Understanding the Requirements
Before starting the Enclosure Design process, it is essential to understand the requirements of the PCBA and the end product. Some of the key factors to consider include:
Environmental Factors
- Operating temperature range
- Humidity levels
- Exposure to dust, moisture, and other contaminants
- Vibration and shock resistance
Electrical Factors
- Electromagnetic Interference (EMI) shielding requirements
- Electrostatic Discharge (ESD) protection
- Grounding and isolation requirements
Mechanical Factors
- Size and weight constraints
- Mounting and fastening requirements
- Accessibility for maintenance and repairs
- Aesthetics and ergonomics
Regulatory Factors
- Safety standards (e.g., UL, CE, RoHS)
- Environmental regulations (e.g., WEEE, REACH)
- Industry-specific standards (e.g., medical, automotive, aerospace)
Selecting the Enclosure Material
The choice of enclosure material depends on various factors such as the operating environment, budget, and aesthetic requirements. Some of the common materials used for PCBA enclosures include:
Plastic
Plastic enclosures are lightweight, cost-effective, and offer good electrical insulation properties. They can be easily molded into complex shapes and are available in a wide range of colors and finishes. Some of the popular plastic materials for enclosures include:
- ABS (Acrylonitrile Butadiene Styrene)
- PC (Polycarbonate)
- PBT (Polybutylene Terephthalate)
- Nylon
Metal
Metal enclosures offer excellent mechanical strength, EMI shielding, and heat dissipation properties. They are often used in harsh industrial environments or when a premium look and feel is desired. Some of the common metal materials for enclosures include:
- Aluminum
- Steel
- Stainless Steel
- Die-cast Zinc
Composite Materials
Composite materials, such as carbon fiber and fiberglass, offer a combination of strength, lightweight, and corrosion resistance. They are often used in high-performance applications such as aerospace and motorsports.
Material | Advantages | Disadvantages |
---|---|---|
Plastic | Lightweight, cost-effective, good insulation | Limited strength, poor heat dissipation |
Metal | High strength, EMI shielding, heat dissipation | Heavy, expensive, requires additional insulation |
Composite | Strong, lightweight, corrosion-resistant | Expensive, complex manufacturing process |
Designing the Enclosure
Once the requirements and materials have been determined, the next step is to design the enclosure. The design process typically involves the following stages:
Concept Development
In this stage, various design concepts are generated based on the requirements and constraints. Sketches, 3D models, and prototypes are created to visualize and evaluate the design ideas.
Detailed Design
The selected concept is refined and optimized for manufacturability, assembly, and performance. Detailed drawings and 3D models are created, specifying the dimensions, tolerances, and material properties.
Design for Manufacturing (DFM)
The design is reviewed and optimized for the chosen manufacturing process, such as injection molding, die casting, or Sheet Metal Fabrication. Design guidelines and best practices specific to the manufacturing process are followed to ensure the enclosure can be produced efficiently and cost-effectively.
Design for Assembly (DFA)
The enclosure design is optimized for easy assembly and disassembly of the PCBA and other components. Factors such as fastening methods, cable routing, and accessibility for maintenance are considered.
Prototyping and Testing
Prototypes of the enclosure are fabricated using 3D printing, CNC Machining, or other rapid prototyping techniques. The prototypes are used to validate the design, test the fit and function, and gather user feedback. Any necessary design modifications are made based on the prototype testing results.
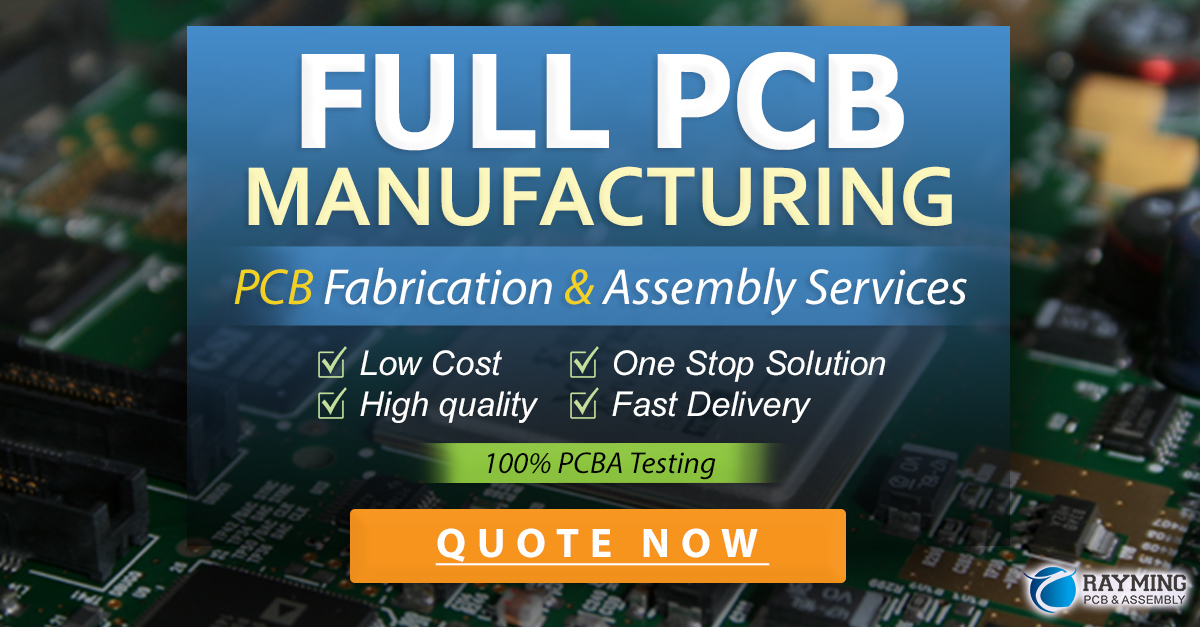
Thermal Management
Thermal management is a critical aspect of enclosure design, as it ensures the PCBA operates within its specified temperature range. Overheating can lead to component failure, reduced performance, and shortened product life. Some of the thermal management techniques used in enclosure design include:
Passive Cooling
Passive cooling relies on natural convection and radiation to dissipate heat from the PCBA. This is achieved through the use of heat sinks, thermal interface materials, and proper ventilation in the enclosure.
Active Cooling
Active cooling involves the use of fans, blowers, or thermoelectric coolers to forcibly remove heat from the PCBA. This is necessary when the heat generated by the components exceeds the capacity of passive cooling methods.
Liquid Cooling
Liquid cooling systems use a fluid, such as water or a dielectric liquid, to transfer heat away from the PCBA. This method is highly effective but is more complex and expensive than air cooling methods.
Cooling Method | Advantages | Disadvantages |
---|---|---|
Passive Cooling | Simple, reliable, no moving parts | Limited cooling capacity, requires larger enclosure |
Active Cooling | Higher cooling capacity, compact design | Added complexity, noise, and power consumption |
Liquid Cooling | Highest cooling capacity, efficient heat transfer | Complex, expensive, potential for leaks |
EMI/RFI Shielding
Electromagnetic Interference (EMI) and Radio Frequency Interference (RFI) can disrupt the operation of the PCBA and other nearby electronic devices. Enclosures designed for EMI/RFI shielding help to contain the electromagnetic emissions from the PCBA and protect it from external interference. Some of the shielding techniques used in enclosure design include:
Conductive Coatings
Conductive coatings, such as nickel, copper, or silver, are applied to the interior surfaces of plastic enclosures to create a Faraday cage effect. These coatings provide a low-impedance path for electromagnetic waves, effectively shielding the PCBA.
Conductive Gaskets
Conductive gaskets, made from materials such as silicone or foam with embedded conductive particles, are used to seal gaps and openings in the enclosure. These gaskets maintain electrical continuity between mating surfaces, preventing electromagnetic leakage.
Shielding Vents
Shielding vents, made from perforated metal or wire mesh, allow airflow for cooling while maintaining EMI/RFI shielding effectiveness. The size and spacing of the perforations are designed to attenuate electromagnetic waves at the desired frequencies.
Ingress Protection (IP) Rating
The Ingress Protection (IP) rating system is used to classify the level of protection an enclosure provides against the intrusion of solid objects and liquids. The IP rating consists of two digits: the first digit indicates the protection against solid objects, and the second digit indicates the protection against liquids.
First Digit | Protection Against Solid Objects |
---|---|
0 | No protection |
1 | Objects > 50 mm |
2 | Objects > 12.5 mm |
3 | Objects > 2.5 mm |
4 | Objects > 1 mm |
5 | Dust-protected |
6 | Dust-tight |
Second Digit | Protection Against Liquids |
---|---|
0 | No protection |
1 | Vertically dripping water |
2 | Dripping water (15° tilted) |
3 | Spraying water |
4 | Splashing water |
5 | Water jets |
6 | Powerful water jets |
7 | Immersion up to 1 m |
8 | Immersion beyond 1 m |
9K | High-pressure, high-temperature water jets |
For example, an enclosure with an IP rating of IP65 is completely dust-tight and protected against low-pressure water jets from any direction.
Documentation and Compliance
Proper documentation is essential for communicating the design intent, manufacturing requirements, and compliance with relevant standards and regulations. Some of the key documents associated with enclosure design include:
- 3D CAD models and 2D drawings
- Bill of Materials (BOM)
- Assembly instructions
- Manufacturing specifications
- Test reports and certificates
- Compliance declarations (e.g., CE, RoHS, UL)
Maintaining accurate and up-to-date documentation helps to ensure the enclosure is manufactured and assembled correctly, meets the required performance and safety standards, and can be easily maintained and serviced throughout its lifecycle.
Best Practices for Enclosure Design
To ensure a successful enclosure design, follow these best practices:
-
Involve all stakeholders (e.g., electrical, mechanical, and industrial designers) early in the design process to ensure all requirements are considered.
-
Use 3D CAD tools to create and validate the enclosure design, and to communicate the design intent to manufacturers and suppliers.
-
Follow Design for Manufacturing (DFM) and Design for Assembly (DFA) guidelines to optimize the enclosure for the chosen fabrication and assembly processes.
-
Conduct Finite Element Analysis (FEA) to evaluate the structural integrity, thermal performance, and EMI/RFI shielding effectiveness of the enclosure.
-
Create prototypes early in the design process to validate the form, fit, and function of the enclosure, and to gather user feedback.
-
Specify the appropriate IP rating and environmental tests to ensure the enclosure meets the required level of protection against dust, moisture, and other contaminants.
-
Follow relevant industry standards and regulations, such as UL, CE, and RoHS, to ensure the enclosure is safe, reliable, and compliant with environmental and safety requirements.
-
Maintain accurate and up-to-date documentation, including 3D CAD models, drawings, BOMs, and manufacturing specifications, to ensure the enclosure can be manufactured and assembled consistently and efficiently.
Frequently Asked Questions (FAQ)
- What is the difference between an enclosure and a housing?
-
An enclosure is a protective case that surrounds and supports the internal components of a device, such as a PCBA. A housing, on the other hand, is a more general term that can refer to any type of casing or container for a device, including enclosures, shells, and cabinets.
-
What is the most common material used for PCBA enclosures?
-
The most common material used for PCBA enclosures is plastic, particularly ABS (Acrylonitrile Butadiene Styrene) and PC (Polycarbonate). These materials are lightweight, cost-effective, and offer good electrical insulation properties.
-
How do I choose the right IP rating for my enclosure?
-
The choice of IP rating depends on the intended operating environment and the level of protection required against dust and moisture. For example, an outdoor enclosure may require a higher IP rating (e.g., IP67) compared to an indoor enclosure (e.g., IP54). Consult the IP rating chart and consider the specific environmental factors your device will be exposed to.
-
What is the purpose of EMI/RFI shielding in enclosure design?
-
EMI/RFI shielding helps to contain the electromagnetic emissions from the PCBA and protect it from external interference. This is important for ensuring the proper operation of the device and compliance with electromagnetic compatibility (EMC) regulations.
-
How can I optimize my enclosure design for thermal management?
- To optimize your enclosure design for thermal management, consider the following techniques:
- Use materials with good thermal conductivity, such as aluminum or copper, for heat-sensitive components.
- Incorporate heat sinks, thermal interface materials, and proper ventilation to facilitate heat dissipation.
- Use active cooling methods, such as fans or thermoelectric coolers, when necessary.
- Conduct thermal simulations to evaluate the temperature distribution and identify hot spots in the enclosure.
By following the guidelines and best practices outlined in this article, you can design an enclosure that effectively protects your PCBA, meets the required performance and safety standards, and contributes to the overall success of your product.
Leave a Reply