What is Galvanising?
Galvanising is a process of applying a protective zinc coating to steel or iron to prevent rusting. The most common method is hot-dip galvanizing, in which parts are submerged in a bath of molten zinc. This process forms a thick, durable, and corrosion-resistant coating that can protect the underlying metal for many years.
Galvanising PCBs: An Overview
While galvanising is traditionally associated with steel and iron, the term “galvanising PCBs” refers to applying a protective coating to printed circuit boards (PCBs) to enhance their durability and resistance to environmental factors. However, the process used for PCBs is not the same as the hot-dip galvanizing method used for steel.
Why Galvanise PCBs?
PCBs are essential components in modern electronics, found in everything from smartphones and laptops to industrial control systems and medical devices. These boards are subjected to various environmental stresses, such as:
- Temperature fluctuations
- Humidity
- Dust and debris
- Chemical exposure
- Mechanical stress
Over time, these factors can lead to corrosion, short circuits, and other issues that can cause device failure. By applying a protective coating to PCBs, manufacturers can improve their reliability and extend their lifespan.
Methods for Galvanising PCBs
There are several methods for applying protective coatings to PCBs, each with its own advantages and disadvantages. The most common methods include:
Conformal Coating
Conformal coating involves applying a thin, polymeric film to the surface of a PCB. This coating conforms to the contours of the board, providing a barrier against moisture, dust, and other contaminants. Common conformal coating materials include:
- Acrylic
- Silicone
- Polyurethane
- Epoxy
- Parylene
Material | Advantages | Disadvantages |
---|---|---|
Acrylic | Easy to apply and repair, cost-effective | Limited chemical and abrasion resistance |
Silicone | Excellent flexibility and temperature resistance | Difficult to apply and repair |
Polyurethane | Good humidity and abrasion resistance | Can be difficult to remove for repairs |
Epoxy | High chemical and abrasion resistance | Brittle and can crack under thermal stress |
Parylene | Uniform, thin coating with excellent barrier properties | Expensive and requires specialized equipment |
Potting
Potting involves encapsulating a PCB in a solid compound, typically a thermosetting polymer such as epoxy or silicone. This process provides excellent protection against moisture, shock, and vibration. However, potted PCBs are difficult to repair and may suffer from thermal stress due to the different expansion rates of the potting material and the PCB.
Encapsulation
Encapsulation is similar to potting but involves placing the PCB in a pre-formed shell or case and then filling the case with a protective compound. This method provides many of the same benefits as potting but allows for easier assembly and repair.
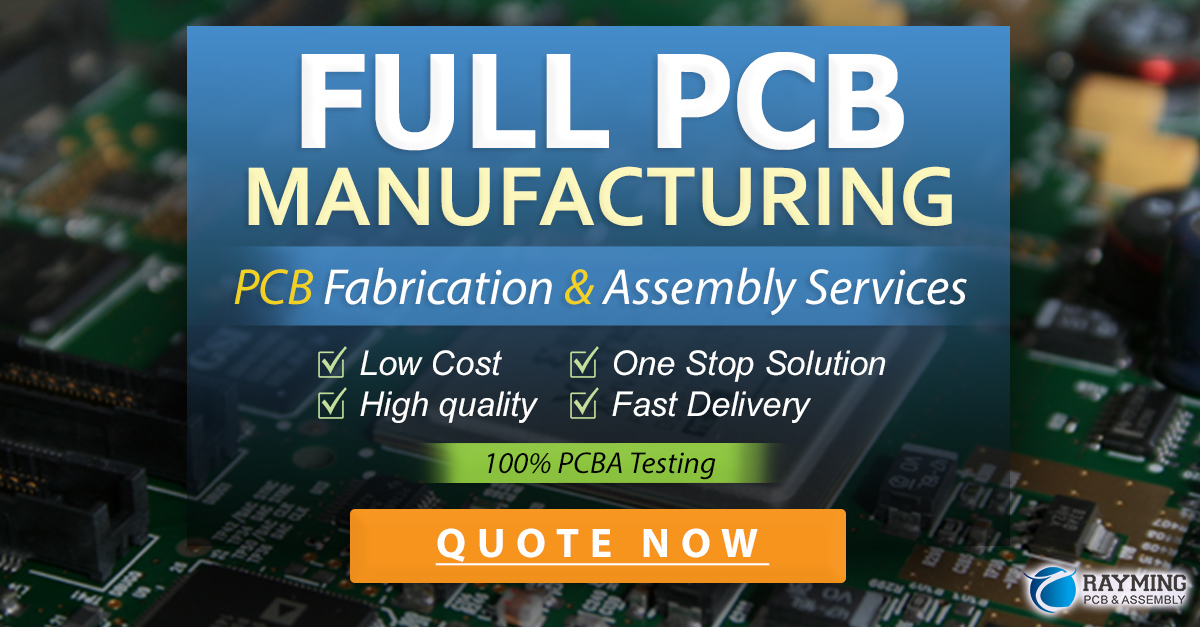
Choosing the Right Galvanising Method
When selecting a method for galvanising PCBs, consider the following factors:
- Environmental conditions: What types of stresses will the PCB be exposed to?
- Application requirements: Does the PCB need to be repairable, or is a permanent encapsulation acceptable?
- Cost: What is the budget for protective coatings, and how does this impact the choice of materials and methods?
- Manufacturing process: Can the chosen galvanising method be easily integrated into the existing PCB manufacturing process?
By carefully evaluating these factors, manufacturers can choose the most appropriate galvanising method for their specific PCBs and applications.
Advantages of Galvanising PCBs
Galvanising PCBs offers several key benefits:
-
Enhanced durability: Protective coatings help PCBs withstand harsh environmental conditions, increasing their lifespan and reducing the need for frequent replacements.
-
Improved reliability: By preventing corrosion, short circuits, and other issues, galvanised PCBs are more reliable and less likely to fail during operation.
-
Cost savings: While galvanising PCBs requires an initial investment, the long-term cost savings from reduced maintenance and fewer failures can be significant.
-
Compliance with industry standards: Many industries, such as automotive and aerospace, have strict requirements for PCB Protection. Galvanising helps manufacturers meet these standards and qualify for use in demanding applications.
Challenges and Considerations
Despite the benefits of galvanising PCBs, there are some challenges and considerations to keep in mind:
-
Material compatibility: Not all protective coatings are compatible with every PCB material or component. Manufacturers must carefully select coatings that will not negatively impact the performance or functionality of the PCB.
-
Application process: Some galvanising methods, such as conformal coating, require specialized equipment and skilled operators to ensure consistent and reliable results.
-
Rework and repair: Galvanised PCBs can be more difficult to rework or repair, as the protective coating must be removed and reapplied after any modifications.
-
Cost: While galvanising PCBs can lead to long-term cost savings, the initial investment in materials, equipment, and training can be substantial.
FAQ
-
Q: Is galvanising the same as conformal coating?
A: No, galvanising is a general term for applying a protective coating to PCBs, while conformal coating is a specific method that involves applying a thin, polymeric film to the board’s surface. -
Q: Can all PCBs be galvanised?
A: Most PCBs can be galvanised, but the specific method and materials used may vary depending on the board’s design, components, and intended application. -
Q: How long does the galvanising process take?
A: The time required for galvanising PCBs depends on the chosen method and the size and complexity of the board. Conformal coating can be completed in minutes to hours, while potting and encapsulation may take several hours to cure fully. -
Q: Does galvanising PCBs affect their performance?
A: When done correctly, galvanising should not negatively impact PCB performance. However, improper application or incompatible materials can lead to issues such as increased capacitance or reduced heat dissipation. -
Q: How much does it cost to galvanise PCBs?
A: The cost of galvanising PCBs varies depending on the method, materials, and scale of production. In general, conformal coating is the most cost-effective option, while potting and encapsulation are more expensive due to the larger amounts of materials required.
Conclusion
Galvanising PCBs is an essential process for improving the durability, reliability, and longevity of these critical components. By applying protective coatings such as conformal coating, potting, or encapsulation, manufacturers can shield PCBs from environmental stresses and ensure their proper function in a wide range of applications.
When choosing a galvanising method, it is crucial to consider factors such as the intended application, environmental conditions, cost, and manufacturing process. By carefully evaluating these aspects and selecting the most appropriate method and materials, manufacturers can effectively protect their PCBs and enjoy the long-term benefits of galvanising.
As electronics continue to advance and find use in increasingly demanding environments, the importance of galvanising PCBs will only continue to grow. By staying informed about the latest methods and best practices for PCB protection, manufacturers can position themselves to create more robust, reliable, and cost-effective products that meet the needs of their customers and the evolving market.
Leave a Reply