Introduction
Printed circuit boards (PCBs) form the core of all modern electronic devices. With some basic understanding of electronics and PCB design software, anyone can design their own PCBs. This allows inventors, hobbyists and electronics enthusiasts to create customized circuit boards for prototype development, small batch production or simply for self-education. This article provides a step-by-step guide on designing your own PCB successfully.
Step 1: Develop the Circuit Schematic
The first step is to create the electronic circuit schematic depicting the components and their interconnectivity. This involves:
Determine circuit requirements
- Define the input/output and functionality needed from the circuit. List all required sub-systems.
- Specify key parameters like voltage levels, power requirements, frequency response etc.
Select components
- Determine the types of components (resistors, capacitors, ICs etc) and their values/ratings required to implement the circuit.
- Group related components into functional sub-circuits or modules.
Draw circuit diagram
- Use EDA software to create the circuit schematic, adding symbols for each component.
- Label components with their values and designate unique names for identification.
- Connect symbols to define electrical connectivity and buses for common signals.
- Annotate signal polarities, pin numbers, voltages and timing relationships.
Validate design
- Perform circuit simulation to validate functionality and electrical performance.
- Refine schematic by iterating based on simulation results.
Step 2: Learn PCB Design Software
With the schematic complete, you need to learn to use EDA or PCB design software to design the physical layout of the board. Some options are:
- Eagle – Easy to learn software with free version
- KiCad – Free, open-source software with great capabilities
- Altium – Used by professionals, full featured with some free tools
- OrCAD – Powerful tool from Cadence, free trial available
- DipTrace – Affordable tool good for hobbyists
Key functionality
- Component library – Symbols, footprints, and 3D models
- PCB editor – Create board outline and component placement
- Autorouter – To automatically route connections
- DRC engine – Checks design rule violations
- Layer stackup – Define board layers and properties
- Manufacturing outputs – Gerber, drill and pick-and-place files
Step 3: Plan the Board Layout
Before routing the board, planning is important for good layout:
Component placement
- Group related components together
- Ensure adequate spacing for routing and heat dissipation
- Place priority components first
Decoupling capacitors
- Place bypass/decoupling caps close to ICs power pins
High speed signals
- Keep traces short, control impedance
Board orientation
- Locate connectors, indicators as per product design
Thermal design
- Ensure proper heat sinking and airflow
Grounding
- Define ground zones for noise reduction
Board outline
- Consider housing dimensions and mounting style
Step 4: Route the PCB
With components placed, we can route the connections between pins:
Link schematic
- Associate component footprints with schematic symbols
Autorouter
- Quickly route connections automatically
Manual routing
- Precisely route traces meeting length, impedance and spacing constraints
Bypass capacitors
- Route short tracks between supply pins and bypass caps
Bus routing
- Use wider traces or polygons to route bus signals
Power and ground
- Use planes to distribute power and ground nets
High speed
- Control impedance, length matching, terminate lines
Crossing traces
- Route perpendicular traces on different layers
Post-routing cleanup
- Optimize traces, remove neckdowns, tidy up tracks
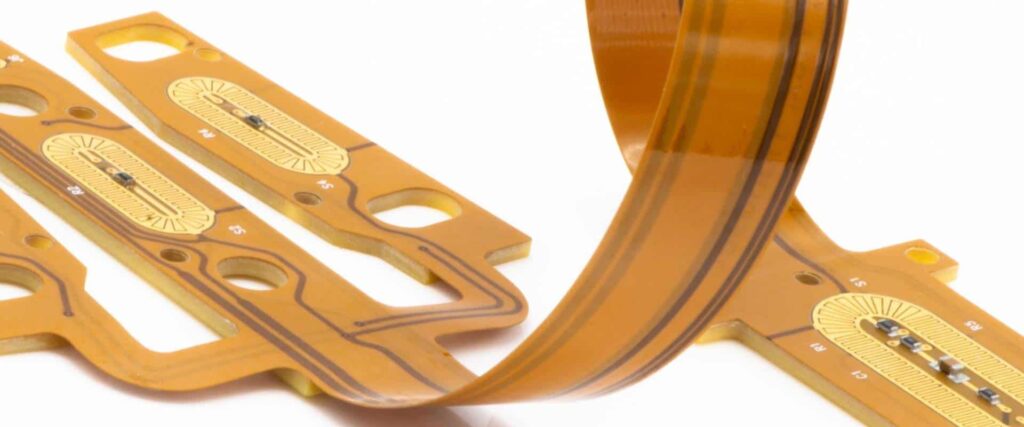
Step 5: Complete PCB Design Requirements
Finish board layout by meeting all design rules and manufacturing requirements:
Design rules check
- Validate traces widths, spacings, mask expansion etc
Copper pour
- Fill empty spaces on copper layers with ground planes
Finish selection
- Specify surface platings – HASL, ENIG, Immersion silver etc
Silkscreen
- Add labels, markings using silkscreen layer
Solder mask
- Define solder mask openings for paste deposition
Panelization
- Add mouse bites, tooling holes and borders
Stackup review
- Validate board stackup configuration
3D view
- Visually inspect clearance and footprints
Step 6: Generate Manufacturing Outputs
To build the designed PCBs, we need to generate the required manufacturing data:
Gerber files
- Industry standard format for PCB fabrication data
Drill file
- Specify drill locations and sizes for holes
Pick-and-place file
- Position and rotation for automated SMT assembly
BOM or bill of materials
- List of components with suppliers and ids
Assembly drawings
- Mechanical drawings to aid assembly
Fabrication drawings
- Layer plots, stackup diagrams, outlines etc
Readme file
- Design notes and instructions for manufacturer
Step 7: Select a Manufacturer
To produce the designed boards, you need to choose a suitable PCB manufacturer:
Volume
- Prototype boards vs mass production runs
Lead time
- Days to weeks depending on priority
Capabilities
- Technology support – multilayer, HDI, flex, RF etc
Quality
- Valued providers offer test coupons and qualification data
Assembled boards
- Many offer full assembly as turnkey service
Cost
- Balance budget constraints with features, quality and service
Online PCB fabs
- Convenient ordering and rapid delivery
Step 8: Review the Manufactured Boards
It’s crucial to inspect the boards received before assembling components:
Visual inspection
- Check for any scratches, nicks, handling marks etc
Dimensional check
- Validate board outline and mounting hole positions
Test points
- Probe test points to verify electrical connectivity
Microsection
- Check inner layer registration and copper bond
Plating quality
- Look for uniform plating thickness and surface finish
Impedance testing
- Use TDR to measure matched transmission line impedance
Rework if needed
- Get defects reworked by manufacturer under warranty
Step 9: Assemble and Test
With validated boards, we can proceed with populating and bringing up the design:
Procure components
- Order parts for assembly from suppliers
Soldering
- Hand solder components or use reflow process
Inspection
- Visually inspect for missing or misplaced parts
Apply power
- Gradually power up the board using current limited supply
Functional test
- Verify key functionality against circuit requirements
Debugging
- Troubleshoot any issues using multimeter, oscilloscope etc
Enclosures
- Mount boards along with hardware into enclosure
Certifications
- Get any regulatory or product safety approvals
Step 10: Document and Iterate
Documentation is key for replicability, enhancements and knowledge transfer:
Schematics
- Fully annotated schematics with component references
Bill of materials
- Approved vendor list with part numbers
Board files
- Release manufacturing design files and outputs
Design notes
- Assumptions, considerations and lessons captured
Mechanical drawings
- Enclosure and assembly drawings
Version control
- Maintain revisions and configuration management
Further enhancements
- List new features and changes planned in next revision
Knowledgebase
- Build database of reference designs and solutions
Following these steps will enable you to successfully design, develop and deploy your custom PCB and unlock the possibilities of electronics innovation!
Frequently Asked Questions
Question 1: What are some important considerations in selecting PCB design software?
Answer 1: Key considerations in choosing PCB design software:
- Features – Schematic capture, autorouter, design rule checks, 3D viewer etc.
- Ease of use – Intuitive UI and short learning curve help beginners.
- Library – Extensive component libraries speed up design process.
- Output and integration – Industry standard file formats for manufacturing and simulation.
- Cost – Free or low cost tools reduce expense for hobbyists.
- Support – Online resources, tutorials, videos and community aid learning.
- Future needs – Scalability for more complex designs as you progress.
Question 2: What are good online resources to learn PCB design?
Answer 2: Useful online resources for learning PCB design include:
- Software documentation – Many tools provide extensive manuals and docs to refer.
- Tutorials and videos – Step-by-step beginner tutorials at aggregators like YouTube.
- Courses – Structured online courses at sites like Udemy or Coursera.
- Forums and groups – Active discussions at Reddit, Quora, technology forums etc.
- Reference designs – Open source designs with documentation aid learning.
- Blogs – Many designers blog about the workflows and tips.
- Manufacturers website – Provides resources on capabilities and design considerations.
- Community meets – Attend local meets of PCB designers to learn.
Question 3: What are some key tips for routing a PCB cleanly?
Answer 3: Tips for clean routing:
- Plan routes beforehand for difficult connections.
- Route in order of priority – power, clock signals first.
- Use grid for tidy trace angles – 45, 90 degrees etc.
- Group similar signals using buses with parallel traces.
- Use curved traces for better aesthetics.
- Avoid right angle trace junctions. Use rounded bends or 45 degree turns.
- Replace necked down traces with full width tracks for reliable current flow.
- Use ground or power planes for easier routing over solid regions.
- Add silkscreen labels clearly identifying components and signals.
Question 4: How can I get low volume PCBs prototyped cost effectively?
Answer 4: Options for low cost PCB prototyping:
- Use PCB fabs with low minimum order quantities like 1 or 5 boards.
- Order boards in small panel sizes for better cost.
- Standardize processes like standard drill sizes where possible.
- Minimize special processes like 4-layer board instead of 6-layer.
- Order from local manufacturers to reduce shipping cost.
- Avail discounts for new customers or multi-order.
- Use coupon codes and promos from fabrication marketplaces.
- Lower specs like 1oz copper instead of 2 oz to save cost.
- Undersize large copper zones to use less copper.
Question 5: What tools are used in PCB debugging and testing?
Answer 5: Common tools used for PCB testing and debugging are:
- Multimeter – Measures voltage, current, continuity, resistance.
- Oscilloscope – Visualizes signals, measures frequency, rise times.
- Logic analyzer – Captures digital signal timings and logic states.
- Signal generator – Generates test waveforms as input stimulus.
- Spectrum analyzer – Analyze signal power and frequency components.
- Bus pirate – Debug serial buses like SPI, I2C.
- Power supply – Clean, regulated, variable DC power source.
- EMI receiver – Detects electromagnetic interference issues.
- Thermal camera – Visualizes hot spots and heat dissipation.
Leave a Reply