Introduction
Flex circuits, also known as flex PCBs or flexible printed circuit boards, are playing an increasingly important role in modern electronics. A flex circuit consists of conductive traces and pads printed or etched onto a thin, flexible dielectric substrate such as polyimide. The ability of flex circuits to bend and flex makes them ideal for applications where printed circuit boards would be too rigid, such as in mobile devices, medical devices, wearables, IoT products, and automotive electronics.
For product developers, getting flex circuit prototypes made quickly is key to bringing new products to market faster. In this article, we’ll look at the flex circuit prototyping process, technologies and techniques that enable rapid prototyping, and how to work effectively with a flex circuit manufacturer to accelerate your time-to-market.
Overview of the Flex Circuit Prototyping Process
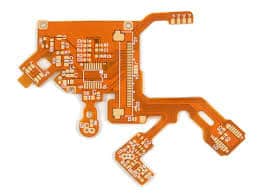
The overall process of taking a flex circuit design from concept to prototype includes the following key steps:
- Design creation – The flex circuit design is created in CAD software, showing the conductive traces, coverlay cutouts, connectors, and other features.
- Design review – The design gerber files are reviewed by the manufacturer and any improvements or modifications are discussed.
- Prototype fabrication – The actual flex circuit prototypes are fabricated, often using faster techniques optimized for prototyping.
- Testing and evaluation – The prototypes are tested for fit, form, and function in the product. If needed, design modifications are made.
- Pre-production – Once the design is finalized, pre-production flex circuits are ordered in small batches.
- Full production – The full production design is sent to mass manufacturing.
Accelerating the prototyping stage is crucial to getting your product to market faster. The rest of this article examines flex circuit prototyping in more detail.
Flex Circuit Prototyping Techniques and Technologies
Several advancements in flex circuit fabrication make prototyping faster and more cost-effective:
Laser Direct Imaging (LDI)
Laser direct imaging uses a laser to precisely “draw” the circuit traces directly onto the flex circuit material, eliminating the need for phototools. This allows rapid design revisions and on-demand fabrication of prototypes.
Laser Cutting
A laser can quickly and accurately cut flex circuits to shape after imaging. Laser cutting enables fast prototyping of complex flex shapes.
On-Demand Fabrication
With LDI and laser cutting, flex circuits can be fabricated within 24-48 hours without any tooling. This enables getting prototype iterations back from the manufacturer much faster.
Panel Prototyping
Multiple flex circuit designs can be grouped on a panel for panelization. This allows multiple prototype designs to be fabricated together, increasing efficiency and driving down costs.
Stiffener Panels
Polyimide-based flex circuits have high flexibility. Adding a rigid stiffener panel provides stability for circuitry that needs to maintain a set shape. This facilitates prototyping complex 3D flex shapes.
Double-Sided Flex
Flex circuits can have circuit traces on both sides of the substrate. This allows higher circuit density in a small space – ideal for complex flex prototypes.
Flex-Rigid Integration
Combining flex circuits and rigid printed circuit boards enables integrated flex-rigid prototypes. The rigid sections provide stability while the flex areas allow movement and adjustment.
By leveraging these kinds of advanced prototyping technologies, flex circuit manufacturers can deliver prototypes in just a few days. This allows product developers to take an iterative design approach with multiple prototype iterations in parallel with other product development workstreams.
Working With a Flex Circuit Manufacturer
Selecting the right flex circuit manufacturer and establishing an effective working relationship is key to smooth prototyping. Here are some best practices:
- Select a manufacturer with proven flex prototyping experience – Ask about their specific prototyping capabilities and expertise with technologies like LDI.
- Get the manufacturer involved early in the design phase – Their input can help optimize the design for manufacturability and minimize prototype iterations.
- Communicate clearly – Provide all the necessary design files and specifications to avoid back and forth. Be clear about quantity and schedule requirements.
- Visit the manufacturer’s facility – Tour their production floor firsthand to gain insight into their capabilities.
- Build personal rapport – Develop a good working relationship with your account manager and engineers. This helps accelerate fabrication and issue resolution.
- Leverage design review – Take advantage of the manufacturer’s design review process before prototyping begins. This prevents errors and saves time.
- Plan prototype phases – Map out a prototyping plan and timeline with the manufacturer early on. Communicate key milestone dates.
Following these kinds of best practices with an experienced flex circuit manufacturer enables getting well-made prototypes delivered on schedule, letting you evaluate designs faster and accelerate time-to-market.
Typical Flex Circuit Prototype Process Timeline
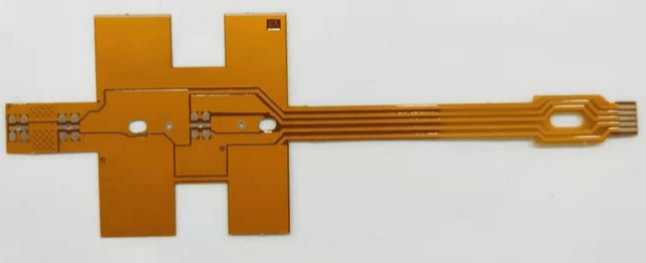
To understand how quickly modern flex circuit prototyping can move, here is a typical timeline from design to prototype:
Stage | Timeframe |
---|---|
Initial design files submitted | Day 1 |
Design review and feedback | Day 2 |
Design files updated | Day 3 |
Prototype fabrication with LDI | Day 4-5 |
Prototypes shipped to customer | Day 6 |
Testing and evaluation | Day 7-9 |
Design revisions submitted | Day 10 |
Revised prototypes fabricated | Day 11-12 |
Revised prototypes shipped | Day 13 |
This shows how, by leveraging the latest prototyping processes, an initial prototype can be in hand within 5 business days, with additional revisions possible within 2-3 days each. For products where time-to-market is critical, these rapid turnaround capabilities are extremely valuable.
Cost Analysis
Here is an overview of typical costs for flex circuit prototyping:
Prototyping Options | Typical Cost Per Piece |
---|---|
2-layer simple flex prototype | $100-$300 |
Multilayer complex rigid-flex | $300-$1,000 |
Prototype tooling and setup | $1,500-$3,000 |
Expedited fabrication (24-48 hrs) | +50% |
Design engineering support | $125/hr |
Keep in mind these are just general estimates – actual pricing depends on design complexity, order quantities, lead times, and manufacturer capabilities. Using panelization and engineering collaboration with the manufacturer can help drive down prototyping costs significantly.
Key Takeaways
Here are some key points on the flex circuit prototyping process:
- New technologies like LDI allow on-demand fabrication of flex circuit prototypes.
- Leveraging techniques like panels and laser cutting provide more flexibility.
- Getting the manufacturer engaged early in the design process helps optimize prototyping.
- Clear communication and setting expectations are crucial to smooth prototyping.
- A typical timeline can deliver initial prototypes in less than a week.
- Prototyping cost depends on complexity, quantities, and manufacturer capabilities.
By working effectively with an experienced manufacturer, product developers can now get high-quality flex circuit prototypes fabricated in just days to meet tight time-to-market objectives.
FQA
What are the benefits of flex circuit prototypes?
Some key benefits of flex circuit prototypes include:
- Evaluating form, fit, and function early in the design cycle
- Allowing testing of interconnections and movements
- Identifying design improvements needed
- Ensuring the flex PCB will work as intended when manufactured
- Accelerating overall product development timelines
How are flex prototypes different from production flex circuits?
There are a few key differences between prototypes and production flex circuits:
- Prototypes use faster fabrication techniques like LDI instead of traditional photoimaging. This enables faster turnaround with less tooling.
- Prototypes are often fabricated in small batches vs. high-volume production runs.
- Prototype designs may not be fully optimized for manufacturing yield and efficiency.
- The quality, tolerances, and reliability may be reduced in prototypes to save time and cost.
- Prototypes focus on evaluating the core design vs. production where complete test coverage and inspection is implemented.
What are some tips for effective flex circuit prototyping?
Some best practice tips include:
- Build in test points and interfaces to make it easy to evaluate the prototype
- Clearly document known prototype limitations and risks
- Define metrics for prototype evaluation and testing
- Record results meticulously to inform potential design changes
- Get feedback from team members outside the core engineering group
- Only move to production once the prototype is completely validated
How many prototype iterations are typical?
The number of prototype iterations varies significantly depending on the application complexity, team experience, time pressures, etc. In general, expect at least 2-3 iterations before moving to production. Higher complexity designs may require 5 or more iterations to get right. With effective planning and collaboration with manufacturing partners, the goal is to minimize the number of iterations.
What are the steps after flex circuit prototypes are complete?
The typical next steps after prototype completion are:
- Thoroughly evaluate against requirements and identify improvements needed
- Work with the manufacturer on design revisions
- Fabricate the next version and repeat tests
- Once design is finalized, order a small pilot production run
- Conduct qualification testing, environmental testing, etc. on the pre-production units
- Obtain all necessary certifications
- Launch mass production once fully validated
So prototyping is just the first phase, but it provides the data needed to proceed confidently to larger scale manufacturing.
Conclusion
By leveraging advances in flex circuit fabrication technology and finding the right manufacturing partner, product developers can now obtain high-quality flex PCB prototypes in just days. This enables taking an iterative prototyping approach to refine the design prior to committing to full production. With expertise in rapid prototyping processes, an experienced flex manufacturer helps accelerate time-to-market and get innovative products to market faster. The key is close collaboration between designer and manufacturer, starting as early as possible in the development process. With this approach, flex circuits become an enabler to respond quickly to market opportunities and compete on speed.
Leave a Reply