Introduction to PCB Soldering
PCB soldering is a crucial process in the manufacturing of electronic devices. It involves attaching electronic components to a printed circuit board (PCB) using molten solder. The quality of the solder joint plays a significant role in the reliability and longevity of the electronic device. One of the most important aspects of PCB soldering is creating a good solder ball.
What is a Solder Ball?
A solder ball is a small sphere of solder that is used to attach electronic components to a PCB. It is created by melting solder wire or paste and allowing it to cool and solidify into a spherical shape. The size of the solder ball depends on the specific application and the size of the components being soldered.
Why is a Good Solder Ball Important?
A good solder ball is essential for creating a strong and reliable solder joint. If the solder ball is too small or misshapen, it may not provide adequate contact between the component and the PCB, leading to a weak or intermittent connection. On the other hand, if the solder ball is too large, it may cause short circuits or other issues.
Factors Affecting Solder Ball Quality
Several factors can affect the quality of a solder ball. Understanding these factors is essential for creating consistently good solder balls.
Solder Composition
The composition of the solder plays a significant role in the quality of the solder ball. Different types of solder have different melting points, wetting properties, and mechanical strengths. The most common types of solder used in PCB soldering are lead-based and lead-free solder.
Solder Type | Composition | Melting Point | Wetting Properties | Mechanical Strength |
---|---|---|---|---|
Lead-based | 63% Sn, 37% Pb | 183°C | Excellent | Good |
Lead-free | 96.5% Sn, 3% Ag, 0.5% Cu | 217°C | Good | Excellent |
Soldering Temperature
The temperature of the soldering iron or reflow oven can also affect the quality of the solder ball. If the temperature is too low, the solder may not melt completely, resulting in a poor connection. If the temperature is too high, the solder may oxidize or burn, leading to a brittle or weak joint.
The ideal soldering temperature depends on the type of solder being used. For lead-based solder, the recommended soldering temperature is between 300°C and 350°C. For lead-free solder, the recommended temperature is between 350°C and 400°C.
Soldering Time
The amount of time the solder is exposed to heat can also affect the quality of the solder ball. If the soldering time is too short, the solder may not have enough time to melt and flow properly, resulting in a poor connection. If the soldering time is too long, the solder may oxidize or burn, leading to a weak or brittle joint.
The ideal soldering time depends on the size of the component and the type of solder being used. For small components, a soldering time of 1-2 seconds is typically sufficient. For larger components, a soldering time of 3-5 seconds may be necessary.
Flux Selection
Flux is a chemical compound that is used to clean and activate the surfaces being soldered. It helps to remove oxides and other contaminants from the metal surfaces, allowing the solder to flow and bond more easily.
There are several types of flux available for PCB soldering, including rosin-based flux, water-soluble flux, and no-clean flux. The type of flux used can affect the quality of the solder ball, as well as the ease of cleaning after soldering.
Flux Type | Composition | Cleaning | Residue | Solder Ball Quality |
---|---|---|---|---|
Rosin-based | Rosin, activators | Requires cleaning | Can leave residue | Good |
Water-soluble | Organic acids, activators | Water-soluble | Minimal residue | Excellent |
No-clean | Synthetic resins, activators | No cleaning required | Minimal residue | Good |
Techniques for Creating Good Solder Balls
There are several techniques that can be used to create good solder balls consistently. These techniques involve controlling the factors that affect solder ball quality, such as solder composition, temperature, time, and flux selection.
Hand Soldering Technique
Hand soldering is a manual technique that involves using a soldering iron to melt and apply solder to the component and PCB. To create a good solder ball using hand soldering, follow these steps:
- Select the appropriate solder wire and flux for the application.
- Set the soldering iron temperature to the recommended range for the type of solder being used.
- Apply a small amount of flux to the component lead and PCB pad.
- Touch the soldering iron tip to the component lead and PCB pad simultaneously.
- Feed the solder wire into the joint, allowing it to melt and flow around the component lead and PCB pad.
- Remove the soldering iron and allow the solder to cool and solidify into a ball shape.
- Inspect the solder ball for size, shape, and coverage.
Reflow Soldering Technique
Reflow soldering is an automated technique that involves using a reflow oven to melt and flow solder paste onto the component and PCB. To create a good solder ball using reflow soldering, follow these steps:
- Select the appropriate solder paste and stencil for the application.
- Apply the solder paste to the PCB pads using the stencil.
- Place the components onto the PCB, aligning them with the solder paste.
- Load the PCB into the reflow oven and set the temperature profile to the recommended range for the type of solder being used.
- Allow the solder paste to melt and flow around the component leads and PCB pads.
- Cool the PCB and inspect the solder balls for size, shape, and coverage.
Inspection and Quality Control
Regardless of the soldering technique used, it is important to inspect the solder balls for quality and consistency. This can be done using visual inspection, X-ray inspection, or automated optical inspection (AOI).
Visual inspection involves examining the solder balls under magnification to check for size, shape, and coverage. X-ray inspection uses X-rays to create images of the solder joints, allowing for detection of voids, cracks, or other defects. AOI uses cameras and image processing software to automatically inspect the solder balls for defects.
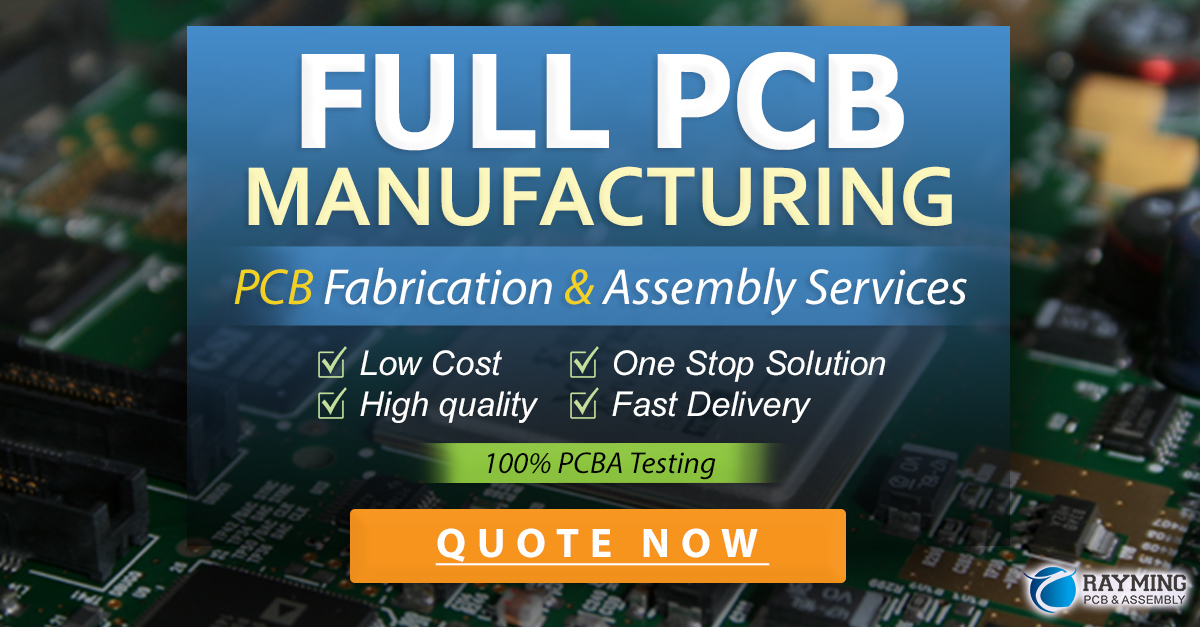
Common Solder Ball Defects and How to Avoid Them
Despite best efforts, solder ball defects can still occur. Some of the most common solder ball defects include:
Solder Bridges
Solder bridges occur when solder flows between two adjacent pads or components, creating an unintended electrical connection. To avoid solder bridges, ensure that the solder paste or wire is applied accurately and in the correct amount. Use a stencil or template to control the solder volume and placement.
Solder Balls
Solder balls are small spheres of solder that can form on the PCB surface during reflow soldering. They can cause short circuits or other issues if they come into contact with other components or pads. To avoid solder balls, ensure that the solder paste is mixed and applied correctly, and that the reflow oven temperature profile is optimized for the specific application.
Insufficient Solder
Insufficient solder occurs when there is not enough solder to create a strong and reliable joint. This can be caused by incorrect solder volume, poor wetting, or incorrect soldering temperature or time. To avoid insufficient solder, ensure that the correct amount of solder is applied, and that the soldering temperature and time are optimized for the specific application.
Tombstoning
Tombstoning occurs when a component stands up on one end during reflow soldering, creating an open circuit. This can be caused by uneven heating, incorrect component placement, or incorrect solder paste volume. To avoid tombstoning, ensure that the component is placed correctly and that the reflow oven temperature profile is optimized for even heating.
FAQ
What is the difference between lead-based and lead-free solder?
Lead-based solder contains a mixture of tin and lead, while lead-free solder contains a mixture of tin, silver, and copper. Lead-free solder has a higher melting point and better mechanical strength than lead-based solder, but can be more difficult to work with due to its higher melting temperature.
How do I choose the right type of flux for my application?
The type of flux used depends on the specific application and the type of solder being used. Rosin-based flux is commonly used for hand soldering, while water-soluble flux is often used for reflow soldering. No-clean flux can be used for both hand and reflow soldering, and does not require cleaning after soldering.
Can I use the same soldering technique for all components?
Different components may require different soldering techniques depending on their size, shape, and material. For example, surface mount components may require reflow soldering, while through-hole components may require hand soldering. It is important to select the appropriate soldering technique for each component to ensure a strong and reliable solder joint.
How can I tell if my solder ball is the correct size and shape?
Visual inspection under magnification is the most common method for checking solder ball size and shape. The solder ball should be spherical in shape and should completely cover the component lead and PCB pad. X-ray inspection or automated optical inspection can also be used to check for voids, cracks, or other defects.
What should I do if I encounter a solder ball defect?
If a solder ball defect is detected, it may be necessary to rework or repair the solder joint. This can involve removing the defective solder and reapplying new solder using the appropriate technique. In some cases, the component may need to be replaced entirely. It is important to identify and correct solder ball defects as early as possible to avoid further issues down the line.
Conclusion
Creating a good PCB solder ball is essential for ensuring the reliability and longevity of electronic devices. By understanding the factors that affect solder ball quality, such as solder composition, temperature, time, and flux selection, and by using the appropriate soldering techniques and inspection methods, it is possible to create consistently good solder balls. While solder ball defects can still occur, they can be minimized by following best practices and correcting issues as early as possible. With practice and attention to detail, anyone can learn to create high-quality PCB solder balls.
Leave a Reply