Introduction
A flex PCB, also known as a flexible printed circuit board, is a type of PCB that can bend and flex. Flex PCBs are made with flexible substrate materials like polyimide or polyester rather than traditional rigid FR-4. The ability to flex makes them useful for many applications where a rigid PCB would be impractical.
One of the key specifications for a flex PCB is the thickness. Selecting the right thickness for your application requires understanding the tradeoffs between thickness, flexibility, and durability. This guide will examine flex PCB thickness in detail, including common thickness ranges, how thickness impacts performance, and recommendations for selecting the optimal thickness.
Common Thickness Ranges
Flex PCBs are available in a wide range of thicknesses to suit different applications. Here are some of the most common thickness ranges:
- Extremely thin: 25-50 μm. Ultra-thin boards with very high flexibility.
- Very thin: 50-100 μm. High flexibility with good durability.
- Thin: 100-150 μm. Balances flexibility and durability.
- Thick: 150-200 μm. Prioritizes durability over flexibility.
- Very thick: 200+ μm. Maximizes durability for more rigid requirements.
In general, thinner flex PCBs are more flexible and can handle tighter bends, while thicker boards are more durable for complex shapes and dynamic flexing.
How Thickness Impacts Performance
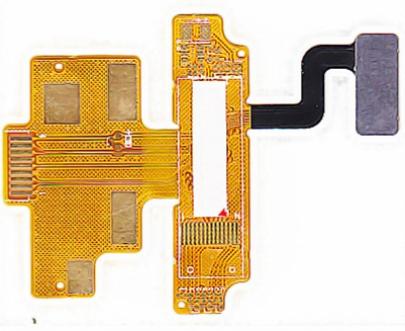
Flex PCB thickness has several important impacts on performance:
Flexibility
- Thinner flex PCBs can bend into tighter radii.
- Minimum bend radius typically ranges from 2-10 times the thickness.
- Thinner boards conform better to surfaces and moving parts.
Durability
- Thicker boards better withstand dynamic flexing and repeated bends.
- Thicker laminate and copper help prevent cracking.
- Thicker PCBs resist damage from impacts and abrasion.
Manufacturability
- Thinner boards facilitate high-density fine line traces and spaces.
- Thicker boards allow more complex circuitry and components.
- Thicker laminate aids processing—thinner can be more challenging.
Stiffness
- Thicker flex PCBs have higher stiffness and act more rigid.
- Thinness allows a more seamless flexible transition.
As a guideline, a minimum thickness of around 75-100 μm offers a good balance between flexibility, durability, and ease of manufacturing for many typical applications. More demanding uses may require thicker or thinner extremes.
Recommendations for Selecting Thickness
Here are some best practice recommendations when selecting the thickness for your flex PCB design:
- Consider minimum bend radius requirements. Aim for 2-10x the thickness.
- Account for dynamic flexing, repeated bends, and expected service life.
- Thicker for complex shapes, thin for simple folds.
- Thinner for compact, dense circuits. Thicker for more complex boards.
- Evaluate manufacturability tradeoffs with your PCB supplier.
- Prototype with different thicknesses when possible.
- Choose thicker laminate for rigid sections and components.
- Allow slightly thicker finished thickness for coverlay or stiffeners.
- Budget for potential later thickness reductions if needed.
Using these guidelines, you can dial in the optimal flex PCB thickness for your specific mechanical and electrical requirements.
Thickness Requirements for Common Applications
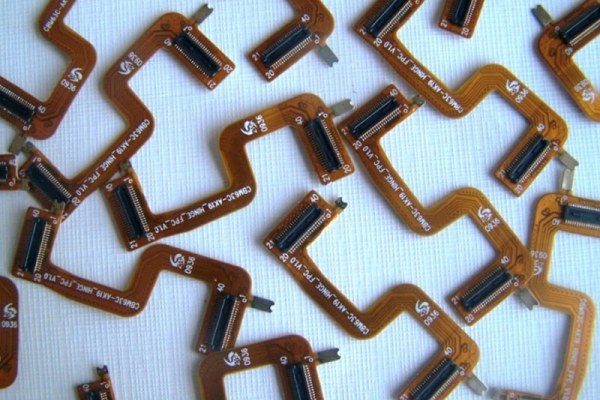
The preferred PCB thickness varies for different flex circuit applications. Here are typical ranges:
Application | Thickness Range |
---|---|
Wearables | 25-100 μm |
Medical Devices | 50-150 μm |
Consumer Electronics | 50-175 μm |
Automotive | 100-200 μm |
Industrial | 125-250 μm |
Military/Aerospace | 150-250+ μm |
Wearables and consumer electronics value thin, highly flexible PCBs, while automotive and industrial applications demand maximum durability. In general, dynamic and high-stress environments warrant thicker flex PCBs.
Conclusion
Flex PCB thickness has a major impact on flexibility, durability, manufacturability, and performance. Carefully selecting the right thickness involves balancing tradeoffs while meeting mechanical and electrical requirements. With an understanding of common thickness ranges, performance impacts, and design recommendations, engineers can optimize their flex PCB thickness for any application. Proper thickness selection ensures your flex PCB can withstand its intended operating conditions and environment while delivering reliable performance.
FQA Section
Below are some commonly asked questions and answers about flex PCB thickness:
Q: What is the thinnest available flex PCB thickness?
A: Extremely thin flex PCBs of 25-50 μm are available, but can be challenging to manufacture and fragile in use. 50 μm is a practical lower limit for simple circuits.
Q: When should I use a thicker vs. thinner flex PCB?
A: Use thinner when high flexibility and tight bend radii are critical. Use thicker when ruggedness and repeated dynamic flexing are needed.
Q: How do I calculate the ideal thickness for my application?
A: Consider minimum bend requirements, expected life cycle, stiffener locations, and manufacturability. Involve your flex PCB supplier for recommendations.
Q: Can different thicknesses be combined on one flex board?
A: Yes, rigid sections and components can use thicker laminate than dynamic flexing areas on the same board.
Q: Does flex PCB thickness affect impedance control and signal integrity?
A: Yes, thinner dielectrics require tighter trace geometries. Thicker laminates allow wider lines and spacing. Involve your PCB designer to account for thickness.
Q: Can a flex PCB be made thinner after initial fabrication?
A: Yes, but with limited tolerance. Having margin in your initial design accommodates potential future thinning.
Leave a Reply