Introduction to Hand-soldering techniques
Hand-soldering is a crucial skill in the world of electronics manufacturing and repair. It involves the manual application of solder to join electronic components to a printed circuit board (PCB). Two commonly used hand-soldering techniques are point-by-point soldering and mini-wave soldering. In this article, we will explore these techniques in detail, discussing their advantages, disadvantages, and best practices.
Point-by-Point Soldering
What is Point-by-Point Soldering?
Point-by-point soldering, also known as iron soldering or manual soldering, is a technique where the soldering iron is used to apply heat directly to the component lead and the PCB pad. The solder is then fed into the joint, creating a strong electrical and mechanical connection.
Advantages of Point-by-Point Soldering
-
Precision: Point-by-point soldering allows for precise control over the soldering process, making it ideal for soldering small components or working on densely populated PCBs.
-
Versatility: This technique can be used for a wide range of components, including through-hole and surface-mount devices (SMDs).
-
Cost-effective: Point-by-point soldering requires minimal equipment, making it a cost-effective option for small-scale production or repair work.
Disadvantages of Point-by-Point Soldering
-
Time-consuming: Soldering each joint individually can be a slow process, especially for larger PCBs or high-volume production.
-
Operator skill-dependent: The quality of the solder joints heavily relies on the skill and experience of the operator.
-
Inconsistency: Manual soldering can lead to inconsistencies in joint quality, particularly when working with multiple operators or over extended periods.
Best Practices for Point-by-Point Soldering
-
Use the appropriate soldering iron tip size and shape for the component being soldered.
-
Maintain proper tip temperature (typically between 600-700°F or 315-370°C) to ensure optimal heat transfer and prevent damage to components.
-
Apply solder to both the component lead and the PCB pad simultaneously to create a strong joint.
-
Use flux to improve solder flow and prevent oxidation.
-
Inspect solder joints for quality, looking for a concave, shiny appearance and proper wetting of the component lead and PCB pad.
Mini-Wave Soldering
What is Mini-Wave Soldering?
Mini-wave soldering is a semi-automated technique that uses a small wave of molten solder to create joints on a PCB. The PCB is passed over a nozzle that applies the solder wave to the underside of the board, soldering the component leads in one pass.
Advantages of Mini-Wave Soldering
-
Speed: Mini-wave soldering is significantly faster than point-by-point soldering, as multiple joints can be soldered simultaneously.
-
Consistency: The automated nature of mini-wave soldering ensures consistent joint quality across the entire PCB.
-
Reduced operator fatigue: Operators experience less fatigue compared to manual soldering, as the process is semi-automated.
Disadvantages of Mini-Wave Soldering
-
Equipment cost: Mini-wave soldering machines are more expensive than basic Soldering Irons, making them less suitable for small-scale production or hobbyists.
-
Limited flexibility: Mini-wave soldering is less versatile than point-by-point soldering, as it is primarily used for through-hole components and may not be suitable for certain SMDs or densely populated PCBs.
-
Setup time: Configuring the mini-wave soldering machine for a specific PCB design can be time-consuming, particularly when dealing with multiple board designs.
Best Practices for Mini-Wave Soldering
-
Ensure proper PCB design, including appropriate hole sizes and pad dimensions, to accommodate the solder wave.
-
Preheat the PCB to minimize thermal shock and improve solder flow.
-
Adjust the solder wave height, width, and flow rate to optimize joint quality and prevent bridging or insufficient filling.
-
Use appropriate flux to enhance solder wetting and protect the PCB and components from oxidation.
-
Regularly maintain and clean the mini-wave soldering machine to ensure consistent performance and minimize defects.
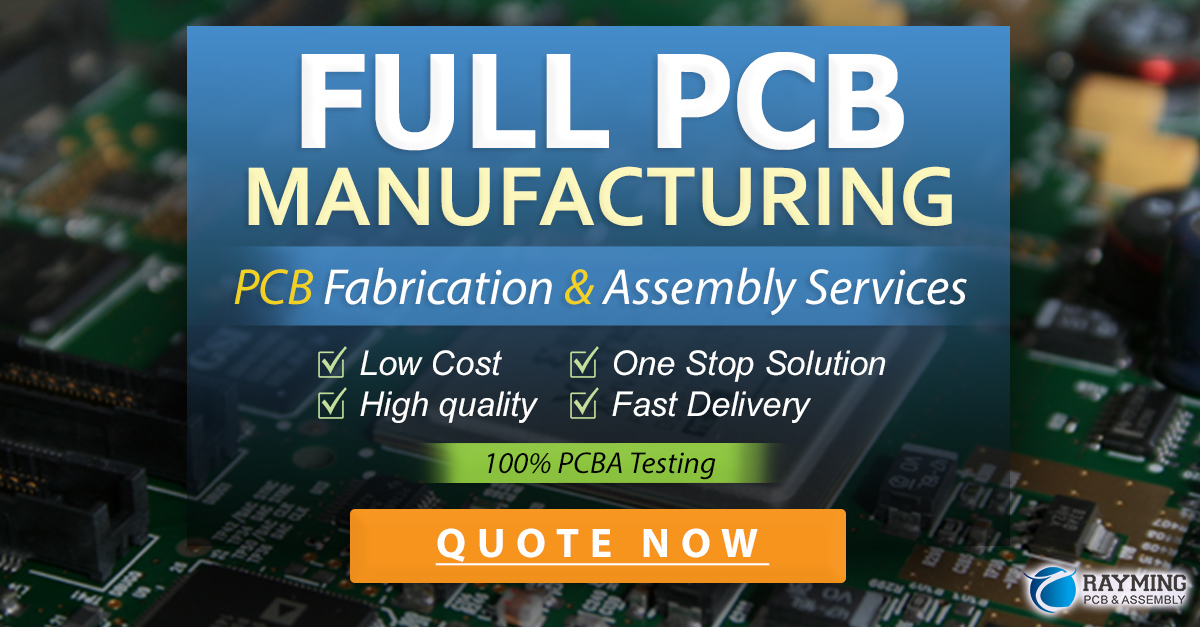
Comparison of Point-by-Point and Mini-Wave Soldering Techniques
Aspect | Point-by-Point Soldering | Mini-Wave Soldering |
---|---|---|
Speed | Slow | Fast |
Precision | High | Moderate |
Versatility | High | Limited |
Consistency | Operator-dependent | High |
Equipment Cost | Low | High |
Operator Fatigue | High | Low |
Setup Time | Minimal | Considerable |
Frequently Asked Questions (FAQ)
- Q: What is the main difference between point-by-point soldering and mini-wave soldering?
A: The main difference lies in the method of solder application. Point-by-point soldering involves manually applying solder to each joint using a soldering iron, while mini-wave soldering uses a small wave of molten solder to create joints on multiple components simultaneously.
- Q: Which technique is better for small-scale production or hobbyists?
A: Point-by-point soldering is generally better suited for small-scale production or hobbyists due to its low equipment cost and high versatility. Mini-wave soldering machines are more expensive and may not be justifiable for low-volume work.
- Q: Can surface-mount devices (SMDs) be soldered using mini-wave soldering?
A: While mini-wave soldering is primarily used for through-hole components, some SMDs can be soldered using this technique. However, the PCB design must accommodate the solder wave, and the process may not be suitable for all SMD types or densely populated boards.
- Q: How can I ensure consistent joint quality when using point-by-point soldering?
A: To ensure consistent joint quality, use the appropriate soldering iron tip size and shape, maintain proper tip temperature, apply solder to both the component lead and PCB pad simultaneously, use flux, and regularly inspect solder joints for quality.
- Q: What maintenance is required for mini-wave soldering machines?
A: Regular maintenance of mini-wave soldering machines includes cleaning the solder pot, nozzle, and wave-forming plates, as well as monitoring and adjusting the solder level, temperature, and flow rate. Proper maintenance ensures consistent performance and minimizes defects.
Conclusion
Both point-by-point soldering and mini-wave soldering have their merits and drawbacks, and the choice between the two depends on factors such as production scale, component types, and available resources. Point-by-point soldering offers high precision and versatility, making it ideal for small-scale work and diverse component types, while mini-wave soldering excels in speed and consistency, making it suitable for larger-scale production of through-hole components.
By understanding the advantages, disadvantages, and best practices associated with each technique, manufacturers and hobbyists can make informed decisions and achieve optimal results in their soldering processes. Regardless of the chosen method, proper training, attention to detail, and adherence to best practices are essential for creating reliable, high-quality solder joints.
Leave a Reply