Key Information About Flexible Printed Circuit Board Suppliers
Flexible printed circuits (FPCs), also known as flex circuits, are made from flexible polymer substrates that allow circuits to bend and flex. FPCs are commonly used in consumer electronics, medical devices, automotive electronics, aerospace applications, and more. Choosing the right flex circuit board supplier is crucial to get high-quality and reliable flex PCBs for your application. This guide provides key information about flex PCB suppliers to assist with supplier selection.
What are the Different Types of Flex PCB Suppliers?
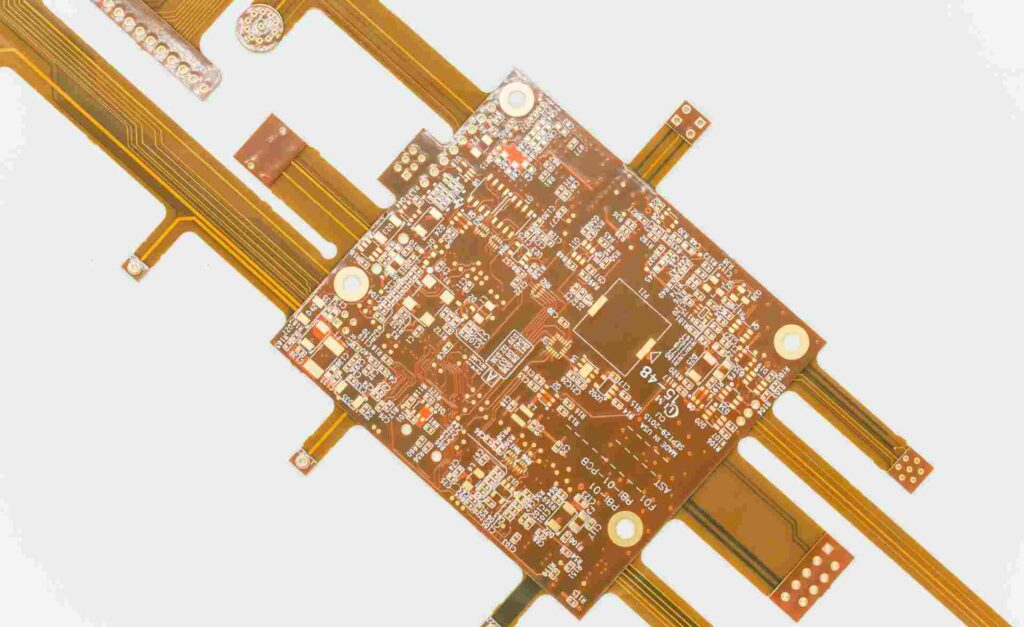
There are a few main types of flex PCB suppliers:
- Flex PCB manufacturers – These suppliers have their own flex PCB fabrication facilities to manufacture the flex circuits. They directly control the production process.
- Flex PCB trading companies – These suppliers source and trade flex circuits from multiple factories. They do not own their own fabrication capabilities.
- OEM flex PCB suppliers – Some original equipment manufacturers (OEMs) that make finished products also fabricate flex PCBs as part of their vertical integration strategy.
- Flex PCB prototypes vs. production – Some suppliers specialize in fast prototype PCB production while others are set up for higher volume manufacturing.
Key Flex PCB Supplier Capabilities to Evaluate
When comparing and selecting a flex PCB supplier, some key capabilities and qualifications to look for include:
Flex PCB Manufacturing Technology
- Photolithography equipment – High resolution equipment like laser direct imaging (LDI) offers fine line capabilities.
- Etching processes – Can they do different types of chemical etching like cupric chloride and ammonium persulfate?
- Layer alignment – How accurately can they align layers and vias during lamination?
- Finishing – What plating and coating options are available like ENIG, immersion tin, solder mask, etc.?
Flex PCB Materials Offered
- Substrate types – Polyimide, polyester, PEN, PET, composite, adhesiveless, etc.
- Copper thickness – Can they handle different copper weights?
- Coverlay – What types of coverlay materials are supported?
- Bonding films – Do they offer acrylic, modified acrylic, or polyimide bonding films?
Design Capabilities
- Design support – Do they offer flex PCB layout services and design for manufacturing (DFM) review?
- Complex circuits – Can they manufacture high density interconnects (HDI) flex?
- Simulation – Are modeling, thermal analysis, and signal integrity services available?
Quality Certifications
- ISO 9001/13485/TS16949 – Certified quality management systems for different markets.
- IATF 16949 – Automotive quality standard.
- AS9100 – Aerospace quality management certification.
- ITAR – Compliance for manufacturing defense and military products.
- IPC standards – Validated processes according to IPC standards for flex PCBs.
- Testing – In-house testing like AOI, flying probe, fixture testing to ensure quality.
Customer Service Capability
- Technical support – How responsive are they to technical questions during design and qualification?
- Documentation – How detailed and organized are their process specs and quality reports?
- Communication – Do they have an established sales team and account manager structure? Is English fluency good?
- Responsiveness – Are they flexible and timely with quotes, prototyping, and order deliveries?
Company Background Factors
- Specialization – Flex PCB manufacturing should be a core competency, not a side business.
- Financials – Stable financial track record provides supply assurance.
- Manufacturing scale – Do they have capacity and experience for your projected volumes?
- Geographic location – Proximity can help with communication, delivery, quality control visits.
Flex PCB Supplier Search Process
Follow these steps when researching and selecting a flex PCB supplier:
Step 1. Define Technical Requirements
- Outline the key parameters for your flex board like PCB specs, design requirements, materials needed, quality standards, volume projections, etc. This helps determine supplier capabilities needed.
Step 2. Make a Flex PCB Supplier List
- Search for suppliers online, check directories, ask colleagues for referrals. Include different supplier types – manufacturers, traders, OEMs, prototyping specialists.
Step 3. Issue RFQs
- Send the PCB requirements and request for quotation (RFQ) to 5-10 suppliers. Get quotes for cost, lead times, and production plan.
Step 4. Evaluate Quotes and Capabilities
- Review theDetailed responses and select 2-3 top candidates that best fit. Verify their capabilities match your needs.
Step 5. Send Test Orders
- Have candidates produce a small test batch to evaluate quality firsthand. Test their service delivery.
Step 6. Select Primary Flex Supplier
- After validating performance on prototypes/tests, choose 1 preferred supplier for production. Negotiate pricing/terms.
Step 7. Manage and Monitor Performance
- During production, closely monitor quality levels, on-time delivery, responsiveness and continuously improve.
Top 10 Flex PCB Suppliers in China
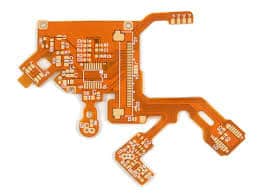
China has the largest flex PCB manufacturing ecosystem globally. Here are 10 leading flex circuit suppliers headquartered and operating in China:
Flex PCB Company | Key Capabilities |
---|---|
Avary Holding | Flex & rigid-flex PCBs up to 30 layers. Focus on automotive electronics. |
Cicor | Swiss-owned. Flex, rigid-flex, HDI, substrate, ceramic PCBs. |
Compass Technology | Flex, rigid-flex, sculpted circuits. Consumer electronics focus. |
Dongguan Somacis | Quick-turn prototypes, small to medium flex PCB production. |
Kinwong Electronics | Large flex & rigid-flex PCB manufacturer. Consumer and automotive applications. |
Multek Flexible Circuits | Flex, rigid-flex, roll-to-roll processing. Part of big PCB manufacturer Zhen Ding Tech. |
Suzhou Dongshan Precision | Medium to large volumes. Auto, medical, industrial apps. |
Topscom | Flex and rigid-flex PCBs. Mobile phone flex boards. |
Wus Printed Circuit | Large manufacturer, especially for consumer electronics. |
ZDT (Zhen Ding Technology) | One of largest PCB producers globally. Flex, HDI, substrate PCB capabilities. |
This list provides an overview of major flex circuit suppliers in China for consideration and benchmarking. The companies have expertise working with international customers. With its expansive flex PCB manufacturing ecosystem, China offers cost competitiveness, but be sure to validate quality systems and product consistency.
Flex PCB Supplier Selection Checklist
Use this checklist of key points when evaluating flex PCB supplier options:
- Specialized in flex PCB manufacturing and engineering
- Production scale matches projected volumes
- Technically capable of meeting PCB requirements
- High quality standards and testing – ISO, IPC certifications
- Competitive pricing with acceptable payment terms
- Reasonable production lead times
- Responsive customer service and technical support
- Fluent communications in English
- Stable financial condition of company
- Positive reviews from existing customers
- Acceptable location for logistics and site visits
- Flexibility to handle prototype builds
- Continuously improves processes and performance
Flex PCB Supplier Qualification Process
Once prospective flex PCB suppliers are identified, a structured qualification process helps verify their capabilities before selecting a long-term partner. Key elements of flex circuit supplier qualification include:
Engineering Assessment
Review the supplier’s design, fabrication and testing capabilities in detail. Verify they can produce the required PCB specs by examining:
- Equipment types and production processes
- Range of PCB materials and constructions possible
- Complexity of designs previously produced
- Evidence of process validations and IPC certifications
- Knowledge and expertise of engineering team
Quality System Audit
Conduct an on-site audit of the supplier’s quality management system. Review elements like:
- Quality control procedures and inspection stages
- Equipment calibration and maintenance
- Traceability methods
- Handling of non-conforming materials
- Corrective/preventive action approaches
- Quality certifications achieved
Sample Builds
Have the supplier produce a pilot run of PCB samples to test performance firsthand. Test samples for:
- PCB quality – layer accuracy, line width, spacing, etc.
- Reliability testing – thermal stress, voltage stress, vibration, etc.
- Product-level testing once assembled into a system
Business Relationship Factors
Assess strategic fit factors like:
- Ability to scale production up or down
- Supply chain transparency and continuity assurances
- Payment terms and pricing model
- Communication responsiveness and collaboration willingness
- Protecting IP and confidential information
Using controlled build samples, audits, analysis of capabilities, and relationship evaluations helps comprehensively qualify flex PCB suppliers. This reduces risk of problems during volume production.
Flex PCB Supplier Management Best Practices
Once a flex circuit supplier is selected, it’s important to actively manage the relationship for continued success. Follow these best practices:
- Maintain frequent communication – Have regular status calls, quality reviews, and business meetings with stakeholders. Visit the supplier site when possible.
- Give feedback – Provide constructive feedback so the supplier can improve. Recognize excellent performance too.
- Monitor quality – Review quality reports every shipment. Periodically audit and inspect at their facility.
- Resolve issues quickly – Rapidly troubleshoot any problems jointly and implement corrective actions.
- Plan ahead – Keep supplier updated on forecasted demand and new product plans. Improve processes proactively.
- Negotiate win-win deals – Structure pricing and agreements in a fair, sustainable manner. Support the supplier’s business needs.
- Explore technology advances – Learn about the supplier’s new capabilities and machinery investments applicable to your products.
- Build rapport – Develop mutual understanding and trust with your supplier account team for a smoother partnership.
Proactively managing flex PCB supplier relationships reduces defects, improves satisfaction, and drives innovation.
Conclusion
Selecting qualified and reliable flex PCB suppliers is crucial for product quality and performance. Use the guidance in this article to choose flex circuit partners with the right capabilities, quality systems, customer service, and collaborative business relationships. With an effective supplier, you gain access to innovative flex PCB technology and robust global supply chains to fulfill your program needs. Partner with a few complimentary suppliers and manage them closely to make your new product introductions faster and more successful using flexible circuits.
Flex PCB Supplier Selection FAQs
Here are some frequently asked questions about selecting flex PCB suppliers:
Q: Should I use flex PCB suppliers in China or a different country?
A: Many leading flex PCB suppliers are located in China due to its expansive manufacturing ecosystem. However, also consider options in your region if supplier proximity is beneficial for delivery, communication, quality control, IP protection, regulatory compliance, etc.
Q: How many potential suppliers should I evaluate when selecting one?
A: It’s recommended to start with 5-10 suppliers to issue RFQs. Narrow down to 2-3 for prototype builds. Finally select 1 primary supplier for production with a 2nd source as a backup plan.
Q: What volume of flex PCBs should be produced during supplier testing?
A: 10-25 boards is a typical quantity for initial samples to fully evaluate quality. For longer test runs, produce 100-500 boards to also assess process consistency.
Q: Should I choose the flex PCB supplier with the lowest price quote?
A: No, you should not just choose based on price alone. Ensure the supplier has proven technical capabilities for your needs and strong quality systems beyond just having the cheapest quote.
Q: How often should I visit our flex PCB supplier’s factory?
A: Plan to visit 1-2 times per year for an audit. New product introduction and ramp up may require more frequent visits. Ongoing open communication is essential.
Leave a Reply