What is an LED PCB?
An LED PCB, or Light Emitting Diode Printed Circuit Board, is a specialized type of circuit board designed to efficiently power and control LEDs. These boards are essential components in various applications, from simple indicators to complex lighting systems. LED PCBs combine the functionality of a traditional PCB with the specific requirements of LEDs, such as heat dissipation, current regulation, and optimal layout for light distribution.
Key Components of an LED PCB
- Substrate Material:
- FR-4: A common, cost-effective, and flame-retardant material
- Aluminum: Provides excellent heat dissipation for high-power LEDs
-
Flexible PCBs: Used in applications requiring bendable or wearable lighting solutions
-
Copper Traces:
- Designed to carry electrical current to the LEDs
-
Trace width and thickness are determined by the current requirements of the LEDs
-
Solder Mask:
- Insulating layer that covers the copper traces
- Protects against short circuits and environmental factors
-
Available in various colors, with white being popular for LED PCBs to enhance light reflection
-
Silkscreen:
- Text and symbols printed on the PCB for identification and assembly guidance
-
Helps in orienting and placing components correctly
-
LED Components:
- Surface Mounted Devices (SMD) LEDs: Small, compact, and easily soldered onto the PCB
-
Through-Hole LEDs: Traditional LED packages with leads that are inserted into holes on the PCB
-
Additional Components:
- Resistors: Current-limiting components to protect LEDs from excessive current
- Capacitors: Smooth out voltage fluctuations and reduce noise
- Drivers: Regulate current and provide constant voltage to the LEDs
- Heat Sinks: Dissipate heat generated by high-power LEDs to maintain optimal performance
Advantages of Using LED PCBs
Efficiency and Energy Savings
LED PCBs offer significant energy savings compared to traditional lighting solutions. LEDs consume less power and convert a higher percentage of that power into light, resulting in lower energy costs and a reduced environmental impact. This efficiency also translates to longer battery life in portable devices and lower cooling requirements in larger systems.
Durability and Long Lifespan
LEDs, when properly integrated with a well-designed PCB, can last for tens of thousands of hours. This extended lifespan reduces maintenance costs and minimizes the need for frequent replacements. Additionally, LEDs are solid-state devices, making them more resistant to vibration, shock, and extreme temperatures than traditional lighting solutions.
Versatility and Design Flexibility
LED PCBs offer unparalleled design flexibility. They can be manufactured in various shapes and sizes to fit specific application requirements, from tiny indicators to large-scale lighting installations. The compact nature of SMD LEDs allows for high-density layouts and enables the creation of thin, lightweight lighting solutions.
Controllability and Color Options
LED PCBs can be designed with sophisticated control circuits, enabling features such as dimming, color mixing, and dynamic lighting effects. By combining LEDs of different colors or using RGB LEDs, a wide range of colors can be achieved, allowing for customizable and adaptive lighting solutions.
Table: Comparison of LED PCBs and Traditional Lighting PCBs
Feature | LED PCBs | Traditional Lighting PCBs |
---|---|---|
Energy Efficiency | High | Low to Moderate |
Lifespan | Long (50,000+ hours) | Short to Moderate |
Design Flexibility | High | Limited |
Color Options | Wide Range | Limited |
Heat Dissipation | Critical | Less Critical |
Environmental Impact | Low | Moderate to High |
Cost (Long-Term) | Lower | Higher |
Applications of LED PCBs
Automotive Lighting
LED PCBs have revolutionized the automotive lighting industry. They are used in various applications, such as:
- Headlights and Taillights
- Interior Lighting
- Dashboard Indicators
- Daytime Running Lights (DRLs)
The compact size, high efficiency, and long lifespan of LED PCBs make them ideal for automotive applications, where reliability and durability are critical. Additionally, the design flexibility of LED PCBs allows for creative and distinctive lighting designs that enhance the overall aesthetics of vehicles.
General Lighting
LED PCBs are widely used in general lighting applications, replacing traditional incandescent and fluorescent bulbs in residential, commercial, and industrial settings. Some common applications include:
- Ceiling Lights
- Desk Lamps
- Downlights
- Street Lights
The energy efficiency and long lifespan of LED PCBs result in significant cost savings and reduced maintenance requirements. Moreover, the controllability of LED PCBs enables features such as dimming, color temperature adjustment, and smart lighting systems that adapt to user preferences and environmental conditions.
Signage and Displays
LED PCBs are extensively used in signage and display applications, such as:
- Digital Billboards
- Retail Store Displays
- Wayfinding Signs
- Scoreboards
The high brightness, wide viewing angles, and dynamic color capabilities of LED PCBs make them ideal for attention-grabbing and informative displays. The modular nature of LED PCBs allows for the creation of large-scale displays by seamlessly connecting multiple panels.
Wearable Electronics
LED PCBs have found their way into wearable electronics, offering unique lighting features in:
- Smartwatches
- Fitness Trackers
- Safety Clothing
- Fashion Accessories
The use of flexible PCBs and miniaturized LEDs enables the integration of lighting into wearable devices without compromising comfort or style. LED PCBs in wearable electronics can provide visual notifications, enhance visibility in low-light conditions, or simply add a decorative element to the device.
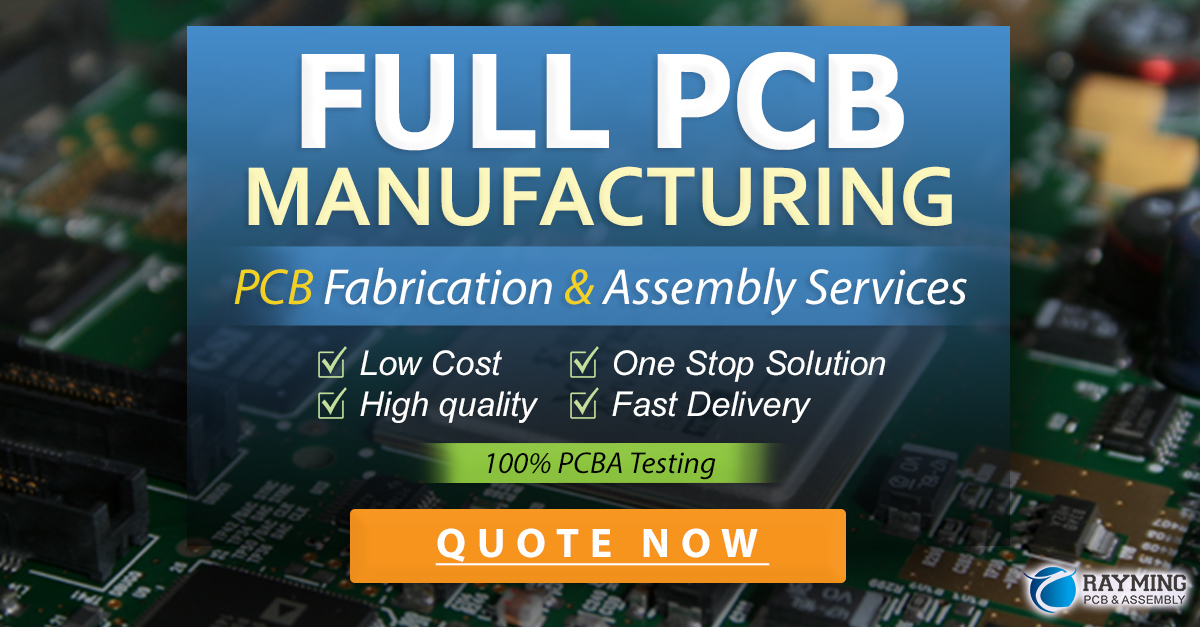
Designing LED PCBs
Thermal Management
One of the most critical aspects of LED PCB design is proper thermal management. Although LEDs are highly efficient, they still generate heat that must be dissipated to maintain optimal performance and longevity. Poor thermal management can lead to reduced light output, color shifts, and premature failure of the LEDs.
To effectively manage heat, designers must consider:
- PCB Material: Using materials with high thermal conductivity, such as Aluminum PCBs or metal core PCBs (MCPCBs), can greatly improve heat dissipation.
- Thermal Vias: Incorporating thermal vias, which are conductive paths through the PCB layers, helps transfer heat from the LEDs to the other side of the board or to an external heat sink.
- Heat Sinks: Attaching heat sinks to the PCB or using the PCB itself as a heat sink can significantly enhance heat dissipation.
- Airflow: Ensuring adequate airflow around the LED PCB, either through natural convection or forced air cooling, helps remove heat from the system.
Current Regulation
LEDs are current-driven devices, meaning that their brightness and color are directly related to the amount of current flowing through them. Overdriving LEDs with excessive current can lead to reduced lifespan or even immediate failure. Therefore, proper current regulation is essential in LED PCB design.
Current limiting resistors are the most basic form of current regulation. They are connected in series with the LEDs and limit the current flowing through them based on Ohm’s law. However, for more precise control and efficiency, designers often use dedicated LED drivers. These drivers provide constant current to the LEDs, ensuring stable brightness and color consistency.
Layout Considerations
The layout of an LED PCB plays a crucial role in its performance and functionality. Some key layout considerations include:
- LED Placement: Arrange LEDs in a way that promotes uniform light distribution and avoids shadowing effects. Consider the viewing angle and intensity of the chosen LEDs.
- Trace Routing: Ensure that the copper traces connecting the LEDs are wide enough to handle the required current without excessive voltage drop. Use thicker traces for high-current applications.
- Electromagnetic Interference (EMI): LEDs can generate high-frequency noise that may interfere with other electronic components. Proper grounding, shielding, and filtering techniques help minimize EMI.
- Mounting Holes: Include mounting holes in the PCB design to facilitate secure attachment to the enclosure or heat sink.
Table: LED PCB Design Checklist
Design Aspect | Considerations |
---|---|
Thermal Management | – PCB Material – Thermal Vias – Heat Sinks – Airflow |
Current Regulation | – Current Limiting Resistors – LED Drivers |
Layout | – LED Placement – Trace Routing – EMI Reduction – Mounting Holes |
Component Selection | – LED Type and Package – Driver Compatibility – Quality and Reliability |
Manufacturing | – PCB Fabrication Specifications – Assembly Requirements |
Testing and Validation | – Electrical Testing – Optical Testing – Environmental Testing |
Manufacturing LED PCBs
Once the LED PCB design is complete, it needs to be manufactured. The manufacturing process involves several steps:
- PCB Fabrication:
- The PCB design files are sent to a PCB manufacturer, who creates the physical board based on the provided specifications.
- The manufacturer starts with a bare substrate, typically FR-4 or aluminum, and applies a layer of copper to both sides.
- The copper is then patterned using photolithography and etching processes to create the desired traces and pads.
-
Additional layers, such as solder mask and silkscreen, are applied to protect the traces and provide assembly guidance.
- The fabricated PCB is populated with the required components, including LEDs, resistors, capacitors, and drivers.
- Surface mount components, like SMD LEDs, are placed using automated pick-and-place machines and then soldered using reflow ovens.
- Through-hole components are inserted manually or by machines and soldered using wave soldering or selective soldering processes.
-
Quality control checks are performed to ensure proper component placement and soldering.
-
Testing and Validation:
- The assembled LED PCBs undergo various tests to verify their functionality and performance.
- Electrical tests check for shorts, opens, and proper connectivity between components.
- Optical tests measure light output, color consistency, and viewing angles to ensure they meet the specified requirements.
- Environmental tests, such as temperature cycling and humidity exposure, are conducted to validate the PCB’s reliability and durability.
Frequently Asked Questions (FAQ)
- What are the benefits of using LED PCBs over traditional lighting solutions?
-
LED PCBs offer numerous benefits, including higher energy efficiency, longer lifespan, greater design flexibility, wider color options, and lower long-term costs compared to traditional lighting solutions.
-
How do I choose the right LED PCB for my application?
-
When selecting an LED PCB, consider factors such as the required light output, color, viewing angle, power consumption, and environmental conditions. Consult with LED PCB manufacturers or experienced designers to determine the best solution for your specific application.
-
Can LED PCBs be customized to fit my specific requirements?
-
Yes, LED PCBs can be customized in terms of size, shape, LED arrangement, and control features. Many LED PCB manufacturers offer design services to help create a solution tailored to your unique needs.
-
How do I ensure proper thermal management in my LED PCB design?
-
To ensure effective thermal management, consider using PCB materials with high thermal conductivity, incorporating thermal vias, attaching heat sinks, and providing adequate airflow around the PCB. Conduct thermal simulations and tests to validate the design’s thermal performance.
-
What are the key considerations when designing an LED PCB layout?
- When designing an LED PCB layout, consider factors such as LED placement for uniform light distribution, trace routing for optimal current handling, EMI reduction techniques, and the inclusion of mounting holes for secure attachment. Follow best practices and guidelines provided by LED manufacturers and PCB design resources.
Conclusion
LED PCBs have revolutionized the lighting industry, offering numerous benefits over traditional lighting solutions. Their high efficiency, long lifespan, design flexibility, and controllability make them suitable for a wide range of applications, from automotive lighting to general illumination, signage, and wearable electronics.
Designing LED PCBs requires careful consideration of thermal management, current regulation, and layout optimization. Proper thermal management ensures optimal LED performance and longevity, while current regulation maintains consistent brightness and color. A well-designed layout promotes uniform light distribution, minimizes EMI, and facilitates manufacturing and assembly.
The manufacturing process of LED PCBs involves PCB fabrication, assembly, and thorough testing to ensure functionality, reliability, and adherence to specified requirements. Close collaboration between designers, manufacturers, and end-users is essential for creating successful LED PCB solutions.
As LED technology continues to advance, LED PCBs are expected to find new applications and enable even more innovative lighting solutions. By understanding the fundamentals of LED PCBs and staying updated with the latest trends and best practices, designers and engineers can create efficient, reliable, and visually appealing lighting solutions that meet the evolving needs of various industries.
Leave a Reply