Introduction to Kapton PCB
Kapton PCB, also known as polyimide PCB, is a type of printed circuit board that utilizes Kapton as the base material. Kapton is a polyimide film developed by DuPont that possesses exceptional thermal, mechanical, and electrical properties. These characteristics make Kapton PCBs ideal for applications that demand high performance and reliability in challenging environments.
What is Kapton?
Kapton is a polyimide film that was introduced by DuPont in the late 1960s. It is a synthetic polymer that is produced by condensation of pyromellitic dianhydride and 4,4′-oxydianiline. The resulting material is a golden-colored film that exhibits outstanding properties, including:
– High thermal stability (up to 400°C)
– Excellent mechanical strength and flexibility
– Superior electrical insulation
– Resistance to chemicals and radiation
Advantages of Kapton PCB
Kapton PCBs offer several advantages over traditional PCB materials, such as FR-4. Some of the key benefits include:
1. High Temperature Resistance: Kapton PCBs can withstand temperatures up to 400°C, making them suitable for high-temperature applications like aerospace and automotive industries.
2. Flexibility: The flexibility of Kapton allows for the creation of flexible and bendable PCBs, which are essential for wearable electronics and compact designs.
3. Excellent Electrical Insulation: Kapton has a high dielectric strength and low dielectric constant, providing superior electrical insulation properties.
4. Mechanical Strength: Despite its flexibility, Kapton possesses high tensile strength and tear resistance, ensuring the durability of Kapton PCBs.
5. Chemical and Radiation Resistance: Kapton PCBs can withstand exposure to various chemicals and radiation, making them suitable for harsh environments.
Manufacturing Process of Kapton PCB
The manufacturing process of Kapton PCBs is similar to that of traditional PCBs, with a few key differences. The process typically involves the following steps:
1. Substrate Preparation
The Kapton film is cut to the desired size and shape, and any necessary pre-treatment, such as cleaning or surface modification, is performed.
2. Copper Cladding
A thin layer of copper is laminated onto the Kapton substrate using heat and pressure. The copper layer can be applied to one or both sides of the substrate, depending on the PCB design.
3. Photoresist Application
A photoresist layer is applied to the copper-clad Kapton substrate. The photoresist is a light-sensitive material that will be used to transfer the circuit pattern onto the copper layer.
4. Exposure and Development
The PCB design is transferred onto the photoresist layer using UV light exposure. The exposed areas of the photoresist are then removed using a developer solution, revealing the underlying copper layer.
5. Etching
The exposed copper layer is etched away using a chemical solution, leaving only the desired circuit pattern on the Kapton substrate.
6. Photoresist Removal
The remaining photoresist layer is removed using a stripping solution, exposing the final circuit pattern on the Kapton PCB.
7. Drilling and Plating
Holes are drilled through the Kapton PCB for component mounting and interconnections. The holes are then plated with copper to ensure electrical continuity.
8. Solder Mask and Silkscreen
A solder mask layer is applied to the Kapton PCB to protect the copper traces and prevent short circuits. A silkscreen layer is then added to provide component labels and other markings.
Applications of Kapton PCB
Kapton PCBs find applications in various industries due to their unique properties. Some of the common applications include:
Aerospace and Aviation
Kapton PCBs are extensively used in the aerospace and aviation industries due to their ability to withstand extreme temperatures and mechanical stresses. They are used in:
– Satellite communication systems
– Avionics
– Radar systems
– Space exploration equipment
Automotive Electronics
The high-temperature resistance and flexibility of Kapton PCBs make them ideal for automotive electronics applications, such as:
– Engine control units (ECUs)
– Transmission control modules
– Sensor systems
– Infotainment systems
Medical Devices
Kapton PCBs are used in medical devices that require biocompatibility, reliability, and resistance to sterilization processes. Examples include:
– Implantable devices
– Diagnostic equipment
– Surgical instruments
– Wearable health monitors
Industrial Equipment
Kapton PCBs are employed in industrial equipment that operates in harsh environments, such as:
– Oil and gas exploration
– Chemical processing plants
– Power generation facilities
– Robotics and automation systems
Consumer Electronics
The flexibility and durability of Kapton PCBs make them suitable for consumer electronics applications, such as:
– Wearable devices
– Smartphones and tablets
– Flexible displays
– Smart clothing
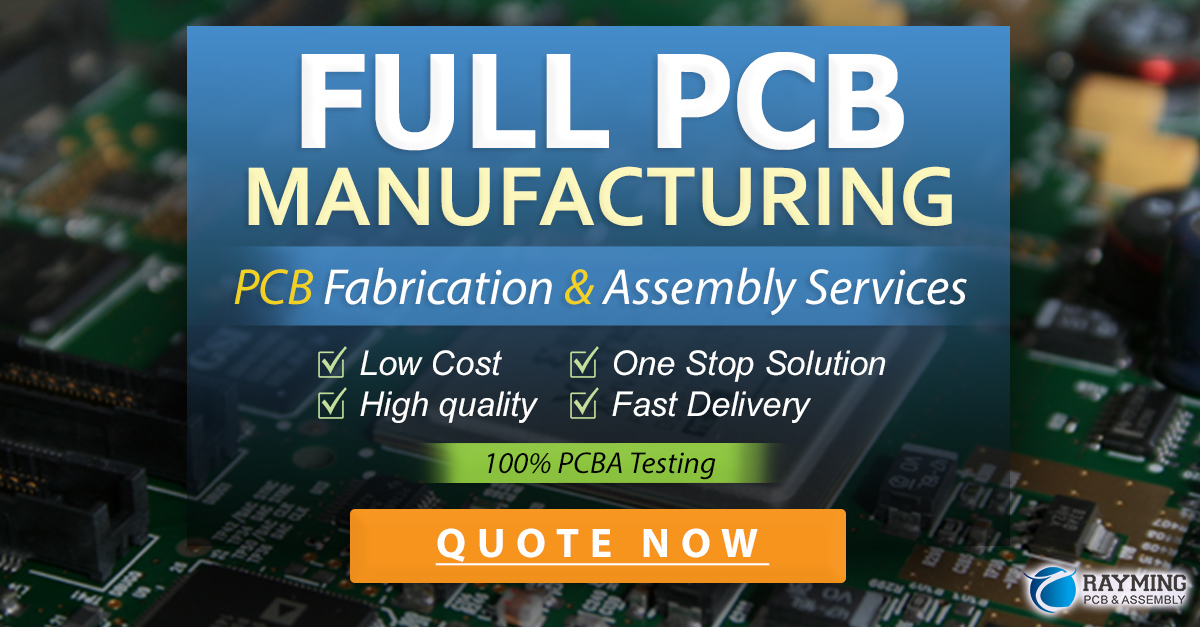
Designing with Kapton PCB
When designing Kapton PCBs, several factors need to be considered to ensure optimal performance and reliability.
Material Selection
Choosing the appropriate Kapton film thickness and copper weight is crucial for the PCB’s mechanical and electrical properties. Common Kapton film thicknesses range from 25 µm to 125 µm, while copper weights vary from 17 µm to 70 µm.
Circuit Layout
Designing the circuit layout for Kapton PCBs requires careful consideration of the material’s properties. Factors such as minimum trace width, spacing, and bend radius should be taken into account to ensure the PCB’s integrity and functionality.
Thermal Management
Although Kapton has excellent thermal stability, proper thermal management is still essential to ensure the longevity and performance of the PCB. Techniques such as using thermal vias, heat sinks, and active cooling can be employed to dissipate heat effectively.
Flexibility and Bending
When designing flexible Kapton PCBs, it is important to consider the bending requirements and the PCB’s intended use. The circuit layout should be optimized to minimize stress on components and traces during bending, and the appropriate bend radius should be maintained to prevent damage.
Connector and Component Selection
Selecting the right connectors and components for Kapton PCBs is crucial for ensuring reliable connections and performance. Factors such as temperature ratings, mechanical stability, and compatibility with the Kapton substrate should be considered when making component choices.
Comparison with Other PCB Materials
Kapton PCBs offer unique advantages compared to other common PCB materials. The following table provides a comparison of Kapton with FR-4 and polyester:
Property | Kapton | FR-4 | Polyester |
---|---|---|---|
Max. Operating Temperature | 400°C | 130°C | 105°C |
Dielectric Constant | 3.5 | 4.7 | 3.2 |
Dielectric Strength (kV/mm) | 240 | 20 | 300 |
Tensile Strength (MPa) | 231 | 310 | 200 |
Flexibility | High | Low | High |
Chemical Resistance | High | Moderate | High |
Cost | High | Low | Moderate |
As evident from the table, Kapton PCBs excel in high-temperature performance, electrical insulation, and flexibility compared to FR-4 and polyester. However, they also come at a higher cost due to the specialized materials and manufacturing processes involved.
Challenges and Considerations
While Kapton PCBs offer numerous benefits, there are also some challenges and considerations to keep in mind when working with this material.
Cost
Kapton PCBs are generally more expensive than traditional FR-4 PCBs due to the higher cost of the Kapton film and the specialized manufacturing processes required. This can be a significant consideration for cost-sensitive applications.
Manufacturing Complexity
The manufacturing process for Kapton PCBs is more complex than that of standard PCBs. Special equipment and expertise are required to handle the Kapton material, which can lead to longer lead times and higher production costs.
Compatibility with Standard Components
Some standard electronic components may not be compatible with the high-temperature requirements of Kapton PCBs. Careful selection of components that can withstand the operating conditions is necessary to ensure the reliability of the final product.
Limited Availability
Due to the specialized nature of Kapton PCBs, not all PCB manufacturers offer this service. Finding a reliable supplier with experience in Kapton PCB fabrication can be challenging, especially for small-volume orders.
Future Trends and Developments
As technology advances, the demand for high-performance and flexible PCBs continues to grow. Some of the future trends and developments in Kapton PCB technology include:
Advancements in Materials
Ongoing research and development efforts are focused on improving the properties of Kapton and other polyimide films. This includes the development of thinner, more flexible, and higher-temperature resistant materials that can further expand the applications of Kapton PCBs.
Integration with Additive Manufacturing
The combination of Kapton PCBs with additive manufacturing techniques, such as 3D printing, opens up new possibilities for creating complex, three-dimensional circuit structures. This integration can lead to more compact, lightweight, and customizable electronic devices.
Expansion of Application Areas
As the benefits of Kapton PCBs become more widely recognized, their use is expected to expand into new application areas. This includes the development of advanced wearable electronics, implantable medical devices, and high-performance aerospace and defense systems.
Sustainable and Eco-Friendly Production
With the increasing focus on sustainability and environmental responsibility, efforts are being made to develop more eco-friendly production processes for Kapton PCBs. This includes the use of recycled materials, reduced waste generation, and the development of biodegradable polyimide films.
FAQ
1. What is the maximum operating temperature of Kapton PCBs?
Kapton PCBs can withstand temperatures up to 400°C, making them suitable for high-temperature applications in industries such as aerospace, automotive, and industrial equipment.
2. Are Kapton PCBs flexible?
Yes, one of the key advantages of Kapton PCBs is their flexibility. The Kapton film allows for the creation of flexible and bendable PCBs, which are essential for applications like wearable electronics and compact designs.
3. How does the cost of Kapton PCBs compare to traditional FR-4 PCBs?
Kapton PCBs are generally more expensive than FR-4 PCBs due to the higher cost of the Kapton film and the specialized manufacturing processes required. The cost difference can be a significant consideration for cost-sensitive applications.
4. Can standard electronic components be used with Kapton PCBs?
Some standard electronic components may not be compatible with the high-temperature requirements of Kapton PCBs. Careful selection of components that can withstand the operating conditions is necessary to ensure the reliability of the final product.
5. Are Kapton PCBs widely available from PCB manufacturers?
Due to the specialized nature of Kapton PCBs, not all PCB manufacturers offer this service. Finding a reliable supplier with experience in Kapton PCB fabrication can be challenging, especially for small-volume orders.
Conclusion
Kapton PCBs offer a unique combination of high-temperature resistance, flexibility, and excellent electrical and mechanical properties. These characteristics make them ideal for a wide range of applications in industries such as aerospace, automotive, medical devices, industrial equipment, and consumer electronics.
However, working with Kapton PCBs also presents some challenges, such as higher costs, manufacturing complexity, and limited availability. As technology continues to advance, ongoing research and development efforts are focused on improving the properties of Kapton and expanding its application areas.
By understanding the advantages, limitations, and design considerations of Kapton PCBs, engineers and designers can leverage this technology to create innovative, high-performance electronic devices that can withstand the most demanding environments.
Leave a Reply