Introduction
For companies developing products with flex PCBs, being able to quickly iterate on design concepts and obtain flex circuit prototypes is critical during the development process. Long turnaround times can slow down innovation and delay time-to-market.
This article explores strategies for fast turnaround flex PCB prototyping including:
- What is considered fast turnaround?
- Why speed is important for prototypes
- Design considerations for rapid fabrication
- Flex PCB quickly manufacturing methods
- Partnering with the right flex PCB supplier
- Cost tradeoffs for accelerated schedules
With the right approach, flex PCB prototypes can be produced in just days or weeks instead of multiple months.
What is Considered Fast Turnaround for Flex PCBs?
For flexible PCB prototypes, the typical range of fabrication turnaround times is:
- Standard Turn – 2 to 4 weeks
- Expedited Turn – 1 to 2 weeks
- Super Expedited – 5 days to 2 weeks
The table below summarizes common flex PCB prototype lead times across different urgency levels:
Lead Time | Definition |
---|---|
2-4 weeks | Standard turnaround for prototyping |
1-2 weeks | Expedited turn with premium fee |
5-10 days | Extremely rushed super expedited service |
24-48 hours | Ultra-fast turn for simple boards |
Of course, lead time depends on many variables including flex PCB complexity, quantity, and supplier capabilities.
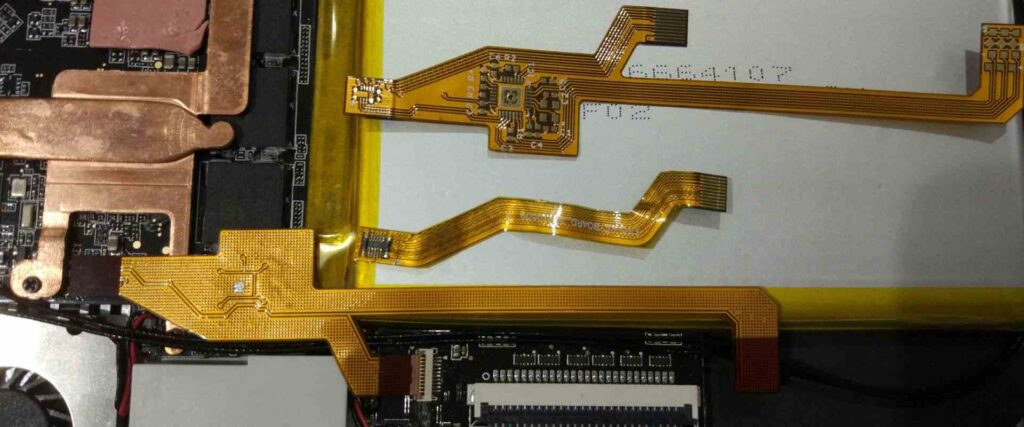
Why Fast Turnaround is Critical for Prototypes
There are several benefits of being able to quickly receive flexible PCB prototypes:
- Faster design validation – Test concepts and identify improvements sooner
- Accelerated development – Reduce overall product development timeline
- Rapid design iterations – Iterate faster based on prototype feedback
- Improved innovation – Speed up the innovation process
- Faster time-to-market – Enable launching products sooner
For products where flex PCBs are a key component, fast prototyping turnaround provides a significant competitive advantage.
Flex PCB Design Considerations for Fast Turnaround
The design itself impacts how rapidly flex PCB prototypes can be fabricated. Strategies that enable faster fabrication include:
- Use a simple 2-layer or single sided layout
- Avoid high density interconnects if possible
- Minimize small features like microvias
- Standardize on commonly available materials
- Reduce layer count since each adds alignment steps
- Loosen up tolerances for prototypes
- Make board outline and cutouts rectilinear instead of curved
- Provide complete design files upfront – avoid iterative rounds of changes
- Keep quantities around 5-10 boards for prototyping stage
A clean, simplified design is most conducive to fast PCB prototype turnaround. Overly dense or complex boards will be harder to produce quickly.
Methods for Fast Turn Flex PCB Prototypes
Flex PCB manufacturers have several techniques to help reduce prototyping lead times:
Prioritized Scheduling
Prototype orders can jump ahead of production orders in scheduling to start fabrication immediately.
Front-Loading Engineering
Much of the engineering review work is completed upfront so manufacturing can begin without delay.
Streamlined Processes
Removing non-critical steps from the fabrication sequence and simplifying procedures where possible.
Strategic Material Selections
Choosing commonly used base materials already in inventory avoids lead time for special material procurement.
Parallel Workflows
Performing multiple process steps simultaneously instead of sequentially. For example, plating can begin before etching is fully finished.
Direct Imaging
Using laser direct imaging for creating traces eliminates lead time associated with producing phototools.
Limited Testing
Only high priority functional tests are done to verify the design. Full IPC testing happens at production stage.
Partnering with the Right Flex PCB Manufacturer
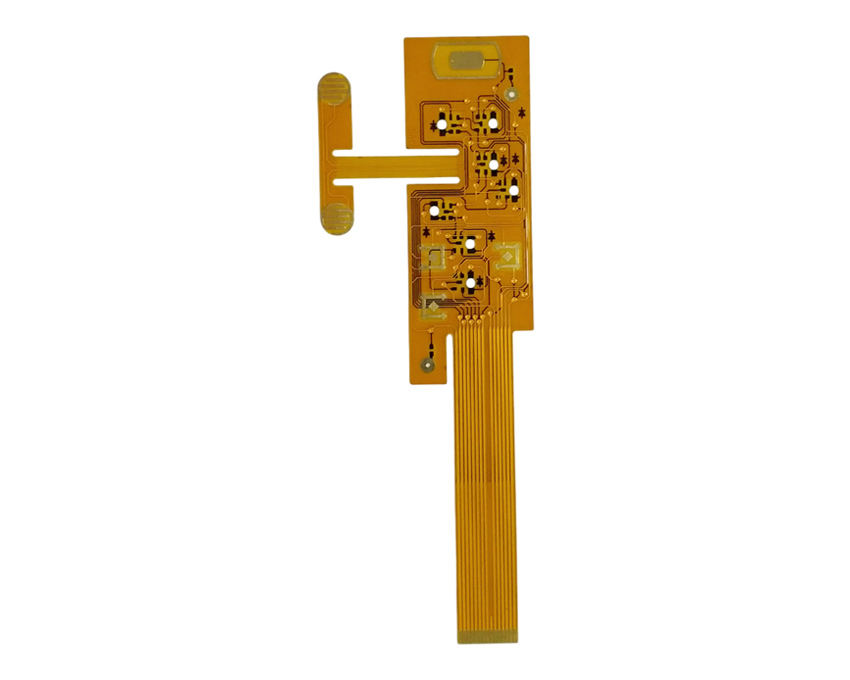
Choosing a flex PCB supplier with capabilities tuned for fast prototyping makes a significant difference in turnaround time. Key supplier attributes for rapid support include:
- Prototype focus – Infrastructure optimized for low volume prototyping versus high volume production
- High mix – Ability to efficiently switch between different designs day-to-day
- Design support – Experienced engineering team to assist with rapid design reviews
- Supplier integration – Tight supplier base able to deliver urgent material orders
- Quality processes – Mature quality systems that avoid lengthy delays from errors
- Active communication – Turnaround focused project management with frequent client updates
- Leading equipment – Manufacturing technology well-maintained for uptime
- Lean operations – Culture of continuous improvement further enhancing velocity
Of course, lead time cannot compromise quality – finding suppliers able to deliver both speed and quality is key.
Cost Tradeoffs for Faster Flex PCB Turnaround
Accelerating delivery of flex PCB prototypes has cost implications that are important to weigh:
- Higher per unit costs – Smaller quantities and expedited fabrication increase cost
- Premium service fees – Added charges for super expedited turn services
- Increased scrap – Faster processing can lead to more waste
- Supply surcharges – Getting materials faster often increases material costs
- Resource overtime – Additional labor to enable aggressive schedule
- Quality risks – Chance of rework from condensed processes
However, the long-term benefits of getting to market faster can offset short-term prototyping costs.
When is Fast Turnaround Most Necessary?
While it’s always desirable to receive prototypes faster, some scenarios warrant the premiums associated with extremely urgent delivery:
- Preparing for important concept demos or design reviews
- Iterating quickly at start of new product development
- Validating models/simulations with empirical data
- Verifying a new flex material or process works as expected
- Prototyping a competitive response product
- Resolving issues right before production launch
Knowing the business context helps determine when fast turnaround is most valuable.
Conclusion
Accelerating flex PCB prototype delivery enables validating designs faster and reducing overall product development timelines. Simplified layouts, partnering with dedicated flex prototyping suppliers, and applying optimized processes are key enablers for fast turnaround. While surcharges may apply, the long term gains of reaching market faster frequently outweigh short-term prototype costs. With the right approach, flex PCB prototypes for simpler designs can be delivered in just days for urgent projects.
FAQ
What are typical standard turnaround times for flex PCB production?
For flex PCB production orders, standard turnaround times are generally 4-8 weeks depending on quantity, design complexity, and supplier capacity.
What design factors tend to increase flex PCB prototyping time?
High density routing, large quantities, tight tolerances, flex-rigid designs, and thick multilayer constructions tend to require longer fabrication times.
What are some alternatives if extremely urgent flex PCB delivery is needed?
Options include breadboards, wire-wrap prototypes, rigid-flex PCBs, or interim use of standard rigid boards if design allows.
When shifted to production, will lead time be similar to prototyping?
No, production lead times tend to be longer as full testing is conducted and optimized scheduling for high volume occurs.
Does faster turnaround affect long-term flex PCB quality?
With proper design and qualified supplier, fast-turn prototypes can deliver equal long-term reliability vs standard turn boards when shifted to production.
Leave a Reply