Understanding High Current in PCBs
Before diving into the design aspects, it’s important to understand what constitutes “high current” in the context of PCBs. The definition of high current can vary depending on the specific application and the PCB’s size. However, as a general guideline, a PCB is considered to be handling high current when it carries more than 1 amp per trace. In some power electronics applications, the current can go up to hundreds or even thousands of amps.
When a PCB carries high current, several factors come into play:
-
Heat generation: As current flows through the traces, it encounters resistance, leading to power dissipation in the form of heat. The higher the current, the more heat is generated.
-
Voltage drop: The resistance of the traces causes a voltage drop along the length of the trace. This voltage drop can impact the performance of the connected components.
-
Electromagnetic interference (EMI): High current flows can create electromagnetic fields that can interfere with nearby components or circuits.
Key Considerations in High Current PCB Design
To design a PCB that can handle high currents effectively, several key factors must be considered:
Trace Width and Thickness
One of the most critical aspects of high current PCB design is determining the appropriate trace width and thickness. The trace width must be sufficient to carry the required current without excessive heating or voltage drop. The thickness of the copper trace also plays a role in current carrying capacity.
The IPC-2152 standard provides guidelines for determining the minimum trace width based on the current requirements, temperature rise, and copper thickness. Here’s an example table showing the minimum trace widths for different current levels at a 10°C temperature rise:
Current (A) | 1 oz Copper | 2 oz Copper | 3 oz Copper |
---|---|---|---|
1 | 0.0100″ | 0.0079″ | 0.0067″ |
2 | 0.0316″ | 0.0200″ | 0.0158″ |
3 | 0.0548″ | 0.0316″ | 0.0245″ |
4 | 0.0774″ | 0.0424″ | 0.0324″ |
5 | 0.1000″ | 0.0532″ | 0.0400″ |
As a rule of thumb, using thicker copper traces allows for higher current carrying capacity and better heat dissipation.
Layer Stack-up
The layer stack-up of a high current PCB is another crucial consideration. In general, it’s recommended to use thicker copper layers for the power and ground planes to minimize resistance and improve heat dissipation. The use of multiple power and ground layers can also help distribute the current more evenly.
Here’s an example of a typical 4-layer PCB Stack-Up for high current applications:
Layer | Copper Thickness | Purpose |
---|---|---|
Top | 1 oz | Signal |
Inner | 2 oz | Ground plane |
Inner | 2 oz | Power plane |
Bottom | 1 oz | Signal |
Using thicker copper for the inner layers allows for better current handling and heat dissipation.
Thermal Management
Proper thermal management is essential in high current PCB design to prevent overheating and ensure reliable operation. The heat generated by the high current traces must be effectively dissipated to avoid damage to the PCB and its components.
Some thermal management techniques used in high current PCBs include:
-
Using large copper pours: Creating large copper pours connected to the high current traces helps spread the heat over a larger area, improving heat dissipation.
-
Implementing thermal vias: Placing thermal vias near high current components and traces allows heat to be transferred to the other layers of the PCB, enhancing cooling.
-
Using heatsinks: Attaching heatsinks to high power components helps dissipate heat away from the PCB.
-
Providing adequate ventilation: Ensuring proper airflow around the PCB and its components is crucial for effective cooling.
Component Selection
Choosing the right components is critical in high current PCB design. The components must be rated to handle the expected current levels and must be able to dissipate heat effectively.
When selecting components for high current applications, consider the following:
-
Current rating: Ensure that the components can handle the maximum expected current without overheating or failing.
-
Package size: Larger component packages generally have better thermal dissipation capabilities.
-
Thermal resistance: Components with lower thermal resistance can dissipate heat more effectively.
-
Power dissipation: The power dissipation of the component must be considered to ensure it operates within its safe limits.
Applications of High Current PCBs
High current PCBs find applications in various industries where high power densities and currents are required. Some common applications include:
Power Electronics
Power electronics involves the control and conversion of electrical power using electronic devices. High current PCBs are extensively used in power electronic systems such as:
-
Switching mode power supplies (SMPS): These power supplies convert AC to DC or DC to DC using high frequency switching techniques. They require high current PCBs to handle the large currents involved in the power conversion process.
-
Motor drives: PCBs used in motor drive systems need to handle high currents to control and power the motors efficiently.
-
Inverters and converters: High current PCBs are used in inverters and converters that convert DC to AC or AC to DC at high power levels.
Automotive Electronics
The automotive industry extensively uses high current PCBs in various applications, including:
-
Electric vehicle (EV) charging systems: EV charging stations require high current PCBs to handle the large currents needed to charge the vehicle’s battery quickly.
-
Engine control units (ECUs): ECUs manage various aspects of the vehicle’s engine, including fuel injection and ignition. They require high current PCBs to handle the currents involved in controlling the engine’s functions.
-
Power distribution systems: Automotive power distribution systems use high current PCBs to distribute power from the battery to various electrical systems in the vehicle.
Industrial Automation
Industrial automation systems often involve high power machinery and equipment that require high current PCBs for control and power management. Some applications include:
-
Motor control: Industrial motor control systems use high current PCBs to manage the large currents required to drive heavy-duty motors.
-
Power supplies: Industrial power supplies often need to provide high currents to power various equipment and machines. High current PCBs are used to handle these currents efficiently.
-
Robotics: High current PCBs are used in robotic systems to control and power the motors and actuators that enable the robot’s movement and functionality.
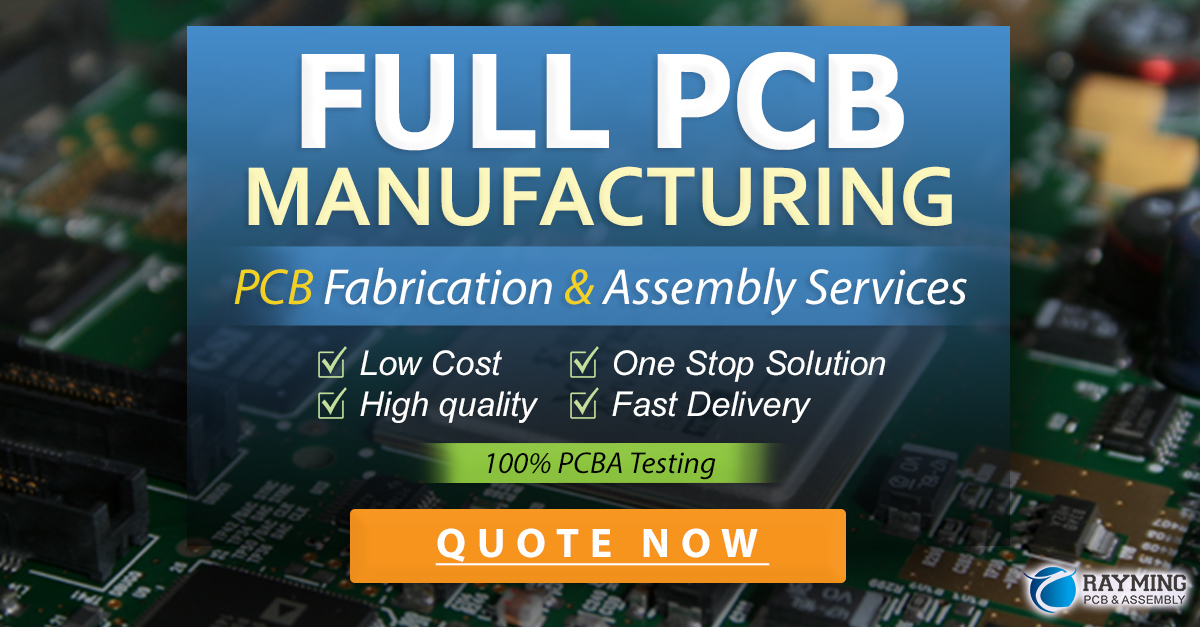
FAQs
-
What is considered high current in PCB design?
In PCB design, high current typically refers to currents exceeding 1 amp per trace. However, the exact definition can vary depending on the specific application and the size of the PCB. -
How can I determine the appropriate trace width for high current PCBs?
The IPC-2152 standard provides guidelines for determining the minimum trace width based on the current requirements, temperature rise, and copper thickness. You can refer to the standard or use online trace width calculators to determine the appropriate trace width for your specific high current application. -
What is the purpose of using thicker copper layers in high current PCBs?
Using thicker copper layers, especially for the power and ground planes, helps minimize resistance and improves heat dissipation. Thicker copper traces can carry higher currents without excessive heating or voltage drop. -
How can I manage the heat generated in high current PCBs?
To manage the heat generated in high current PCBs, you can use techniques such as large copper pours, thermal vias, heatsinks, and adequate ventilation. These methods help dissipate the heat away from the PCB and its components, preventing overheating and ensuring reliable operation. -
What should I consider when selecting components for high current PCBs?
When selecting components for high current PCBs, consider factors such as the current rating, package size, thermal resistance, and power dissipation. Ensure that the components can handle the expected current levels and can dissipate heat effectively to avoid overheating or failure.
Conclusion
High current PCB design is crucial for applications that require handling large amounts of electrical current. Designing PCBs for high current involves careful consideration of trace widths, layer stack-up, thermal management, and component selection. By following best practices and guidelines, such as the IPC-2152 standard, designers can create PCBs that can handle high currents efficiently and reliably.
High current PCBs find applications in various industries, including power electronics, automotive electronics, and industrial automation. As technology advances and the demand for high power systems increases, the importance of high current PCB design will continue to grow.
By understanding the fundamentals of high current PCB design and its applications, engineers and designers can create robust and efficient PCBs that meet the power requirements of modern electronic systems.
Leave a Reply