What is FR4-TG?
FR4-TG is a high-performance variant of the standard FR-4 (Flame Retardant 4) printed circuit board (PCB) material. It is a glass-reinforced epoxy laminate that offers enhanced thermal stability and improved mechanical properties compared to conventional FR-4. The “TG” in FR4-TG stands for “Tg,” which refers to the glass transition temperature of the material.
Key Features of FR4-TG
- Higher glass transition temperature (Tg)
- Improved thermal stability
- Enhanced mechanical strength
- Better dimensional stability
- Suitable for high-temperature applications
Advantages of Using FR4-TG in PCB Manufacturing
1. Increased Thermal Stability
One of the primary advantages of using FR4-TG in PCB manufacturing is its increased thermal stability. The higher glass transition temperature (Tg) of FR4-TG allows it to maintain its mechanical and electrical properties at elevated temperatures. This makes it an ideal choice for applications that require exposure to high temperatures, such as automotive, aerospace, and industrial electronics.
The table below compares the glass transition temperatures of standard FR-4 and FR4-TG:
Material | Glass Transition Temperature (Tg) |
---|---|
FR-4 | 130°C – 140°C |
FR4-TG | 170°C – 180°C |
2. Improved Mechanical Strength
FR4-TG exhibits improved mechanical strength compared to standard FR-4. The enhanced mechanical properties of FR4-TG make it more resistant to warping, twisting, and bending, which is particularly important for applications that require high reliability and durability. The increased mechanical strength also allows for the manufacturing of thinner PCBs without compromising their structural integrity.
3. Better Dimensional Stability
Another benefit of using FR4-TG is its better dimensional stability. The material’s higher glass transition temperature and improved mechanical properties contribute to its ability to maintain its dimensions under varying environmental conditions. This is crucial for applications that require precise component placement and high-density interconnects, as it minimizes the risk of signal integrity issues caused by dimensional changes in the PCB.
4. Compatibility with High-Temperature Assembly Processes
FR4-TG’s increased thermal stability makes it compatible with high-temperature assembly processes, such as lead-free soldering and reflow soldering. The material’s ability to withstand higher temperatures without degradation ensures that the PCB remains stable during the assembly process, reducing the likelihood of defects and improving the overall reliability of the final product.
Applications of FR4-TG PCBs
FR4-TG PCBs find applications in various industries where high-temperature performance and reliability are critical. Some of the common applications include:
- Automotive electronics
- Engine control units (ECUs)
- Transmission control modules
- Brake control systems
-
Infotainment systems
-
Aerospace and defense
- Avionics systems
- Radar and communication equipment
-
Satellite components
-
Industrial automation
- Motor drives and controllers
- Power inverters
-
Sensors and actuators
-
Medical devices
- Diagnostic equipment
- Surgical instruments
-
Implantable devices
-
Telecommunications
- Base stations
- Routers and switches
- Optical network equipment
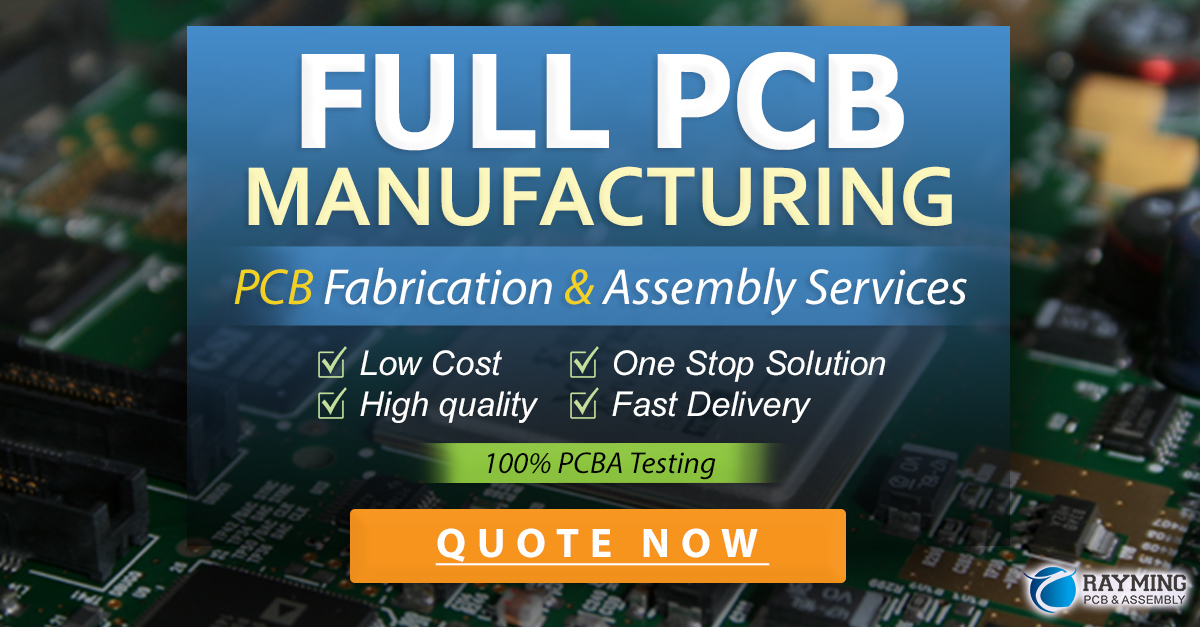
Manufacturing Process of FR4-TG PCBs
The manufacturing process of FR4-TG PCBs is similar to that of standard FR-4 PCBs, with a few key differences:
-
Material selection: FR4-TG laminates are chosen instead of standard FR-4 laminates to achieve the desired thermal and mechanical properties.
-
Lamination: The glass fabric is impregnated with the epoxy resin and cured under high pressure and temperature to form the FR4-TG laminate.
-
Drilling: Holes are drilled into the laminate to accommodate through-hole components and vias.
-
Copper plating: The drilled holes are plated with copper to create electrical connections between layers.
-
Patterning: The desired circuit pattern is transferred onto the copper-clad laminate using photolithography and etching processes.
-
Solder mask application: A solder mask is applied to protect the copper traces and prevent short circuits.
-
Surface finish: A surface finish, such as HASL (Hot Air Solder Leveling) or ENIG (Electroless Nickel Immersion Gold), is applied to protect the exposed copper and enhance solderability.
-
Electrical testing: The finished PCB undergoes electrical testing to ensure that it meets the required specifications and performance criteria.
Challenges and Considerations in Using FR4-TG PCBs
Despite the numerous advantages of using FR4-TG PCBs, there are some challenges and considerations to keep in mind:
-
Cost: FR4-TG laminates are more expensive than standard FR-4 laminates due to their enhanced properties and specialized manufacturing process. This can increase the overall cost of the PCB.
-
Availability: FR4-TG laminates may not be as widely available as standard FR-4 laminates, which can lead to longer lead times and potential supply chain issues.
-
Design considerations: When designing PCBs using FR4-TG, it is essential to consider the material’s unique properties and how they may affect the design rules, such as minimum trace widths and spacings, via sizes, and thermal management strategies.
-
Compatibility with other materials: In some cases, FR4-TG may not be compatible with certain adhesives, coatings, or encapsulants used in the assembly process. It is crucial to ensure that all materials used are compatible with FR4-TG to avoid potential reliability issues.
Future Trends and Developments in FR4-TG PCBs
As the demand for high-performance electronics continues to grow, the development of advanced PCB materials like FR4-TG is expected to accelerate. Some of the future trends and developments in FR4-TG PCBs include:
-
Higher glass transition temperatures: Researchers are working on developing FR4-TG variants with even higher glass transition temperatures to cater to the growing needs of high-temperature applications.
-
Improved thermal conductivity: Efforts are being made to enhance the thermal conductivity of FR4-TG laminates to facilitate better heat dissipation in high-power electronics.
-
Integration with other advanced materials: Combining FR4-TG with other advanced materials, such as carbon nanotubes or graphene, could lead to the development of hybrid PCB substrates with exceptional thermal, mechanical, and electrical properties.
-
Increased adoption in emerging applications: As new technologies, such as electric vehicles, 5G networks, and IoT devices, continue to evolve, the adoption of FR4-TG PCBs in these applications is expected to grow, driving further innovation in the field.
Frequently Asked Questions (FAQ)
- What is the difference between FR-4 and FR4-TG?
-
FR-4 is a standard glass-reinforced epoxy laminate used in PCBs, while FR4-TG is a high-performance variant that offers higher glass transition temperature, improved thermal stability, and enhanced mechanical properties.
-
Can FR4-TG be used for Multilayer PCBs?
-
Yes, FR4-TG can be used for manufacturing Multilayer PCBs, offering the same benefits of increased thermal stability and mechanical strength as in single-layer boards.
-
Is FR4-TG suitable for lead-free soldering processes?
-
Yes, FR4-TG’s increased thermal stability makes it compatible with lead-free soldering processes, which typically require higher temperatures compared to traditional lead-based soldering.
-
How does the cost of FR4-TG compare to standard FR-4?
-
FR4-TG laminates are generally more expensive than standard FR-4 laminates due to their enhanced properties and specialized manufacturing process. However, the added cost may be justified for applications that require high-temperature performance and reliability.
-
Can FR4-TG be used in medical devices?
- Yes, FR4-TG PCBs are suitable for use in medical devices, particularly in applications that require high reliability and stability under demanding environmental conditions, such as diagnostic equipment, surgical instruments, and implantable devices.
Conclusion
FR4-TG is a high-performance PCB material that offers numerous advantages over standard FR-4, including increased thermal stability, improved mechanical strength, better dimensional stability, and compatibility with high-temperature assembly processes. These properties make FR4-TG an ideal choice for applications in industries such as automotive, aerospace, industrial automation, medical devices, and telecommunications.
While there are challenges and considerations to keep in mind when using FR4-TG, such as cost and design requirements, the benefits of this material often outweigh the drawbacks in critical applications. As technology continues to advance, the development and adoption of FR4-TG PCBs are expected to grow, driving innovation in the electronics industry and enabling the creation of more reliable, high-performance devices.
Leave a Reply