Introduction
Flexible printed circuit boards (PCBs) are essential components in modern electronic devices where flexibility, space savings, and weight reduction are required. As flexible PCBs become more popular, the choice of flexible substrate materials is also expanding to meet various application requirements. This article provides a detailed overview of the most common flexible PCB materials, their properties, advantages and limitations to help designers select the optimal flexible substrate.
Polyimide (Kapton)
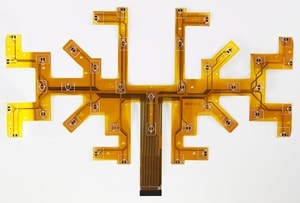
Polyimide, commonly known by DuPont’s brand name Kapton, is the most widely used flexible PCB material today. The key properties of polyimide include:
- Exceptional thermal stability and heat resistance – With a glass transition temperature over 300°C, polyimide can withstand soldering processes and high operating temperatures. This makes it suitable for various high-temperature applications.
- Excellent chemical resistance – Polyimide offers good resistance to most solvents and acids, except alkaline solutions. This allows polyimide PCBs to be widely used in harsh environments.
- Good dielectric properties – Polyimide has a dielectric strength of 15kV/mm along with good insulation resistance. This enables polyimide PCBs to operate at high voltages if required.
- High mechanical strength – Polyimide substrates have very high tensile strength and are not brittle. This imparts good flex life and makes polyimide suitable for dynamic flexing applications.
- Relatively high cost – Polyimide is more expensive than other flexible PCB materials like PET and PEN. This limits its use in high-volume cost-sensitive applications.
Polyimide is an excellent general-purpose flexible PCB substrate due to its overall balance of electrical, thermal, chemical and mechanical properties. It is commonly used in consumer electronics, automotive, aerospace, medical and industrial applications.
Polyester (PET)
Polyethylene terephthalate (PET) is another widely adopted flexible substrate material. The major advantages of PET include:
- Low cost – PET is the one of the least expensive flexible substrate materials. This makes it suitable for high-volume consumer electronics applications.
- Good chemical resistance – Similar to polyimide, PET offers resistance to most chemicals except alkaline solutions.
- Clear transparency – PET films are optically clear, which is useful for some display and lighting applications.
- Recyclability – PET is highly recyclable, which provides environmental benefits.
However, PET also has some disadvantages:
- Low maximum operating temperature – With a glass transition temperature around 80°C, PET flexible PCBs cannot withstand soldering processes or high operating temperatures.
- Higher water absorption – PET absorbs more moisture compared to polyimide, which can affect electrical properties.
- Lower mechanical strength – PET has lower tensile strength than polyimide, so it cannot endure as much repeated flexing.
PET’s ultra-low-cost and transparency make it suitable for high-volume consumer electronics like wearables, while its temperature and flex life limits usage in more demanding applications.
Polyethylene Naphthalate (PEN)
Polyethylene naphthalate (PEN) is a higher-performance version of PET, offering:
- Higher temperature rating – With a glass transition temperature around 155°C, PEN can withstand reflow soldering processes.
- Lower moisture absorption – PEN absorbs only half as much water as PET, resulting in better electrical performance in damp conditions.
- Higher mechanical strength – PEN has over 50% higher tensile strength versus PET, enabling improved flex life.
- Higher cost – PEN is more expensive than PET but lower cost than polyimide substrates.
The balanced cost and improved thermal/mechanical properties make PEN a popular choice for automotive, industrial and other mid-range flexible circuit applications.
Polyamide (Kapton HN, Upilex)
Polyamide-imide films like Kapton HN and Upilex offer further improved thermal performance versus polyimide:
- Very high temperature rating – With glass transition temperatures over 400°C, polyamide films enable flex PCB usage in extremely high-temperature environments like aerospace systems.
- Better dielectric properties – Polyamide has lower dielectric constant and loss factor than polyimide, resulting in superior high frequency electrical performance.
- Higher cost – Polyamide flexible substrates have a higher cost than polyimide and other standard flexible materials.
The exceptional thermal and electrical characteristics make polyamide the material of choice for the most demanding flexible PCB applications in aerospace, defense and communication systems.
Liquid Crystal Polymer (LCP)
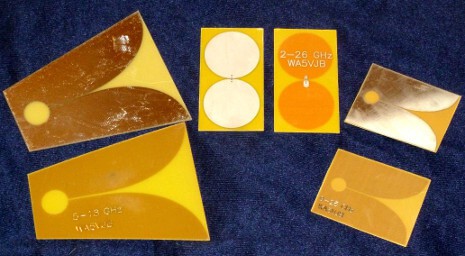
Liquid crystal polymer (LCP) is an advanced flexible substrate designed for next-generation applications:
- Excellent high frequency performance – LCP has the lowest dielectric constant (Dk=2.9) and loss factor of any standard flex material, enabling flex PCB operation up to mmWave frequencies.
- Improved chemical resistance – LCP provides the best chemical resistance, allowing use in almost any harsh environment.
- Lead-free soldering compatible – LCP has very high temperature resistance, enabling lead-free soldering processes.
- Most expensive option – As a newer, more advanced material, LCP flexible substrates have the highest cost.
LCP’s superior electrical and chemical properties make it the premier choice for cutting-edge applications like 5G devices, aerospace systems, and harsh environment electronics.
Comparison of Flexible PCB Materials
Material | Dielectric Constant | Loss Tangent | Glass Transition Temperature | Water Absorption | Typical Cost |
---|---|---|---|---|---|
Polyimide | 3.4 | 0.002 | >300°C | 1.7% | $$$ |
PET | 3.0 | 0.02 | About 80°C | 0.4% | $ |
PEN | 3.0 | 0.02 | About 155°C | 0.2% | $$ |
Polyamide | 3.2 | 0.002 | >400°C | 0.5% | $$$$ |
LCP | 2.9 | 0.0013 | >300°C | 0.04% | $$$$ |
This comparison summarizes the key electrical, thermal, and cost properties of the major flexible PCB substrate materials. Polyimide provides the best overall balance at a moderate cost point for most applications. PET/PEN are suitable for high-volume consumer uses, while polyamide and LCP meet the most demanding electrical and thermal requirements despite higher costs.
Flexible PCB Constructions
In additional to the base substrate material, the construction of the flexible PCB itself is also an important consideration for the intended application. Here are some common flex PCB constructions:
- Single-layer – A simple single conductive copper layer on the flexible substrate. Low cost but lacks ability to create complex circuits.
- Double-sided – Copper layers on both sides of the substrate allow more complex wiring but increases thickness.
- Multilayer – Flexible substrates bonded together in a press with adhesive. Allows the most complex circuit designs by enabling inner copper layers.
- Rigid-flex – Combines rigid FR-4 PCB sections with flexible polyimide/LCP areas on the same PCB. Provides flexibility where needed while maintaining rigidity for components.
- Metal-backed – A thin layer of metal like aluminum or copper-Invar-copper is laminated to the backside of the flexible substrate. This provides enhanced thermal performance.
Flexible PCB Design and Manufacturing
Designing and manufacturing flexible PCBs requires special considerations:
- Dynamic flexing endurance must be evaluated to ensure sufficient flex life for the application based on the flex material and PCB construction.
- Trace widths and spaces are typically larger than traditional PCBs to accommodate flexing without copper cracking.
- Special CAD tools are needed to design rigid-flex PCBs.
- Flex-to-through-hole connections require stepped pad shapes to avoid flex crack propagation.
- Careful process controls are required during lamination to avoid damaging flexible substrates.
By partnering with an experienced flex PCB manufacturer during design, these unique considerations can be addressed to produce a reliable flexible circuit board.
Applications of Flexible PCBs
The versatility of flexible PCBs allows them to be used across a wide range of applications:
- Consumer electronics – Wearables, phones, tablets, laptops. Low-cost PET/PEN substrates.
- Automotive – Instrument panels, engine control units, LED lighting. Polyimide and PEN substrates.
- Industrial – Robotics, machine controls. Polyimide or polyamide boards.
- Medical – Implants, monitors. Biocompatible substrates.
- Defense/Aerospace – Avionics, radars, sensors. Polyimide or high-temp polyamide substrates.
As electronic devices continue getting smaller and more portable, flexible PCB usage will expand into additional applications that require compact, lightweight and dynamic solutions.
Choosing the Right Flexible PCB Material
When selecting a flexible PCB material, here are some key considerations:
- Temperature – The substrate must withstand all soldering and maximum operating temperatures.
- Flexibility – Evaluate required dynamic flexing performance.
- High Frequency – If high frequency operation is needed, consider LCP or polyamide substrates.
- Chemical Exposure – Applications with chemical exposure require maximum chemical resistance.
- Cost – Weigh cost objectives versus performance requirements.
By carefully balancing these factors, designers can match the optimal flexible PCB substrate material to the application needs.
Conclusion
Flexible PCBs enable electronics to be integrated into tight spaces, move dynamically, or conform around other components. As flexible PCB usage grows, the material options continue expanding to suit the needs of next-generation devices. Polyimide delivers proven performance at moderate cost for most mainstream applications. LCP and polyamide substrates push the boundaries of electrical and thermal properties for advanced uses. With their versatility, flexible PCBs will be core components enabling further miniaturization and innovation across the electronics industry.
Frequently Asked Questions
Q: What are some key considerations when selecting a flexible PCB material?
A: The most important considerations are:
- Temperature rating to withstand soldering and max operating temps
- Flexibility requirements and dynamic flexing endurance
- High frequency electrical performance needs
- Chemical resistance for environmental exposure
- Cost and budget objectives
By balancing these factors, the optimal flexible substrate can be selected.
Q: Can standard FR-4 PCB laminates be used for flexible PCBs?
A: No, FR-4 laminates are fiberglass-reinforced and too rigid to be flexed repeatedly. They would crack and fail quickly under dynamic bending stresses. Only engineered flexible polymer films like polyimide and LCP are suitable for flex PCB applications.
Q: How are components mounted onto flexible PCBs?
A: There are two main approaches:
- SMT components mounted with solder paste and reflow like traditional PCBs
- Conductive adhesive bonding for improved flexibility and reduced solder joint stresses
The assembly process depends on the substrate material’s thermal rating and application flexibility requirements.
Q: How do flexible PCBs connect to rigid PCBs?
A: Rigid-flex PCBs use specialized zones with polyimide substrates to bridge between rigid sections. Flex connectors like ZIF connectors can also solder flex PCB tails onto rigid boards. Careful structuring is needed to avoid flexing stresses at joints.
Q: How small can flex PCB conductors and spaces be fabricated?
A: The state-of-the-art is trace/space of 25 microns (0.001″) and getting smaller. However, typical design rules are larger – around 100 microns minimum – to ensure reliability under dynamic flexing.
Leave a Reply