Introduction to Double-sided SMT Assembly
Double-sided Surface Mount Technology (SMT) assembly is a sophisticated manufacturing process that allows electronic components to be mounted on both sides of a Printed Circuit Board (PCB). This advanced technique has revolutionized the electronics industry by enabling the production of compact, high-density, and cost-effective electronic devices. In this comprehensive article, we will delve into the intricacies of double-sided SMT Assembly, exploring its benefits, challenges, and the step-by-step process involved.
Key Benefits of Double-Sided SMT Assembly
- Increased Component Density
- Enhanced Functionality
- Reduced PCB Size and Weight
- Improved Reliability and Performance
- Cost-Effectiveness
Challenges in Double-Sided SMT Assembly
- Component Placement Accuracy
- Reflow Soldering Complexity
- Potential for Component Damage
- Inspection and Quality Control
The Double-Sided SMT Assembly Process
Step 1: PCB Design and Preparation
The double-sided SMT assembly process begins with the design and preparation of the PCB. The PCB layout is created using specialized software, taking into account the component placement, routing, and design rules specific to double-sided assembly. The PCB is then manufactured, typically using a multi-layer process to accommodate the high component density.
Key Considerations in PCB Design for Double-Sided SMT Assembly
- Component Placement Strategy
- Thermal Management
- Signal Integrity
- Manufacturing Constraints
Step 2: Solder Paste Printing
Once the PCB is ready, the next step is to apply solder paste to the component pads on both sides of the board. This is typically done using a stencil printing process, where a metal stencil with apertures corresponding to the component pads is aligned with the PCB. Solder paste, a mixture of powdered solder and flux, is then spread over the stencil, filling the apertures and depositing the paste onto the pads.
Solder Paste Printing Process
- Stencil Alignment
- Solder Paste Application
- Inspection and Correction
Step 3: Component Placement
With the solder paste applied, the PCB is ready for component placement. This is typically done using automated pick-and-place machines, which use vacuum nozzles to pick up components from feeders and place them precisely on the solder paste-coated pads. The placement process is guided by computer-aided design (CAD) data, ensuring accurate positioning of each component.
Component Placement Equipment and Techniques
- Automated Pick-and-Place Machines
- Vision Systems for Alignment
- Component Feeders and Packaging
- Placement Accuracy and Speed
Step 4: Reflow Soldering
After component placement, the PCB undergoes reflow soldering, where it is subjected to a controlled heating process to melt the solder paste and form permanent electrical and mechanical connections between the components and the PCB. In double-sided SMT assembly, the reflow soldering process is performed twice, once for each side of the board.
Reflow Soldering Process
- Preheat Zone
- Soak Zone
- Reflow Zone
- Cooling Zone
Challenges in Double-Sided Reflow Soldering
- Thermal Profile Optimization
- Component Shadowing
- Solder Joint Reliability
Step 5: Inspection and Quality Control
Following the reflow soldering process, the assembled PCBs undergo thorough inspection and quality control to ensure the integrity of the solder joints and the overall functionality of the board. Various techniques, such as automated optical inspection (AOI), X-ray inspection, and electrical testing, are employed to detect any defects or issues.
Common Inspection Methods
- Automated Optical Inspection (AOI)
- X-Ray Inspection
- In-Circuit Testing (ICT)
- Functional Testing
Defect Types and Remediation
- Solder Bridges and Short Circuits
- Component Misalignment
- Insufficient or Excessive Solder
- Rework and Repair Techniques
Advanced Techniques in Double-Sided SMT Assembly
Flexible PCB Assembly
Flexible PCBs, also known as flex circuits, are increasingly used in double-sided SMT assembly to create compact, lightweight, and bendable electronic devices. The assembly process for flexible PCBs involves unique challenges, such as handling the delicate substrate and ensuring reliable solder joints under flexing conditions.
Key Considerations in Flexible PCB Assembly
- Material Selection
- Bend Radius and Strain Relief
- Solder Joint Reliability
- Handling and Fixturing
Package-on-Package (PoP) Assembly
Package-on-Package (PoP) assembly is an advanced technique that involves stacking multiple integrated circuit (IC) packages on top of each other, enabling even higher component density and functionality. In double-sided SMT assembly, PoP can be used to create complex, multi-layer structures with enhanced performance.
PoP Assembly Process
- Bottom Package Mounting
- Top Package Stacking
- Reflow Soldering
- Underfill Application
Embedded Component Assembly
Embedded component assembly takes double-sided SMT to the next level by integrating passive components, such as resistors and capacitors, within the layers of the PCB itself. This technique offers several advantages, including further miniaturization, improved electrical performance, and reduced component count on the surface of the board.
Key Benefits of Embedded Component Assembly
- Reduced PCB Size and Thickness
- Enhanced Electrical Performance
- Improved Reliability
- Simplified Surface Assembly
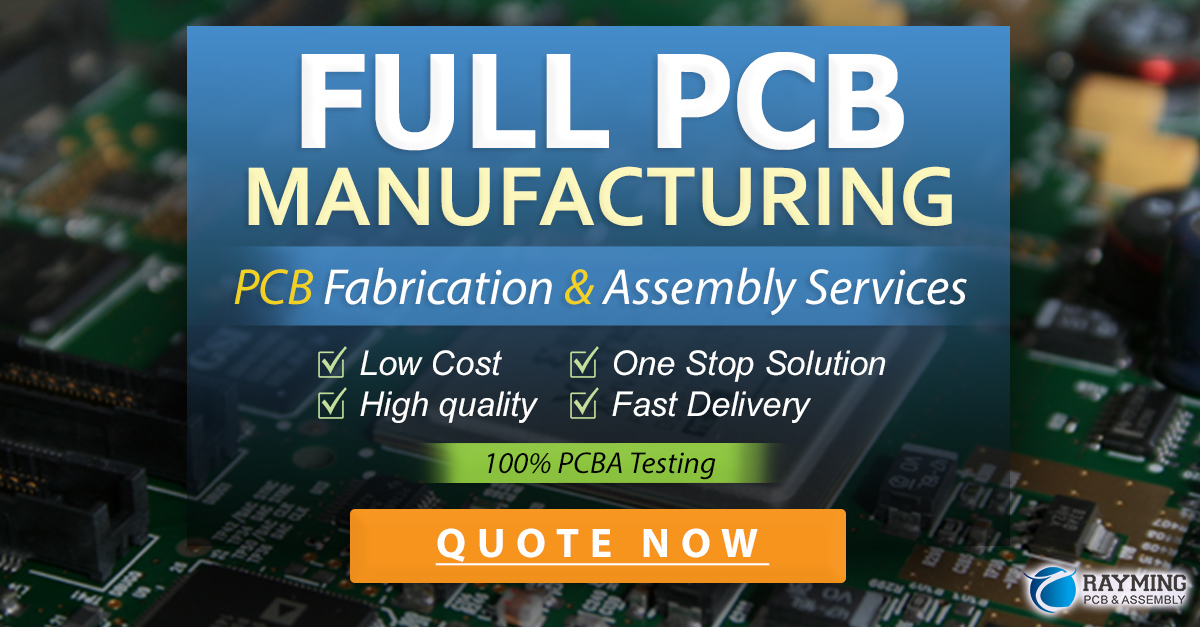
Future Trends in Double-Sided SMT Assembly
As the electronics industry continues to evolve, double-sided SMT assembly is expected to adapt to new challenges and demands. Some of the future trends in this field include:
- Miniaturization and High-Density Assembly
- Advanced Materials and Substrates
- Automation and Smart Manufacturing
- Integration of Additive Manufacturing Techniques
- Environmental Sustainability and Green Electronics
Conclusion
Double-sided SMT assembly is a complex and sophisticated manufacturing process that has enabled the production of compact, high-performance electronic devices. By allowing components to be mounted on both sides of the PCB, this technique offers numerous benefits, including increased component density, enhanced functionality, and cost-effectiveness. However, double-sided SMT assembly also presents unique challenges, such as component placement accuracy, reflow soldering complexity, and inspection requirements.
As technology advances, double-sided SMT assembly continues to evolve, incorporating advanced techniques like PCB-Assembly/”>flexible PCB assembly, Package-on-Package (PoP) assembly, and embedded component assembly. Future trends in this field are expected to focus on further miniaturization, automation, and environmental sustainability.
By understanding the intricacies of double-sided SMT assembly and staying abreast of the latest developments, electronics manufacturers can leverage this powerful technique to create innovative, high-quality products that meet the ever-increasing demands of the modern world.
Frequently Asked Questions (FAQ)
- What is the main difference between single-sided and double-sided SMT assembly?
-
Single-sided SMT assembly involves mounting components on only one side of the PCB, while double-sided SMT assembly allows components to be mounted on both sides of the board, resulting in higher component density and enhanced functionality.
-
What are the key benefits of using double-sided SMT assembly?
-
The key benefits of double-sided SMT assembly include increased component density, enhanced functionality, reduced PCB size and weight, improved reliability and performance, and cost-effectiveness.
-
What are some of the challenges faced in double-sided SMT assembly?
-
Some of the challenges in double-sided SMT assembly include ensuring accurate component placement, managing the complexity of the reflow soldering process, preventing component damage, and conducting thorough inspection and quality control.
-
How does the reflow soldering process work in double-sided SMT assembly?
-
In double-sided SMT assembly, the reflow soldering process is performed twice, once for each side of the board. The PCB is subjected to a controlled heating process that melts the solder paste and forms permanent electrical and mechanical connections between the components and the PCB.
-
What are some of the advanced techniques used in double-sided SMT assembly?
- Advanced techniques in double-sided SMT assembly include flexible PCB assembly, which involves assembling components on bendable substrates; Package-on-Package (PoP) assembly, which enables stacking of multiple IC packages; and embedded component assembly, where passive components are integrated within the layers of the PCB itself.
Leave a Reply