Introduction to Electronic Manufacturing
Electronic manufacturing is a rapidly evolving industry that plays a crucial role in the production of electronic devices and components. From smartphones and laptops to automotive electronics and medical devices, electronic manufacturing encompasses a wide range of products and technologies. In this article, we will explore nine key points of knowledge that shed light on the development and current state of the electronic manufacturing industry.
1. The Global Market for Electronic Manufacturing
1.1 Market Size and Growth
The global electronic manufacturing market has experienced significant growth in recent years. According to a report by Grand View Research, the global electronic manufacturing services (EMS) market size was valued at USD 463.2 billion in 2020 and is expected to expand at a compound annual growth rate (CAGR) of 7.7% from 2021 to 2028.
Year | Market Size (USD Billion) |
---|---|
2020 | 463.2 |
2028 | 832.1 (projected) |
1.2 Key Players in the Industry
The electronic manufacturing industry is dominated by several key players, including:
- Foxconn (Hon Hai Precision Industry Co., Ltd.)
- Pegatron Corporation
- Flex Ltd.
- Jabil Inc.
- Sanmina Corporation
These companies offer a range of services, including printed circuit board (PCB) assembly, product design and engineering, supply chain management, and logistics.
2. Technological Advancements in Electronic Manufacturing
2.1 Surface Mount Technology (SMT)
Surface Mount Technology (SMT) has revolutionized the electronic manufacturing industry by enabling the production of smaller, more complex electronic devices. SMT involves mounting electronic components directly onto the surface of a PCB, allowing for higher component density and improved performance compared to through-hole technology.
2.2 Automation and Robotics
Automation and robotics have become increasingly prevalent in electronic manufacturing, improving efficiency, accuracy, and productivity. Automated assembly lines, pick-and-place machines, and robotic arms are used to perform tasks such as component placement, soldering, and inspection.
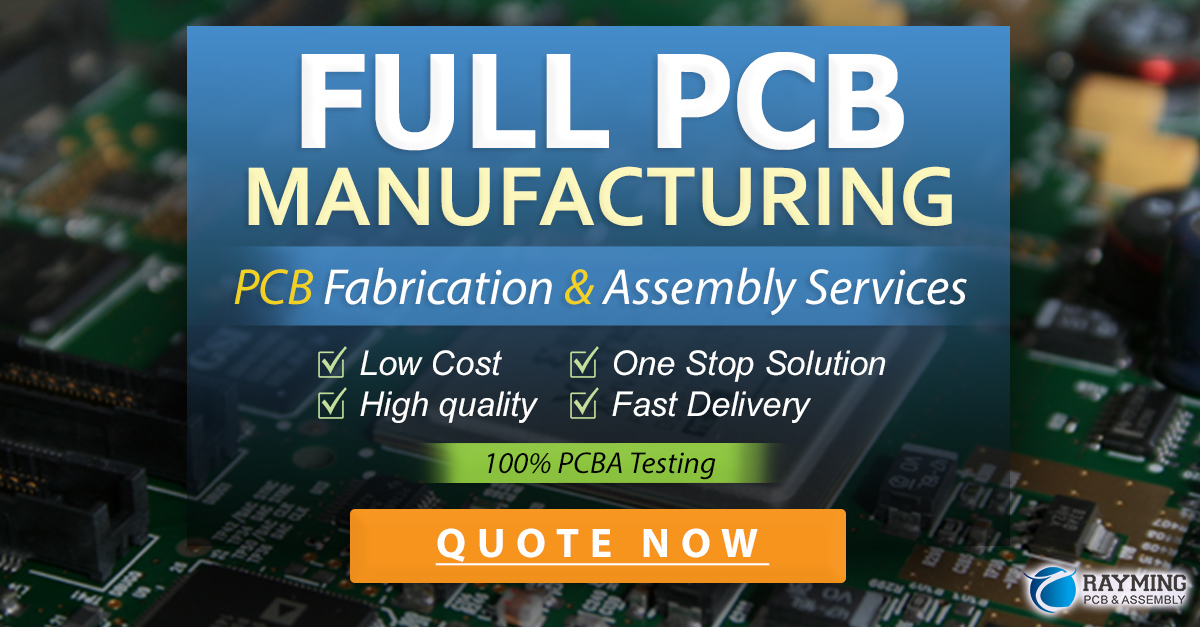
3. Supply Chain Management in Electronic Manufacturing
3.1 Global Supply Chain Networks
Electronic manufacturing relies on complex global supply chain networks to source raw materials, components, and subassemblies. Effective supply chain management is crucial for ensuring the timely delivery of high-quality products while minimizing costs and risks.
3.2 Just-in-Time (JIT) Manufacturing
Just-in-Time (JIT) manufacturing is a production strategy that aims to reduce inventory levels and improve efficiency by delivering materials and components only when they are needed in the manufacturing process. JIT manufacturing requires close collaboration between manufacturers and suppliers to ensure seamless integration and timely delivery.
4. Quality Control and Testing in Electronic Manufacturing
4.1 Quality Management Systems (QMS)
Quality Management Systems (QMS) are essential for ensuring the consistent production of high-quality electronic products. Manufacturers often adhere to international standards such as ISO 9001 and IATF 16949 to demonstrate their commitment to quality and continuous improvement.
4.2 Testing and Inspection Techniques
Electronic manufacturers employ various testing and inspection techniques to identify defects and ensure product reliability. These techniques include:
- In-Circuit Testing (ICT)
- Functional Testing
- Boundary Scan Testing
- X-Ray Inspection
- Automated Optical Inspection (AOI)
5. Environmental Considerations in Electronic Manufacturing
5.1 RoHS and REACH Compliance
The Restriction of Hazardous Substances (RoHS) directive and the Registration, Evaluation, Authorization, and Restriction of Chemicals (REACH) regulation are two key environmental regulations that impact electronic manufacturing. These regulations restrict the use of certain hazardous substances in electronic products and require manufacturers to ensure compliance throughout their supply chains.
5.2 E-Waste Management
Electronic waste (e-waste) is a growing concern in the electronic manufacturing industry. Proper e-waste management, including recycling and safe disposal of end-of-life products, is essential for minimizing the environmental impact of electronic manufacturing.
6. Printed Circuit Board (PCB) Manufacturing
6.1 PCB Design and Layout
PCB design and layout are critical aspects of electronic manufacturing. PCB designers use specialized software tools to create schematics and layouts that optimize performance, reliability, and manufacturability.
6.2 PCB Fabrication Processes
PCB fabrication involves several key processes, including:
- Copper Clad Laminate (CCL) Production
- Drilling and Plating
- Etching and Patterning
- Solder Mask and Silkscreen Application
- Surface Finishing
7. Outsourcing and Contract Manufacturing
7.1 Electronic Manufacturing Services (EMS)
Electronic Manufacturing Services (EMS) providers offer a range of services to original equipment manufacturers (OEMs), including PCB Assembly, product design and engineering, testing, and logistics. Outsourcing to EMS providers allows OEMs to focus on their core competencies while benefiting from the expertise and economies of scale offered by specialized manufacturers.
7.2 Choosing an EMS Provider
When selecting an EMS provider, OEMs should consider factors such as:
- Technical capabilities and experience
- Quality management systems and certifications
- Financial stability and scalability
- Intellectual property (IP) protection
- Geographic location and logistics capabilities
8. Industry 4.0 and Smart Manufacturing
8.1 Internet of Things (IoT) in Electronic Manufacturing
The Internet of Things (IoT) is transforming electronic manufacturing by enabling the integration of connected devices, sensors, and analytics throughout the production process. IoT technologies allow for real-time monitoring, predictive maintenance, and optimization of manufacturing operations.
8.2 Data Analytics and Artificial Intelligence (AI)
Data analytics and Artificial Intelligence (AI) are increasingly being applied in electronic manufacturing to improve efficiency, quality, and decision-making. By analyzing vast amounts of data collected from manufacturing processes, AI algorithms can identify patterns, detect anomalies, and optimize production parameters.
9. Future Trends and Challenges in Electronic Manufacturing
9.1 Miniaturization and High-Density Interconnect (HDI)
The demand for smaller, more compact electronic devices is driving the trend towards miniaturization and High-Density Interconnect (HDI) in electronic manufacturing. HDI PCBs feature finer pitch components, smaller vias, and higher layer counts, enabling the production of more complex and high-performance devices.
9.2 Sustainable and Eco-Friendly Manufacturing
As environmental concerns continue to grow, electronic manufacturers are increasingly focusing on sustainable and eco-friendly manufacturing practices. This includes the use of renewable energy, the adoption of circular economy principles, and the development of biodegradable and recyclable materials.
Frequently Asked Questions (FAQ)
-
What is the difference between through-hole and surface mount technology (SMT) in electronic manufacturing?
Through-hole technology involves inserting component leads through holes drilled in a PCB and soldering them on the opposite side, while SMT involves mounting components directly onto the surface of the PCB. SMT allows for higher component density and improved performance compared to through-hole technology. -
What are some common testing and inspection techniques used in electronic manufacturing?
Common testing and inspection techniques in electronic manufacturing include In-Circuit Testing (ICT), Functional Testing, Boundary Scan Testing, X-Ray Inspection, and Automated Optical Inspection (AOI). These techniques help identify defects and ensure product reliability. -
What are the benefits of outsourcing to an Electronic Manufacturing Services (EMS) provider?
Outsourcing to an EMS provider allows original equipment manufacturers (OEMs) to focus on their core competencies while benefiting from the expertise and economies of scale offered by specialized manufacturers. EMS providers offer a range of services, including PCB assembly, product design and engineering, testing, and logistics. -
How is the Internet of Things (IoT) transforming electronic manufacturing?
The Internet of Things (IoT) is transforming electronic manufacturing by enabling the integration of connected devices, sensors, and analytics throughout the production process. IoT technologies allow for real-time monitoring, predictive maintenance, and optimization of manufacturing operations, leading to improved efficiency and quality. -
What are some future trends in electronic manufacturing?
Some future trends in electronic manufacturing include miniaturization and High-Density Interconnect (HDI), which enable the production of smaller, more complex devices, and sustainable and eco-friendly manufacturing practices, such as the use of renewable energy, the adoption of circular economy principles, and the development of biodegradable and recyclable materials.
Conclusion
The electronic manufacturing industry is a dynamic and rapidly evolving sector that plays a crucial role in the production of a wide range of electronic devices and components. By understanding the key points of knowledge discussed in this article, including market trends, technological advancements, supply chain management, quality control, environmental considerations, PCB manufacturing, outsourcing, Industry 4.0, and future trends, stakeholders can better navigate the complexities of this industry and position themselves for success in the years to come.
Leave a Reply