Signal Integrity in High-speed PCB Design
Signal integrity is a critical aspect of high-speed PCB design, as it directly impacts the quality and reliability of the transmitted signals. Poor signal integrity can lead to issues such as signal distortion, crosstalk, and reflections, which can compromise the performance of your design. To maintain good signal integrity, consider the following factors:
Impedance Matching
Impedance matching is essential for minimizing signal reflections and ensuring efficient power transfer. When designing high-speed PCBs, it is crucial to match the impedance of the transmission lines to the characteristic impedance of the connected components. Common impedance values for high-speed design include 50Ω for single-ended signals and 100Ω for differential pairs.
To achieve proper impedance matching, consider the following:
- Use Controlled Impedance PCB stackups
- Choose appropriate trace widths and spacing
- Use termination resistors where necessary
Transmission Line Effects
At high frequencies, PCB traces behave like transmission lines rather than simple conductors. This means that the propagation delay, characteristic impedance, and signal reflections become significant factors. To mitigate transmission line effects:
- Keep trace lengths as short as possible
- Use serpentine routing for length matching
- Avoid sharp corners and use smooth bends
- Use appropriate dielectric materials
Via Optimization
Vias are essential for connecting traces across different layers of a PCB, but they can also introduce discontinuities and reflections. To optimize vias for high-speed design:
- Minimize the number of vias
- Use smaller via diameters and anti-pads
- Use via stitching to reduce inductance
- Consider using blind and buried vias
Power Integrity in High-speed PCB Design
Power integrity is another critical aspect of high-speed PCB design, as it ensures that the power supply remains stable and free from noise. Poor power integrity can lead to issues such as voltage drops, ground bounces, and power supply induced jitter. To maintain good power integrity, consider the following factors:
Power Distribution Network (PDN)
A well-designed PDN is essential for maintaining a stable power supply and minimizing noise. When designing the PDN for your high-speed PCB:
- Use appropriate decoupling capacitors
- Place decoupling capacitors close to ICs
- Use multiple power and ground planes
- Minimize the inductance of the PDN
Ground Plane Design
A solid ground plane is crucial for providing a low-impedance return path for high-speed signals and minimizing EMI. When designing the ground plane:
- Use a continuous ground plane where possible
- Avoid splitting the ground plane
- Use stitching vias to connect ground planes across layers
Power Plane Segmentation
In some cases, it may be necessary to segment the power plane to isolate noisy regions or to provide separate power supplies for different parts of the circuit. When segmenting the power plane:
- Use appropriate isolation techniques, such as split planes or moats
- Ensure that each segment has adequate decoupling
- Use ferrite beads or inductors to isolate noisy regions
EMI Reduction in High-speed PCB Design
Electromagnetic interference (EMI) is a common problem in high-speed PCB design, as fast-switching signals can generate high-frequency noise that can interfere with other components or systems. To reduce EMI, consider the following strategies:
Shielding
Shielding is an effective way to contain EMI and prevent it from radiating to other parts of the circuit or external devices. When implementing shielding:
- Use conductive enclosures or shields
- Ensure proper grounding of the shield
- Use shielded cables and connectors where necessary
Filtering
Filtering can help to attenuate high-frequency noise and prevent it from propagating through the circuit. When implementing filtering:
- Use appropriate filter components, such as capacitors, inductors, or ferrite beads
- Place filters close to the noise source
- Use common-mode and differential-mode filtering where appropriate
Layout Techniques
Proper PCB layout is essential for minimizing EMI. When designing your PCB layout:
- Minimize loop areas to reduce magnetic field coupling
- Use ground planes to provide shielding
- Route high-speed signals away from sensitive circuits
- Use differential signaling where possible
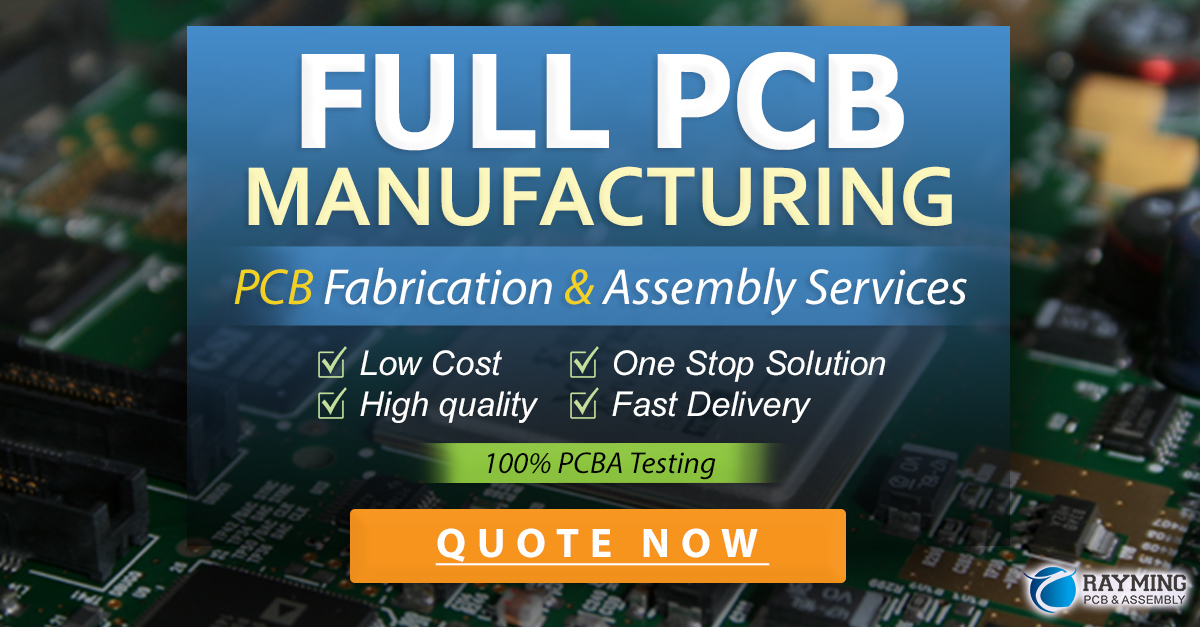
High-speed PCB Design Best Practices
In addition to the specific techniques mentioned above, there are several general best practices that can help you create successful high-speed PCB designs:
Simulation and Modeling
Before finalizing your design, perform simulations and modeling to predict the behavior of your high-speed circuits. This can help you identify potential issues and optimize your design before manufacturing.
Design Rules and Constraints
Establish clear design rules and constraints for your high-speed PCB, including trace widths, spacing, via sizes, and clearances. Use PCB design software that supports high-speed design rules and constraints to ensure consistency and accuracy.
Documentation and Collaboration
Maintain clear documentation of your high-speed PCB design, including schematics, layout files, and design notes. Collaborate with your team members and stakeholders to ensure that everyone is aligned on the design requirements and constraints.
Testing and Validation
After manufacturing your high-speed PCB, perform thorough testing and validation to ensure that it meets your performance requirements. Use appropriate test equipment and techniques, such as time-domain reflectometry (TDR), network analysis, and EMI scanning.
FAQs
Q1: What is the most important factor to consider when designing high-speed PCBs?
A1: Signal integrity is arguably the most important factor in high-speed PCB design, as it directly impacts the quality and reliability of the transmitted signals. However, power integrity and EMI reduction are also critical for ensuring overall system performance.
Q2: How can I ensure proper impedance matching in my high-speed PCB design?
A2: To ensure proper impedance matching, use controlled impedance PCB stackups, choose appropriate trace widths and spacing, and use termination resistors where necessary. PCB design software with high-speed design capabilities can help you calculate and maintain the correct impedance values.
Q3: What is the role of decoupling capacitors in power integrity?
A3: Decoupling capacitors help to maintain a stable power supply by providing a local reserve of charge and minimizing noise. They should be placed close to the ICs they are decoupling and sized appropriately based on the frequency range of the noise they are targeting.
Q4: How can I reduce EMI in my high-speed PCB design?
A4: To reduce EMI, use shielding techniques such as conductive enclosures or shields, implement filtering using capacitors, inductors, or ferrite beads, and adopt proper PCB layout techniques such as minimizing loop areas and using ground planes for shielding.
Q5: What are some common mistakes to avoid in high-speed PCB design?
A5: Some common mistakes to avoid in high-speed PCB design include:
- Neglecting signal integrity and power integrity considerations
- Failing to properly match impedances or terminate transmission lines
- Overlooking the impact of vias and connectors on signal quality
- Inadequate EMI reduction measures
- Not performing simulations or testing to validate the design
By understanding and avoiding these mistakes, you can create more robust and reliable high-speed PCB designs.
Conclusion
High-speed PCB design is a complex and challenging task that requires careful consideration of signal integrity, power integrity, EMI reduction, and best design practices. By understanding and applying the principles and techniques discussed in this article, you can create high-quality, reliable high-speed PCB designs that meet your performance requirements. Remember to perform simulations, establish clear design rules, collaborate with your team, and thoroughly test and validate your design to ensure its success.
Leave a Reply