Introduction to Multilayer PCB Manufacturing
Multilayer PCBs are essential components in modern electronic devices, enabling the integration of complex circuitry into compact spaces. The manufacturing process of multilayer PCBs involves several stages, each requiring precision and adherence to industry standards. In this article, we will delve into the step-by-step process of manufacturing multilayer PCBs, covering everything from design to final inspection.
Understanding Multilayer PCB Structure
Before diving into the manufacturing process, it’s essential to understand the structure of a multilayer PCB. A multilayer PCB consists of multiple layers of conductive copper foil separated by insulating dielectric material. The number of layers can vary depending on the complexity of the circuit design, with common configurations ranging from 4 to 12 layers or more.
Layers | Typical Applications |
---|---|
4 | Simple devices, such as consumer electronics |
6-8 | Medium complexity devices, like industrial control systems |
10-12 | High-end devices, such as telecommunications equipment |
14+ | Extremely complex devices, including aerospace and military applications |
Benefits of Multilayer PCBs
Multilayer PCBs offer several advantages over single or double-layer boards:
- Increased circuit density: Multilayer PCBs allow for more components and traces to be packed into a smaller area.
- Improved signal integrity: The use of dedicated power and ground planes helps reduce electromagnetic interference (EMI) and crosstalk between signals.
- Enhanced thermal management: Multiple copper layers can help dissipate heat more effectively, improving the overall reliability of the device.
Multilayer PCB Manufacturing Process
Step 1: PCB Design and Preparation
The manufacturing process begins with the creation of a PCB design using specialized software, such as Altium Designer or KiCad. The design includes the placement of components, routing of traces, and the definition of layer stackups. Once the design is finalized, the following files are generated:
- Gerber files: These files contain the information needed to create the copper layers, solder mask, and silkscreen.
- Drill files: These files specify the locations and sizes of holes to be drilled in the PCB.
- Bill of Materials (BOM): This list contains all the components required for the assembly of the PCB.
Step 2: Inner Layer Fabrication
The inner layers of the multilayer PCB are fabricated using a process called photolithography. Here’s a breakdown of the steps involved:
- Copper-clad laminate sheets are cleaned and coated with a light-sensitive photoresist.
- The photoresist is exposed to UV light through a photomask, which contains the desired circuit pattern for the specific layer.
- The exposed photoresist is developed, revealing the copper that needs to be etched away.
- The unwanted copper is removed using a chemical etching process, leaving behind the desired circuit pattern.
- The remaining photoresist is stripped away, and the inner layers are inspected for accuracy.
Step 3: Lamination
Once the inner layers are fabricated, they are stacked together with insulating dielectric material (prepreg) between each layer. Copper foil is added to the top and bottom of the stack to form the outer layers. The stack is then subjected to high pressure and heat in a lamination press, bonding the layers together to form a solid board.
Step 4: Drilling
After lamination, the multilayer PCB undergoes drilling to create holes for through-hole components and vias. The drilling process is guided by the drill files generated during the design phase. The holes are drilled using high-speed, computer-controlled drill machines capable of achieving the required accuracy and precision.
Step 5: Plating
To establish electrical connectivity between layers, the drilled holes are plated with copper. This process involves the following steps:
- The board is cleaned and prepared for plating.
- A thin layer of copper is deposited onto the entire board, including the inside of the drilled holes, using an electroless copper plating process.
- Additional copper is electroplated onto the board to achieve the desired thickness.
Step 6: Outer Layer Fabrication
The outer layers of the multilayer PCB are fabricated using the same photolithography process described in Step 2. This process creates the final circuit pattern, including component pads and surface traces.
Step 7: Solder Mask Application
A solder mask is applied to the outer layers of the PCB to protect the copper traces from oxidation and prevent solder bridges during assembly. The solder mask is typically applied using a screen printing process and then cured using UV light.
Step 8: Surface Finish Application
A surface finish is applied to the exposed copper areas of the PCB to prevent oxidation and enhance solderability. Common surface finishes include:
- Hot Air Solder Leveling (HASL)
- Electroless Nickel Immersion Gold (ENIG)
- Immersion Silver
- Immersion Tin
- Organic Solderability Preservative (OSP)
The choice of surface finish depends on factors such as the intended application, environmental conditions, and assembly requirements.
Step 9: Silkscreen Application
A silkscreen layer is applied to the outer layers of the PCB to provide identification markings, component outlines, and other important information. The silkscreen is typically applied using a screen printing process and then cured using UV light.
Step 10: Final Inspection and Testing
Before the multilayer PCBs are packaged and shipped, they undergo a rigorous inspection and testing process to ensure they meet the required quality standards. This includes:
- Visual inspection for defects such as scratches, cracks, or contamination
- Electrical testing to verify continuity and isolation between layers
- Impedance testing to ensure the PCB meets the specified impedance requirements
- Microsectioning to verify the integrity of internal layers and plated through-holes
Multilayer PCBs that pass the final inspection and testing are packaged and shipped to the customer for assembly.
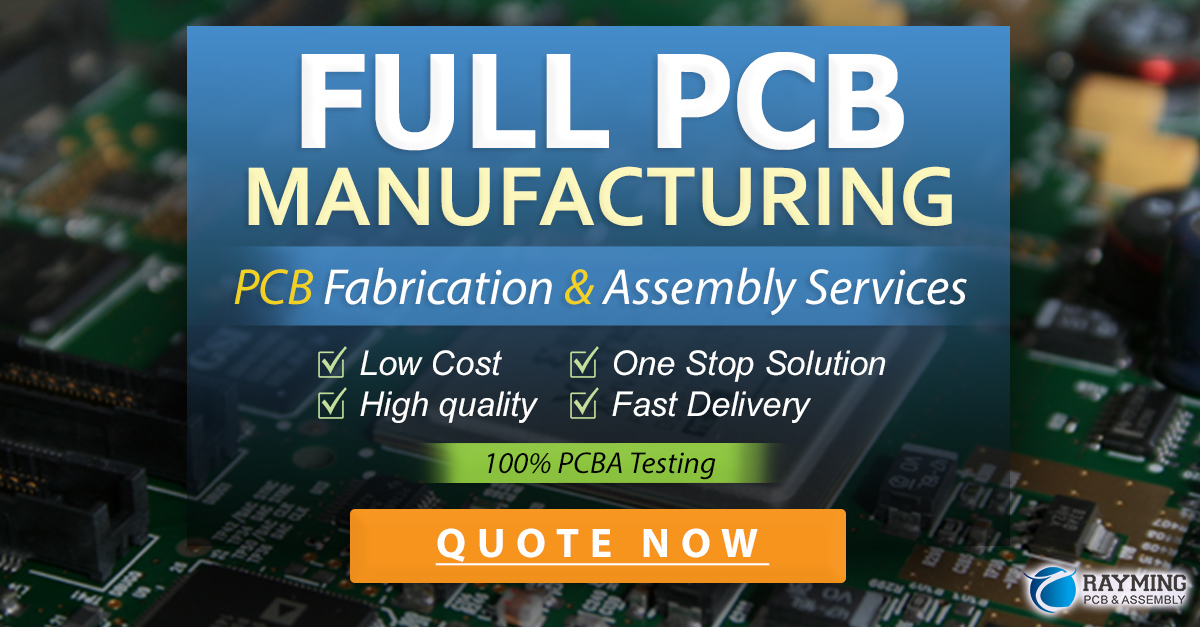
Quality Control in Multilayer PCB Manufacturing
Ensuring the quality of multilayer PCBs is essential for the reliability and performance of the end product. Key aspects of quality control in multilayer PCB manufacturing include:
- Adherence to industry standards, such as IPC-A-600 for acceptability of printed boards and IPC-6012 for qualification and performance specifications.
- Implementation of a robust quality management system, such as ISO 9001, to ensure consistent process control and continuous improvement.
- Regular maintenance and calibration of manufacturing equipment to ensure accuracy and precision.
- Thorough documentation of processes, materials, and test results for traceability and accountability.
Challenges in Multilayer PCB Manufacturing
Manufacturing multilayer PCBs presents several challenges that manufacturers must address to ensure high-quality, reliable boards:
-
Managing signal integrity: As the number of layers and circuit complexity increases, maintaining signal integrity becomes more challenging. Manufacturers must carefully design layer stackups, select appropriate materials, and control impedance to minimize signal degradation and crosstalk.
-
Controlling thermal expansion: The various materials used in multilayer PCBs have different coefficients of thermal expansion (CTE). Mismatches in CTE can lead to warpage, delamination, or other reliability issues. Manufacturers must select materials with compatible CTEs and employ techniques like symmetrical layer stackups to minimize these problems.
-
Ensuring plating uniformity: Achieving uniform copper plating in high-aspect-ratio through-holes can be challenging, particularly in thick multilayer boards. Manufacturers must optimize plating processes and use techniques like pulse plating to ensure adequate copper coverage and avoid plating voids.
-
Handling thin materials: As the demand for miniaturization grows, manufacturers must work with increasingly thin materials, such as ultra-thin prepregs and copper foils. Handling these materials requires specialized equipment and processes to prevent damage and ensure consistent results.
Future Trends in Multilayer PCB Manufacturing
As electronic devices continue to evolve, multilayer PCB manufacturing must adapt to meet new challenges and requirements. Some of the key trends shaping the future of multilayer PCB manufacturing include:
-
Increasing layer counts: The demand for more complex and compact devices is driving the need for multilayer PCBs with higher layer counts. Manufacturers are developing new materials and processes to enable the production of PCBs with 20, 30, or even more layers.
-
Adoption of advanced materials: New materials, such as low-loss dielectrics and high-performance copper alloys, are being developed to improve signal integrity, thermal management, and reliability in high-speed, high-frequency applications.
-
Embedded components: Embedding active and passive components within the layers of a multilayer PCB can save space, reduce parasitic effects, and improve overall performance. Manufacturers are developing new techniques for embedding components, such as 3D printing and laminated component assembly.
-
Automation and digitalization: The increasing complexity of multilayer PCBs is driving the need for greater automation and digitalization in the manufacturing process. Manufacturers are investing in advanced equipment, software, and data analytics to improve efficiency, quality, and traceability.
Frequently Asked Questions (FAQ)
- What is the typical turnaround time for manufacturing a multilayer PCB?
-
The turnaround time for manufacturing a multilayer PCB depends on factors such as the complexity of the design, the number of layers, and the manufacturer’s capacity. Typical turnaround times range from 1-2 weeks for standard designs to several weeks for complex, high-layer-count boards.
-
How much does it cost to manufacture a multilayer PCB?
-
The cost of manufacturing a multilayer PCB varies depending on factors such as the size of the board, the number of layers, the materials used, and the quantity ordered. As a rough estimate, a 4-layer PCB might cost around $10-20 per board for a small to medium-sized production run, while a 12-layer PCB could cost $100 or more per board.
-
What is the minimum feature size achievable in multilayer PCB manufacturing?
-
The minimum feature size in multilayer PCB manufacturing depends on the capabilities of the manufacturer and the chosen fabrication process. Typically, manufacturers can achieve minimum trace widths and spacings of around 3-4 mils (75-100 microns) for standard designs. Advanced processes, such as HDI (High Density Interconnect), can achieve even smaller feature sizes, down to 1-2 mils (25-50 microns).
-
Can multilayer PCBs be manufactured with flexible materials?
-
Yes, multilayer PCBs can be manufactured using flexible materials, such as polyimide or polyester. These flexible multilayer PCBs, also known as flex-rigids, combine rigid and flexible layers to create boards that can bend or fold to fit into tight spaces or conform to unique shapes. Flex-Rigid PCBs are commonly used in applications such as wearable devices, medical equipment, and aerospace systems.
-
What are the environmental considerations in multilayer PCB manufacturing?
- Multilayer PCB manufacturing involves the use of various chemicals and materials that can have an impact on the environment. Manufacturers must adhere to environmental regulations and implement eco-friendly practices to minimize their environmental footprint. This includes proper handling and disposal of hazardous waste, using lead-free and halogen-free materials, and adopting green manufacturing processes like water conservation and energy efficiency.
Conclusion
Multilayer PCB manufacturing is a complex process that requires a combination of advanced technology, skilled workmanship, and strict quality control. By understanding the various steps involved in the manufacturing process, as well as the challenges and trends shaping the industry, designers and engineers can make informed decisions when developing and sourcing multilayer PCBs for their projects. As the demand for more complex and compact electronic devices continues to grow, the importance of reliable, high-quality multilayer PCBs will only increase, driving innovation and progress in the field of PCB manufacturing.
Leave a Reply