What is ENEPIG?
ENEPIG, short for Electroless Nickel Electroless Palladium Immersion Gold, is a multi-layer surface finish that consists of three distinct layers:
-
Electroless Nickel (Ni): This layer acts as a barrier between the copper substrate and the subsequent layers, providing excellent corrosion resistance and a uniform surface for the palladium layer.
-
Electroless Palladium (Pd): The palladium layer serves as a solderable surface and prevents the diffusion of nickel into the gold layer, enhancing the finish’s thermal stability and durability.
-
Immersion Gold (Au): The thin gold layer provides excellent solderability, protects the palladium from oxidation, and improves the shelf life of the PCB.
ENEPIG offers several advantages, including:
- Excellent solderability
- Superior thermal stability
- Compatibility with fine-pitch components
- Resistance to multiple reflow cycles
- Extended shelf life
What is ENIG?
ENIG, which stands for Electroless Nickel Immersion Gold, is another popular surface finish that consists of two layers:
-
Electroless Nickel (Ni): Similar to ENEPIG, the nickel layer in ENIG provides a barrier between the copper substrate and the gold layer, offering corrosion resistance and a uniform surface.
-
Immersion Gold (Au): The gold layer in ENIG serves as a solderable surface, protects the nickel from oxidation, and enhances the PCB’s shelf life.
ENIG has its own set of advantages, such as:
- Good solderability
- Compatibility with a wide range of components
- Resistance to oxidation
- Relatively low cost compared to ENEPIG
Comparing ENEPIG and ENIG
To better understand the differences between ENEPIG and ENIG, let’s compare their properties and performance in various aspects:
Solderability
Both ENEPIG and ENIG offer good solderability, but ENEPIG has a slight edge due to the presence of the palladium layer. The palladium layer in ENEPIG provides a more consistent and reliable solderable surface, especially for fine-pitch components and high-density interconnects (HDI) designs.
Thermal Stability
ENEPIG exhibits superior thermal stability compared to ENIG. The palladium layer in ENEPIG acts as a barrier, preventing the diffusion of nickel into the gold layer during multiple reflow cycles. This stability ensures the integrity of the solder joint and reduces the risk of intermetallic compound (IMC) formation, which can lead to brittle and weak joints.
Durability
ENEPIG’s multi-layer structure provides better durability than ENIG. The palladium layer in ENEPIG enhances the finish’s resistance to wear, abrasion, and corrosion. This durability is particularly important for applications that require frequent handling or exposure to harsh environments.
Cost
ENIG is generally more cost-effective than ENEPIG. The additional palladium layer in ENEPIG adds to the overall cost of the surface finish. However, the cost difference between ENEPIG and ENIG has been reducing over the years due to advancements in the plating process and increased adoption of ENEPIG in the industry.
Compatibility
Both ENEPIG and ENIG are compatible with a wide range of components and assembly processes. However, ENEPIG’s compatibility with fine-pitch components and HDI designs gives it an advantage over ENIG in certain applications.
Here’s a table summarizing the comparison between ENEPIG and ENIG:
Property | ENEPIG | ENIG |
---|---|---|
Solderability | Excellent, especially for fine-pitch | Good |
Thermal Stability | Superior, prevents nickel diffusion | Good, but prone to nickel diffusion |
Durability | Excellent, resistant to wear and corrosion | Good |
Cost | Higher than ENIG | Lower than ENEPIG |
Compatibility | Excellent for fine-pitch and HDI | Good for general applications |
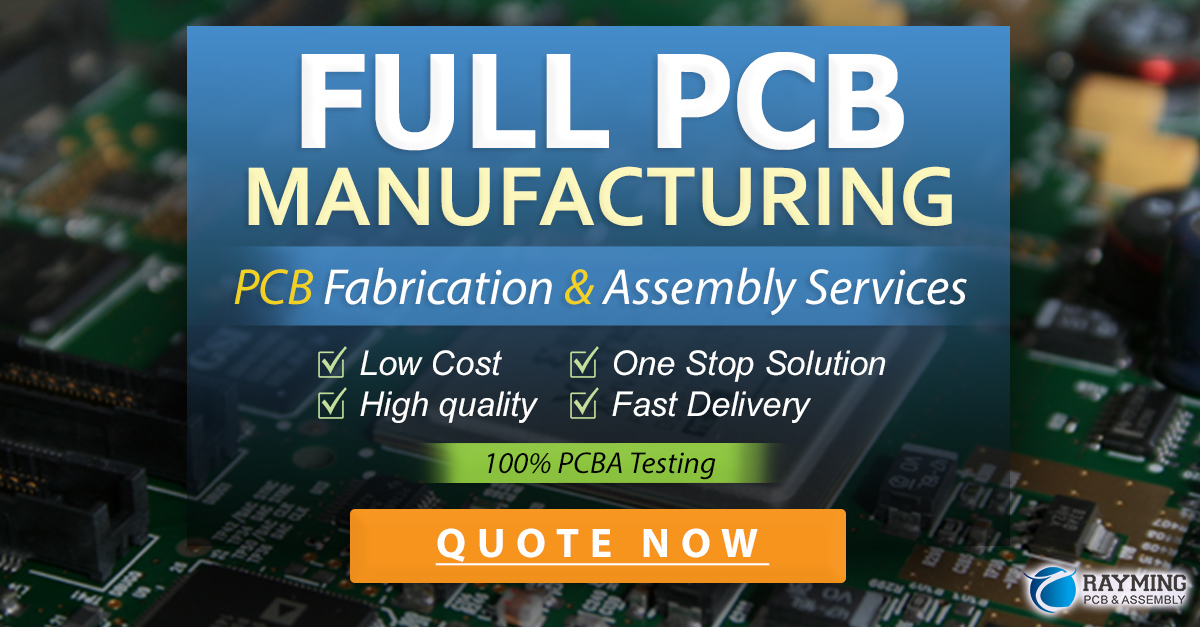
Choosing Between ENEPIG and ENIG
When deciding between ENEPIG and ENIG for your PCB surface finish, consider the following factors:
-
Application requirements: If your design involves fine-pitch components, HDI, or requires superior thermal stability and durability, ENEPIG might be the better choice. For general applications with less demanding requirements, ENIG can be a cost-effective option.
-
Cost considerations: ENIG is generally more affordable than ENEPIG. If cost is a primary concern and your application doesn’t require the advanced features of ENEPIG, ENIG may be the preferred choice.
-
Manufacturing capabilities: Ensure that your PCB manufacturer has the capability and expertise to apply the chosen surface finish consistently and reliably.
-
Industry standards and regulations: Some industries, such as automotive and aerospace, may have specific requirements or preferences for surface finishes. Always consult the relevant standards and regulations for your industry when selecting a surface finish.
FAQ
-
Q: Can ENEPIG be used for wire bonding?
A: Yes, ENEPIG is suitable for wire bonding applications. The palladium layer provides a stable surface for wire bonding, ensuring reliable connections. -
Q: Is ENIG suitable for high-temperature applications?
A: ENIG can be used for high-temperature applications, but it may not perform as well as ENEPIG due to the potential for nickel diffusion into the gold layer during multiple reflow cycles. -
Q: How does the shelf life of ENEPIG compare to ENIG?
A: ENEPIG generally offers a longer shelf life than ENIG. The palladium layer in ENEPIG provides better protection against oxidation, preserving the solderability of the finish for an extended period. -
Q: Can ENEPIG and ENIG be used together on the same PCB?
A: Yes, it is possible to use both ENEPIG and ENIG on the same PCB. This is called a “mixed finish” board, where different surface finishes are applied to specific areas based on their requirements. -
Q: Are there any environmental concerns associated with ENEPIG or ENIG?
A: Both ENEPIG and ENIG processes involve the use of chemicals that can have environmental impacts if not handled and disposed of properly. However, many PCB manufacturers have implemented eco-friendly practices and comply with environmental regulations to minimize these concerns.
Conclusion
ENEPIG and ENIG are both reliable and widely used surface finishes in the PCB industry. While ENEPIG offers superior solderability, thermal stability, and durability, ENIG remains a cost-effective option for general applications. When choosing between the two, it’s essential to consider your specific application requirements, cost constraints, manufacturing capabilities, and industry standards.
As technology advances and the demand for high-performance PCBs grows, it’s likely that ENEPIG will continue to gain popularity, especially in applications that require fine-pitch components, HDI designs, and enhanced reliability. However, ENIG will still have its place in the market, particularly for less demanding applications and cost-sensitive projects.
Ultimately, the choice between ENEPIG and ENIG depends on a careful evaluation of your project’s needs and priorities. By understanding the strengths and limitations of each surface finish, you can make an informed decision that ensures the success and reliability of your PCB Assembly.
Leave a Reply