a continuous overvoltage or a series of closely spaced surge events, it may enter a state of thermal runaway, where the device’s temperature increases uncontrollably, leading to failure.
-
Short-circuit failure: In some cases, a varistor may fail short-circuit, effectively creating a low-resistance path between the protected line and ground. This can cause excessive current flow and damage to the protected equipment.
-
Open-circuit failure: Less commonly, a varistor may fail open-circuit, losing its ability to provide overvoltage protection.
To minimize the risk of varistor failure and ensure long-term reliability, the following precautions should be taken:
-
Proper voltage rating selection: Choose a varistor with a continuous operating voltage rating higher than the expected normal operating voltage of the protected circuit.
-
Adequate energy absorption capability: Select a varistor with sufficient energy absorption capacity to handle the expected surge energy in the application.
-
Thermal management: Implement proper thermal management techniques, such as heat sinks or thermal fuses, to prevent overheating and thermal runaway.
-
Regular maintenance and replacement: Periodically inspect the varistors for signs of degradation or damage, and replace them as necessary to ensure continued protection.
Frequently Asked Questions (FAQ)
-
What is the difference between a varistor and a surge suppressor?
A varistor is a voltage-dependent resistor that is used as a key component in surge suppressors. A surge suppressor, also known as a surge protector, is a device that incorporates one or more varistors, along with other components such as capacitors and inductors, to provide comprehensive overvoltage protection for electronic equipment. -
Can a varistor protect against lightning strikes?
While varistors can provide some protection against voltage surges caused by nearby lightning strikes, they may not be sufficient to fully protect equipment from direct lightning strikes. In applications with a high risk of direct lightning strikes, additional protection measures, such as lightning rods and grounding systems, should be implemented in conjunction with varistors. -
How do I know when a varistor needs to be replaced?
Varistors can degrade over time, especially if they have been subjected to frequent or severe surge events. Signs that a varistor may need to be replaced include visible cracks or discoloration on the device’s surface, increased leakage current, or a shift in the varistor’s voltage-current characteristic. Regular inspection and testing of varistors can help identify when replacement is necessary. -
Can I connect multiple varistors in parallel for increased protection?
Yes, connecting multiple varistors in parallel can increase the total energy absorption capability of the protection circuit. However, it is important to ensure that the varistors are closely matched in terms of their voltage and energy ratings to prevent uneven current sharing and premature failure of individual devices. -
Are there any environmental factors that can affect varistor performance?
Temperature and humidity can affect the performance of metal oxide varistors. High temperatures can accelerate the degradation of the varistor and increase the risk of thermal runaway. High humidity can lead to moisture ingress, which can cause corrosion and deterioration of the device’s performance. In applications with extreme environmental conditions, specialized varistors with enhanced temperature and humidity ratings may be required.
Conclusion
Metal oxide varistors are essential components in overvoltage protection circuits, offering fast response times, high energy absorption capabilities, and compact size. By understanding the working principles, selection criteria, and design considerations for MOVs, engineers can effectively integrate these devices into their systems to ensure reliable protection against voltage surges and transients.
As technology advances and new applications emerge, the demand for robust overvoltage protection solutions will continue to grow. Ongoing research and development in the field of metal oxide varistors will lead to further improvements in performance, reliability, and cost-effectiveness, making these devices an indispensable part of modern electronic systems.
Leave a Reply