Introduction
Flexible printed circuit boards (flex PCBs or flex circuits) are an important enabling technology in modern electronics. As devices continue getting smaller and more portable, flex PCBs allow circuitry to bend and flex to fit into tight spaces.
The substrate, or base material, is a key part of any flex PCB. The substrate provides the foundation for mounting components and routing circuit traces. Properties like flexibility, thermal performance, and dielectric constant are largely determined by the substrate material.
This guide provides an overview of common flex PCB substrate materials, their properties, and typical applications. We’ll look at popular options like polyimide, polyester, PEN, PET, and composites. Understanding substrate properties helps designers select the optimal material for each use case.
Flexible PCB Substrate Materials
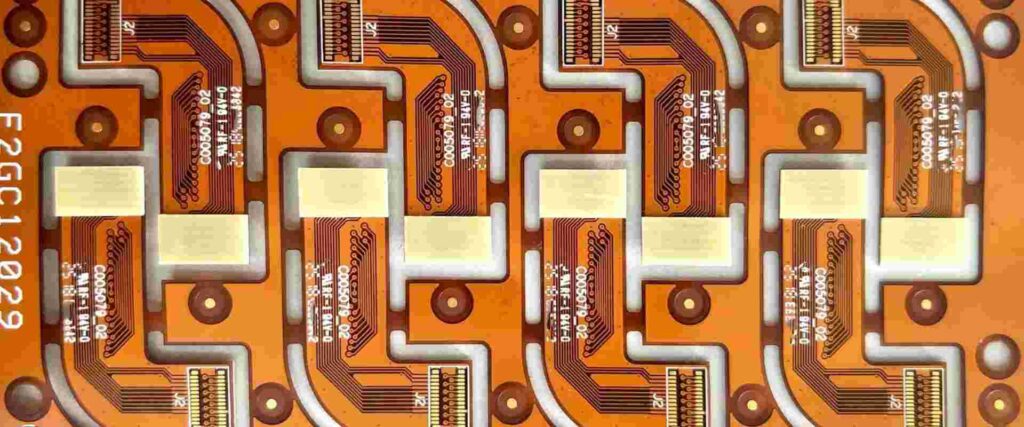
There are two main categories of substrates used in flex PCBs: plastic films and composite materials. Here are some of the most common.
Polyimide
Polyimide (PI) films like Kapton® are the most widely used flexible PCB substrate. PI offers an excellent balance of flexibility, heat resistance, and electrical performance.
Key properties:
- High flexibility and foldability
- Withstands temperatures up to 400°C
- Low dielectric constant (~3.4)
- Good chemical resistance
Common applications:
- Consumer electronics
- Automotive electronics
- Medical devices
- Aerospace and defense
Polyester
Polyester (PET or PETE) films provide good flexibility and dielectric performance at a lower cost than polyimide. However, maximum operating temperature is limited to around 150°C.
Key properties:
- Low cost
- Moderate flexibility
- Maximum temperature ~150°C
- Dielectric constant ~3.0
Common applications:
- Low-end consumer electronics
- Appliances
- RFID antennas
PEN
Polyethylene naphthalate (PEN) is a high-temperature polyester film with better dimensional stability than PET. It has excellent flex life and operates up to 200°C.
Key properties:
- High dimensional stability
- Withstands temperatures up to 200°C
- Low humidity absorption
- Dielectric constant ~3.2
Common applications:
- Automotive electronics
- LED lighting
- Medical devices
PET
Polyethylene terephthalate (PET) is the most widely used polyester film. It’s low cost but has limited heat resistance (~120°C).
Key properties:
- Low cost
- Moderate flexibility
- Maximum temperature ~120°C
- Dielectric constant ~3.3
Common applications:
- Low-end consumer products
- Static control applications
LCP
Liquid crystal polymer (LCP) films provide the highest heat resistance among flex substrates, withstanding temperatures exceeding 300°C. However, LCP is more rigid than other films.
Key properties:
- Extremely high heat resistance (>300°C)
- Low moisture absorption
- Relatively rigid/less flexible
- Dielectric constant ~3.0
Common applications:
- Aerospace and defense
- Automotive electronics near engines
- High temperature sensors
Composites
Composite materials like polyimide/glass blends provide enhanced dimensional stability and tear resistance compared to plastic films.
Key properties:
- Improved tear strength
- Enhanced rigidity and stability
- Higher dielectric constant (~4.5+)
Common applications:
- Highly dynamic flexing applications
- Flex-to-install PCBs
- Production flex boards
Selecting the Right Flexible PCB Substrate
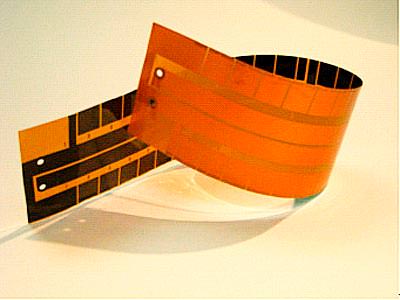
Choosing the right substrate material depends on factors like application environment, performance requirements, and product lifetime.
Here are some key considerations when selecting a flex PCB substrate:
- Temperature range – How much heat will the flex circuit experience during operation and storage? This affects material choice.
- Flexibility requirements – Is the circuit design low profile or does it need to handle tight dynamic bending? More flexible films can enable compact form factors.
- Dielectric requirements – High frequency or impedance controlled circuits may require substrates with specific dielectric constants.
- Cost – Polyester and PET films tend to be cheaper than polyimide, which is important for high volume consumer products.
- Lifetime – How long does the product need to perform reliably? Higher performance films generally provide better longevity.
Understanding substrate properties enables picking the right material for each unique application. Consulting with your flex PCB manufacturer early in the design process is recommended.
Flex PCB Substrate Property Comparison
Here is a comparison of typical properties for common flexible PCB substrate materials:
Property | Polyimide | Polyester | PEN | PET | LCP |
---|---|---|---|---|---|
Dielectric Constant | 3.4 | 3.0 | 3.2 | 3.3 | 3.0 |
Dissipation Factor | 0.002 | 0.02 | 0.003 | 0.02 | 0.0023 |
Dielectric Strength (V/mil) | 5300 | 4000 | 5800 | 5500 | >5000 |
Young’s Modulus (kpsi) | 360 | 550 | 690 | 450 | 2,700 |
Moisture Absorption (%) | 1.7 | 0.15 | 0.04 | 0.77 | 0.04 |
Maximum Temperature (°C) | 400 | 150 | 200 | 120 | >300 |
Thermal Expansion (ppm/°C) | 20 | 20 | 20 | 18 | 17 |
This comparison shows how properties like temperature resistance, flexibility, and dielectric performance vary across substrate materials. These differences make each material suitable for certain applications.
Tips for Designing Flex Circuits with Different Substrates
Here are some tips to consider when designing flex PCBs with different substrate materials:
- Polyimide – Best for tight dynamic flexing thanks to excellent flexibility. Withstands high temperatures.
- Polyester – Most economical option. Avoid sharp bending or folding.
- PEN – Provides enhanced thermal performance over PET. Useful for automotive applications.
- PET – Only suitable for low temperature environments like consumer electronics.
- LCP – Ideal for circuits near engines or other high heat sources. Expect less flexibility.
- Composites – Provides stability for flex-to-install designs. Expect higher dielectric constant.
In general, consult manufacturer guidelines and test performance over the full range of bending and temperature conditions.
Applications and Examples
Flex PCB substrates serve a wide variety of end use applications. Here are a few examples:
- Wearable devices – Polyimide flex circuits allow wearable products to bend and conform to the body.
- Automotive – Polyimide and PEN substrates withstand under-hood temperatures for engine control and monitoring.
- Consumer electronics – Low cost PET and polyester films are commonly used in phones, laptops, cameras, etc.
- Medical – Thin, flexible polyimide substrates enable compact implantables and body-worn devices.
- Aerospace – Reliable high-temperature LCP and polyimide substrates meet avionics needs.
The range of properties across substrate materials makes flex PCBs viable options for many demanding environments.
Frequently Asked Questions
What is the most flexible PCB substrate material?
Polyimide films generally provide the best flexibility and dynamic bending properties among common flex PCB substrates. Polyimide can withstand millions of flex cycles.
How do I know if I need a flexible PCB?
Flexible PCBs are required when the circuit needs to bend and flex during use. They are ideal for portable electronics, wearables, and space-constrained designs. Rigid PCBs are unable to flex repeatedly without failure.
What are the main advantages of flexible PCBs?
Compared to rigid boards, advantages include:
- Extremely thin, lightweight, and customizable shapes
- Can conform to 3D surfaces and move dynamically
- Improved durability with flexing stress
- Enables more compact, ergonomic product designs
Are flexible PCBs more expensive than rigid PCBs?
Flex PCBs typically have higher material costs than rigid FR-4 boards. But they can reduce total product costs through space and weight savings. Cost depends on volume, materials, and complexity.
How do I decide between single, double, or multilayer flex PCBs?
- Single layer: lowest cost, simple wiring
- Double layer: allows more complex wiring while remaining thin
- Multilayer: enables high density, complex circuits but increases thickness and cost
The layer count should be based on intricacy of routing, thickness limits, and budget.
How are flex PCBs manufactured?
There are two main approaches:
- Subtractive – A copper clad laminate is selectively etched to form traces and features.
- Additive – Traces are built up on the substrate with an electroplating process.
Photolithographic processes transfer the intricate circuit patterns. Flexible boards may also be laser direct structuring (LDS) compatible.
Leave a Reply