Introduction
Flex circuits, also known as flexible printed circuits (FPCs), are made from flexible materials that allow them to bend and flex. They are used in a variety of electronics when flexibility is required, like in cell phones, wearables, medical devices, and more. The materials used in flex circuits are constantly evolving to meet industry demands for smaller, faster, and more durable electronics. This article will examine the key materials used in flex circuits today, recent developments, and what’s on the horizon for 2023 and beyond.
Flex Circuit Materials
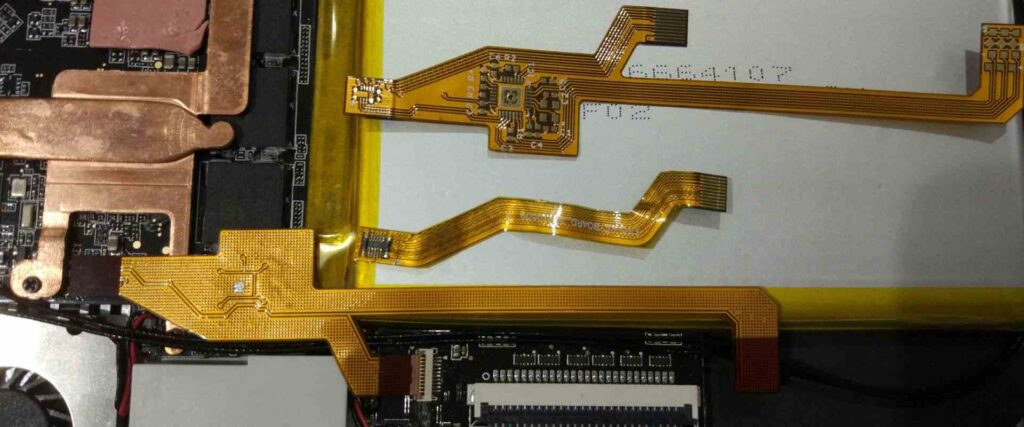
The main component materials of a flex circuit include the base material, conductive materials, and cover layers.
Base Materials
The flexible base, also called the dielectric, provides the circuit’s form and structure. The most common base materials include:
- Polyimide (PI) – Used in over 70% of flex circuits, polyimide offers exceptional thermal stability and chemical resistance. Popular brands include DuPont’s Kapton.
- Polyester (PET) – More economical option than PI, with reasonable flex life and temperature resistance. Melinex is a common PET film.
- Polyethylene Naphthalate (PEN) – High temperature resistance up to 155°C. Teonex is a common PEN film.
- Fluoropolymers (PTFE) – Extremely thin films with excellent chemical resistance. Common options are polytetrafluoroethylene films (PTFE).
Base Material | Key Properties |
---|---|
Polyimide (PI) | Excellent thermal stability, chemical resistance |
Polyester (PET) | Economical, moderate flexibility |
Polyethylene Naphthalate (PEN) | High temp resistance up to 155°C |
Fluoropolymers (PTFE) | Extreme chemical resistance |
Conductors
Conductive materials carry current through the circuit. Common options include:
- Copper – Most commonly used conductor due to high conductivity and flexibility. Available in rolled annealed or rolled tempered.
- Silver – Even higher conductivity than copper but much higher cost. Usually plated only in high frequency or low current circuits.
- Aluminum – Lower conductivity than copper but lighter weight. Sometimes used when weight reduction is critical.
- Carbon – Silk-screened carbon ink used in high volume disposable medical applications.
Cover Layers
Cover layers are laminated over the top of the circuitry for protection. Some options are:
- Coverlay – Primary covering material, often same base material as the flex circuit like Kapton or PET.
- Solder mask – Coating to prevent solder bridging between pads during assembly. Usually epoxy or acrylic based.
- Adhesives – Bond flex circuit layers. Popular choices are acrylic or epoxy adhesives.
- Stiffeners – Materials added to flex or rigid-flex circuits to provide stability and rigidity in certain areas. Common stiffener materials are polyimide, PEN, FR4, aluminum.
Recent Material Developments
Some newer materials making an impact in flex circuit design include:
- Liquid Crystal Polymer (LCP) – Has excellent high frequency signal performance. Allows finer circuit traces.
- Nano materials – Particles added to base materials for increased thermal or electrical performance.
- Biodegradable materials – New materials that decompose in landfills. Helpful for disposable electronics.
- Stretchable circuits – Materials like silicones allow circuits to stretch and flex repeatedly. Used in wearable devices.
The Future of Flex Circuit Materials
Looking ahead, here are some key trends shaping flex circuit material development:
Thinner Base Materials
There is continual effort to reduce thickness of flex circuit base materials. Thinner dielectric films allow finer circuit traces and help reduce overall size in space-constrained electronics. Films as thin as 6 microns are now commercially available.
Flexible Glass
Flexible glass materials like Corning Willow Glass provide the hermetic properties of glass with bendability. This could enable flexible electronics that require glass-like barrier properties against moisture and oxygen.
Higher Temperature Materials
New base materials are being developed to withstand higher temperatures, broadening the applications for flex circuits. PEEK films, for example, can potentially withstand over 230°C for short durations.
Stretchable Circuits
Stretchable conductive materials that can flex repeatedly are an area of highly active research. Applications include skin-like patches for healthcare monitoring and diagnostics.
Biodegradable Substrates
Biodegradable base materials and conductors enable disposable flex circuits that decompose naturally. This helps reduce e-waste from disposable electronics.
Nanomaterials
Adding nanoparticles like graphene to base materials allow thinner, higher performing flex circuits. This enhances properties like thermal conductivity, electrical performance, and barrier properties.
Sustainability
More focus is being placed on sustainable flex circuit materials such as biodegradable or recycled materials. This reduces environmental impact as flex circuits grow in volume.
Conclusion
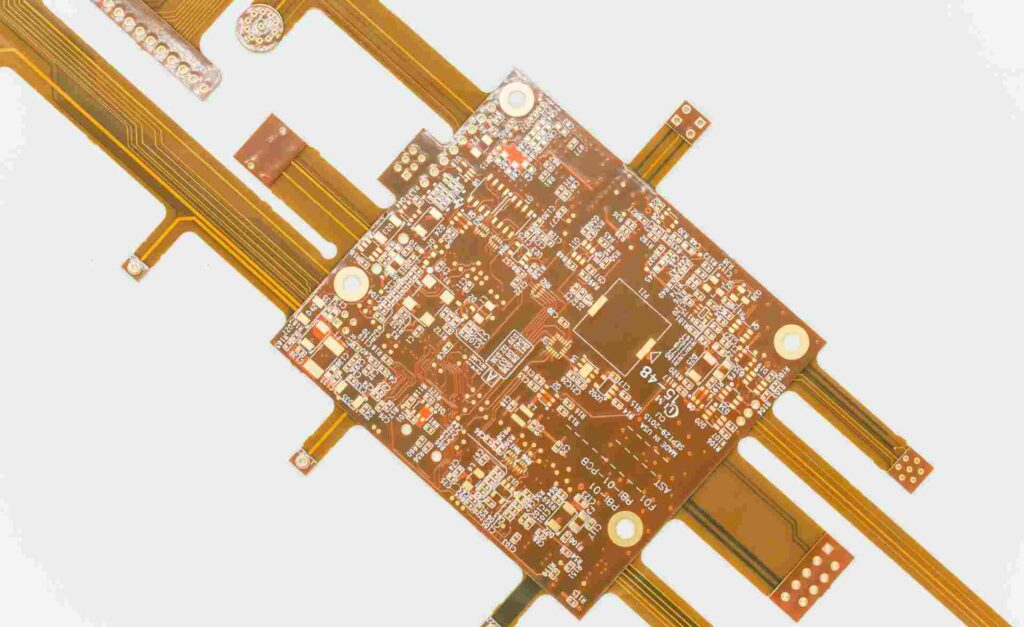
Flex circuit material technology continues advancing rapidly, enabling their use in more diverse and demanding applications. Polyimide remains the most popular base material, while other films offer advantages for high temperature or biodegradability. Conductors continue getting thinner to allow finer circuit traces. Nanomaterials and stretchable substrates are active research areas that could reshape capabilities. Sustainability is also becoming a higher priority in material selection. With so much continued innovation, flex circuits are poised to enable many new generations of thin, powerful, and robust electronic devices.
Flex Circuit Materials FQA
What are the most commonly used base materials for flex circuits?
The most common base materials are polyimide (PI) films like Kapton, followed by polyester (PET) films like Melinex. Polyimide offers high heat resistance while polyester is more economical. Other key films include polyethylene naphthalate (PEN) for higher temperatures and fluoropolymers like PTFE for chemical resistance.
Why is copper the most popular conductor used in flex circuits?
Copper is the dominant flex circuit conductor material due to its high electrical conductivity and flexibility. Copper has lower electrical resistance than alternatives like aluminum, allowing thinner trace widths. It also has good bendability compared to more brittle metals. These advantages make it the ideal choice despite higher cost compared to aluminum.
What are some new advanced materials used in flex circuits?
Some newer advanced materials include liquid crystal polymer (LCP) which has excellent high frequency signal performance, nano materials like graphene to enhance properties, stretchable substrates like silicones for flexible wearables, and biodegradable conductors and base films for environmentally friendly circuits.
How are flexible glass materials like Willow Glass used in flex circuits?
Flexible glass can provide a glass-like barrier against moisture and oxygen permeation. This enables very thin glass circuits to be bent or rolled while maintaining glass’s hermetic properties. Flexible glass could allow glass-based flex circuits for applications requiring glass’s barrier properties, like OLED displays.
What are some key sustainability trends in flex circuit materials?
Sustainability is becoming a higher priority. Trends include renewable materials like cellulose, biodegradable conductors to reduce e-waste, and integration of recycled materials. The materials and manufacturing processes used will increasingly factor sustainability along with performance.
Leave a Reply