Keywords: PCB, hard gold, thickness, plating, electronic circuits
Printed circuit boards (PCBs) form the backbone of modern electronics. From computers to smartphones to medical devices – virtually every electronic product relies on PCBs to connect components and circuits. One key element in PCB design and manufacturing is the plating – a coating of metal laid on top of the copper traces. Gold plating is commonly used for its high conductivity and resistance to corrosion and wear. But how thick should this precious metal coating be for optimal performance? Let’s explore the details of PCB hard gold plating thickness.
What is Hard Gold Plating?
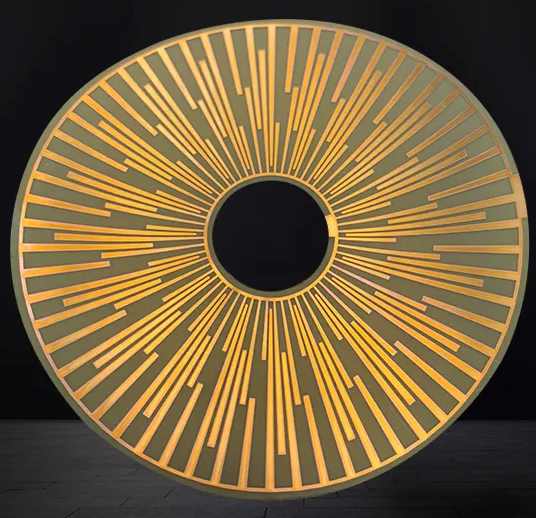
Purpose of Gold Plating
Gold provides excellent conductivity and does not tarnish or corrode over time like other metals such as copper or silver. This makes it ideal for coating the copper traces of PCBs used in demanding environments where reliability and longevity are critical.
Gold plating achieves several goals:
- Protect copper traces from corrosion and abrasion
- Allow soldering without oxidizing the joints
- Provide a surface for wire bonding in semiconductor packages
- Enhance conductivity between boards and connectors
Hard vs Soft Gold
There are two main types of gold plating for PCBs:
Soft gold is pure gold, very malleable but prone to scratches and wear.
Hard gold is gold alloyed with other metals like cobalt, nickel, or iron to increase hardness and durability. The most common alloy is with cobalt at 1-5%.
Hard gold is able to withstand repeated insertions and removals of connectors without wearing down the surface. For PCBs that will need to survive thousands of mating cycles, hard gold is the preferred choice.
What Determines Hard Gold Thickness?
The ideal thickness of hard gold plating depends on several factors:
Application Requirements
What is the intended use and environment of the PCB? Thicker gold layers are recommended for boards in harsh conditions with exposure to abrasion, temperature swings, humidity, and frequent mating connections. Medical, military, and aerospace applications often specify thicker gold.
Budget
Thicker gold plating costs more – both in materials and processing time. So cost is a key factor in determining gold thickness.
Manufacturing Process
The plating equipment and process used also impacts final thickness. Thicker layers may require multiple plating steps or longer plating times.
Industry Standards
Certain standards bodies like IPC provide guidelines on minimum gold thickness for various PCB types. Common requirements are:
- IPC Class 2 – 0.5-2.5 microns
- IPC Class 3 – 2.5 – 10 microns
- Connectors – 2-25 microns
Performance Requirements
Thicker gold provides higher conductivity and robustness against wear and soldering. So the electrical and lifespan demands influence thickness.
Typical Thickness Ranges
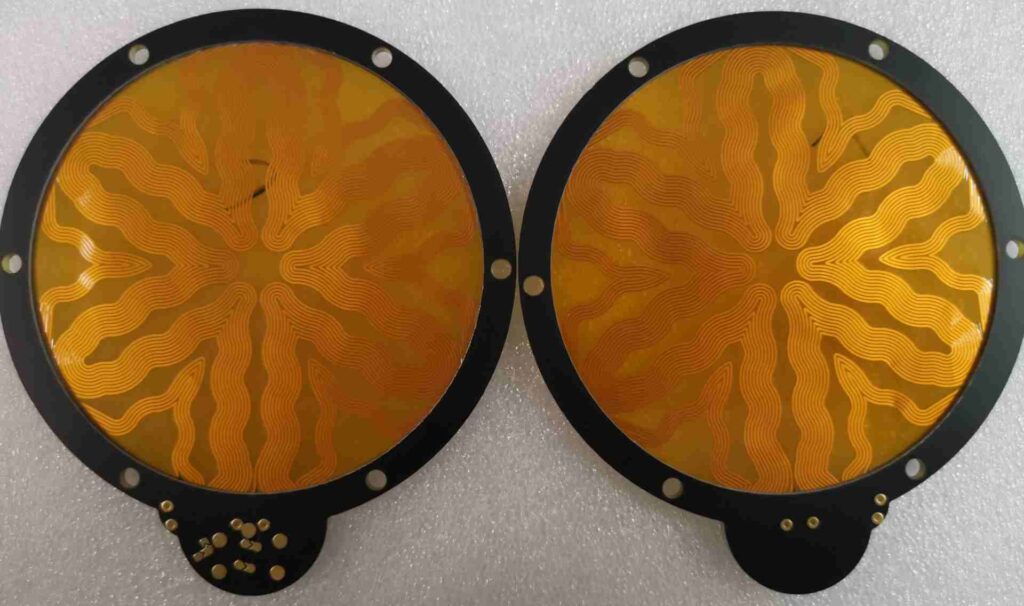
Based on the above criteria, here are typical hard gold thickness ranges:
0.5-2 microns
This is the minimum thickness for most PCBs. It provides basic corrosion protection, solderability, and conductivity. Common for cost-sensitive consumer electronics.
2-5 microns
Recommended for industrial grade electronics where reliability is more critical. Can withstand some mating cycles and abrasion resistance needed.
5-25 microns
Used for harsh environments like military, aerospace, and medical. Highest durability against corrosion, scratching, and frequent matings. Optimizes conductivity over 30+ year lifespan.
50+ microns
Only for specialized applications like high-power electronics. Very thick gold provides maximum conductivity and protection. But also costly.
Recommended Thickness By Application
Here are typical hard gold thickness recommendations based on application:
Consumer Electronics
- Cell phones, laptops, IoT devices: 0.5-2 microns
- Wearables, smart home: 1-2 microns
Automotive
- Engine control units: 2-5 microns
- Sensors: 2-5 microns
- High temperature areas: 5+ microns
Industrial
- PLCs, controllers: 2-5 microns
- Robotics: 2-10 microns
Medical Devices
- Implantable devices: 5-10 microns
- Diagnostic equipment: 2-5 microns
- Life support systems: 10+ microns
Aerospace/Defense
- Avionics: 5-25 microns
- Radars, communications: 10-25 microns
Connectors and Headers
- General use: 2-5 microns
- High-durability connectors: 10-25 microns
Key Factors in Determining Thickness
To summarize, the key factors to determine appropriate hard gold plating thickness are:
- Reliability requirements – Higher reliability needs thicker gold
- Operating environment – Harsh conditions require thicker layers
- PCB technology – HDI and flex circuits need more gold than rigid PCBs
- Budget constraints – More gold costs more
- Product lifespan – Longer lifespan (10+ years) benefits from thicker plating
- Industry standards – Meet minimum thickness values per application standards
- Soldering methods – Multiple heat cycles need more gold than single soldering
- Conductivity needs – High speed/high power demands thicker plating
Hard Gold Plating Process
The actual plating process involves several steps to deposit uniform, durable hard gold onto PCB copper traces.
1. Surface Preparation
The copper is cleaned and microetched to remove oxides and roughen the surface. This improves adhesion of subsequent layers.
2. Nickel Plating
A layer of nickel (2-5 microns) is plated first to protect the copper traces. Nickel provides a barrier against copper migration.
3. Hard Gold Deposition
The gold-cobalt alloy is plated to the required thickness based on specifications. Tight process controls during plating ensures proper hardness and color.
4. Post-Plating Treatment
A baking process helps to relieve stress and enhance hardness in the gold-cobalt alloy deposit.
5. Testing and QA
100% testing of plated boards verifies gold thickness meets specifications. Other tests check hardness, porosity, and solderability.
Frequently Asked Questions
Here are answers to some common FAQs about PCB hard gold plating thickness:
Q: Does thicker gold increase conductivity?
A: Yes, to a point. Going from 0.5 microns to 2 microns significantly boosts conductivity. But above 10 microns, the gains are small.
Q: Can gold plating thickness be measured?
A: Yes, X-ray fluorescence (XRF) or eddy current methods can accurately measure PCB gold thickness.
Q: Is hardness affected by thickness?
A: Hardness is more dependent on the alloy composition. But in general, thicker gold is slightly harder.
Q: Does the plating process impact thickness uniformity?
A: Yes, process controls like rack loading and solution agitation are key to ensuring an even deposit.
Q: How often does gold plating need to be reapplied?
A: Under normal conditions, hard gold plating should last the lifetime of the PCB with no need for replating.
Conclusion
Specifying the optimal hard gold plating thickness for a PCB application requires balancing performance, durability, and budget. Typical thicknesses range from 0.5 microns for consumer devices to 25+ microns for extreme environments. Factors like reliability needs, operating conditions, product lifespan and industry standards help determine the ideal gold thickness. With the proper gold plating, PCBs can deliver long-lasting connectivity and performance.
Leave a Reply