What is Insufficient Solder?
Insufficient solder refers to a situation where there is not enough solder present to create a strong and reliable connection between electronic components and the printed circuit board (PCB). When the amount of solder is inadequate, it can lead to weak or incomplete joints, which can cause various issues in the performance and longevity of the electronic device.
Types of Insufficient Solder Joints
There are several types of insufficient solder joints that can occur:
-
Cold Joints: These joints occur when the solder does not melt completely, resulting in a dull, grainy appearance. Cold joints are weak and prone to cracking.
-
Dry Joints: Dry joints happen when there is not enough solder to create a proper connection. They are characterized by a lack of solder fillets and a matte appearance.
-
Starved Joints: Starved joints are similar to dry joints, but they have a small amount of solder present. However, the solder is not sufficient to create a strong and reliable connection.
-
Incomplete Joints: Incomplete joints occur when the solder does not cover the entire joint area, leaving gaps or voids.
Causes of Insufficient Solder
Several factors can contribute to insufficient solder during the soldering process:
Incorrect Solder Amount
One of the primary causes of insufficient solder is using an incorrect amount of solder. If too little solder is applied, it will not be enough to create a strong and reliable joint. On the other hand, applying too much solder can lead to bridging or short circuits.
Improper Soldering Technique
Improper soldering technique can also result in insufficient solder. If the soldering iron is not applied correctly or for the right duration, it can cause the solder to not melt completely or flow properly, leading to weak joints.
Contamination
Contamination on the PCB or component surfaces can prevent the solder from adhering properly. Dirt, grease, or oxidation can create a barrier between the solder and the surfaces, resulting in insufficient solder joints.
Incorrect Temperature
Using the wrong temperature during the soldering process can also contribute to insufficient solder. If the temperature is too low, the solder may not melt completely, leading to cold joints. Conversely, if the temperature is too high, it can cause the solder to oxidize or burn off, resulting in insufficient solder.
Preventing Insufficient Solder
To minimize the occurrence of insufficient solder, consider the following preventive measures:
Use the Right Amount of Solder
Ensure that you are using the appropriate amount of solder for each joint. The amount of solder needed depends on the size of the components and the PCB pads. As a general rule, the solder joint should have a concave shape, with the solder covering the entire joint area.
Maintain Proper Soldering Technique
Practice proper soldering technique to ensure consistent and reliable solder joints. Hold the soldering iron at a 45-degree angle to the joint and apply heat to both the component lead and the PCB pad simultaneously. Allow the solder to melt and flow around the joint, creating a smooth and shiny finish.
Keep Surfaces Clean
Before soldering, clean the PCB and component surfaces to remove any contaminants that may hinder solder adhesion. Use a suitable cleaning solution, such as isopropyl alcohol, and a lint-free cloth to wipe the surfaces clean.
Use the Correct Temperature
Set your soldering iron to the appropriate temperature for the type of solder you are using. Most lead-free solders require a higher melting temperature compared to leaded solders. Consult the solder manufacturer’s specifications for the recommended temperature range.
Perform Visual Inspection
After soldering, perform a visual inspection of each joint to ensure that there is sufficient solder coverage. Use a magnifying glass or microscope to check for any gaps, voids, or inconsistencies in the solder joints.
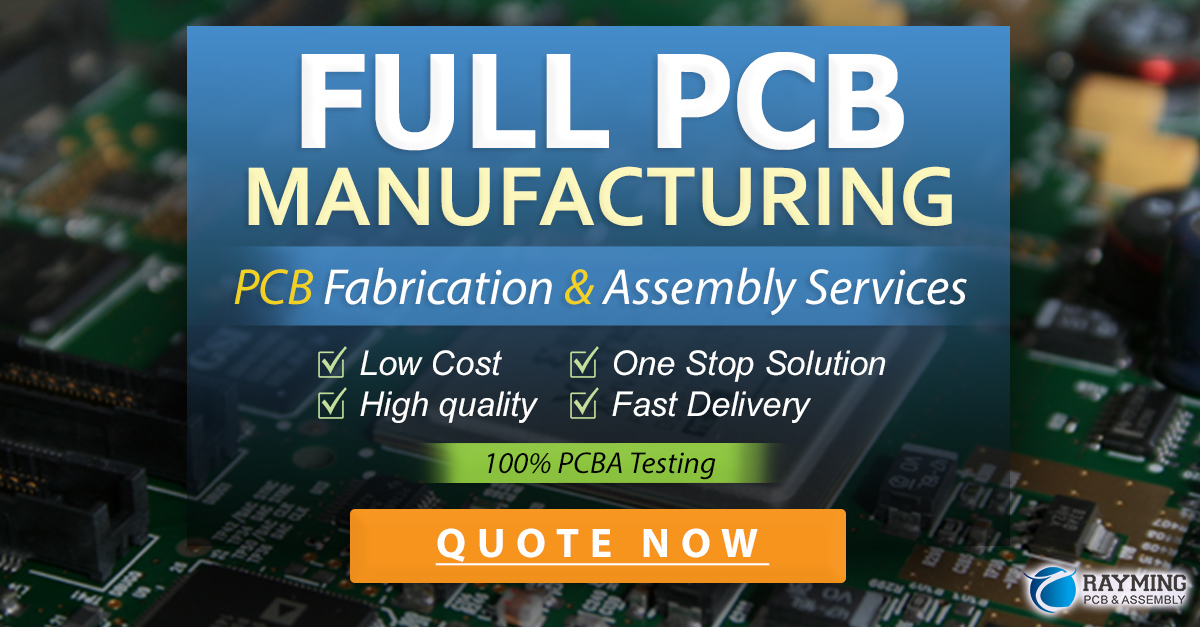
Fixing Insufficient Solder
If you encounter insufficient solder joints during the manufacturing process, there are several steps you can take to fix the problem:
Rework the Joint
To fix an insufficient solder joint, you can rework the joint by applying additional solder. First, remove any existing solder using a desoldering tool, such as a solder sucker or desoldering braid. Clean the joint area thoroughly, then reapply solder using the proper technique and amount.
Use Flux
Applying flux to the joint before reworking can help improve solder flow and adhesion. Flux removes oxidation and promotes better wetting of the solder to the surfaces. Choose a suitable flux type based on the solder and PCB materials.
Consider Solder Paste
For surface mount components, using solder paste can help ensure sufficient solder coverage. Solder paste is a mixture of solder particles suspended in flux. Apply the paste to the PCB pads using a stencil or syringe, then place the components and reflow the solder using a controlled heating process.
Implement Quality Control Measures
To catch insufficient solder issues early, implement quality control measures throughout the manufacturing process. This can include automated optical inspection (AOI) systems, X-ray inspection, or manual visual inspection at various stages of production.
Consequences of Insufficient Solder
Insufficient solder can have several negative consequences on the performance and reliability of electronic devices:
Poor Electrical Conductivity
Insufficient solder leads to weak or incomplete connections, which can result in poor electrical conductivity. This can cause intermittent failures, signal distortion, or complete loss of functionality in the affected circuit.
Mechanical Weakness
Solder joints with insufficient solder are mechanically weak and prone to cracking or breaking under stress. This can occur due to vibration, thermal expansion, or physical handling of the device. Broken solder joints can cause open circuits and device failure.
Increased Resistance
Insufficient solder can increase the electrical resistance of the joint, leading to voltage drops and power dissipation. This can affect the overall performance and efficiency of the electronic device.
Reduced Lifespan
Electronic devices with insufficient solder joints are more likely to experience premature failure. The weak and unstable connections can deteriorate over time, leading to a shorter lifespan of the device compared to one with proper solder joints.
FAQ
-
Q: How can I tell if a solder joint has insufficient solder?
A: Insufficient solder joints often appear dull, grainy, or incomplete. They may lack proper solder fillets or have gaps or voids in the solder coverage. Visual inspection using a magnifying glass or microscope can help identify insufficient solder joints. -
Q: Can insufficient solder cause intermittent failures in electronic devices?
A: Yes, insufficient solder can lead to intermittent failures. The weak and unstable connections can cause temporary loss of contact, resulting in intermittent functionality issues in the affected circuit. -
Q: Is it possible to fix insufficient solder joints without removing the component?
A: In some cases, it may be possible to fix insufficient solder joints without removing the component. This can be done by applying additional solder and flux to the joint and using a soldering iron to reflow the solder. However, if the joint is severely compromised, it may be necessary to remove the component and start over. -
Q: Can using too much solder cause problems?
A: Yes, using too much solder can also cause issues. Excessive solder can lead to bridging between adjacent pins or pads, causing short circuits. It can also make the joint more susceptible to cracking under thermal stress due to the larger solder mass. -
Q: How important is cleaning the surfaces before soldering?
A: Cleaning the PCB and component surfaces before soldering is crucial for achieving good solder joints. Contaminants such as dirt, grease, or oxidation can prevent the solder from adhering properly, leading to insufficient solder joints. Always ensure that the surfaces are clean and free of contaminants before soldering.
Conclusion
Insufficient solder is a common issue in electronics manufacturing that can have significant consequences on the performance and reliability of electronic devices. Understanding the causes, prevention, and correction of insufficient solder is essential for ensuring the production of high-quality and robust electronic products.
By using the right amount of solder, maintaining proper soldering technique, keeping surfaces clean, using the correct temperature, and implementing quality control measures, you can minimize the occurrence of insufficient solder joints. If insufficient solder is detected, prompt rework and repair can help salvage the affected joints and prevent further issues down the line.
Investing time and effort into preventing and addressing insufficient solder will ultimately lead to improved product quality, reduced rework costs, and enhanced customer satisfaction in the competitive world of electronics manufacturing.
Leave a Reply