Types of PCB Enclosures
1. Plastic Enclosures
Plastic enclosures are the most common type of PCB enclosure due to their versatility, cost-effectiveness, and ease of manufacturing. They are available in a wide range of sizes, shapes, and colors, making them suitable for various applications. Some popular types of plastic enclosures include:
a. ABS Enclosures
Acrylonitrile Butadiene Styrene (ABS) is a popular choice for PCB enclosures due to its strength, durability, and resistance to impact and chemicals. ABS enclosures are often used in consumer electronics, industrial controls, and medical devices.
b. Polycarbonate Enclosures
Polycarbonate (PC) enclosures offer excellent transparency, high impact resistance, and temperature stability. They are commonly used in applications that require visual inspection of the internal components or in harsh environments.
c. PVC Enclosures
Polyvinyl Chloride (PVC) enclosures are known for their low cost, good insulation properties, and resistance to chemicals and moisture. They are often used in electrical junction boxes and industrial control systems.
2. Metal Enclosures
Metal enclosures provide superior strength, durability, and electromagnetic interference (EMI) shielding compared to plastic enclosures. They are ideal for applications that require high levels of protection or where EMI shielding is crucial. Some common types of metal enclosures include:
a. Aluminum Enclosures
Aluminum enclosures are lightweight, corrosion-resistant, and offer good heat dissipation. They are frequently used in industrial, automotive, and aerospace applications.
b. Steel Enclosures
Steel enclosures offer the highest level of strength and durability among metal enclosures. They are often used in harsh industrial environments, outdoor applications, and where high levels of security are required.
c. Diecast Enclosures
Diecast enclosures, typically made from aluminum or zinc alloys, provide excellent EMI shielding and heat dissipation. They are commonly used in telecommunications, automotive, and industrial control applications.
3. 3D Printed Enclosures
3D printing technology has revolutionized the way we create prototypes and small series PCB enclosures. With 3D printing, designers can quickly and cost-effectively produce custom enclosures tailored to their specific requirements. Some popular 3D printing materials for PCB enclosures include:
a. PLA
Polylactic Acid (PLA) is a biodegradable thermoplastic derived from renewable resources like corn starch or sugarcane. It is easy to print with and offers good strength and surface finish.
b. ABS
ABS is a popular choice for 3D printed enclosures due to its strength, durability, and resistance to high temperatures. It can be easily post-processed and painted for improved aesthetics.
c. Nylon
Nylon is known for its high strength, flexibility, and durability. It is ideal for applications that require a combination of toughness and flexibility, such as snap-fit enclosures or living hinges.
Considerations When Choosing a PCB Enclosure
When selecting a PCB enclosure for your prototype or small series production, there are several key factors to consider:
1. Size and Shape
The size and shape of your PCB enclosure should accommodate your PCB and any additional components, such as connectors, switches, or displays. Consider the available space within the device and ensure that the enclosure allows for proper airflow and heat dissipation.
2. Environmental Factors
Consider the environment in which your device will operate. If it will be exposed to moisture, dust, or extreme temperatures, choose an enclosure material that can withstand these conditions. For outdoor applications, UV-resistant materials like polycarbonate or ABS with UV stabilizers are recommended.
3. EMI Shielding
If your device is sensitive to electromagnetic interference or needs to comply with EMC regulations, consider using a metal enclosure or a plastic enclosure with a conductive coating or EMI shielding gaskets.
4. Aesthetics and Branding
The appearance of your device can greatly impact its perceived value and user experience. Choose an enclosure material and color that aligns with your brand identity and the intended use of the device. Consider adding custom graphics, logos, or textures to enhance the visual appeal.
5. Manufacturing Process
The choice of enclosure material and design should also take into account the manufacturing process. For example, if you plan to use injection molding for mass production, ensure that your enclosure design is optimized for this process, with proper draft angles, wall thicknesses, and features like ribs and bosses.
Customizing PCB Enclosures
In some cases, off-the-shelf enclosures may not meet the specific requirements of your project. Customizing PCB enclosures allows you to create a unique design that perfectly fits your PCB and enhances the overall functionality and aesthetics of your device.
1. Custom Cutouts and Openings
Creating custom cutouts and openings in your enclosure allows you to accommodate connectors, switches, displays, or other components specific to your PCB. This can be done through CNC Machining, laser cutting, or 3D printing, depending on the enclosure material and the complexity of the design.
2. Surface Finishes and Coatings
Applying surface finishes or coatings to your PCB enclosure can enhance its appearance, durability, and functionality. Some common surface treatments include:
a. Powder Coating
Powder coating is a dry finishing process that involves applying a powdered polymer to the surface of the enclosure and then curing it under heat. This results in a durable, uniform, and attractive finish that can be customized in various colors and textures.
b. Anodizing
Anodizing is an electrochemical process that creates a protective oxide layer on the surface of aluminum enclosures. This layer enhances the corrosion resistance and durability of the enclosure while allowing for color customization.
c. Painting
Painting is a versatile and cost-effective way to customize the appearance of your PCB enclosure. It can be done using various techniques, such as spray painting, brush painting, or dip coating, depending on the desired finish and the enclosure material.
3. Custom Labeling and Branding
Adding custom labels, logos, or branding elements to your PCB enclosure can help to create a professional and cohesive look for your device. This can be achieved through various methods, such as:
a. Silk Screening
Silk screening is a printing technique that involves forcing ink through a fine mesh screen onto the surface of the enclosure. It is ideal for creating sharp, high-contrast graphics and text on flat or slightly curved surfaces.
b. Pad Printing
Pad printing is a versatile printing method that uses a silicone pad to transfer ink from a printing plate to the surface of the enclosure. It is suitable for printing on irregular or curved surfaces and can produce fine details and gradients.
c. Laser Engraving
Laser engraving uses a high-powered laser beam to create precise, permanent markings on the surface of the enclosure. It is ideal for creating durable, high-quality graphics and text on metal or plastic enclosures.
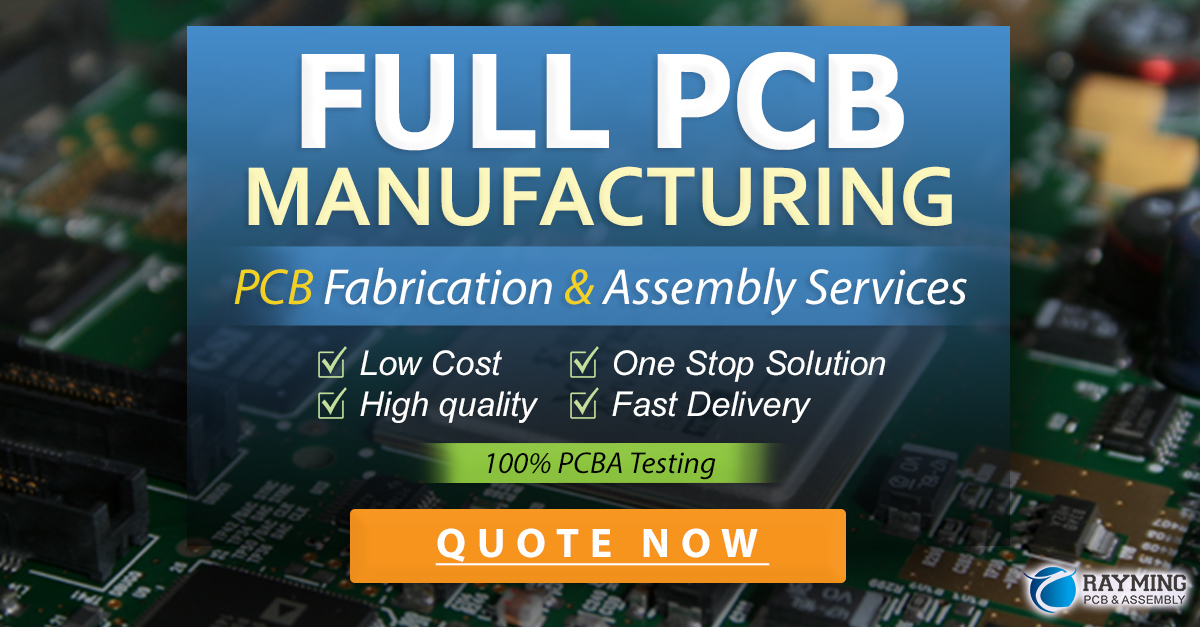
PCB Enclosure Standards and Certifications
When selecting a PCB enclosure, it is essential to consider relevant industry standards and certifications to ensure that your device meets the necessary requirements for safety, performance, and compatibility.
Some common standards and certifications for PCB enclosures include:
1. IP Rating
The Ingress Protection (IP) rating system classifies the level of protection provided by an enclosure against the intrusion of solid particles and liquids. A higher IP rating indicates better protection against environmental factors like dust and moisture.
2. NEMA Rating
The National Electrical Manufacturers Association (NEMA) rating system is used in North America to classify enclosures based on their ability to protect against environmental hazards such as corrosion, dust, oil, and coolants.
3. UL Certification
Underwriters Laboratories (UL) is a global safety certification company that tests and certifies products, including PCB enclosures, to ensure they meet specific safety standards. UL certification is often required for electrical devices sold in North America.
4. RoHS Compliance
The Restriction of Hazardous Substances (RoHS) directive restricts the use of certain hazardous substances in electrical and electronic equipment. Ensuring that your PCB enclosure is RoHS compliant helps to minimize the environmental impact of your device and comply with international regulations.
FAQ
1. What is the most cost-effective PCB enclosure material for prototypes?
3D printed enclosures using materials like PLA or ABS are often the most cost-effective option for prototypes and small series production. They offer quick turnaround times, low setup costs, and the ability to create custom designs without the need for expensive tooling.
2. How can I ensure that my PCB enclosure provides adequate EMI shielding?
To ensure adequate EMI shielding, consider using a metal enclosure, such as aluminum or steel, or a plastic enclosure with a conductive coating or EMI shielding gaskets. Additionally, ensure that any openings or seams in the enclosure are properly sealed to prevent EMI leakage.
3. Can I use 3D printed enclosures for outdoor applications?
While 3D printed enclosures can be used for outdoor applications, it is essential to choose a material that can withstand UV exposure and environmental factors like moisture and temperature fluctuations. Materials like ASA (Acrylonitrile Styrene Acrylate) or PETG (Polyethylene Terephthalate Glycol) are more suitable for outdoor use compared to standard PLA or ABS.
4. How do I determine the appropriate size for my PCB enclosure?
To determine the appropriate size for your PCB enclosure, consider the dimensions of your PCB, including any additional components like connectors, switches, or displays. Allow for some extra space around the PCB for proper airflow and ease of assembly. If using an off-the-shelf enclosure, refer to the manufacturer’s specifications and compare them with your PCB dimensions.
5. Can I customize the appearance of my PCB enclosure without compromising its performance?
Yes, there are various methods to customize the appearance of your PCB enclosure without compromising its performance. These include surface finishes like powder coating, anodizing, or painting, as well as custom labeling and branding techniques like silk screening, pad printing, or laser engraving. When applying any surface treatments or modifications, ensure that they do not interfere with the enclosure’s ability to provide the necessary protection and shielding for your PCB.
Conclusion
Selecting the right enclosure for your prototype or small series PCB is a critical aspect of the design process. By considering factors such as size, environmental protection, EMI shielding, aesthetics, and manufacturing processes, you can create a device that is functional, reliable, and visually appealing.
With the wide range of enclosure materials and customization options available, from traditional plastic and metal enclosures to cutting-edge 3D printed solutions, designers have the flexibility to create unique enclosures that perfectly fit their PCB and meet the specific requirements of their project.
By understanding the various enclosure standards and certifications, such as IP ratings, NEMA ratings, UL certification, and RoHS compliance, designers can ensure that their devices meet the necessary safety and performance requirements for their intended market.
As technology continues to evolve, so will the options for PCB enclosures. Staying informed about the latest materials, manufacturing processes, and design trends will help you make the best choices for your future projects, ensuring that your devices are well-protected, functional, and ready to make a lasting impression on your target audience.
Enclosure Material | Advantages | Disadvantages |
---|---|---|
ABS Plastic | Strong, durable, and resistant to impact and chemicals | Limited temperature range, not suitable for outdoor use without UV stabilizers |
Polycarbonate | Excellent transparency, high impact resistance, and temperature stability | More expensive than ABS, can scratch easily |
PVC | Low cost, good insulation properties, and resistant to chemicals and moisture | Limited temperature range, lower strength compared to ABS or polycarbonate |
Aluminum | Lightweight, corrosion-resistant, and good heat dissipation | More expensive than plastic, may require additional processing for EMI shielding |
Steel | Highest level of strength and durability among metal enclosures | Heavy, prone to corrosion without proper coating or plating |
3D Printed (PLA) | Biodegradable, easy to print, and good strength and surface finish | Limited temperature resistance, lower durability compared to ABS |
3D Printed (ABS) | Strong, durable, and resistant to high temperatures | Requires a heated print bed, may warp during printing |
3D Printed (Nylon) | High strength, flexibility, and durability | More difficult to print compared to PLA or ABS, requires a heated print bed and enclosed chamber |
Leave a Reply