Flexible printed circuit boards (flex PCBs) have become increasingly popular in recent years due to their versatility and ability to bend and flex to fit into tight spaces. However, some wonder if the benefits of flex PCBs come at too high of a cost. In this article, we’ll examine the costs associated with flex PCBs and look at whether they are truly more expensive than rigid PCBs.
What is a Flex PCB?
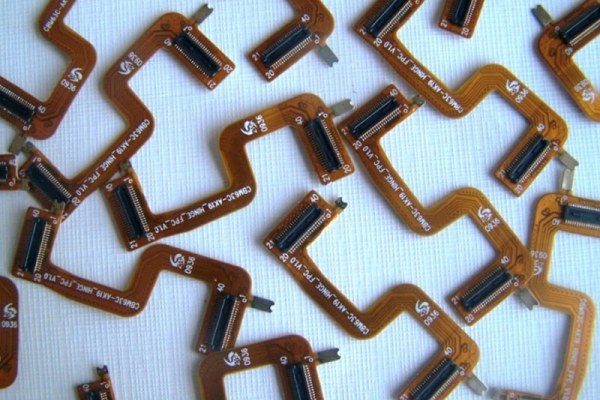
A flex PCB is a printed circuit board that is made of a flexible insulating substrate material such as polyimide or polyester. The conductive traces are printed or laminated onto this flexible base, allowing the board to bend and flex without damaging the traces.
Flex PCBs are ideal for applications where the circuit board needs to move or conform to a particular shape. Common uses include:
- Wearable devices
- Medical devices
- Consumer electronics
- Automotive electronics
- Aerospace and military products
Compared to rigid PCBs, flex PCBs provide:
- Increased reliability and durability under bending and flexing forces
- Ability to fold and fit into tight spaces
- Reduced weight and size
- Lower installation costs
Cost Factors for Flex PCBs
When considering the costs of flex PCBs, it’s important to understand the various factors that contribute to the overall price:
Substrate Material
The flexible substrate material is generally more expensive than the rigid FR-4 material used for most PCBs. Polyimide is the most common flexible substrate and costs range from $20-100 per square foot.
Layer Count
Adding more conductive layers increases costs significantly. 2-layer flex boards are the most affordable, while costs rise steadily for 4, 6, and 8-layer configurations.
Conductor Thickness
Flex PCB tracks are usually thinner than standard PCBs. Typical thicknesses range from 0.5-3.0 mils. Thicker copper layers up to 5 mils are available but increase cost.
Board Size
As with rigid PCBs, larger flex boards that occupy more panel space come at a higher price. Maximum panel sizes for flex PCBs are generally around 18″ x 24″.
Bend Radius
The smallest bend radius a flex board can tolerate largely depends on the substrate material. Smaller bend radii require special treatment during manufacturing and thus increase cost.
Stiffener Layers
Adding stiffener layers to maintain part of the board in a rigid state also adds cost. These provide rigidity where needed while allowing other areas to flex.
Shielding
In some cases, shielding is needed on flex PCBs. This can be done with metal layers or conductive polymers at an additional expense.
Secondary Operations
Common secondary operations like routing, scoring, depaneling, and overmolding can drive up the costs when ordering flex PCBs. The complexity and number of these steps impacts the price.
Volume
As is standard for PCB assembly, higher order volumes bring the price per unit down considerably for flex boards. Prototyping or small batch orders of just a few boards can increase the price per board significantly.
Testing
Testing and inspecting flex PCBs requires specialized fixtures and equipment to handle the flexible boards without damage. This extra process increases costs.
Cost Comparison to Rigid PCBs
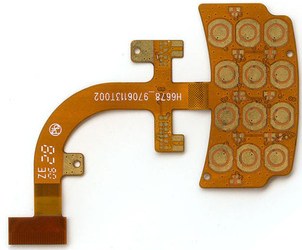
With all of these cost variables at play, how do flex PCBs stack up against standard rigid boards in terms of overall price?
In general, flex PCBs carry a 15-20% premium over rigid boards using a like-for-like comparison. Here are some examples:
Board Type | Layers | Size | Qty | Rigid PCB Cost | Flex PCB Cost | % Increase |
---|---|---|---|---|---|---|
Prototype | 2 | 4″ x 6″ | 5 boards | $160 | $200 | 25% |
Medium Volume | 4 | 6″ x 8″ | 50 boards | $850 | $1,000 | 18% |
High Volume | 6 | 10″ x 12″ | 500 boards | $4,500 | $5,400 | 20% |
However, the additional design freedom and space savings afforded by flex PCBs can often offset their higher cost. When factoring in downstream assembly and installation costs, flex PCBs may actually provide overall savings in many cases.
Manufacturers recommend involving your flex PCB partner early in the design process to maximize cost benefits. Their expertise can help optimize the flex board design and manufacturability.
When do Flex PCBs Make Sense Despite the Cost?
Despite their premium cost, there are many situations where the benefits of flex PCBs easily justify their expense:
- Tight spaces: When space constraints are an issue, flex PCBs can flex and fold to fit. A rigid board may not be usable in these situations regardless of the cost savings.
- Moving parts: For mechanisms involving hinges, sliding, or other moving parts, rigid boards quickly succumb to cracking and failure. Flex boards are sturdier under dynamic bending and flexing stresses.
- Weight reductions: Removing wires and connectors by integrating flex PCBs directly into assemblies provides dramatic weight reduction. This is critical in aerospace, aviation, and satellite applications.
- Simplified assembly: Because they fit into tight spaces and move dynamically, flex PCBs can eliminate mechanical assemblies, connectors, and wires. The resulting lower assembly costs can completely offset the higher board cost.
- Reliability: The durability and flex life of polyimide and other flexible substrates exceed what is possible with rigid boards. For mission-critical electronics, reliability is far more important than saving money on the PCB itself.
For many engineers, the design freedom and problem solving abilities enabled by flex PCBs are worth the premium price of admission. When used appropriately, any higher procurement costs are recouped further down the product development lifecycle.
Flex PCB Cost Reduction Tips
While flex PCB costs may be unavoidably higher for advanced, high-reliability applications, here are some tips for reining in costs when possible:
- Partner early: Work with your flex PCB provider early in the design stage to optimize manufacturing processes and panel utilization.
- Minimize layers: Stick to 2 layers if possible. Move to 4 layers only when routing space becomes too tight.
- Use standardized materials: Select substrate, coverlay, and copper thicknesses from the vendor’s standard offerings. Custom materials increase costs.
- Design panels efficiently: Optimize board sizes and layout on the panel to maximize material utilization and minimize waste.
- Build in volume: The economies of scale for larger orders are substantial. Plan for volume manufacturing even for early prototyping when feasible.
- Simplify testing: Modify designs to enable simple continuity tests rather than complex flying probe or fixture-based testing when reasonable.
- Eliminate stiffeners: Avoid stiffener layers unless absolutely required as they add multiple fabrication steps.
With attention to these design and process considerations, flex PCB assemblies can deliver extreme space, weight, and reliability advantages while remaining cost competitive with alternative solutions.
FQA
What are the main factors that affect the cost of flex PCBs?
The main cost factors are: substrate material, number of conductive layers, conductor thickness, board size, bend radius, stiffeners, shielding, secondary operations like routing and scoring, order volume, and testing complexity.
Does the flexibility of flex PCBs justify their higher cost compared to rigid PCBs?
Yes, the flexibility and durability of flex PCBs provide unique advantages in space-constrained designs, dynamic assemblies, and high reliability applications that often offset their higher procurement costs.
In what applications are flex PCBs indispensable, despite their cost premium?
Flex PCBs are indispensable in very tight spaces where a rigid board won’t fit, in applications with moving parts that requires dynamic flexing, when major weight reduction is critical, and in mission-critical electronics where superior reliability is worth the cost.
What are some tips for lowering the cost of your flex PCB design?
Tips for lower cost include: involve your flex PCB vendor early in the design, minimize the number of conductive layers, use only standard materials, efficiently layout boards on panels, build early prototypes in high volume, simplify testing requirements, and eliminate stiffeners if possible.
Can the long-term savings from easier assembly and installation offset the higher cost of the flex boards themselves?
Yes, by reducing mechanical assemblies, connectors, and wiring, flex PCBs can greatly simplify downstream production processes in many cases. The resulting labor and inventory savings over the product lifecycle can more than offset the initial board fabrication costs.
Leave a Reply