What is Multilayer PCB Pressing?
Multilayer PCB pressing is a crucial step in the manufacturing process of printed circuit boards (PCBs) that have more than two layers. It involves stacking and bonding multiple layers of PCB material together under high pressure and temperature to create a single, unified board. This process ensures that the layers are properly aligned and adhered to one another, resulting in a reliable and functional multilayer PCB.
The Importance of Multilayer PCB Pressing
Pressing is essential for several reasons:
- Ensuring proper layer alignment: Misaligned layers can lead to connectivity issues and decreased performance.
- Creating a strong bond between layers: A well-pressed PCB will have a sturdy, long-lasting bond between its layers.
- Eliminating air pockets and voids: Pressing helps remove any air trapped between layers, which can cause delamination and other defects.
- Maintaining consistent thickness: Pressing ensures that the final PCB has a uniform thickness throughout.
The Multilayer PCB Pressing Process
Step 1: Layer Preparation
Before pressing, each layer of the PCB must be prepared:
- Etching: The copper traces are etched onto each layer using a photoresist and chemical etching process.
- Drilling: Holes are drilled through the layers to accommodate components and vias.
- Cleaning: The layers are cleaned to remove any dirt, debris, or oxidation.
Step 2: Layup
The prepared layers are then stacked in the proper order, with prepreg (pre-impregnated) sheets placed between each layer. Prepreg is a type of fiberglass that has been impregnated with a partially cured resin, which will help bond the layers together during pressing.
Step 3: Pressing
The stacked layers are placed in a press, which applies both heat and pressure to the PCB. The specific temperature and pressure settings will depend on the type of prepreg and laminate materials being used. Typical values are:
- Temperature: 350-400°F (175-205°C)
- Pressure: 300-500 psi (21-35 kg/cm²)
- Duration: 1-2 hours
During pressing, the resin in the prepreg melts and flows, filling any gaps and creating a strong bond between the layers. The heat and pressure also cure the resin, turning it into a solid, durable material.
Step 4: Cooling
After pressing, the PCB is cooled slowly to room temperature. This controlled cooling helps prevent warping or other deformations that can occur due to the different thermal expansion rates of the materials.
Step 5: Final Processing
Once cooled, the pressed PCB undergoes final processing steps, such as:
- Drilling: Additional holes are drilled for mounting and other purposes.
- Plating: The holes are plated with copper to create electrical connections between layers.
- Solder mask application: A protective solder mask is applied to the outer layers.
- Silkscreen printing: Text and symbols are printed onto the PCB for reference and identification.
Factors Affecting Multilayer PCB Pressing
Several factors can influence the success of the pressing process:
- Material selection: Choosing the right prepreg and laminate materials is crucial for achieving a strong, reliable bond.
- Layer alignment: Proper alignment of the layers during layup is essential for ensuring the correct functioning of the final PCB.
- Press parameters: The temperature, pressure, and duration of the pressing process must be carefully controlled to achieve the desired results.
- Cleanliness: Any dirt, debris, or contamination on the layers can lead to defects in the final PCB.
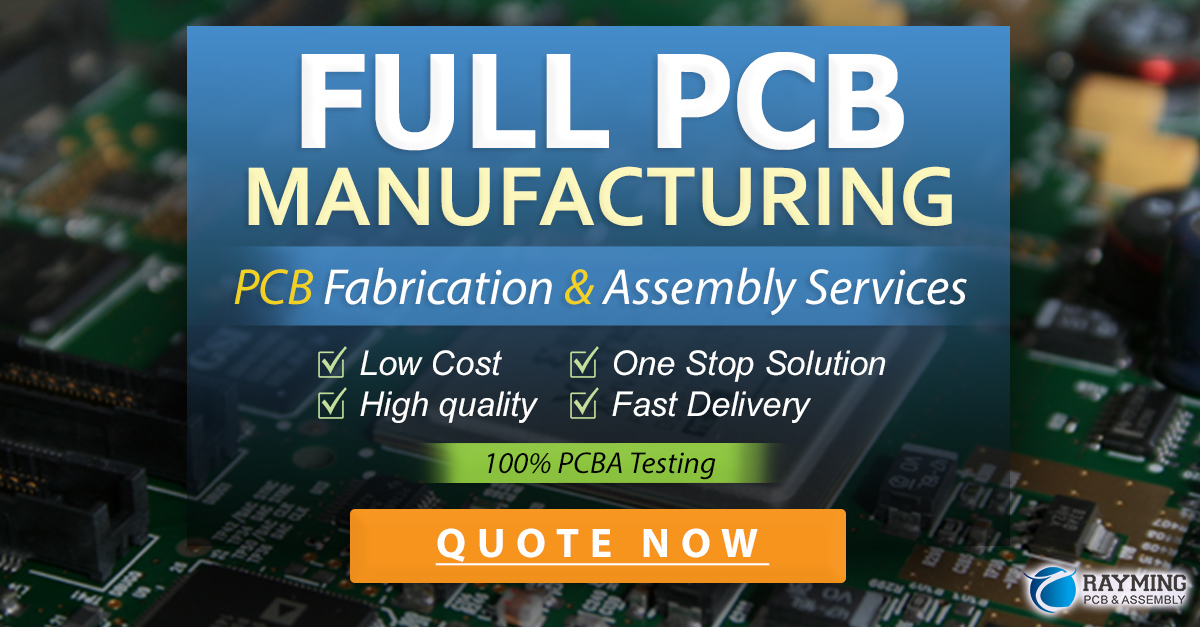
Common Multilayer PCB Pressing Defects
Despite careful control of the pressing process, defects can still occur. Some common defects include:
- Delamination: When the bond between layers fails, causing them to separate.
- Voids: Small air pockets that can form between layers, weakening the bond and potentially causing electrical issues.
- Warping: A distortion of the PCB’s shape, often caused by uneven cooling or improper press parameters.
- Misregistration: Misalignment of the layers, leading to incorrect connections and decreased performance.
Troubleshooting Multilayer PCB Pressing Issues
If defects are discovered after pressing, several steps can be taken to identify and correct the issue:
- Visual inspection: Carefully examining the PCB can reveal surface defects like delamination or warping.
- Microsectioning: Cutting a cross-section of the PCB and examining it under a microscope can show internal defects like voids or misregistration.
- Electrical testing: Performing continuity and insulation resistance tests can help identify any electrical issues caused by pressing defects.
- Process review: If defects are found, reviewing the entire pressing process can help identify the root cause and prevent future occurrences.
Advancements in Multilayer PCB Pressing Technology
As PCBs become more complex and compact, new technologies are being developed to improve the pressing process:
- Vacuum pressing: By performing the pressing process in a vacuum chamber, air pockets and voids can be eliminated more effectively.
- Induction heating: Using induction coils to heat the PCB during pressing can provide more uniform and controllable heating compared to traditional methods.
- Continuous pressing: Instead of pressing one PCB at a time, continuous pressing systems can process multiple PCBs in a single, ongoing operation, increasing efficiency and throughput.
Frequently Asked Questions (FAQ)
1. How many layers can be pressed together in a multilayer PCB?
The number of layers in a multilayer PCB can vary depending on the specific application and design requirements. Most Multilayer PCBs have between 4 and 12 layers, but some advanced designs can have up to 50 layers or more.
2. What materials are used in multilayer PCB pressing?
The most common materials used in multilayer PCB pressing are:
- Laminates: FR-4, a type of fiberglass-reinforced epoxy, is the most widely used laminate material.
- Prepregs: Prepregs are sheets of fiberglass impregnated with partially cured resin, which melts and flows during pressing to bond the layers together.
- Copper foil: Thin sheets of copper are used to create the conductive traces on each layer of the PCB.
3. How long does the multilayer PCB pressing process take?
The duration of the pressing process can vary depending on the specific materials and parameters used, but it typically takes between 1 and 2 hours. This includes the time for heating, pressing, and cooling the PCB.
4. Can multilayer PCBs be repaired if damaged during pressing?
In most cases, PCBs that are damaged during pressing cannot be repaired and must be scrapped. This is why it is crucial to carefully control the pressing process and inspect the PCBs thoroughly to catch any defects as early as possible.
5. How much does multilayer PCB pressing cost?
The cost of multilayer PCB pressing can vary widely depending on factors such as the number of layers, the materials used, and the complexity of the design. In general, multilayer PCBs are more expensive than single- or double-sided PCBs due to the additional materials and processing steps required. However, the exact cost will depend on the specific manufacturer and the volume of PCBs being produced.
In conclusion, multilayer PCB pressing is a critical step in the manufacturing process of complex, high-density circuit boards. By carefully controlling the pressing process and using advanced technologies, manufacturers can produce reliable, high-quality multilayer PCBs for a wide range of applications.
Leave a Reply