Introduction
Printed Circuit Board (PCB) soldering is a crucial process in the manufacturing of electronic devices. It involves joining electronic components to the PCB using solder, a metal alloy that melts at a relatively low temperature. The quality of the soldering process directly affects the functionality, reliability, and longevity of the electronic device. Poor PCB Soldering can lead to various issues, such as short circuits, open circuits, and intermittent connections, which can cause the device to malfunction or fail prematurely.
In this article, we will discuss the factors that contribute to poor PCB soldering and how to mitigate them. We will cover topics such as soldering techniques, equipment, materials, and environmental conditions.
PCB Soldering Techniques
Hand Soldering
Hand soldering is a manual process that involves using a soldering iron to melt solder onto the PCB and components. It is a common technique used for prototyping, small-scale production, and repairs. However, hand soldering is prone to human error and can result in poor soldering quality if not performed correctly.
Common issues with hand soldering include:
- Insufficient or excessive solder
- Cold solder joints
- Bridging between adjacent pads
- Overheating components
To minimize these issues, it is essential to use the correct soldering iron temperature, apply the right amount of solder, and maintain a steady hand while soldering.
Wave Soldering
Wave soldering is an automated process that involves passing the PCB over a molten solder wave. It is commonly used for through-hole components and is suitable for high-volume production. However, wave soldering can also result in poor soldering quality if not set up and maintained properly.
Common issues with wave soldering include:
- Insufficient or excessive solder
- Solder bridges
- Solder balls
- Uneven solder distribution
To minimize these issues, it is essential to optimize the solder wave height, conveyor speed, and preheat temperature. Regular maintenance of the wave soldering machine is also crucial to ensure consistent soldering quality.
Reflow Soldering
Reflow soldering is an automated process that involves applying solder paste to the PCB pads, placing the components, and passing the PCB through a reflow oven. It is commonly used for surface-mount components and is suitable for high-volume production. However, reflow soldering can also result in poor soldering quality if not set up and maintained properly.
Common issues with reflow soldering include:
- Insufficient or excessive solder
- Solder balls
- Tombstoning (components standing on end)
- Uneven solder distribution
To minimize these issues, it is essential to optimize the solder paste application, component placement, and reflow oven temperature profile. Regular maintenance of the reflow soldering machine is also crucial to ensure consistent soldering quality.
Soldering Equipment
Soldering Iron
The soldering iron is the most basic and essential tool for hand soldering. It consists of a heated metal tip that melts the solder and a handle for holding the iron. The quality of the soldering iron directly affects the soldering quality.
Common issues with Soldering Irons include:
- Incorrect tip temperature
- Worn or damaged tips
- Poor thermal recovery
To minimize these issues, it is essential to use a high-quality soldering iron with adjustable temperature control and replace the tips regularly.
Soldering Station
A soldering station is an advanced version of a soldering iron that includes additional features such as digital temperature control, multiple tip sizes, and a stand for holding the iron. It provides more precise control over the soldering process and is suitable for professional use.
Common issues with soldering stations include:
- Incorrect temperature settings
- Dirty or damaged tips
- Poor grounding
To minimize these issues, it is essential to follow the manufacturer’s instructions for setting up and maintaining the soldering station.
Solder Fume Extractor
A solder fume extractor is a device that removes the fumes generated during the soldering process. Solder fumes contain harmful chemicals such as lead and flux that can cause health problems if inhaled.
Common issues with solder fume extractors include:
- Insufficient suction power
- Clogged filters
- Noisy operation
To minimize these issues, it is essential to choose a high-quality solder fume extractor with adequate suction power and replace the filters regularly.
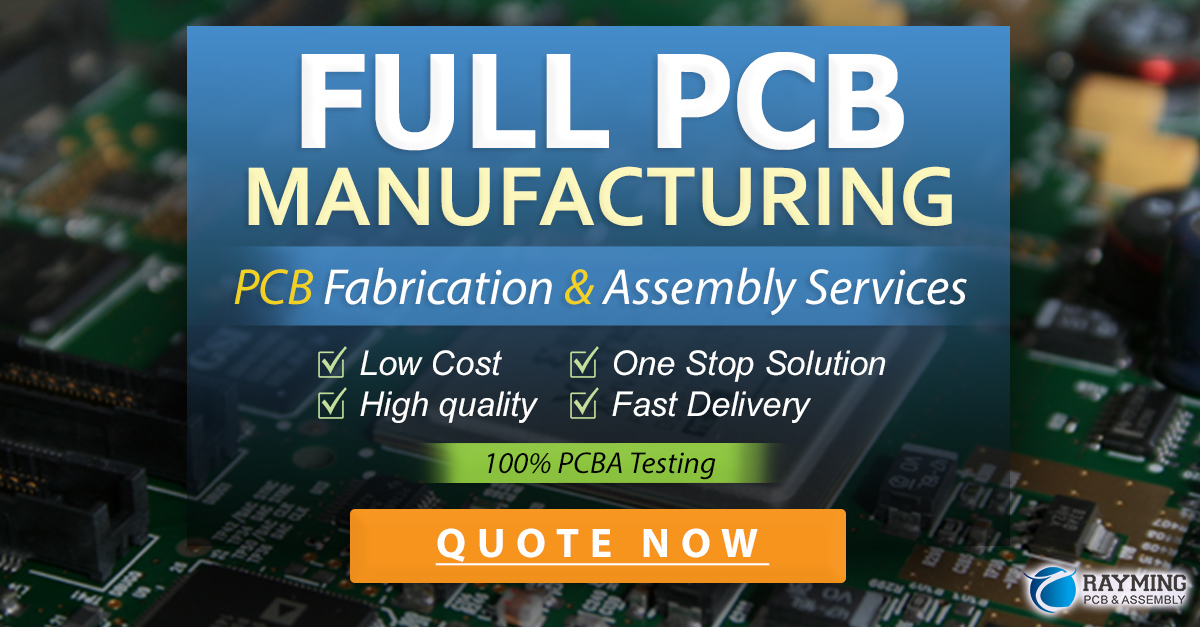
Soldering Materials
Solder
Solder is a metal alloy that melts at a relatively low temperature and is used to join electronic components to the PCB. The most common types of solder are lead-based and lead-free solder.
Common issues with solder include:
- Incorrect alloy composition
- Impurities
- Oxidation
To minimize these issues, it is essential to choose high-quality solder from a reputable supplier and store it in a cool, dry place.
Flux
Flux is a chemical that is used to remove oxides from the surface of the PCB and components and promote solder flow. It is available in various forms, such as liquid, paste, and pen.
Common issues with flux include:
- Incorrect type for the application
- Insufficient or excessive amount
- Residue left on the PCB
To minimize these issues, it is essential to choose the correct type of flux for the application and clean the PCB thoroughly after soldering.
Solder Paste
Solder paste is a mixture of solder powder and flux that is used for reflow soldering. It is applied to the PCB pads using a stencil or syringe.
Common issues with solder paste include:
- Incorrect viscosity
- Insufficient or excessive amount
- Contamination
To minimize these issues, it is essential to choose high-quality solder paste from a reputable supplier and store it in a refrigerator to prevent premature aging.
Environmental Conditions
Temperature and Humidity
Temperature and humidity can affect the soldering process and the quality of the solder joints. High temperature and humidity can cause oxidation and corrosion of the PCB and components, while low temperature and humidity can cause poor solder flow and weak solder joints.
The ideal temperature and humidity range for soldering is:
- Temperature: 20-25°C (68-77°F)
- Relative humidity: 30-50%
To maintain the ideal temperature and humidity range, it is essential to use a temperature and humidity-controlled environment, such as a clean room or a soldering area with air conditioning and dehumidification.
Dust and Contamination
Dust and contamination can affect the soldering process and the quality of the solder joints. Dust particles can settle on the PCB and components, preventing proper solder flow and causing poor solder joints. Contamination, such as oils and greases, can also prevent proper solder flow and cause weak solder joints.
To minimize dust and contamination, it is essential to:
- Use a clean room or a soldering area with air filtration
- Wear clean gloves and protective clothing
- Clean the PCB and components before soldering
- Use a solder fume extractor to remove solder fumes and debris
Common PCB Soldering Defects
Solder Bridges
Solder bridges are unintentional connections between adjacent pads or traces on the PCB. They can cause short circuits and prevent the device from functioning properly.
Common causes of solder bridges include:
- Excessive solder
- Incorrect soldering iron temperature
- Poor PCB design
To prevent solder bridges, it is essential to:
- Use the correct amount of solder
- Set the soldering iron temperature correctly
- Design the PCB with adequate spacing between pads and traces
- Use a magnifying glass or microscope to inspect the solder joints
Cold Solder Joints
Cold solder joints are weak and brittle solder joints that result from insufficient heat or poor solder flow. They can cause intermittent connections and prevent the device from functioning properly.
Common causes of cold solder joints include:
- Insufficient soldering iron temperature
- Incorrect solder alloy composition
- Poor PCB or component cleanliness
To prevent cold solder joints, it is essential to:
- Set the soldering iron temperature correctly
- Use high-quality solder with the correct alloy composition
- Clean the PCB and components before soldering
- Use a soldering iron with good thermal recovery
Tombstoning
Tombstoning is a defect that occurs when a surface-mount component stands on end instead of lying flat on the PCB. It can cause open circuits and prevent the device from functioning properly.
Common causes of tombstoning include:
- Uneven solder paste application
- Incorrect reflow oven temperature profile
- Poor component placement
To prevent tombstoning, it is essential to:
- Apply the solder paste evenly using a stencil or syringe
- Optimize the reflow oven temperature profile
- Use a pick-and-place machine or tweezers for component placement
- Use a PCB with solder mask to prevent solder from flowing onto adjacent pads
Frequently Asked Questions (FAQ)
1. What is the difference between lead-based and lead-free solder?
Lead-based solder contains a mixture of tin and lead, while lead-free solder contains a mixture of tin, silver, and copper. Lead-free solder has a higher melting point and requires higher soldering iron temperatures. It is also more prone to brittle solder joints and requires more precise temperature control.
2. How often should I replace my soldering iron tips?
The frequency of replacing soldering iron tips depends on the usage and the type of solder used. In general, it is recommended to replace the tips every 1-2 months for regular use and every 2-3 months for occasional use. If the tips become worn, damaged, or contaminated, they should be replaced immediately.
3. Can I use the same flux for all soldering applications?
No, different types of flux are suitable for different soldering applications. For example, rosin flux is commonly used for electronics soldering, while acid flux is used for plumbing and metal work. Using the wrong type of flux can cause poor solder joints, corrosion, and damage to the PCB and components.
4. How can I prevent solder bridges?
To prevent solder bridges, it is essential to use the correct amount of solder, set the soldering iron temperature correctly, and design the PCB with adequate spacing between pads and traces. Using a magnifying glass or microscope to inspect the solder joints can also help identify and correct solder bridges.
5. What is the ideal temperature and humidity range for soldering?
The ideal temperature and humidity range for soldering is 20-25°C (68-77°F) and 30-50% relative humidity. Maintaining the ideal range can help prevent oxidation, corrosion, poor solder flow, and weak solder joints.
Conclusion
PCB soldering is a critical process in the manufacturing of electronic devices. Poor soldering quality can lead to various issues, such as short circuits, open circuits, and intermittent connections, which can cause the device to malfunction or fail prematurely.
To ensure high-quality PCB soldering, it is essential to:
- Use the correct soldering techniques and equipment
- Choose high-quality soldering materials
- Maintain the ideal environmental conditions
- Prevent common soldering defects
By following the guidelines and best practices outlined in this article, manufacturers can improve the quality and reliability of their electronic devices and reduce the risk of costly repairs and recalls.
Leave a Reply