Introduction to PCB Conversion
Printed Circuit Board (PCB) design is a crucial aspect of electronic product development. Eagle, a popular PCB design software, allows designers to create high-quality PCB layouts. However, to manufacture the designed PCB, the Eagle .brd file needs to be converted into Gerber format, which is the industry standard for PCB fabrication. In this article, we will discuss the guidelines for converting Eagle .brd files to Gerber format, ensuring a smooth and error-free PCB conversion process.
Understanding Eagle and Gerber Formats
What is Eagle?
Eagle (Easily Applicable Graphical Layout Editor) is a powerful PCB design software developed by Autodesk. It provides a user-friendly interface for creating schematic diagrams and designing PCB layouts. Eagle supports a wide range of features, including multi-layer boards, advanced routing capabilities, and extensive component libraries.
What is Gerber Format?
Gerber format, also known as RS-274X, is the industry standard for describing PCB designs. It consists of a set of files that contain the necessary information for PCB fabrication, such as copper layers, solder mask, silkscreen, and drill data. Gerber files are ASCII text files that use a specific format to represent the PCB layout data.
Eagle .brd to Gerber Conversion Process
Step 1: Preparing the Eagle .brd File
Before converting the Eagle .brd file to Gerber format, it is essential to ensure that the PCB design is complete and error-free. Follow these tips to prepare your Eagle .brd file:
- Double-check the schematic diagram for any discrepancies or missing connections.
- Verify that all components are properly placed and oriented on the PCB layout.
- Ensure that the PCB dimensions and layer stackup are correctly defined.
- Run the Design Rule Check (DRC) to identify and resolve any design rule violations.
Step 2: Setting Up the Gerber Output
Eagle provides a built-in Gerber generation tool called the CAM Processor. To set up the Gerber output:
- Open the Eagle .brd file and select “File” > “CAM Processor” from the menu.
- In the CAM Processor window, select “File” > “Open” and choose the appropriate CAM job file (e.g., gerb274x.cam) for Gerber output.
- Customize the output settings according to your PCB manufacturer’s requirements, such as file naming conventions and aperture settings.
Step 3: Generating Gerber Files
With the CAM Processor set up, you can now generate the Gerber files:
- In the CAM Processor window, click on the “Process Job” button to start the Gerber File Generation.
- Eagle will create a set of Gerber files, typically including the following:
- Top and bottom copper layers (.gtl and .gbl)
- Solder mask layers (.gts and .gbs)
- Silkscreen layers (.gto and .gbo)
- Drill data (.drl)
- Review the generated Gerber files to ensure they are complete and error-free.
Step 4: Verifying Gerber Files
Before sending the Gerber files to the PCB manufacturer, it is crucial to verify their integrity. Use a Gerber viewer software to visually inspect the generated files. Some popular Gerber viewers include:
- GC-Prevue
- ViewMate
- Gerbv
When verifying the Gerber files, check for the following:
- All layers are present and correctly aligned.
- Drill holes are properly positioned and sized.
- Copper features and traces are accurately represented.
- Solder mask and silkscreen layers are correctly generated.
Step 5: Sending Gerber Files to PCB Manufacturer
Once you have verified the Gerber files, package them together (usually in a ZIP file) and send them to your chosen PCB manufacturer. Provide any additional instructions or requirements, such as PCB thickness, surface finish, and desired quantities.
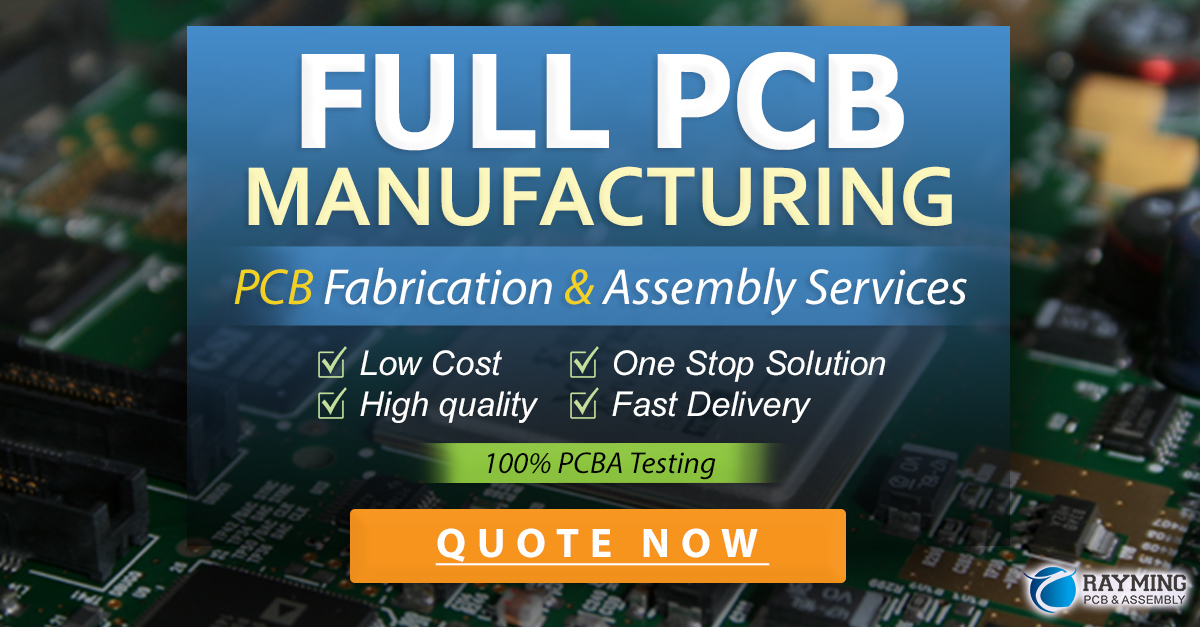
Best Practices for Eagle to Gerber Conversion
To ensure a smooth and successful Eagle to Gerber conversion, follow these best practices:
-
Use a consistent naming convention: Establish a clear and consistent naming convention for your Gerber files. This helps in identifying the different layers and avoids confusion during the manufacturing process.
-
Maintain proper clearances: Ensure that your PCB design maintains the necessary clearances between components, traces, and copper features. Consult your PCB manufacturer’s design guidelines for recommended clearance values.
-
Select appropriate trace widths: Choose trace widths that are suitable for your PCB’s current-carrying requirements and manufacturing capabilities. Wider traces are better for high-current paths, while narrower traces allow for denser routing.
-
Optimize component placement: Arrange components on the PCB layout in a way that minimizes the length of traces and reduces signal integrity issues. Consider factors such as heat dissipation and mechanical constraints when placing components.
-
Use solder mask and silkscreen effectively: Solder mask helps in protecting the PCB from oxidation and prevents short circuits. Silkscreen provides useful information for assembly and debugging. Ensure that the solder mask and silkscreen layers are correctly designed and generated in the Gerber files.
Troubleshooting Common Issues
Despite following the guidelines, you may encounter some common issues during the Eagle to Gerber conversion process. Here are a few troubleshooting tips:
Missing or Incorrect Layers
If certain layers are missing or incorrectly generated in the Gerber files, double-check the CAM Processor settings. Ensure that all required layers are selected and properly mapped to the corresponding Gerber file extensions.
Incorrect Aperture Settings
Aperture settings define the shape and size of the copper features on the PCB. If the aperture settings are incorrect, it can lead to manufacturing issues. Consult your PCB manufacturer’s guidelines for recommended aperture settings and adjust them accordingly in the CAM Processor.
Design Rule Violations
If the PCB design contains design rule violations, such as insufficient clearances or overlapping components, the Gerber files may not accurately represent the intended design. Run the Design Rule Check (DRC) in Eagle and resolve any violations before generating the Gerber files.
Incompatible File Format
Some PCB manufacturers may require specific file formats or variations of the Gerber format. Ensure that you are generating the Gerber files in the format specified by your manufacturer. If necessary, use a Gerber file editor to make any required modifications or conversions.
Frequently Asked Questions (FAQ)
- What is the difference between Eagle .brd and Gerber files?
-
Eagle .brd files are the native PCB design files created in the Eagle software. They contain the complete PCB layout information, including component placement, routing, and layer definitions. Gerber files, on the other hand, are industry-standard files used for PCB fabrication. They represent the individual layers of the PCB design in a format that can be understood by PCB manufacturers.
-
Can I use other PCB design software to generate Gerber files?
-
Yes, most PCB design software packages have the capability to generate Gerber files. The specific steps and settings may vary depending on the software you are using. Consult the software’s documentation or user manual for instructions on generating Gerber files.
-
What should I do if my PCB manufacturer reports issues with the Gerber files?
-
If your PCB manufacturer reports issues with the Gerber files, first verify that you have followed their specific guidelines and requirements. Double-check the Gerber files using a Gerber viewer to ensure they are correctly generated. If the issue persists, communicate with your manufacturer to identify the specific problem and work together to resolve it.
-
How can I ensure the best quality of my PCB when converting from Eagle to Gerber?
-
To ensure the best quality of your PCB, follow the best practices mentioned earlier, such as maintaining proper clearances, selecting appropriate trace widths, and optimizing component placement. Additionally, thoroughly review and verify the Gerber files before sending them to the manufacturer. Consider using a Gerber file analyzer tool to check for any potential issues or manufacturing constraints.
-
Can I include additional information, such as assembly instructions, in the Gerber files?
- Gerber files are primarily used for PCB fabrication and do not include assembly instructions. However, you can provide assembly instructions or other relevant information separately to your PCB manufacturer. This can be done through email communication or by including additional files (e.g., assembly drawings, bill of materials) along with the Gerber files.
Conclusion
Converting Eagle .brd files to Gerber format is a critical step in the PCB manufacturing process. By following the guidelines outlined in this article, you can ensure a smooth and accurate conversion. Remember to prepare your Eagle design files properly, set up the CAM Processor correctly, generate and verify the Gerber files, and communicate clearly with your PCB manufacturer.
By adhering to best practices and troubleshooting common issues, you can minimize the chances of encountering problems during the PCB fabrication process. With the right approach and attention to detail, you can successfully convert your Eagle PCB designs into high-quality Gerber files ready for manufacturing.
Step | Description |
---|---|
1 | Preparing the Eagle .brd File |
2 | Setting Up the Gerber Output |
3 | Generating Gerber Files |
4 | Verifying Gerber Files |
5 | Sending Gerber Files to PCB Manufacturer |
Remember, effective communication with your PCB manufacturer is key to achieving the desired results. Provide them with clear instructions, specifications, and any additional files or information they may require. By working closely with your manufacturer and following the Eagle to Gerber conversion guidelines, you can bring your PCB designs to life with confidence and reliability.
Leave a Reply