Introduction to Flexible Aluminum PCBs
Printed circuit boards (PCBs) are the backbone of modern electronics. Traditional PCBs use rigid insulating substrates like FR-4 fiberglass to provide mechanical support for copper traces. However, emerging flexible circuit board technologies are enabling smaller, lighter, and more robust electronic devices.
One such innovation is flexible aluminum PCBs. As the name suggests, these circuit boards use thin aluminum foil instead of FR-4 as the substrate. The copper traces are chemically bonded to the aluminum surface using a process called direct bond copper (DBC). The result is a flexible PCB that is extremely lightweight, highly conductive, and can withstand extreme temperatures.
In this comprehensive guide, we will explore the benefits, manufacturing processes, and applications of flexible aluminum PCBs.
Benefits of Flexible Aluminum PCBs
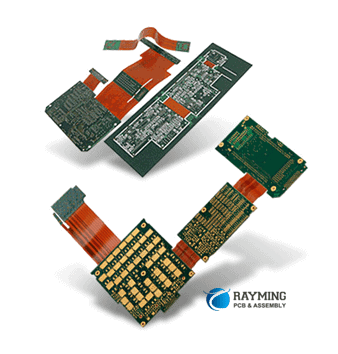
Flexible aluminum PCBs offer several advantages over traditional rigid PCBs:
Lightweight
Aluminum has a density of 2.7 g/cm3 compared to FR-4’s 1.8 g/cm3. By switching to an aluminum substrate, flex PCB weight can be cut almost in half. This enables smaller and lighter end products.
Thermal Conductivity
Aluminum has excellent thermal conductivity of 237 W/mK, nearly 700 times higher than FR-4’s 0.3 W/mK. This allows flexible aluminum PCBs to dissipate heat efficiently from power electronics.
High Temperature Resistance
Aluminum PCBs can operate continuously at temperatures exceeding 200°C without warping or deterioration issues. Rigid FR-4 PCBs can only handle up to 130°C.
Flexibility
With a thin aluminum foil core of around 50-100 μm, flexible PCBs can bend and flex to fit the smallest spaces. Rigid PCBs are prone to cracking under bending stresses.
Chemical Resistance
The aluminum substrate offers excellent chemical resistance, allowing its use in harsh environments. Acids, alkalis, and oils do not affect aluminum.
Cost Savings
Flexible aluminum PCBs leverage established aluminum processing techniques used in the packaging industry, resulting in lower costs than niche ceramic solutions.
Reliability
Aluminum oxide forms a thin passivation layer on the aluminum surface that protects against corrosion. This makes aluminum PCBs highly reliable over thousands of bend cycles.
Manufacturing Process
Flexible aluminum PCB manufacturing involves laminating sheets of aluminum foil with specially treated copper foil. The process steps are outlined below:
Surface Preparation
The aluminum foil is degreased and etched to remove any oxide coating and impurities. This activates the surface for subsequent bonding.
Direct Bond Copper (DBC)
A thin sheet of copper foil is placed over the aluminum. The copper is coated with a proprietary interface layer. The aluminum-copper stack is heated under pressure to around 1065°F. The interfacial layer melts forming a eutectic alloy with aluminum. This alloy solidifies on cooling to form a homogenized bond between aluminum and copper layers.
Photolithography
A photoresist coating is applied on the copper layer. The PCB layout is then transferred to the surface using UV exposure through a mask. After developing, the unexposed copper is etched away chemically leaving behind the desired circuit pattern.
Final Processing
The flex PCB panels go through various plating, cleaning, and testing steps. Mechanical slits are made on the edges to increase flexibility. Finally, the PCBs are sheared into individual boards.
Applications of Flexible Aluminum PCBs
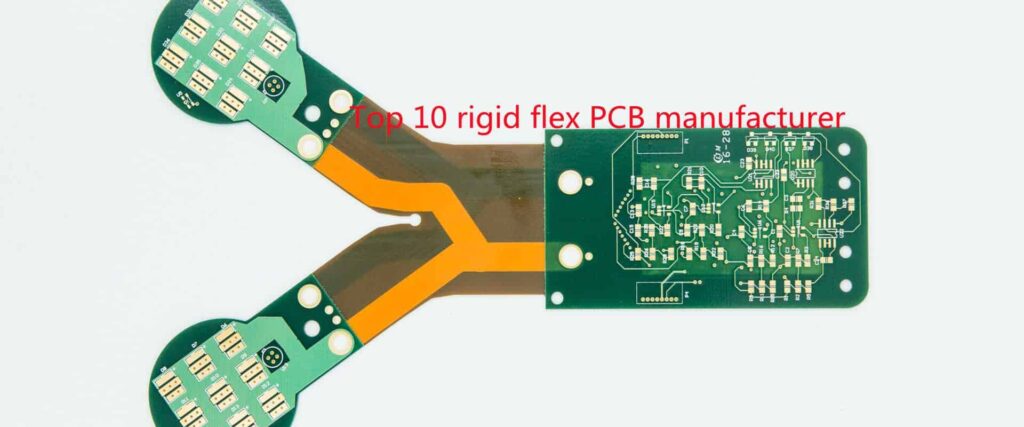
Some of the industries using flexible aluminum PCB technology include:
Automotive
Flexible aluminum backplanes for automotive display panels. High-temperature, high-frequency power boards for electric vehicle systems.
Aerospace and Defense
Rugged PCBs for avionics operating under extremes of temperature, vibration, and chemical exposure. Lightweight boards to reduce weight in satellites and aircraft.
Industrial
Thermal management boards for power electronics in industrial equipment. Flex-to-install PCBs that conform to equipment housings.
Consumer Electronics
Flexible interconnects for wearable devices that can bend and flex with body movements. Low-weight PCBs for mobile phones and tablets.
Medical
X-ray detectable aluminum PCBs used in medical implants that must be transparent to imaging. High reliability boards for lifesaving equipment in hospitals.
Internet of Things
Flexible sensor nodes in smart city and home automation networks. Boards for miniature IoT edge devices.
In summary, flexible aluminum PCB technology enables reliability, thermal performance, and lightweight design needed for modern electronics. As IoT and high-power applications continue to grow, flexible aluminum PCBs will see expanded adoption across industries.
Flexible Aluminum PCB Design Considerations
Designers should keep the following guidelines in mind when laying out flexible aluminum PCBs:
- Use large bend radii (>10X foil thickness) in dynamic flex areas
- Avoid rigid components in flex zones
- Minimize board thickness for maximal flexibility
- Ensure trace widths/spacings account for flexibility
- Include thermal reliefs around heat-generating components
- Select cold/hot solder masks rated for high temperatures
- Allow for thermal expansion of aluminum substrate
- Take aluminum CTE into account during assembly
Following established flexible PCB design rules will ensure the boards survive mechanical stresses during use without any cracking or delamination issues.
Flexible Aluminum vs. FR-4 PCB Comparison
Parameter | Flexible Aluminum PCB | FR-4 PCB |
---|---|---|
Weight | Lightweight | Heavy |
Thermal conductivity | Excellent | Poor |
Temperature resistance | >200°C continuous | 130°C max |
Flexibility | Highly flexible | Rigid |
Chemical resistance | Excellent | Moderate |
Cost | Lower | Higher |
Reliability | Very high | Moderate |
Flexible Aluminum PCBs – Frequently Asked Questions
Q: How are components mounted on flexible aluminum PCBs?
A: Flexible aluminum PCBs use SMT components secured with high-temperature solder pastes and epoxy adhesives. Through-hole components with compliant leads are also used in dynamic flex areas.
Q: Can flex aluminum PCBs be bent repeatedly?
A: Yes, aluminum PCBs are engineered to withstand thousands of tight bend cycles without any cracks in copper or substrate. This makes them ideal for dynamic flexible applications.
Q: Are there any limitations on the minimum bend radius?
A: As a rule of thumb, the minimum bend radius should be at least 10X the total board thickness. Sharp folds below this can overstress the copper traces.
Q: Can aluminum PCBs be soldered using regular tin-lead or lead-free solders?
A: No, high lead-containing solders will dissolve aluminum. Soldering must be done using aluminum-compatible alloys like tin-zinc or tin-silver-copper solders.
Q: Is the thermal expansion of aluminum a concern during soldering?
A: The CTE mismatch between aluminum and other metals can induce stresses during soldering. Using a step-down thermal profile and aluminum-specific solders minimizes these effects.
Conclusion
Flexible aluminum PCBs represent an enabling technology for next-generation lightweight and reliable electronics. With their unbeatable thermal performance and robust mechanical properties, flex aluminum boards are finding increased applications in extreme environment industries from automotive to aerospace. As manufacturing costs continue to decline, flexible aluminum PCBs will become the substrate of choice for high-frequency and high-power portable devices.
Leave a Reply