Introduction to MCPCB
Metal Core Printed Circuit Boards (MCPCBs) are a specialized type of PCB that uses a metal substrate instead of the traditional FR-4 material. The metal substrate, typically aluminum, provides excellent Thermal Conductivity, making MCPCBs ideal for applications that generate significant heat, such as high-power LED lighting and power electronics.
MCPCBs offer several advantages over standard PCBs:
- Enhanced thermal management
- Improved electrical performance
- Increased reliability and longevity
- Reduced size and weight
In this article, we will delve into the world of MCPCBs, exploring their construction, applications, design considerations, and manufacturing processes.
Construction of MCPCBs
Layers of an MCPCB
An MCPCB consists of three main layers:
-
Dielectric layer: This layer is a thin, electrically insulating material that sits between the metal substrate and the copper circuit layer. It is typically made of a thermally conductive but electrically insulating material, such as aluminum oxide or boron nitride.
-
Metal substrate: The metal substrate, usually aluminum, serves as the base of the MCPCB and provides the main thermal management function. Other metals, such as copper or steel, may be used for specific applications.
-
Copper circuit layer: The copper circuit layer is where the electrical components and traces are located. This layer is similar to the copper layer in a standard PCB.
Thermal Conductivity Comparison
The table below compares the thermal conductivity of common materials used in PCBs:
Material | Thermal Conductivity (W/mK) |
---|---|
FR-4 | 0.3 |
Aluminum | 150-200 |
Copper | 385-400 |
As evident from the table, aluminum and copper offer significantly higher thermal conductivity than FR-4, making MCPCBs more effective at dissipating heat.
Applications of MCPCBs
High-Power LED Lighting
One of the most common applications of MCPCBs is in high-power LED lighting. LEDs generate a significant amount of heat, which can negatively impact their performance and lifespan. By using an MCPCB, the heat generated by the LEDs can be efficiently dissipated, ensuring optimal performance and longevity.
MCPCBs are used in various LED lighting applications, such as:
- Street lighting
- Automotive lighting
- Industrial lighting
- Architectural lighting
Power Electronics
MCPCBs are also used in power electronics applications, where efficient thermal management is crucial. Some examples include:
- Motor drives
- Power inverters
- Switching power supplies
- High-current amplifiers
In these applications, MCPCBs help to dissipate heat generated by power components, such as MOSFETs, IGBTs, and rectifiers, ensuring reliable operation and preventing premature failure.
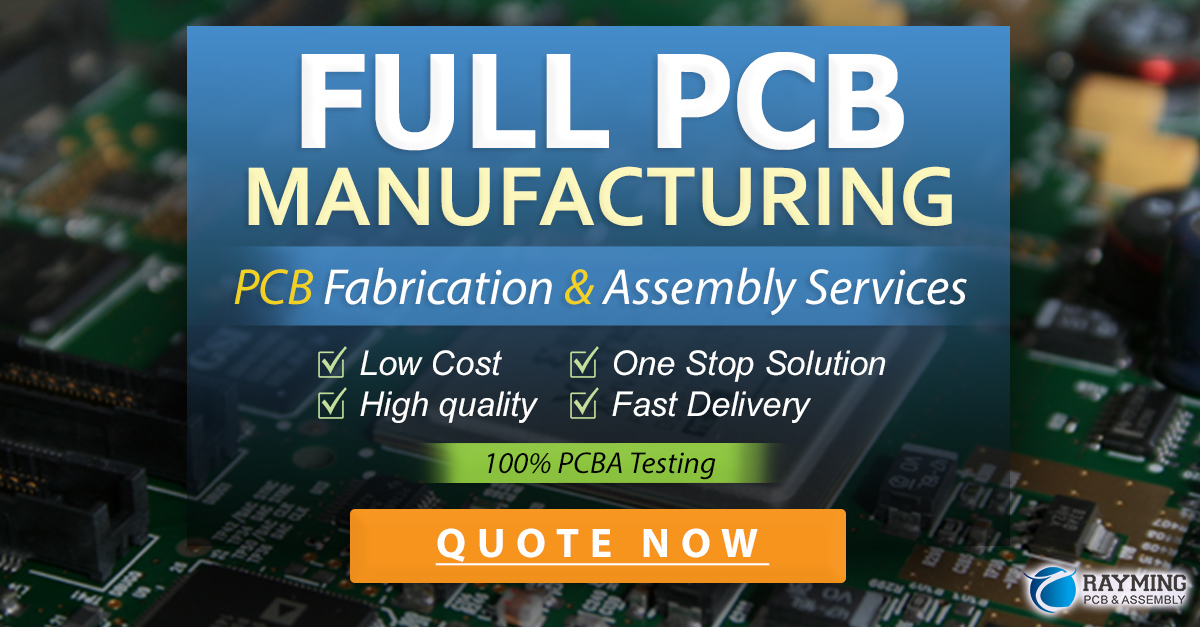
Design Considerations for MCPCBs
When designing an MCPCB, several factors must be considered to ensure optimal performance and reliability.
Thermal Management
The primary purpose of an MCPCB is to effectively dissipate heat. To achieve this, designers must consider:
-
Thermal resistance: The thermal resistance of the MCPCB should be as low as possible to facilitate efficient heat transfer from the components to the metal substrate.
-
Dielectric layer thickness: A thinner dielectric layer improves thermal conductivity but may compromise electrical insulation. Designers must strike a balance between thermal performance and electrical safety.
-
Metal substrate thickness: A thicker metal substrate provides better thermal conductivity but increases the overall weight and cost of the MCPCB.
Electrical Performance
While thermal management is the primary focus of MCPCBs, electrical performance must not be overlooked. Designers should consider:
-
Impedance control: Proper impedance control is essential for high-speed circuits to minimize signal reflections and ensure signal integrity.
-
Electromagnetic compatibility (EMC): MCPCBs must be designed to minimize electromagnetic interference (EMI) and ensure compliance with relevant EMC standards.
Mechanical Considerations
MCPCBs must also be designed with mechanical factors in mind, such as:
-
Coefficient of thermal expansion (CTE): The CTE of the metal substrate should be as close as possible to that of the components to minimize stress due to thermal expansion.
-
Mounting and assembly: The MCPCB Design should facilitate easy mounting and assembly of components, considering factors such as component placement, soldering, and heat sinking.
Manufacturing Process of MCPCBs
The manufacturing process of MCPCBs is similar to that of standard PCBs, with a few key differences.
Substrate Preparation
The metal substrate, typically aluminum, is first cleaned and roughened to improve adhesion of the dielectric layer. The substrate may also undergo a pre-treatment process, such as anodizing, to enhance its electrical insulation properties.
Dielectric Layer Application
The dielectric layer is applied to the metal substrate using one of several methods:
-
Lamination: A pre-fabricated dielectric sheet is laminated onto the metal substrate using heat and pressure.
-
Coating: A liquid dielectric material is coated onto the metal substrate and then cured.
-
Sputtering: A thin layer of dielectric material is deposited onto the metal substrate using a sputtering process.
Circuit Layer Formation
The copper circuit layer is formed on top of the dielectric layer using standard PCB manufacturing processes, such as:
-
Electroless copper plating: A thin layer of copper is deposited onto the dielectric layer using an electroless plating process.
-
Electroplating: Additional copper is electroplated onto the electroless copper layer to achieve the desired thickness.
-
Etching: The copper layer is selectively etched to form the circuit pattern.
Finishing and Assembly
Finally, the MCPCB undergoes finishing processes, such as Solder Mask application and surface finish (e.g., HASL, ENIG), and components are assembled onto the board using standard SMT or through-hole assembly techniques.
Advantages and Disadvantages of MCPCBs
Advantages
- Excellent thermal management
- Improved electrical performance
- Increased reliability and longevity
- Reduced size and weight
Disadvantages
- Higher cost compared to standard PCBs
- Limited flexibility in design due to the metal substrate
- Potential for thermal expansion mismatch between components and substrate
Future Trends in MCPCB Technology
As the demand for high-performance electronics continues to grow, MCPCB technology is expected to evolve to meet new challenges. Some future trends in MCPCB technology include:
-
Advanced dielectric materials: Researchers are developing new dielectric materials with higher thermal conductivity and better electrical insulation properties to improve MCPCB performance.
-
Embedded components: Integrating passive components, such as resistors and capacitors, directly into the MCPCB can further reduce size and improve electrical performance.
-
3D printing: Additive manufacturing techniques, such as 3D printing, may be used to create MCPCBs with complex geometries and improved thermal management capabilities.
-
Hybrid MCPCBs: Combining MCPCBs with other advanced PCB technologies, such as flexible or Rigid-Flex PCBs, can provide new opportunities for designing compact, high-performance electronics.
Frequently Asked Questions (FAQ)
-
Q: What is the main difference between MCPCBs and standard PCBs?
A: The main difference is that MCPCBs use a metal substrate, typically aluminum, instead of the traditional FR-4 material. This metal substrate provides excellent thermal conductivity, making MCPCBs ideal for applications that generate significant heat. -
Q: Can MCPCBs be used for all types of electronic devices?
A: While MCPCBs offer excellent thermal management and electrical performance, they may not be suitable for all applications. They are best suited for devices that generate significant heat, such as high-power LEDs and power electronics. -
Q: Are MCPCBs more expensive than standard PCBs?
A: Yes, MCPCBs are generally more expensive than standard PCBs due to the additional materials and manufacturing processes involved. However, the improved thermal management and performance often justify the higher cost in applications where thermal management is critical. -
Q: Can MCPCBs be manufactured using the same processes as standard PCBs?
A: The manufacturing process for MCPCBs is similar to that of standard PCBs, but with some additional steps. These include preparing the metal substrate, applying the dielectric layer, and ensuring proper bonding between the layers. -
Q: What are some common applications of MCPCBs?
A: MCPCBs are commonly used in high-power LED lighting applications, such as street lighting, automotive lighting, and industrial lighting. They are also used in power electronics applications, such as motor drives, power inverters, and switching power supplies.
Conclusion
Metal Core PCBs (MCPCBs) are a valuable technology for applications that require efficient thermal management and high electrical performance. By using a metal substrate, typically aluminum, MCPCBs can effectively dissipate heat generated by components, ensuring optimal performance and reliability.
MCPCBs find widespread use in high-power LED lighting and power electronics applications, where thermal management is critical. When designing MCPCBs, engineers must consider factors such as thermal resistance, dielectric layer thickness, and mechanical properties to ensure the best possible performance.
As the demand for high-performance electronics continues to grow, MCPCB technology is expected to evolve, with advancements in materials, manufacturing processes, and integration with other PCB technologies. By understanding the principles, applications, and design considerations of MCPCBs, engineers can leverage this technology to create compact, efficient, and reliable electronic devices.
Leave a Reply