What is Electronics Manufacturing?
Electronics manufacturing is the process of designing, fabricating, testing, and assembling electronic components and systems. It encompasses a wide range of products, from simple circuit boards to complex electronic devices used in various industries, such as consumer electronics, automotive, aerospace, medical, and telecommunications.
Key Components of Electronics Manufacturing
- Printed Circuit Boards (PCBs)
- Integrated Circuits (ICs)
- Capacitors
- Resistors
- Inductors
- Transistors
- Diodes
- Connectors
- Switches
- Sensors
History of Electronics Manufacturing
The history of electronics manufacturing can be traced back to the early 20th century, with the invention of the vacuum tube and the development of radio technology. However, the industry truly began to take shape in the 1940s and 1950s, with the introduction of the transistor and the integrated circuit.
Timeline of Electronics Manufacturing
Year | Milestone |
---|---|
1906 | First vacuum tube invented by Lee De Forest |
1947 | Transistor invented at Bell Labs |
1958 | Integrated circuit invented by Jack Kilby and Robert Noyce |
1960s | Development of surface mount technology (SMT) |
1970s | Introduction of microprocessors |
1980s | Advent of computer-aided design (CAD) and computer-aided manufacturing (CAM) |
1990s | Outsourcing of electronics manufacturing to Asia |
2000s | Miniaturization and increased complexity of electronic devices |
2010s | Growth of Internet of Things (IoT) and wearable technology |
Electronics Manufacturing Processes
Electronics manufacturing involves several processes, each critical to ensuring the quality and reliability of the final product.
Design and Prototyping
The first step in electronics manufacturing is the design and prototyping phase. This involves creating a schematic diagram of the electronic circuit, selecting components, and designing the PCB layout. Prototypes are then built and tested to ensure functionality and identify any potential issues.
PCB Fabrication
Once the design is finalized, the next step is PCB fabrication. This process involves creating a copper pattern on a non-conductive substrate, typically made of fiberglass or ceramic. The copper pattern is etched using a photolithographic process, and holes are drilled for component placement.
Component Placement
After the PCB is fabricated, electronic components are placed on the board using automated pick-and-place machines. These machines use computer vision and robotic arms to accurately place components at high speeds.
Soldering
Once the components are placed, they are soldered to the PCB using either through-hole or surface mount technology (SMT). Through-hole soldering involves inserting component leads through holes in the PCB and soldering them on the opposite side. SMT, on the other hand, involves placing components directly on the surface of the PCB and soldering them using a reflow oven.
Testing and Inspection
After soldering, the assembled PCBs undergo rigorous testing and inspection to ensure they meet the required specifications. This may include visual inspection, automated optical inspection (AOI), X-ray inspection, and functional testing.
Packaging and Shipping
Finally, the finished electronic products are packaged and shipped to the customer. Packaging must be designed to protect the products from damage during transportation and storage.
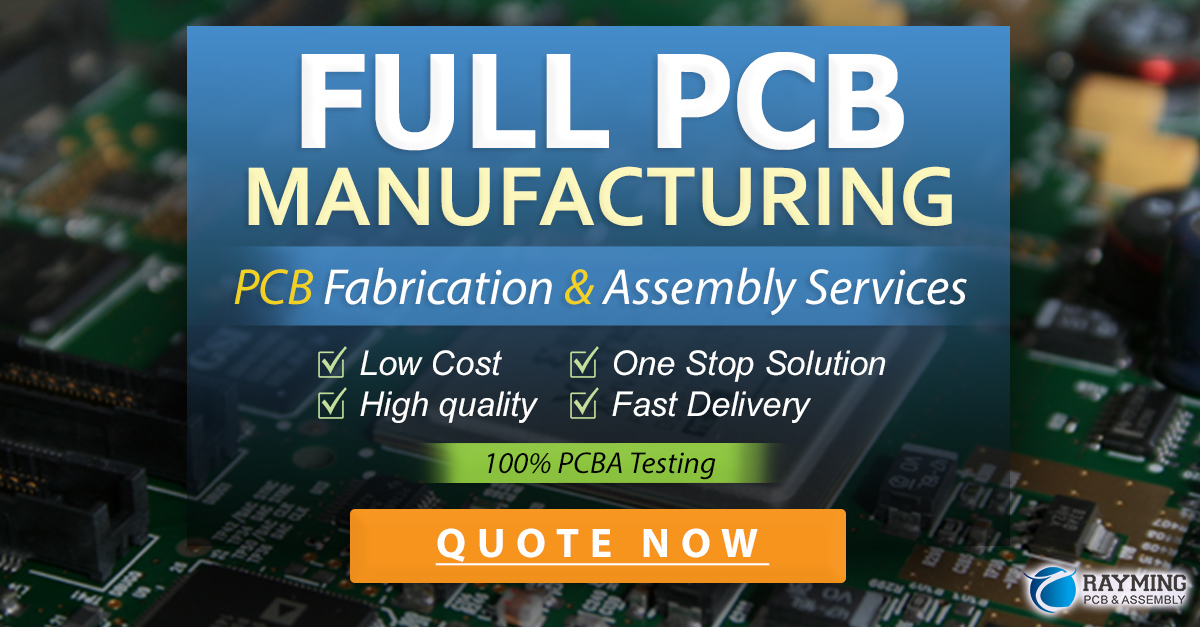
Challenges in Electronics Manufacturing
Despite the advancements in technology and processes, electronics manufacturing still faces several challenges.
Miniaturization
As electronic devices become smaller and more complex, manufacturing processes must adapt to handle the increased precision and accuracy required. This often involves investing in new equipment and training personnel.
Supply Chain Management
Electronics manufacturing relies on a complex global supply chain, with components sourced from multiple suppliers across different countries. Managing this supply chain can be challenging, particularly in times of disruption, such as natural disasters or geopolitical events.
Skilled Labor Shortage
The electronics manufacturing industry requires a highly skilled workforce, including engineers, technicians, and operators. However, many countries face a shortage of skilled labor, particularly in the areas of science, technology, engineering, and mathematics (STEM).
Environmental Regulations
Electronics manufacturing involves the use of hazardous materials, such as lead and other heavy metals. As environmental regulations become more stringent, manufacturers must invest in eco-friendly materials and processes to comply with these regulations.
Future Trends in Electronics Manufacturing
The electronics manufacturing industry is constantly evolving, driven by advancements in technology and changing consumer demands.
Industry 4.0
Industry 4.0, also known as the Fourth Industrial Revolution, involves the integration of advanced technologies, such as artificial intelligence (AI), robotics, and the Internet of Things (IoT), into manufacturing processes. This is expected to lead to increased automation, efficiency, and flexibility in electronics manufacturing.
5G and IoT
The rollout of 5G networks and the growth of the IoT are expected to drive demand for new electronic devices and components. This will create new opportunities for electronics manufacturers, particularly in the areas of sensors, connectivity, and edge computing.
Sustainable Manufacturing
As consumers become more environmentally conscious, there is growing demand for sustainable and eco-friendly electronic products. This is driving the adoption of sustainable manufacturing practices, such as the use of renewable energy, recycled materials, and closed-loop supply chains.
FAQ
- What is the difference between EMS and OEM?
-
EMS (Electronics Manufacturing Services) companies provide manufacturing services to OEMs (Original Equipment Manufacturers). OEMs design and sell their own products, while EMS companies manufacture products on behalf of OEMs.
-
What is the role of automation in electronics manufacturing?
-
Automation plays a critical role in electronics manufacturing, enabling faster, more precise, and more efficient production processes. Automated equipment, such as pick-and-place machines and reflow ovens, are used to place components and solder them to PCBs.
-
What are the benefits of outsourcing electronics manufacturing?
-
Outsourcing electronics manufacturing can provide several benefits, including cost savings, access to specialized expertise and equipment, and increased flexibility and scalability. It can also allow companies to focus on their core competencies, such as product design and marketing.
-
What are the key considerations when selecting an electronics manufacturing partner?
-
When selecting an electronics manufacturing partner, key considerations include technical capabilities, quality management systems, supply chain management, cost, and location. It is also important to consider the partner’s experience in the specific industry or application area.
-
What is the future outlook for the electronics manufacturing industry?
- The future outlook for the electronics manufacturing industry is positive, driven by the growing demand for electronic devices and the adoption of advanced technologies, such as 5G, IoT, and AI. However, the industry also faces challenges, such as increasing competition, supply chain disruptions, and skilled labor shortages.
Conclusion
Electronics manufacturing is a complex and dynamic industry that plays a critical role in the production of electronic devices and components. From design and prototyping to PCB fabrication, component placement, soldering, testing, and packaging, each step in the manufacturing process is essential to ensuring the quality and reliability of the final product.
As the industry continues to evolve, driven by advancements in technology and changing consumer demands, electronics manufacturers must adapt to stay competitive. This may involve investing in new equipment and processes, developing new skills and expertise, and forming strategic partnerships with suppliers and customers.
Despite the challenges, the future outlook for electronics manufacturing is bright, with opportunities for growth and innovation in areas such as Industry 4.0, 5G and IoT, and sustainable manufacturing. By staying at the forefront of these trends and delivering high-quality products and services, electronics manufacturers can position themselves for success in the years to come.
Leave a Reply