Introduction
Aircraft flex stiffeners are structural reinforcements installed on aircraft skins to increase stiffness and reduce flexing. They play a critical role in aircraft design by allowing for thinner and lighter skins without sacrificing strength or aerodynamic smoothness. In this article, we will discuss what flex stiffeners are, why they are important, the different types used, and some key design considerations when working with them.
What are Flex Stiffeners?

Flex stiffeners, also known as stringers, are long, thin strips of metal or composite material that run spanwise along the aircraft’s fuselage or wings. They are typically made of aluminum or advanced composites like carbon fiber.
Flex stiffeners serve two key functions:
- Increase the stiffness of the skin panels they are attached to
- Transfer load from the skin into internal structure like spars and ribs
By making the skin stiffer, flex stiffeners allow it to be made thinner and lighter while still maintaining required strength and stiffness levels. This optimization is crucial for improving aircraft performance.
Why are Flex Stiffeners Important?
There are several key reasons flex stiffeners play such an important role:
Strength
- Transfer loads from skin to internal structure
- Allow thinner skins by increasing panel stiffness
Aerodynamics
- Enable smooth exterior surfaces
- Prevent skin buckling at high speeds
Weight Savings
- Enable thinner, lighter skins
- Are lightweight themselves
Damage Tolerance
- Slow crack growth rate
- Provide redundant load paths
Manufacturing
- Simple shapes allow efficient manufacturing
- Compatible with skin fabrication processes
By providing all these benefits, proper use of flex stiffeners is critical for building lightweight, efficient aircraft.
Types of Flex Stiffeners
There are two main types of flex stiffeners used in aircraft design:
Longitudinal Stringers
- Run lengthwise along the fuselage
- Transfer bending loads into frames
- Made of metal or composites
Circumferential Frames
- Run across fuselage circumference
- Transfer hoop stresses into longitudinal members
- Usually made of metal
Stringers make up the majority of flex stiffeners. On wings, they run spanwise from root to tip. On fuselages, they run fore and aft.
Key Design Considerations
Designing an optimal flex stiffener system requires considering many factors:
Stiffness Requirements
- Determine minimum stiffener size to meet panel stiffness needs
Load Transfer
- Size and space stiffeners to properly transfer skin loads
Manufacturability
- Select sizes and shapes that allow efficient fabrication
Damage Tolerance
- Ensure fail-safety through crack stiffening or stiffener spacing
Weight Optimization
- Balance stiffener weight vs. skin thickness
Aerodynamic Smoothness
- Avoid steps at stiffener interfaces
Inspections and Repair
- Allow access for inspection and repair
Corrosion Resistance
- Use corrosion-resistant materials/treatments
Cost
- Optimize manufacturing and material costs
Careful trade studies are carried out during design to optimize the flex stiffener system.
Conclusion
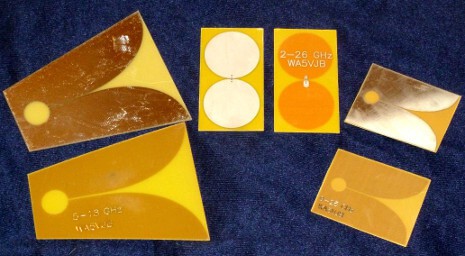
Flex stiffeners like stringers and frames are deceptively simple but enable structurally efficient, damage-tolerant skins that are lighter, thinner, and aerodynamically smoother. Understanding key design principles allows aircraft engineers to tailor flex stiffener systems to unique program requirements. With the growing use of advanced composite materials, flex stiffeners will continue playing a key enabling role in building the next generation of lightweight, high-performance aircraft.
Frequently Asked Questions
What are the main functions of aircraft flex stiffeners?
The two main functions of flex stiffeners are:
- Increase the bending stiffness of skin panels they are attached to
- Transfer skin loads into internal structural elements like spars and ribs
By making the skin stiffer, flex stiffeners allow it to be made thinner and lighter. They also provide redundant load paths for fail-safety.
How do stringers and frames differ?
Stringers primarily run longitudinally along the aircraft, transferring bending loads. Frames run circumferentially around fuselage barrels, transferring hoop stresses.
Stringers are more numerous and account for most flex stiffeners. Frames are heavier and used at discrete locations to maintain cross-section shape.
What materials are used for modern aircraft flex stiffeners?
Most modern large aircraft use advanced composites like carbon fiber reinforced plastic (CFRP) for stringers and frames. Aluminum alloys are also still widely used.
Composites provide high stiffness- and strength-to-weight ratios. But aluminum alloys retain advantages like corrosion resistance, conductivity, and repairability.
How are composite flex stiffeners manufactured?
Common methods include:
- Pre-impregnated unidirectional tape layup
- Braiding over mandrels
- Automated fiber placement
- Filament winding
The stiffeners are usually cured integrally with the skin for joint optimization. The low temperatures needed to cure composites avoid skin damage.
How does damage tolerance factor into flex stiffener design?
Designers ensure adequate fail-safety through proper sizing, spacing, and material selection. Crack retarders may be used to slow propagation. If one stiffener fails, others provide alternate load paths.
Leave a Reply