What are Drag Chain Cables?
Drag chain cables are specialized cable management systems designed to protect and guide cables, hoses, and other conduits in applications where there is repetitive linear motion. These systems consist of interconnected links or segments that form a continuous, flexible chain. The cables and hoses are safely housed within the chain, which moves along with the attached machine parts, such as gantries, cranes, or robotic arms.
The primary purpose of drag chain cables is to prevent damage to the cables and hoses caused by constant movement, friction, and exposure to harsh environments. By keeping the cables and hoses organized and protected, drag chain cables help maintain the reliability and longevity of the entire system.
Applications of Drag Chain Cables
Drag chain cables find applications in a wide range of industries and machinery. Some common applications include:
-
Machine Tools: Drag chain cables are extensively used in machine tools, such as CNC machines, to protect power cables, data cables, and hydraulic or pneumatic hoses that supply the moving parts of the machine.
-
Automation Systems: In automated manufacturing and assembly lines, drag chain cables are employed to manage the cables and hoses connecting various components, such as robotic arms, conveyor systems, and pick-and-place machines.
-
Material Handling: Drag chain cables are crucial in material handling equipment, such as overhead cranes, gantry systems, and storage and retrieval systems, to ensure the safe and reliable operation of the moving parts.
-
Packaging Machinery: In packaging machines, drag chain cables protect the cables and hoses that supply power, data, and media to the moving parts involved in filling, sealing, and labeling processes.
-
Medical Equipment: Drag chain cables are used in medical devices and equipment, such as X-ray machines and surgical robots, to manage the cables and hoses connected to the moving components while maintaining a clean and safe environment.
Benefits of Using Drag Chain Cables
Implementing drag chain cables in your application offers several key benefits:
-
Cable Protection: Drag chain cables provide excellent protection for cables and hoses against damage caused by constant movement, friction, and exposure to harsh environments. This protection helps extend the life of the cables and minimizes downtime due to cable failures.
-
Improved Reliability: By keeping cables and hoses organized and protected, drag chain cables contribute to the overall reliability of the system. This is particularly important in critical applications where downtime can lead to significant losses in productivity and revenue.
-
Enhanced Safety: Drag chain cables help prevent accidents caused by loose or damaged cables and hoses. By keeping the cables contained and guided, the risk of tripping hazards or entanglement with moving parts is greatly reduced, creating a safer working environment.
-
Increased Flexibility: Drag chain cables are designed to be flexible and adaptable to various motion requirements. They can accommodate different travel lengths, speeds, and acceleration rates, making them suitable for a wide range of applications.
-
Space Optimization: By organizing and guiding cables and hoses, drag chain cables help optimize the use of space in the machine or system. This is particularly beneficial in applications where space is limited, such as in compact machines or in areas with high cable density.
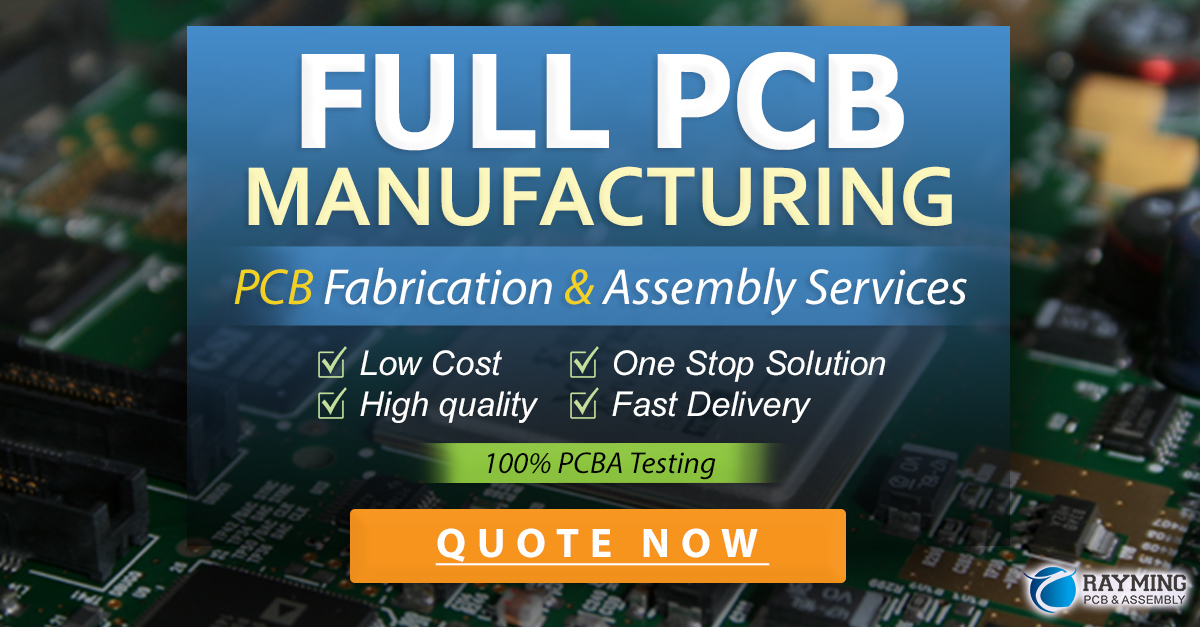
Types of Drag Chain Cables
Drag chain cables come in various types and configurations to suit different application requirements. Some common types include:
Plastic Drag Chain Cables
Plastic drag chain cables are lightweight, cost-effective, and suitable for applications with moderate loads and speeds. They are made from high-quality plastics, such as polyamide (PA) or polyoxymethylene (POM), which offer good resistance to wear, abrasion, and chemicals. Plastic drag chain cables are available in different sizes and configurations to accommodate various cable and hose diameters.
Steel Drag Chain Cables
Steel drag chain cables are designed for heavy-duty applications that require higher load capacities, longer travel lengths, and resistance to extreme environments. They are made from high-grade steel alloys and feature robust construction to withstand the demands of harsh industrial conditions. Steel drag chain cables are available in different sizes and configurations, including open and closed designs, to suit specific application needs.
Hybrid Drag Chain Cables
Hybrid drag chain cables combine the benefits of both plastic and steel materials. They typically feature a steel frame for strength and stability, with plastic crossbars and side plates for lightweight and low-noise operation. Hybrid drag chain cables offer a balance between the cost-effectiveness of plastic and the durability of steel, making them suitable for a wide range of applications.
Specialized Drag Chain Cables
In addition to the standard types, there are specialized drag chain cables designed for specific requirements, such as:
-
High-Speed Drag Chain Cables: These cables are optimized for applications with high travel speeds and acceleration rates, featuring low-friction designs and materials to minimize wear and noise.
-
High-Flexibility Drag Chain Cables: These cables are designed for applications that require tight bending radii or complex motion profiles, featuring highly flexible materials and construction.
-
Extreme Temperature Drag Chain Cables: These cables are designed to withstand extreme temperature conditions, either high or low, using materials and components suitable for the specific temperature range.
Selecting the Right Drag Chain Cable
When choosing a drag chain cable for your application, consider the following factors:
-
Application Requirements: Evaluate the specific requirements of your application, such as travel length, speed, acceleration, load capacity, and environmental conditions (e.g., temperature, humidity, chemical exposure).
-
Cable and Hose Specifications: Consider the types, sizes, and quantities of cables and hoses that need to be accommodated within the drag chain. Ensure that the selected drag chain cable has sufficient space and support for the required cables and hoses.
-
Material Compatibility: Choose a drag chain cable material that is compatible with the cables and hoses being used, as well as the environmental conditions. Consider factors such as abrasion resistance, chemical resistance, and temperature stability.
-
Installation and Maintenance: Evaluate the ease of installation and maintenance of the drag chain cable system. Look for features such as quick-release links, modular designs, and accessible cable entry points to simplify installation and maintenance tasks.
-
Cost and Lifecycle: Consider the initial cost of the drag chain cable system, as well as the total cost of ownership over its lifecycle. Factor in aspects such as durability, maintenance requirements, and potential downtime costs when making your selection.
Best Practices for Installing and Maintaining Drag Chain Cables
To ensure optimal performance and longevity of your drag chain cable system, follow these best practices for installation and maintenance:
-
Proper Sizing: Select a drag chain cable with sufficient internal space to accommodate the cables and hoses without overcrowding. Allow for some extra space to facilitate cable movement and prevent pinching or damage.
-
Correct Installation: Follow the manufacturer’s guidelines for installing the drag chain cable system. Ensure that the chain is properly aligned, tensioned, and supported to prevent sagging or misalignment during operation.
-
Cable Arrangement: Arrange the cables and hoses within the drag chain in a manner that minimizes cross-over points and allows for smooth movement. Use cable separators or dividers to keep the cables organized and prevent tangling or rubbing.
-
Strain Relief: Implement proper strain relief techniques at the entry and exit points of the drag chain cable to prevent damage to the cables and hoses. Use strain relief clamps or connectors to secure the cables and distribute the stress evenly.
-
Regular Inspection: Conduct regular inspections of the drag chain cable system to identify any signs of wear, damage, or misalignment. Check for excessive debris accumulation, frayed cables, or damaged links, and address any issues promptly.
-
Lubrication: If recommended by the manufacturer, lubricate the drag chain cable system periodically to reduce friction and wear. Use the specified lubricant and follow the recommended application intervals.
-
Cable Management: Implement a cable management plan that includes proper cable routing, labeling, and documentation. This will facilitate easier maintenance, troubleshooting, and upgrades in the future.
Frequently Asked Questions (FAQ)
-
What is the difference between a drag chain cable and a cable carrier?
Drag chain cables and cable carriers are essentially the same things. Both terms refer to a flexible cable management system that protects and guides cables and hoses in applications with repetitive linear motion. -
Can drag chain cables be used for rotary motion applications?
While drag chain cables are primarily designed for linear motion applications, there are specialized rotary drag chain cables available for applications that involve rotary motion. These rotary drag chains are designed to accommodate the specific requirements of rotary movement, such as continuous rotation or limited angle rotation. -
How do I determine the required size of a drag chain cable for my application?
To determine the required size of a drag chain cable, you need to consider several factors, such as the number, size, and type of cables and hoses being used, the required travel length, speed, and acceleration of the application, and the environmental conditions. It is recommended to consult with the drag chain cable manufacturer or supplier to ensure proper sizing based on your specific application requirements. -
What is the maximum travel length that a drag chain cable can support?
The maximum travel length of a drag chain cable depends on various factors, such as the size and type of the chain, the load capacity, and the application requirements. Some drag chain cable systems can support travel lengths up to several hundred meters. However, for longer travel lengths, it is crucial to consider additional support mechanisms, such as intermediate supports or guide trays, to prevent sagging and ensure smooth operation. -
How often should I replace my drag chain cable system?
The replacement interval for a drag chain cable system depends on the specific application, operating conditions, and the level of wear and tear experienced by the system. Regular inspections should be conducted to assess the condition of the drag chain cable and identify any signs of wear, damage, or deterioration. The manufacturer’s guidelines and recommendations should be followed for the specific drag chain cable model being used. In general, a well-maintained drag chain cable system can last for several years, depending on the application demands.
Drag Chain Cable Type | Typical Applications | Key Features |
---|---|---|
Plastic | Light to medium-duty applications, moderate speeds and loads | Lightweight, cost-effective, good resistance to wear and chemicals |
Steel | Heavy-duty applications, high loads, long travel lengths, extreme environments | Robust construction, high load capacity, suitable for harsh conditions |
Hybrid | Applications requiring a balance between cost-effectiveness and durability | Combination of steel frame for strength and plastic components for lightweight design |
High-Speed | Applications with high travel speeds and acceleration rates | Low-friction design and materials to minimize wear and noise |
High-Flexibility | Applications requiring tight bending radii or complex motion profiles | Highly flexible materials and construction for improved flexibility |
Extreme Temperature | Applications exposed to extreme high or low temperature conditions | Materials and components suitable for specific temperature ranges |
Conclusion
Drag chain cables are essential components in various industrial applications that involve moving parts and require reliable protection for cables and hoses. By providing a flexible and durable cable management solution, drag chain cables help prevent damage to cables and hoses, improve system reliability, enhance safety, and optimize space utilization.
When selecting a drag chain cable for your application, it is crucial to consider factors such as application requirements, cable and hose specifications, material compatibility, installation and maintenance aspects, and cost-effectiveness. By following best practices for installation and maintenance, you can ensure optimal performance and longevity of your drag chain cable system.
As technology advances and industrial applications evolve, drag chain cables continue to play a vital role in enabling the smooth and reliable operation of moving machinery. With a wide range of types, configurations, and specialized designs available, there is a drag chain cable solution suitable for virtually any application requirement.
By understanding the importance of drag chain cables and selecting the right solution for your specific needs, you can enhance the performance, reliability, and safety of your industrial applications, ultimately contributing to increased productivity and profitability.
Leave a Reply