Introduction to PCB Thickness
Printed Circuit Boards (PCBs) are essential components in modern electronic devices. They provide a platform for mounting and interconnecting electronic components, enabling the proper functioning of the device. One crucial factor to consider when designing or selecting a PCB is its thickness. PCB thickness plays a significant role in the board’s mechanical stability, electrical performance, and overall reliability.
In this comprehensive guide, we will explore the various aspects of PCB thickness, including the standard thickness options, factors to consider when choosing the right thickness, and the impact of thickness on the PCB’s performance. By the end of this article, you will have a clear understanding of how to select the optimal PCB thickness for your specific application.
Standard PCB Thickness Options
PCB thickness is typically measured in either millimeters (mm) or mils (thousandths of an inch). The most common PCB thickness options are:
Thickness (mm) | Thickness (mils) |
---|---|
0.4 | 15.75 |
0.6 | 23.62 |
0.8 | 31.50 |
1.0 | 39.37 |
1.2 | 47.24 |
1.6 | 62.99 |
2.0 | 78.74 |
Each thickness option has its advantages and disadvantages, which we will discuss in detail later in this article.
Factors to Consider When Choosing PCB Thickness
When selecting the appropriate PCB thickness for your project, several factors come into play. These factors include:
1. Application Requirements
The specific requirements of your application will greatly influence the choice of PCB thickness. Consider the following:
-
Mechanical Stability: If your PCB will be subjected to vibrations, shocks, or other mechanical stresses, a thicker board may be necessary to ensure adequate stability and prevent warping or cracking.
-
Weight Constraints: In applications where weight is a critical factor, such as in aerospace or portable devices, thinner PCBs may be preferred to minimize the overall weight of the device.
-
Space Limitations: The available space within the device enclosure will also dictate the maximum allowable PCB thickness. Thinner boards may be required to fit within tight spaces.
2. Layer Count
The number of layers in your PCB design directly affects the required thickness. As the layer count increases, the overall thickness of the board also increases. This is because each layer requires a certain amount of dielectric material (substrate) between the conductive layers to provide insulation and maintain the desired electrical properties.
The following table provides a general guideline for the relationship between layer count and PCB thickness:
Layer Count | Typical Thickness Range (mm) |
---|---|
1-2 | 0.4 – 0.8 |
4 | 0.8 – 1.6 |
6 | 1.2 – 2.0 |
8+ | 1.6 – 3.2 |
Keep in mind that these are general ranges, and the actual thickness may vary depending on the specific design requirements and manufacturing capabilities.
3. Manufacturing Capabilities
The manufacturing process and capabilities of your chosen PCB manufacturer will also influence the available thickness options. Some manufacturers may have limitations on the minimum or maximum thickness they can produce reliably.
It’s essential to consult with your PCB manufacturer early in the design process to ensure that your desired thickness is achievable and to discuss any potential manufacturing challenges or constraints.
4. Cost Considerations
PCB thickness can also impact the overall cost of your project. Generally, thinner PCBs are less expensive to manufacture compared to thicker boards. This is because thinner boards require less material and are easier to process, resulting in lower production costs.
However, it’s important to strike a balance between cost and performance. Opting for a thinner PCB to save costs may compromise the board’s mechanical stability or electrical performance, leading to potential issues down the line.
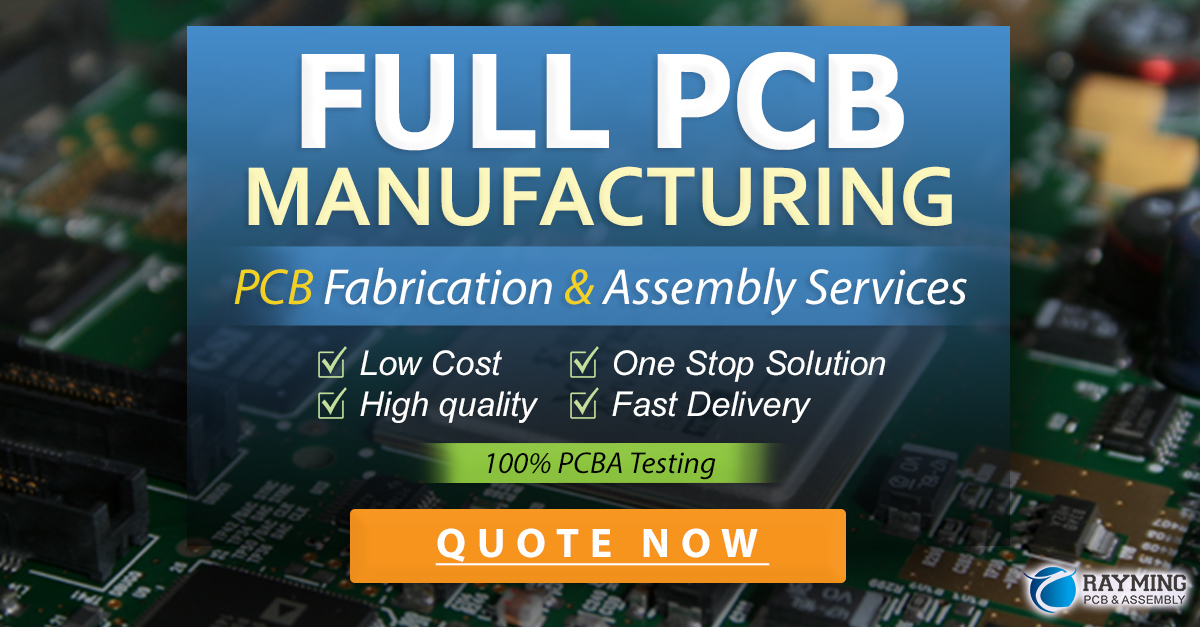
Impact of PCB Thickness on Performance
The chosen PCB thickness can have a significant impact on various aspects of the board’s performance. Let’s explore some of these effects:
1. Mechanical Strength and Rigidity
Thicker PCBs offer greater mechanical strength and rigidity compared to thinner boards. This is particularly important in applications where the PCB is subjected to physical stresses, such as vibrations or impacts. A thicker board is less likely to flex or warp under these conditions, ensuring the integrity of the mounted components and solder joints.
However, it’s worth noting that the mechanical strength of a PCB is not solely determined by its thickness. Other factors, such as the type of material used for the substrate (e.g., FR-4, Rogers, etc.), the copper weight, and the presence of reinforcing elements like stiffeners or metal cores, also contribute to the overall mechanical performance.
2. Thermal Management
PCB thickness plays a role in the board’s ability to dissipate heat generated by the mounted components. Thicker boards have a greater thermal mass and can more effectively spread and dissipate heat compared to thinner boards. This is particularly important in high-power applications or designs with densely populated components.
Adequate thermal management is crucial to ensure the long-term reliability and performance of the PCB and its components. Overheating can lead to component failure, reduced lifespan, and potential safety hazards.
To enhance thermal management, designers may opt for thicker PCBs, incorporate thermal vias to transfer heat to other layers or heatsinks, or use specialized materials with higher thermal conductivity.
3. Electrical Performance
PCB thickness can influence the electrical performance of the board, particularly at high frequencies. Thinner boards have shorter signal paths, which can be advantageous for high-speed designs as it minimizes signal propagation delays and reduces the risk of signal integrity issues.
However, thinner boards also have reduced copper cross-sectional area, which can lead to higher resistance and increased power losses. This can be particularly problematic for power delivery networks or high-current applications.
Thicker boards, on the other hand, offer lower resistance and better power handling capabilities due to the increased copper cross-sectional area. They also provide better shielding against electromagnetic interference (EMI) and can help maintain signal integrity by reducing crosstalk between adjacent layers.
The choice of PCB thickness for optimal electrical performance depends on the specific design requirements, such as the operating frequency, signal integrity concerns, and power delivery demands.
PCB Thickness Selection Process
Now that we have explored the various factors and considerations related to PCB thickness, let’s outline a step-by-step process for selecting the appropriate thickness for your project:
-
Define application requirements: Clearly identify the mechanical, thermal, and electrical requirements of your application. Consider factors such as the operating environment, expected mechanical stresses, power dissipation needs, and signal integrity concerns.
-
Determine the layer count: Based on your circuit complexity and routing requirements, determine the number of layers needed for your PCB design. Refer to the layer count and thickness guideline table provided earlier to get a rough estimate of the required thickness range.
-
Consult with your PCB manufacturer: Engage with your chosen PCB manufacturer early in the design process. Discuss your requirements, layer count, and any specific design challenges. Seek their advice on the recommended thickness options based on their manufacturing capabilities and experience.
-
Evaluate trade-offs: Consider the trade-offs between cost, mechanical strength, thermal management, and electrical performance. Determine which factors are most critical for your application and prioritize accordingly.
-
Conduct simulations and prototyping: If necessary, perform simulations to analyze the mechanical, thermal, and electrical behavior of your PCB design at different thicknesses. Create prototypes to validate the performance and manufacturability of your chosen thickness.
-
Finalize the thickness: Based on the results of your simulations, prototyping, and discussions with the manufacturer, finalize the PCB thickness that best meets your application requirements while considering cost and manufacturability.
Frequently Asked Questions (FAQ)
-
What is the most common PCB thickness?
The most common PCB thickness is 1.6mm (62.99 mils). This thickness offers a good balance between mechanical strength, cost, and ease of manufacturability for a wide range of applications. -
Can I use different thicknesses for different layers in a multi-layer PCB?
Yes, it is possible to use different thicknesses for different layers in a multi-layer PCB. This is known as a “hybrid stack-up” or “mixed stack-up.” Hybrid stack-ups allow designers to optimize the thickness of each layer based on its specific requirements, such as power delivery or signal integrity. -
How does PCB thickness affect the drilling process?
PCB thickness directly impacts the drilling process. Thicker boards require longer drill bits and may necessitate slower drilling speeds to ensure hole quality and prevent drill bit breakage. The aspect ratio, which is the ratio of the hole depth to the hole diameter, becomes more challenging with increasing board thickness. -
What is the maximum PCB thickness that can be manufactured?
The maximum PCB thickness that can be manufactured depends on the capabilities of the PCB manufacturer. Some manufacturers can produce PCBs up to 5mm thick or more. However, such thick boards are less common and may require specialized manufacturing processes and equipment. -
How does PCB thickness affect the assembly process?
PCB thickness can affect the assembly process in several ways. Thicker boards may require longer solder reflow profiles to ensure proper heat transfer and solder joint formation. They may also necessitate the use of specialized component placement and soldering equipment to accommodate the increased thickness. Thinner boards, on the other hand, may be more prone to warping during the reflow process and require additional support or fixturing.
Conclusion
Choosing the right PCB thickness is a critical decision that impacts the mechanical, thermal, and electrical performance of your electronic device. By understanding the standard thickness options, considering the various factors that influence thickness selection, and following a systematic selection process, you can ensure that your PCB design meets the specific requirements of your application.
Remember to engage with your PCB manufacturer early in the design process to discuss your requirements and constraints. Their expertise and guidance can help you navigate the trade-offs and make informed decisions regarding PCB thickness.
By selecting the optimal PCB thickness, you can enhance the reliability, durability, and overall performance of your electronic product, ultimately contributing to its success in the market.
Leave a Reply