What is a High-Current PCB?
A high-current PCB is a printed circuit board that is specifically designed to carry high levels of electrical current without compromising the board’s integrity or performance. These PCBs are characterized by their ability to handle currents ranging from several amperes to hundreds of amperes, depending on the application requirements.
High-current PCBs differ from standard PCBs in several aspects, including the choice of materials, trace widths, and the use of specialized components. These boards are built to withstand the heat generated by high currents and to minimize power losses, ensuring optimal system performance and reliability.
Key Features of High-Current PCBs
Thick Copper Traces
One of the most distinguishing features of high-current PCBs is the use of thick copper traces. The thickness of the copper traces directly influences the board’s current-carrying capacity. High-current PCBs typically employ copper traces with thicknesses ranging from 2 oz/ft² to 10 oz/ft² or more, depending on the current requirements. Thicker copper traces help to minimize resistance, reduce voltage drops, and improve heat dissipation.
Wider Trace Widths
In addition to thicker copper traces, high-current PCBs also feature wider trace widths compared to standard PCBs. Wider traces help to distribute the current more evenly across the board, reducing current density and minimizing the risk of overheating. The trace width is determined based on factors such as the expected current level, the temperature rise limit, and the available board space.
Thermal Management
Effective thermal management is crucial in high-current PCB design. As high currents flow through the board, they generate significant amounts of heat. If not properly managed, this heat can lead to component failure, board delamination, and reduced system reliability. High-current PCBs employ various thermal management techniques, such as the use of heatsinks, thermal vias, and high-temperature materials, to dissipate heat efficiently.
Robust Power and Ground Planes
High-current PCBs often incorporate robust power and ground planes to ensure stable and reliable power distribution. These planes are typically made of thick copper layers that span across the entire board. The power and ground planes help to minimize voltage drops, reduce electromagnetic interference (EMI), and provide a low-impedance return path for the current.
Specialized Components
High-current PCBs may require the use of specialized components that are designed to handle high currents and temperatures. These components include high-current connectors, power resistors, and high-current capacitors. The selection of these components is based on their current ratings, thermal characteristics, and overall compatibility with the high-current PCB design.
Design Considerations for High-Current PCBs
Current Capacity Calculation
One of the primary design considerations for high-current PCBs is determining the required current capacity. This involves calculating the maximum current that the board needs to handle based on the application requirements. The current capacity is influenced by factors such as the copper trace thickness, trace width, and the ambient temperature.
To calculate the current capacity, designers use various formulas and tools, such as the IPC-2221 standard, which provides guidelines for determining the appropriate trace widths based on the current requirements and temperature rise limits.
Trace Routing and Spacing
Proper trace routing and spacing are essential in high-current PCB design to ensure optimal current flow and minimize interference. Traces should be routed in a way that minimizes the overall trace length, reduces sharp bends, and avoids crossing over other traces whenever possible. Additionally, sufficient spacing should be maintained between traces to prevent crosstalk and reduce the risk of short circuits.
Thermal Analysis and Management
Thermal analysis is a critical step in high-current PCB design. Designers use specialized software tools to simulate the thermal behavior of the board under various operating conditions. These simulations help to identify potential hot spots, evaluate the effectiveness of thermal management techniques, and optimize the board layout for better heat dissipation.
Thermal management techniques used in high-current PCBs include the use of heatsinks, thermal vias, and high-temperature materials. Heatsinks are attached to components that generate significant heat, such as power transistors, to facilitate heat transfer away from the component. Thermal vias are used to create a low-resistance thermal path between the component and the heatsink or the board’s external layers. High-temperature materials, such as polyimide or ceramic substrates, are used in applications that require operation at elevated temperatures.
Power and Ground Plane Design
The design of power and ground planes is crucial in high-current PCBs to ensure stable and reliable power distribution. The planes should be sized appropriately to handle the expected current levels and to minimize voltage drops. In multi-layer boards, the power and ground planes are often placed on separate layers to reduce impedance and improve signal integrity.
Designers also need to consider the placement of decoupling capacitors near high-current components to minimize voltage fluctuations and reduce noise. Proper via placement and sizing are also important to ensure a low-impedance connection between the planes and the components.
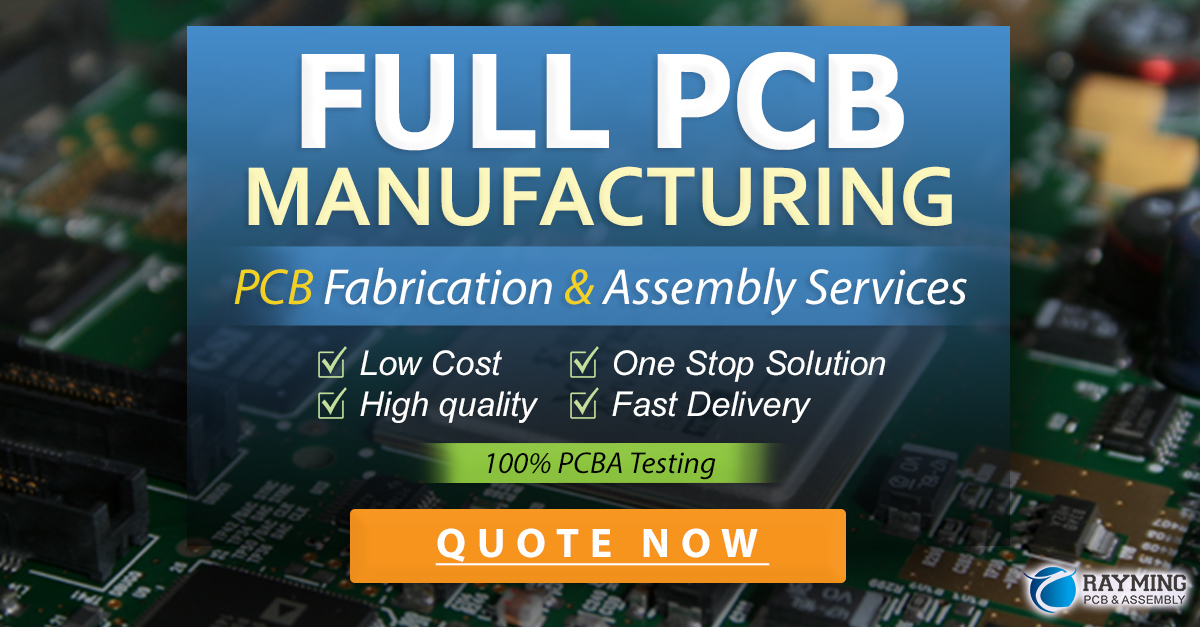
Manufacturing Processes for High-Current PCBs
Material Selection
The choice of materials is critical in the manufacturing of high-current PCBs. The substrate material should have excellent thermal and mechanical properties to withstand the high currents and temperatures. Common substrate materials used in high-current PCBs include FR-4, high-Tg FR-4, polyimide, and ceramic.
The copper foil used for the traces should be of high quality and have the appropriate thickness to meet the current requirements. The use of high-quality copper helps to minimize resistance and improve conductivity.
Copper Plating and Etching
The manufacturing process for high-current PCBs involves copper plating and etching to create the thick copper traces. The board is first plated with a layer of copper, which is then selectively etched away to form the desired trace patterns. The plating process is repeated until the desired copper thickness is achieved.
To ensure accurate and precise etching, high-current PCBs often employ advanced etching techniques, such as pattern plating or differential etching. These techniques help to create well-defined traces with smooth edges and consistent thicknesses.
Multilayer Lamination
High-current PCBs often consist of multiple layers to accommodate the power and ground planes, as well as signal routing. The multilayer lamination process involves stacking and pressing together the individual layers using heat and pressure. The lamination process must be carefully controlled to ensure proper alignment and adhesion between the layers.
Drilling and Via Formation
Drilling and via formation are critical steps in the manufacturing of high-current PCBs. The vias provide electrical connections between the layers and facilitate heat transfer. High-current PCBs often require larger vias to handle the high currents and to improve thermal conductivity.
The drilling process must be precise to ensure accurate via placement and to minimize the risk of defects. Advanced drilling techniques, such as laser drilling or controlled depth drilling, may be employed to create high-quality vias in high-current PCBs.
Quality Control and Testing
Rigorous quality control and testing are essential in the manufacturing of high-current PCBs to ensure their reliability and performance. Visual inspections, electrical testing, and thermal imaging are common quality control methods used to detect defects and verify the board’s functionality.
Electrical testing involves measuring the resistance, continuity, and insulation resistance of the traces and components. Thermal imaging is used to identify hot spots and evaluate the effectiveness of the board’s thermal management techniques.
Applications of High-Current PCBs
High-current PCBs find applications in various industries and systems that require the efficient and reliable transmission of high electrical currents. Some common applications include:
Power Electronics
High-current PCBs are widely used in power electronic systems, such as switch-mode power supplies, motor drives, and inverters. These systems often handle high currents and require robust PCBs that can withstand the associated thermal and mechanical stresses.
Automotive Systems
The automotive industry increasingly relies on high-current PCBs for various applications, such as electric vehicle charging systems, battery management systems, and high-power audio amplifiers. These PCBs must be designed to operate reliably in harsh automotive environments, withstanding vibrations, temperature fluctuations, and exposure to moisture and chemicals.
Industrial Equipment
High-current PCBs are essential in industrial equipment that requires high-power processing, such as welding machines, plasma cutters, and large-scale automation systems. These PCBs must be designed to handle the high currents and temperatures associated with industrial processes while providing reliable and efficient operation.
Telecommunications Infrastructure
The telecommunications industry relies on high-current PCBs for power distribution in base stations, data centers, and other infrastructure equipment. These PCBs must be designed to handle the high currents required by the growing demand for data and the increasing complexity of telecommunications networks.
Frequently Asked Questions (FAQ)
-
What is the difference between a high-current PCB and a standard PCB?
A high-current PCB is designed to handle significantly higher electrical currents compared to a standard PCB. It features thicker copper traces, wider trace widths, and specialized thermal management techniques to ensure reliable operation under high-current conditions. -
How do I determine the appropriate copper thickness for my high-current PCB?
The appropriate copper thickness for a high-current PCB depends on the expected current levels and the temperature rise limits. Designers use guidelines such as the IPC-2221 standard and specialized calculation tools to determine the required copper thickness based on these factors. -
What are some common thermal management techniques used in high-current PCBs?
Common thermal management techniques used in high-current PCBs include the use of heatsinks, thermal vias, and high-temperature materials. Heatsinks are attached to components to facilitate heat transfer, while thermal vias create a low-resistance thermal path between the component and the board’s external layers. High-temperature materials, such as polyimide or ceramic substrates, are used in applications that require operation at elevated temperatures. -
Why is multilayer lamination important in high-current PCB manufacturing?
Multilayer lamination is important in high-current PCB manufacturing because it allows for the incorporation of power and ground planes, as well as signal routing, in a compact and efficient manner. The lamination process ensures proper alignment and adhesion between the layers, which is critical for the board’s structural integrity and electrical performance. -
What kind of testing is performed on high-current PCBs to ensure their reliability?
High-current PCBs undergo rigorous testing to ensure their reliability and performance. Common testing methods include visual inspections, electrical testing, and thermal imaging. Electrical testing involves measuring the resistance, continuity, and insulation resistance of the traces and components, while thermal imaging is used to identify hot spots and evaluate the effectiveness of the board’s thermal management techniques.
Conclusion
High-current PCBs are essential components in various applications that require the efficient and reliable transmission of high electrical currents. These specialized PCBs are designed with thicker copper traces, wider trace widths, and advanced thermal management techniques to ensure optimal performance and reliability under demanding conditions.
The design and manufacturing of high-current PCBs involve careful consideration of factors such as current capacity, trace routing, thermal management, and power distribution. By employing advanced manufacturing processes and rigorous quality control measures, high-current PCBs can be produced to meet the specific requirements of diverse applications, ranging from power electronics and automotive systems to industrial equipment and telecommunications infrastructure.
As technology continues to advance and the demand for high-power systems grows, the importance of high-current PCBs will only continue to increase. By understanding the key features, design considerations, and manufacturing processes involved in creating these specialized boards, engineers and manufacturers can develop innovative solutions that push the boundaries of performance and reliability in high-current applications.
Leave a Reply