What are IPC Standards?
IPC (Association Connecting Electronics Industries) is a global trade association that develops standards for the electronic interconnection industry. IPC standards are widely recognized and adopted worldwide, ensuring consistency, reliability, and quality in the manufacturing of electronic products.
These standards cover various aspects of the electronics industry, including:
– Design
– Materials
– Assembly processes
– Testing
– Quality control
IPC standards are essential for manufacturers, suppliers, and customers in the electronics industry to communicate effectively and maintain a high level of quality and reliability.
Why are IPC Standards Important?
IPC standards play a crucial role in the electronics industry for several reasons:
-
Consistency: IPC standards ensure that electronic products are manufactured consistently, regardless of the location or the company producing them. This consistency helps in maintaining the quality and reliability of the products.
-
Quality: By adhering to IPC standards, manufacturers can produce high-quality electronic products that meet the required specifications and performance criteria.
-
Reliability: IPC standards help in improving the reliability of electronic products by providing guidelines for materials, processes, and testing methods.
-
Cost-effectiveness: Implementing IPC standards can help manufacturers reduce costs by minimizing errors, rework, and scrap, thereby improving efficiency and productivity.
-
Global acceptance: IPC standards are recognized and adopted worldwide, making it easier for manufacturers to enter new markets and collaborate with international partners.
Key IPC Standards
There are numerous IPC standards covering different aspects of the electronics industry. Some of the most important and widely used standards include:
IPC-A-610: Acceptability of Electronic Assemblies
IPC-A-610 is a widely recognized standard that provides acceptance criteria for the manufacture of electronic assemblies. It covers various aspects of the assembly process, including:
– Soldering
– Component placement
– Mechanical assembly
– Cleanliness
The standard defines three classes of production, each with its own set of acceptance criteria:
– Class 1: General Electronic Products
– Class 2: Dedicated Service Electronic Products
– Class 3: High Performance Electronic Products
Class | Description | Examples |
---|---|---|
1 | Includes products suitable for applications where the major requirement is the function of the completed assembly. | Consumer electronics, toys, low-end appliances |
2 | Includes products where continued performance and extended life are required, and for which uninterrupted service is desired but not critical. | Computers, communication equipment, industrial controls |
3 | Includes products where continued high performance or performance-on-demand is critical, equipment downtime cannot be tolerated, and the end-use environment may be uncommonly harsh. | Aerospace, medical devices, military equipment |
IPC-A-600: Acceptability of Printed Boards
IPC-A-600 is a standard that provides acceptance criteria for printed circuit boards (PCBs). It covers various aspects of PCB manufacturing, including:
– Visual examination
– Dimensional requirements
– Workmanship
– Material requirements
The standard defines three classes of production, similar to IPC-A-610:
– Class 1: General Electronic Products
– Class 2: Dedicated Service Electronic Products
– Class 3: High Performance Electronic Products
IPC-J-STD-001: Requirements for Soldered Electrical and Electronic Assemblies
IPC-J-STD-001 is a standard that provides requirements for the manufacture of soldered electrical and electronic assemblies. It covers various aspects of the soldering process, including:
– Materials
– Methods
– Verification
– Quality assurance
The standard also defines three classes of production, similar to IPC-A-610 and IPC-A-600.
IPC-7711/7721: Rework, Modification and Repair of Electronic Assemblies
IPC-7711/7721 is a standard that provides guidelines for the rework, modification, and repair of electronic assemblies. It covers various aspects of the process, including:
– Removal and replacement of components
– Modification of printed boards
– Repair of damaged conductors and laminate
– Cleaning and inspection
The standard aims to ensure that rework, modification, and repair processes do not compromise the quality and reliability of the electronic assembly.
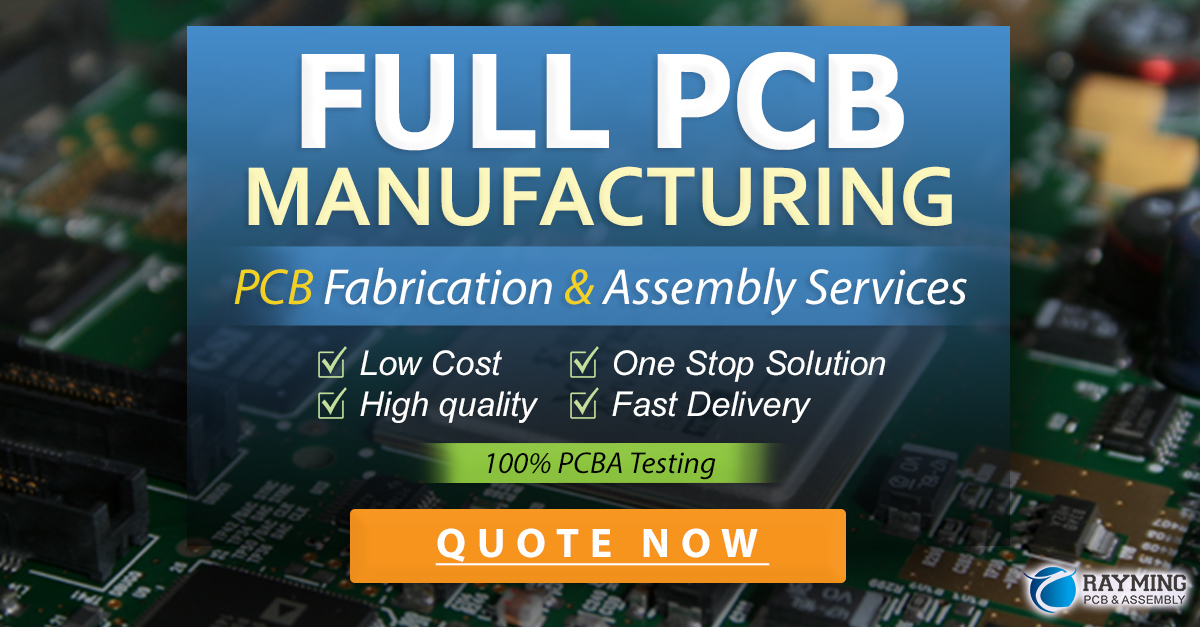
Implementing IPC Standards
Implementing IPC standards in an electronics manufacturing facility involves several steps:
-
Training: Ensure that all personnel involved in the manufacturing process are trained and certified in the relevant IPC standards.
-
Equipment and materials: Use equipment and materials that comply with the requirements specified in the IPC standards.
-
Process control: Implement process controls to ensure that the manufacturing processes are consistent and meet the requirements of the IPC standards.
-
Inspection and testing: Conduct regular inspections and tests to verify that the products meet the acceptance criteria defined in the IPC standards.
-
Documentation: Maintain proper documentation of the manufacturing processes, materials, and test results to demonstrate compliance with the IPC standards.
Benefits of IPC Certification
IPC certification is a recognition that an individual or a company has demonstrated proficiency in a specific IPC standard. Some of the benefits of IPC certification include:
-
Improved quality: IPC-certified personnel and companies are more likely to produce high-quality products that meet the requirements of the IPC standards.
-
Increased credibility: IPC certification demonstrates a commitment to quality and adherence to industry-recognized standards, which can enhance a company’s credibility and reputation.
-
Competitive advantage: IPC certification can help companies differentiate themselves from competitors and win new business opportunities.
-
Employee development: IPC certification programs provide employees with valuable skills and knowledge, which can lead to improved job performance and career advancement opportunities.
Frequently Asked Questions (FAQ)
1. Are IPC standards mandatory?
IPC standards are not mandatory by law, but they are widely recognized and adopted in the electronics industry. Many companies require their suppliers and manufacturers to adhere to IPC standards to ensure the quality and reliability of their products.
2. How often are IPC standards updated?
IPC standards are regularly reviewed and updated to keep pace with the latest technologies and industry practices. The frequency of updates varies depending on the standard and the pace of technological advancements in the specific area covered by the standard.
3. How can I obtain IPC standards?
IPC standards can be purchased directly from the IPC website (www.ipc.org) or through authorized distributors. Some standards may also be available in electronic format for download.
4. What is the difference between IPC classes?
IPC classes define different levels of acceptance criteria for electronic products based on their intended use and the criticality of their performance. Class 1 has the least stringent requirements and is suitable for general electronic products, while Class 3 has the most stringent requirements and is suitable for high-performance products where reliability is critical.
5. How do I become IPC certified?
To become IPC certified, you need to attend an IPC certification training course and pass the corresponding exam. IPC certification courses are offered by IPC-licensed training centers worldwide. You can find more information about IPC certification programs on the IPC website.
Conclusion
IPC standards play a vital role in ensuring the quality, reliability, and consistency of electronic products. By adhering to these standards, manufacturers can produce high-quality products that meet the requirements of their customers and the industry as a whole. Implementing IPC standards and obtaining IPC certification can provide numerous benefits, including improved quality, increased credibility, and a competitive advantage in the market.
As the electronics industry continues to evolve and new technologies emerge, IPC standards will remain essential in maintaining the integrity and performance of electronic products. Staying up-to-date with the latest IPC standards and best practices is crucial for professionals and companies in the electronics industry to remain competitive and deliver the best possible products to their customers.
Leave a Reply