Introduction to High-Tg PCBs
High-Tg PCBs, also known as high glass transition temperature printed Circuit Boards, are a type of PCB that can withstand higher temperatures compared to standard PCBs. The glass transition temperature (Tg) refers to the temperature at which the material transitions from a rigid, glassy state to a more flexible, rubbery state. High-Tg PCBs are designed to maintain their structural integrity and electrical properties even when exposed to elevated temperatures.
What is Tg in PCBs?
Tg, or glass transition temperature, is a critical parameter in PCB Manufacturing. It represents the temperature at which the PCB Material undergoes a significant change in its physical properties. Below the Tg, the material is in a glassy state, characterized by its rigidity and dimensional stability. Above the Tg, the material becomes more flexible and can experience softening or deformation.
In PCBs, the Tg is determined by the properties of the base material, which is typically a composite of glass fibers and epoxy resin. The higher the Tg, the better the PCB can withstand high temperatures without compromising its structural integrity or electrical performance.
Importance of High-Tg PCBs
High-Tg PCBs are essential in applications where the circuit board is exposed to elevated temperatures. Some of the key reasons why high-Tg PCBs are important include:
-
Thermal stability: High-Tg PCBs maintain their structural integrity and dimensions even when subjected to high temperatures. This stability is crucial in applications where the PCB needs to remain flat and resist warping or deformation.
-
Reliability: With their ability to withstand high temperatures, high-Tg PCBs offer improved reliability compared to standard PCBs. They are less likely to experience failures or malfunctions due to thermal stress, ensuring the long-term performance of the electronic device.
-
High-temperature environments: High-Tg PCBs are suitable for use in environments where high temperatures are common, such as automotive, aerospace, and industrial applications. They can withstand the harsh conditions and continue to function reliably.
-
Soldering process compatibility: The higher Tg allows high-Tg PCBs to withstand the high temperatures encountered during soldering processes, such as lead-free soldering. This compatibility ensures that the PCB can be assembled without compromising its integrity.
RF4 PCBs and Their Tg Properties
RF4 is a popular high-Tg PCB material that offers excellent thermal and electrical properties. Let’s explore the characteristics and advantages of RF4 PCBs.
What is RF4?
RF4, also known as Rogers 4000 series, is a glass-reinforced hydrocarbon and ceramic laminate material. It is specifically designed for high-frequency and high-speed digital applications. RF4 offers a combination of low dielectric loss, low moisture absorption, and high thermal conductivity, making it an ideal choice for demanding PCB Applications.
Tg Properties of RF4
One of the key advantages of RF4 is its high glass transition temperature (Tg). The Tg of RF4 can range from 280°C to 360°C, depending on the specific formulation. This high Tg allows RF4 PCBs to withstand extreme temperatures without compromising their performance.
The high Tg of RF4 provides several benefits:
-
Thermal stability: RF4 PCBs maintain their structural integrity and flatness even when exposed to high temperatures. This stability is essential in applications where dimensional accuracy is critical.
-
Reliable performance: With its high Tg, RF4 PCBs offer reliable performance in high-temperature environments. They can withstand the thermal stresses encountered during manufacturing processes and in-field operations.
-
Compatibility with lead-free soldering: The high Tg of RF4 makes it compatible with lead-free soldering processes, which typically require higher temperatures compared to traditional soldering methods. This compatibility ensures that RF4 PCBs can be assembled using modern soldering techniques without issue.
Advantages of RF4 PCBs
In addition to its high Tg, RF4 PCBs offer several other advantages:
-
Low dielectric loss: RF4 has a low dielectric constant (Dk) and low dissipation factor (Df), which minimizes signal loss and ensures high-speed signal integrity. This makes RF4 suitable for high-frequency applications.
-
Low moisture absorption: RF4 has a low moisture absorption rate, which helps maintain its electrical properties and prevents delamination or other moisture-related issues.
-
High thermal conductivity: RF4 has good thermal conductivity, allowing for efficient heat dissipation. This property helps in managing the thermal performance of the PCB and prevents overheating of components.
-
Dimensional stability: RF4 PCBs exhibit excellent dimensional stability, even in varying environmental conditions. This stability is crucial for maintaining the precise alignment of components and ensuring consistent performance.
Tg Options for High-Tg PCBs
When it comes to high-Tg PCBs, manufacturers offer a range of Tg options to suit different application requirements. Let’s explore the common Tg options available for high-Tg PCBs.
Standard Tg Options
Most high-Tg PCB Manufacturers offer a selection of standard Tg options. These options cater to the majority of high-temperature applications. Some common standard Tg options include:
Tg Range | Applications |
---|---|
170°C-180°C | General-purpose high-temperature applications |
200°C-210°C | Automotive and industrial electronics |
240°C-260°C | Aerospace and military applications |
These standard Tg options provide a balance between thermal performance and cost-effectiveness. They are suitable for a wide range of high-temperature applications and can be readily available from most high-Tg PCB manufacturers.
Custom Tg Options
In addition to standard Tg options, some high-Tg PCB manufacturers offer custom Tg options to meet specific application requirements. Custom Tg options allow for fine-tuning the thermal properties of the PCB to match the exact needs of the application.
Custom Tg options may include:
-
Specific Tg values: Manufacturers can provide PCBs with specific Tg values, such as 225°C or 280°C, based on the customer’s requirements. This level of customization ensures that the PCB’s thermal properties are optimized for the intended application.
-
Tg ranges: Some manufacturers offer PCBs with Tg ranges, such as 200°C-220°C or 260°C-280°C. These ranges provide flexibility in meeting the thermal requirements while allowing for some variation in the manufacturing process.
-
High Tg materials: Manufacturers can work with specific high Tg materials, such as polyimide or bismaleimide triazine (BT), to achieve even higher Tg values. These materials can offer Tg values exceeding 300°C for the most demanding high-temperature applications.
Custom Tg options provide greater flexibility and customization for specific application needs. However, they may require longer lead times and higher costs compared to standard Tg options.
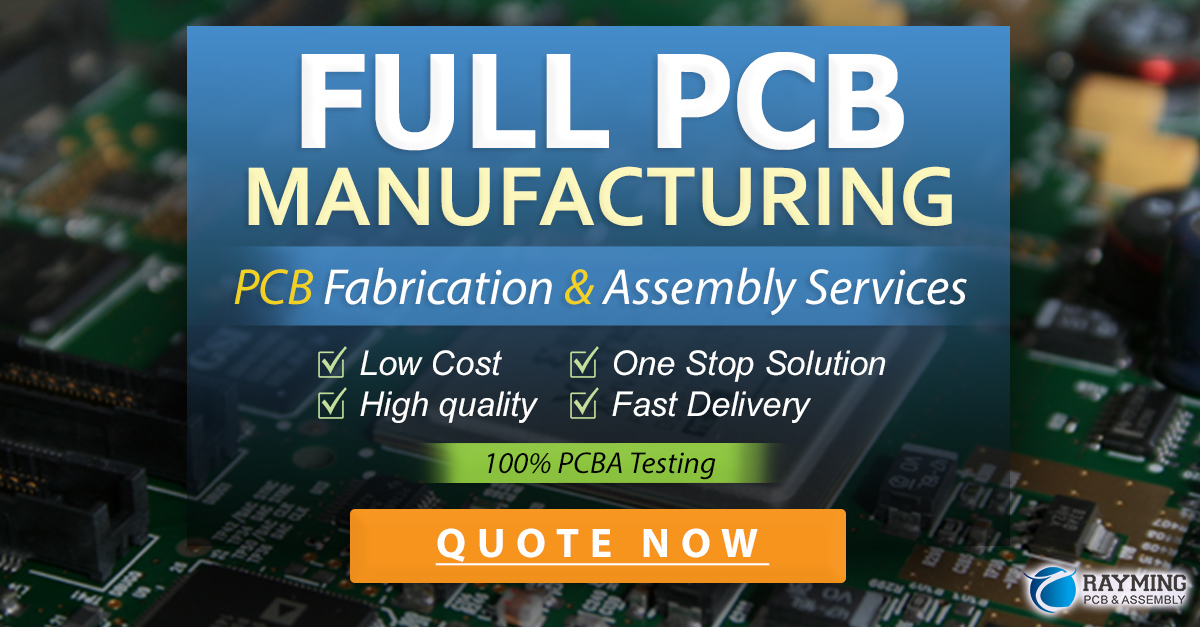
Manufacturing Process for High-Tg PCBs
The manufacturing process for high-Tg PCBs is similar to that of standard PCBs, but with additional considerations to ensure the desired thermal properties are achieved. Let’s overview the key steps involved in manufacturing high-Tg PCBs.
Material Selection
The first step in manufacturing high-Tg PCBs is selecting the appropriate base material. The base material determines the Tg of the PCB. High-Tg materials commonly used include:
- FR-4 with high Tg epoxy resin
- Polyimide
- Bismaleimide triazine (BT)
- RF4 (Rogers 4000 series)
The choice of material depends on the specific Tg requirements, electrical properties, and cost considerations of the application.
Lamination
Once the base material is selected, the next step is lamination. In this process, the copper foil is bonded to the base material using heat and pressure. The lamination process for high-Tg PCBs typically requires higher temperatures and pressures compared to standard PCBs to ensure proper bonding and maintain the high Tg properties.
Circuit Patterning
After lamination, the circuit pattern is transferred onto the PCB. This is typically done using photolithography and etching processes. The copper foil is selectively removed to create the desired circuit pattern. High-Tg PCBs may require special considerations during etching to ensure the integrity of the high Tg material.
Drilling and Plating
Holes are drilled in the PCB to accommodate components and vias. The holes are then plated with copper to establish electrical connections between layers. High-Tg PCBs may require special drilling parameters and plating processes to ensure the holes are properly formed and the plating adheres well to the high Tg material.
Solder Mask and Silkscreen
A solder mask is applied to the PCB to protect the copper traces and prevent solder bridging. Silkscreen is also applied to provide component designators and other markings. High-Tg PCBs may require high-temperature solder masks and silkscreens to withstand the elevated temperatures encountered during assembly and operation.
Surface Finish
The final step in the manufacturing process is applying a surface finish to the exposed copper areas. Common surface finishes for high-Tg PCBs include:
- Hot Air Solder Leveling (HASL)
- Electroless Nickel Immersion Gold (ENIG)
- Immersion Silver
- Immersion Tin
The choice of surface finish depends on the solderability requirements, environmental factors, and compatibility with the high Tg material.
Applications of High-Tg PCBs
High-Tg PCBs find applications in various industries where high-temperature performance is critical. Let’s explore some of the common applications of high-Tg PCBs.
Automotive Electronics
High-Tg PCBs are widely used in automotive electronics due to their ability to withstand the harsh environmental conditions encountered in vehicles. Some automotive applications of high-Tg PCBs include:
- Engine control units (ECUs)
- Transmission control modules
- Power inverters for electric vehicles
- Lighting systems
- Infotainment systems
The high Tg properties of the PCBs ensure reliable performance even in the presence of high temperatures, vibrations, and thermal cycling.
Industrial Electronics
Industrial environments often involve high temperatures, harsh chemicals, and rugged conditions. High-Tg PCBs are suitable for industrial electronics applications such as:
- Motor drives and controls
- Power supplies
- Instrumentation and sensors
- Robotics and automation systems
- Oil and gas exploration equipment
The thermal stability and robustness of high-Tg PCBs make them ideal for industrial applications where reliability and long-term performance are paramount.
Aerospace and Defense
Aerospace and defense applications demand the highest level of reliability and performance. High-Tg PCBs are used in various aerospace and defense systems, including:
- Avionics systems
- Radar and communication equipment
- Satellite systems
- Military vehicles and weaponry
- Unmanned aerial vehicles (UAVs)
The high Tg properties of the PCBs ensure they can withstand the extreme temperatures, vibrations, and environmental conditions encountered in aerospace and defense applications.
High-Temperature Environments
High-Tg PCBs are essential in any application where high temperatures are present. Some examples of high-temperature environments where high-Tg PCBs are used include:
- Downhole drilling equipment
- Geothermal power systems
- Industrial ovens and furnaces
- Exhaust gas sensing systems
- High-temperature lighting fixtures
The ability of high-Tg PCBs to maintain their structural and electrical integrity at elevated temperatures makes them suitable for these demanding applications.
Choosing the Right High-Tg PCB Manufacturer
When selecting a high-Tg PCB manufacturer, several factors should be considered to ensure the best quality and service. Here are some key considerations:
-
Experience and expertise: Look for a manufacturer with extensive experience in producing high-Tg PCBs. They should have a proven track record of successfully delivering high-quality boards for various applications.
-
Technical capabilities: Ensure that the manufacturer has the necessary technical capabilities to produce high-Tg PCBs with the desired specifications. This includes the ability to work with different high Tg materials, offer various Tg options, and meet tight tolerances.
-
Quality control: A reputable high-Tg PCB manufacturer should have robust quality control processes in place. They should adhere to industry standards and perform rigorous testing to ensure the quality and reliability of the PCBs.
-
Customer support: Good customer support is essential when working with a high-Tg PCB manufacturer. They should be responsive to inquiries, provide technical guidance, and offer assistance throughout the design and manufacturing process.
-
Lead times and pricing: Consider the manufacturer’s lead times and pricing structure. They should be able to meet your delivery requirements and offer competitive pricing without compromising on quality.
-
Certifications and compliance: Verify that the manufacturer holds relevant certifications, such as ISO 9001, and complies with industry standards and regulations. This ensures that they follow best practices and meet the necessary quality and environmental requirements.
By carefully evaluating these factors, you can select a high-Tg PCB manufacturer that can deliver high-quality boards that meet your specific application requirements.
Frequently Asked Questions (FAQ)
-
What is the difference between standard PCBs and high-Tg PCBs?
Standard PCBs have a lower glass transition temperature (Tg) compared to high-Tg PCBs. High-Tg PCBs are designed to withstand higher temperatures and maintain their structural integrity and electrical properties even in high-temperature environments. -
What are the common Tg options available for high-Tg PCBs?
High-Tg PCB manufacturers offer a range of Tg options, including standard options like 170°C-180°C, 200°C-210°C, and 240°C-260°C. Some manufacturers also provide custom Tg options to meet specific application requirements. -
What are the advantages of using RF4 material for high-Tg PCBs?
RF4 material offers several advantages for high-Tg PCBs, including high thermal stability, low dielectric loss, low moisture absorption, and high thermal conductivity. These properties make RF4 suitable for high-frequency and high-speed digital applications. -
What industries commonly use high-Tg PCBs?
High-Tg PCBs are commonly used in industries such as automotive, industrial electronics, aerospace and defense, and applications involving high-temperature environments. These industries require PCBs that can withstand extreme temperatures and provide reliable performance. -
How do I choose the right high-Tg PCB manufacturer for my application?
When choosing a high-Tg PCB manufacturer, consider factors such as their experience and expertise, technical capabilities, quality control processes, customer support, lead times, pricing, and certifications. Evaluate these factors to select a manufacturer that can deliver high-quality boards that meet your specific application requirements.
Conclusion
High-Tg PCBs are essential for applications that require reliable performance in high-temperature environments. With their ability to withstand elevated temperatures and maintain structural integrity, high-Tg PCBs offer numerous advantages over standard PCBs.
RF4 is a popular high-Tg PCB material that combines excellent thermal properties with low dielectric loss and high thermal conductivity. RF4 PCBs are suitable for a wide range of high-temperature applications across various industries.
When selecting a high-Tg PCB manufacturer, it is crucial to consider factors such as experience, technical capabilities, quality control, and customer support. By choosing the right manufacturer, you can ensure that you receive high-quality high-Tg PCBs that meet your specific application requirements.
As technology advances and the demand for reliable high-temperature electronics grows, the importance of high-Tg PCBs will only continue to increase. By understanding the properties, manufacturing process, and applications of high-Tg PCBs, designers and engineers can make informed decisions when selecting the appropriate PCB solutions for their projects.
Leave a Reply