What is an Aluminum PCB?
An aluminum PCB is a printed circuit board that uses aluminum as the base material instead of the more commonly used FR-4 fiberglass. The aluminum substrate provides excellent thermal conductivity, allowing heat to dissipate quickly from the components mounted on the PCB. This makes Aluminum PCBs ideal for applications that generate significant amounts of heat, such as high-power LED lighting, motor controllers, and power electronics.
Advantages of Aluminum PCBs
Aluminum PCBs offer several advantages over traditional FR-4 PCBs:
- Excellent thermal conductivity
- High mechanical strength and durability
- Lightweight construction
- Good electrical insulation properties
- Resistance to moisture and chemicals
These properties make aluminum PCBs suitable for a wide range of applications, especially those that require efficient heat dissipation and rugged construction.
Aluminum PCB Construction
Aluminum PCBs are typically constructed using a lamination process. The basic structure consists of a layer of dielectric material, such as polyimide or epoxy, bonded to an aluminum substrate. Copper foil is then laminated onto the dielectric layer to form the conductive circuit pattern. The thickness of the dielectric layer and copper foil can vary depending on the specific application requirements.
Aluminum Substrate Thickness
The thickness of the aluminum substrate is an important consideration in the design of aluminum PCBs. Thicker substrates provide better thermal conductivity and mechanical strength, but they also increase the overall weight and cost of the PCB. The following table shows some common aluminum substrate thicknesses and their typical applications:
Thickness (mm) | Typical Applications |
---|---|
0.5 – 1.0 | Low-power electronics, LED lighting |
1.0 – 2.0 | Medium-power electronics, automotive applications |
2.0 – 3.0 | High-power electronics, industrial control systems |
3.0 – 5.0 | Extreme high-power applications, power converters |
Dielectric Materials
The choice of dielectric material is another critical factor in aluminum PCB design. The dielectric layer provides electrical insulation between the aluminum substrate and the copper circuit layer. Some common dielectric materials used in aluminum PCBs include:
- Polyimide: Offers excellent thermal stability and mechanical strength
- Epoxy: Provides good electrical insulation and adhesion properties
- Ceramic: Ideal for high-temperature applications and power electronics
The dielectric material’s thermal conductivity, dielectric constant, and thickness will affect the PCB’s overall thermal performance and signal integrity.
Thermal Management with Aluminum PCBs
One of the primary reasons for using aluminum PCBs is their superior thermal management capabilities. Aluminum’s high thermal conductivity allows heat to spread quickly from the heat-generating components to the substrate, where it can be dissipated through various cooling methods.
Thermal Vias
Thermal vias are small holes drilled through the PCB that are filled with a conductive material, such as copper or silver epoxy. These vias create a thermal path between the component and the aluminum substrate, allowing heat to transfer more efficiently. The size, number, and placement of thermal vias can be optimized to improve the PCB’s overall thermal performance.
Heat Sinks and Cooling Solutions
In addition to thermal vias, aluminum PCBs can be combined with various heat sinks and cooling solutions to further enhance heat dissipation. Some common cooling methods include:
- Surface-mounted heat sinks: Attached directly to the PCB to increase the surface area for heat dissipation
- Extruded aluminum heat sinks: Provide a larger surface area and can be customized to fit specific application requirements
- Fans and forced air cooling: Used to actively remove heat from the PCB and surrounding components
- Liquid cooling: Employed in high-performance applications where extreme heat dissipation is required
The choice of cooling solution will depend on the specific application, power requirements, and environmental conditions.
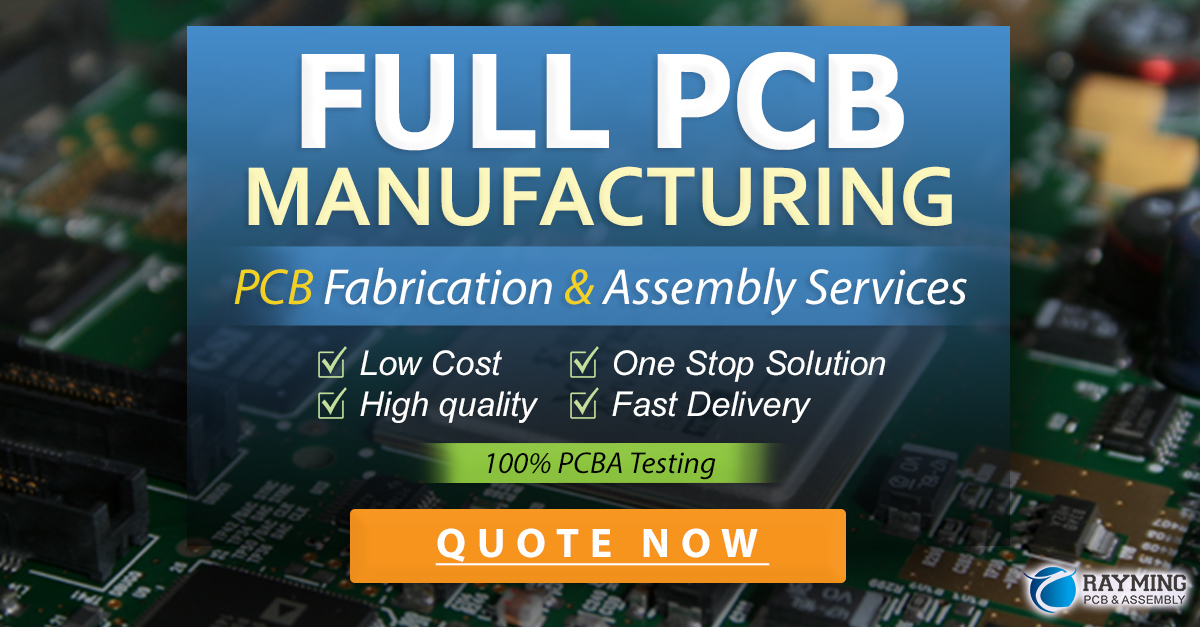
Designing with Aluminum PCBs
Designing with aluminum PCBs requires careful consideration of several factors to ensure optimal performance and reliability. Some key design considerations include:
Thermal Expansion and Stress Management
Aluminum and copper have different coefficients of thermal expansion (CTE), which can lead to mechanical stress and fatigue in the PCB during thermal cycling. To minimize this stress, designers can use several techniques, such as:
- Incorporating expansion slots and cutouts in the PCB layout
- Using flexible dielectric materials to accommodate differential expansion
- Optimizing the placement and orientation of components to reduce stress concentrations
Electrical Insulation and Grounding
The aluminum substrate in an aluminum PCB is electrically conductive, which means that proper insulation and grounding techniques must be employed to prevent short circuits and ensure signal integrity. Some strategies for managing electrical insulation and grounding include:
- Using dielectric materials with sufficient thickness and breakdown voltage ratings
- Incorporating ground planes and shielding to minimize electromagnetic interference (EMI)
- Carefully routing signal traces to avoid coupling with the aluminum substrate
Manufacturing Considerations
Aluminum PCBs require specialized manufacturing processes and equipment compared to traditional FR-4 PCBs. Some key manufacturing considerations include:
- Selecting the appropriate lamination process and parameters for bonding the dielectric layer to the aluminum substrate
- Choosing compatible soldermask and silkscreen materials that can withstand the higher processing temperatures
- Employing specialized drilling and milling techniques to create holes and cutouts in the aluminum substrate
Working closely with an experienced aluminum PCB manufacturer can help ensure that your design is optimized for manufacturability and reliability.
Applications of Aluminum PCBs
Aluminum PCBs are used in a wide range of applications across various industries. Some common applications include:
LED Lighting
Aluminum PCBs are widely used in LED lighting applications due to their excellent thermal management capabilities. They help to dissipate heat generated by high-power LED chips, improving the efficiency and lifespan of the lighting system. Aluminum PCBs also provide a sturdy mechanical base for mounting the LED components and optics.
Automotive Electronics
The automotive industry requires electronics that can withstand harsh environmental conditions, such as high temperatures, vibration, and moisture. Aluminum PCBs offer the necessary thermal management, mechanical strength, and durability for automotive applications like engine control units, power inverters, and LED headlights.
Power Electronics
Aluminum PCBs are essential for power electronics applications that generate significant amounts of heat, such as motor drives, power supplies, and solar inverters. The aluminum substrate helps to dissipate heat from power components like MOSFETs, IGBTs, and rectifiers, ensuring reliable operation and preventing premature failure.
Industrial Control Systems
Industrial control systems often operate in challenging environments with high temperatures, vibration, and electrical noise. Aluminum PCBs provide the necessary thermal management, mechanical stability, and EMI shielding for applications like programmable logic controllers (PLCs), human-machine interfaces (HMIs), and industrial sensors.
Aerospace and Defense
Aluminum PCBs are used in various aerospace and defense applications that require high reliability, ruggedness, and thermal management. Examples include avionics systems, radar modules, and satellite communication equipment. The lightweight nature of aluminum PCBs is also advantageous for weight-sensitive aerospace applications.
FAQ
1. What is the difference between an aluminum PCB and a standard FR-4 PCB?
The main difference between an aluminum PCB and a standard FR-4 PCB is the base material. Aluminum PCBs use an aluminum substrate, while FR-4 PCBs use a fiberglass-reinforced epoxy laminate. Aluminum PCBs offer superior thermal conductivity, mechanical strength, and durability compared to FR-4 PCBs, making them ideal for applications that require efficient heat dissipation and rugged construction.
2. Can aluminum PCBs be used for high-frequency applications?
While aluminum PCBs are primarily used for their thermal management properties, they can also be used in high-frequency applications with proper design considerations. The dielectric material and thickness, as well as the copper foil thickness and surface roughness, must be carefully selected to ensure good signal integrity and minimize losses at high frequencies.
3. How do I select the right aluminum substrate thickness for my application?
The choice of aluminum substrate thickness depends on several factors, including the power dissipation requirements, mechanical strength needed, and weight constraints of your application. Generally, thicker substrates provide better thermal conductivity and mechanical stability, but they also increase the PCB’s weight and cost. Consult with an experienced aluminum PCB manufacturer to determine the optimal substrate thickness for your specific application.
4. Can aluminum PCBs be soldered using standard lead-free soldering processes?
Yes, aluminum PCBs can be soldered using standard lead-free soldering processes, such as reflow soldering and wave soldering. However, it is essential to use soldermask and silkscreen materials that are compatible with the higher processing temperatures required for aluminum PCBs. Additionally, proper preheating and cooling profiles must be employed to minimize thermal stress and ensure reliable solder joints.
5. Are aluminum PCBs more expensive than traditional FR-4 PCBs?
In general, aluminum PCBs are more expensive than traditional FR-4 PCBs due to the higher cost of the aluminum substrate and the specialized manufacturing processes required. However, the total cost of ownership for an aluminum PCB solution may be lower in applications where thermal management and reliability are critical, as they can help to reduce system-level costs associated with heat sinks, fans, and maintenance.
In conclusion, aluminum PCBs offer a compelling solution for applications that demand superior thermal management, mechanical strength, and durability. By understanding the unique properties and design considerations of aluminum PCBs, engineers can create high-performance, reliable electronic systems for a wide range of industries and applications.
Leave a Reply