What is a Regular PCB?
A regular PCB, also known as a conventional PCB, is a printed circuit board that consists of conductive tracks, pads, and other features etched from copper sheets laminated onto a non-conductive substrate. These boards are used to mechanically support and electrically connect electronic components using conductive pathways, tracks, or signal traces.
Characteristics of Regular PCBs
- Larger feature sizes: Regular PCBs typically have wider traces and larger spacing between components compared to HDI PCBs.
- Fewer layers: Conventional PCBs usually have fewer layers, ranging from single-sided to multi-layer boards with up to 8 layers.
- Lower component density: Due to larger feature sizes and fewer layers, regular PCBs have a lower component density compared to HDI boards.
- Lower cost: Regular PCBs are generally less expensive to manufacture than HDI PCBs due to their simpler design and fewer manufacturing steps.
What is an HDI PCB?
HDI, or high-density interconnect, PCBs are advanced printed circuit boards that offer higher component density and more complex designs than regular PCBs. These boards feature finer traces, smaller vias, and higher layer counts, enabling the integration of more components in a smaller space.
Characteristics of HDI PCBs
- Smaller feature sizes: HDI PCBs have narrower traces and smaller spacing between components, allowing for higher component density.
- Higher layer counts: HDI boards often have 8 or more layers, with some designs exceeding 24 layers.
- Microvias: HDI PCBs utilize microvias, which are small, laser-drilled holes that connect different layers of the board, enabling more efficient use of space.
- Blind and buried vias: In addition to microvias, HDI PCBs may also feature blind and buried vias, which are not visible on the surface of the board, further increasing component density.
- Advanced materials: HDI PCBs often use advanced substrate materials, such as high-Tg FR-4 or polyimide, to ensure better thermal and electrical performance.
Differences Between HDI and Regular PCBs
To better understand the distinction between HDI and regular PCBs, let’s compare their key features:
Feature | HDI PCB | Regular PCB |
---|---|---|
Trace width | As small as 50 microns | Typically 100 microns or larger |
Via diameter | As small as 50 microns (microvias) | Typically 200 microns or larger |
Layer count | 8 or more layers | Usually fewer than 8 layers |
Component density | High, enabling miniaturization | Lower, limited by larger feature sizes |
Via types | Microvias, blind vias, buried vias | Mostly through-hole vias |
Manufacturing complexity | Higher, requiring advanced equipment and processes | Lower, using standard PCB fabrication methods |
Cost | Higher due to advanced materials and processing | Lower, due to simpler design and materials |
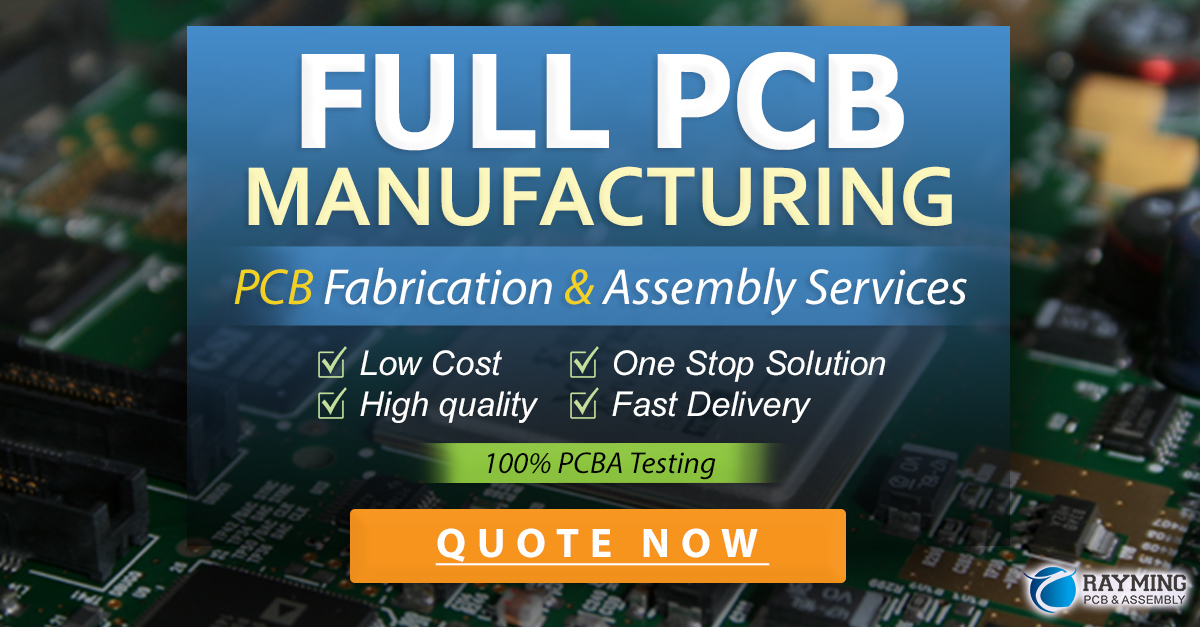
When to Choose HDI PCBs
HDI PCBs are the preferred choice for applications that require high component density, miniaturization, and advanced performance. Some common applications include:
- Smartphones and tablets
- Wearable devices
- Medical devices
- Aerospace and defense systems
- High-performance computing
- Automotive electronics
If your product requires any of the following features, an HDI PCB may be the best option:
- Compact size and weight reduction
- High-speed signal transmission
- Improved thermal management
- Enhanced reliability and durability
- Integration of advanced components (e.g., BGA, CSP)
When to Choose Regular PCBs
Regular PCBs are still widely used in various applications where high component density and miniaturization are not critical factors. Some typical applications include:
- Consumer electronics (e.g., televisions, home appliances)
- Power supplies and converters
- Industrial control systems
- Lighting systems
- Low-cost, high-volume products
If your product has the following characteristics, a regular PCB may be sufficient:
- Larger components and spacing
- Lower layer count requirements
- Less stringent signal integrity demands
- Cost-sensitive applications
Design Considerations for HDI and Regular PCBs
When designing either an HDI or regular PCB, there are several factors to consider to ensure optimal performance and manufacturability:
- Material selection: Choose the appropriate substrate material based on the electrical, thermal, and mechanical requirements of your application.
- Layer stackup: Determine the number of layers and their arrangement to achieve the desired functionality and signal integrity.
- Trace width and spacing: Follow the recommended design guidelines for trace width and spacing based on the PCB type and manufacturing capabilities.
- Via design: Select the appropriate via types and sizes to ensure reliable interconnections between layers.
- Component placement: Optimize component placement to minimize signal path lengths, reduce crosstalk, and improve overall performance.
- Thermal management: Incorporate thermal management techniques, such as heat sinks, thermal vias, or copper pours, to dissipate heat effectively.
- Design for manufacturing (DFM): Adhere to DFM guidelines to ensure the PCB can be manufactured reliably and cost-effectively.
FAQ
-
Q: Can HDI PCBs be used for low-volume production?
A: Yes, HDI PCBs can be used for low-volume production, but the cost per board may be higher compared to regular PCBs due to the advanced manufacturing processes involved. -
Q: Are HDI PCBs more durable than regular PCBs?
A: HDI PCBs can be more durable than regular PCBs due to the use of advanced materials and manufacturing techniques. However, the durability also depends on factors such as the specific application, environmental conditions, and handling. -
Q: Can regular PCBs be upgraded to HDI PCBs?
A: In most cases, regular PCBs cannot be directly upgraded to HDI PCBs. The design, layer stackup, and manufacturing processes for HDI PCBs are different from those of regular PCBs. A redesign would be necessary to convert a regular PCB to an HDI PCB. -
Q: Are there any limitations to using HDI PCBs?
A: The main limitations of HDI PCBs are their higher cost and the need for advanced manufacturing capabilities. Additionally, designers must have expertise in HDI design rules and guidelines to ensure the boards can be manufactured successfully. -
Q: How long does it take to manufacture an HDI PCB compared to a regular PCB?
A: The manufacturing time for an HDI PCB is typically longer than that of a regular PCB due to the additional processing steps and advanced techniques required. However, the exact time difference can vary depending on the specific design, manufacturer, and production volume.
Conclusion
Understanding the differences between HDI and regular PCBs is crucial when determining which type best suits your product’s requirements. HDI PCBs offer higher component density, smaller feature sizes, and advanced performance, making them ideal for applications that demand miniaturization and high-speed signal transmission. On the other hand, regular PCBs are a cost-effective solution for less complex designs with lower component density and performance requirements.
When choosing between HDI and regular PCBs, consider factors such as your product’s size constraints, performance needs, manufacturing complexity, and budget. By carefully evaluating these aspects and collaborating with experienced PCB designers and manufacturers, you can select the most appropriate PCB type for your product, ensuring optimal functionality, reliability, and cost-effectiveness.
Leave a Reply