Introduction to Differential trace impedance
Differential trace impedance is a crucial aspect of high-speed PCB design, especially in applications involving differential signaling. It refers to the characteristic impedance of a pair of traces that carry differential signals. Maintaining a consistent and controlled differential impedance is essential for ensuring signal integrity, minimizing reflections, and reducing electromagnetic interference (EMI).
Traditionally, differential trace impedance is calculated and controlled with the presence of a reference plane, such as a ground or power plane, beneath the differential traces. The reference plane provides a return path for the current and helps in maintaining a stable impedance profile. However, in certain scenarios, such as in flex circuits or when the reference plane is not continuous, designing differential traces without a reference plane becomes necessary.
In this article, we will explore the concept of differential trace impedance without a reference plane, discuss the challenges involved, and provide guidelines for designing and managing differential traces in such situations.
Understanding Differential Signaling
Before delving into differential trace impedance without a reference plane, let’s first understand the basics of differential signaling.
What is Differential Signaling?
Differential signaling is a method of transmitting signals using two complementary signal lines, known as a differential pair. The two lines carry signals that are equal in magnitude but opposite in polarity. The receiver detects the difference between the two signals, rather than their absolute values, to interpret the transmitted data.
Differential signaling offers several advantages over single-ended signaling:
- Noise immunity: Differential signals are less susceptible to common-mode noise, as any noise induced on both lines tends to cancel out at the receiver.
- Reduced EMI: The complementary nature of differential signals results in lower electromagnetic radiation compared to single-ended signals.
- Higher data rates: Differential signaling allows for higher data rates due to its noise immunity and reduced crosstalk.
Importance of Differential Impedance Matching
To ensure proper functioning of differential signaling, it is crucial to maintain a consistent differential impedance along the length of the differential pair. Impedance mismatches can lead to signal reflections, which can cause signal integrity issues, such as ringing, overshoot, and undershoot.
The differential impedance of a trace pair is determined by several factors, including the trace width, trace spacing, dielectric thickness, and dielectric constant of the PCB material. By carefully controlling these parameters, designers can achieve the desired differential impedance and minimize impedance discontinuities.
Challenges of Differential Trace Impedance Without Reference Plane
Designing differential traces without a reference plane presents unique challenges compared to the traditional approach with a solid reference plane. Let’s explore these challenges in detail.
Lack of Controlled Impedance Environment
The absence of a reference plane beneath the differential traces creates an uncontrolled impedance environment. In a typical PCB Stackup, the reference plane acts as a ground or power plane and provides a consistent reference for the differential traces. It helps in maintaining a stable impedance profile and provides a low-impedance return path for the differential current.
Without a reference plane, the impedance of the differential traces becomes more susceptible to variations in the surrounding environment. The coupling between the traces and nearby conductors, such as other traces or components, can influence the differential impedance. This lack of control makes it challenging to achieve and maintain a target impedance value.
Increased Sensitivity to Trace Geometry
In the absence of a reference plane, the differential impedance becomes more sensitive to the trace geometry. Factors such as trace width, trace spacing, and trace thickness have a more significant impact on the impedance when there is no reference plane to provide a stable environment.
Slight variations in the trace geometry can lead to impedance mismatches and discontinuities. Maintaining precise control over the trace dimensions becomes critical to ensure a consistent differential impedance along the length of the traces.
Reduced Coupling between Differential Traces
The presence of a reference plane enhances the coupling between the differential traces. The reference plane helps in confining the electromagnetic fields between the traces and the plane, leading to tighter coupling and better signal integrity.
Without a reference plane, the coupling between the differential traces is reduced. The electromagnetic fields are not confined, and the traces may have increased interaction with other nearby conductors. This reduced coupling can affect the differential impedance and signal quality.
Increased Susceptibility to External Influences
Differential traces without a reference plane are more susceptible to external influences, such as nearby conductors, components, and even air gaps. These external factors can introduce impedance discontinuities and affect the differential impedance profile.
For example, if the differential traces pass over a void or gap in the PCB substrate, the impedance can change abruptly at that location. Similarly, the proximity of other conductors or components can introduce capacitive or inductive coupling, altering the differential impedance.
Limited Applicability of Standard Impedance Calculation Methods
Standard impedance calculation methods, such as the microstrip or stripline formulas, assume the presence of a reference plane. These methods rely on the geometry and properties of the trace, dielectric, and reference plane to calculate the characteristic impedance.
Without a reference plane, these standard calculation methods may not accurately predict the differential impedance. The absence of a well-defined return path and the increased influence of external factors make it challenging to apply traditional impedance calculation techniques.
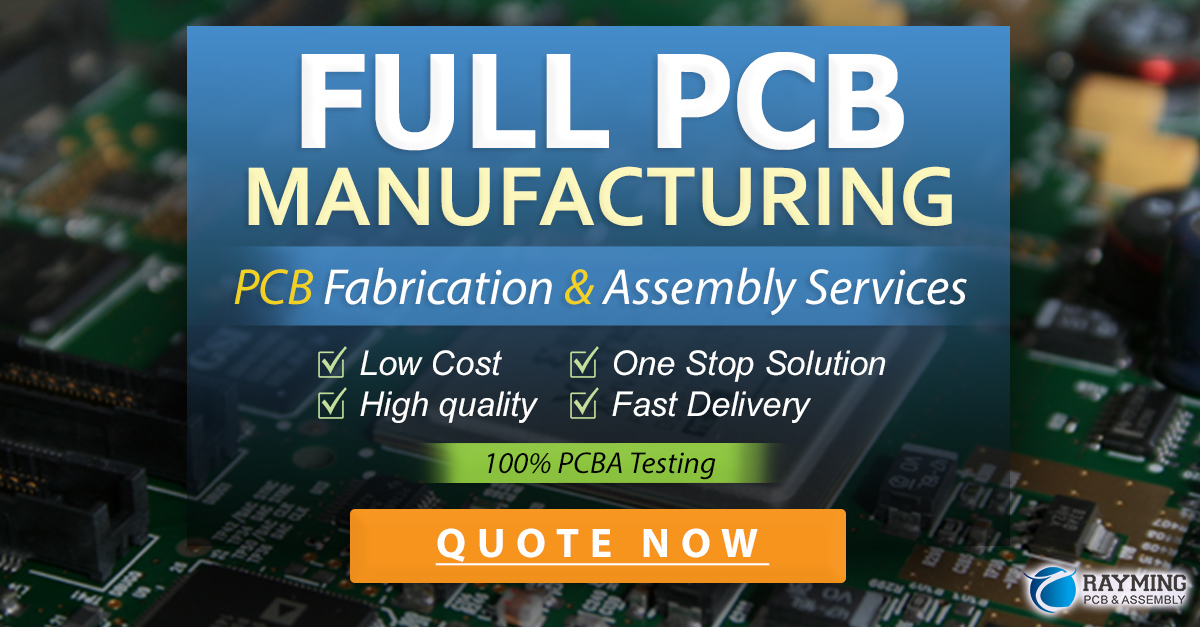
Design Guidelines for Differential Traces Without Reference Plane
Despite the challenges, it is possible to design differential traces without a reference plane while maintaining good signal integrity. Here are some design guidelines to consider:
Minimize Trace Length
When designing differential traces without a reference plane, it is important to keep the trace length as short as possible. Longer traces are more susceptible to impedance variations and external influences. By minimizing the trace length, you can reduce the impact of these factors on the differential impedance.
Maintain Symmetry
Symmetry is crucial in differential trace design, especially in the absence of a reference plane. Ensure that the differential traces are symmetrical in terms of their geometry, spacing, and routing. Any asymmetry can introduce impedance mismatches and degrade signal quality.
Maintain equal trace lengths for the differential pair to avoid Phase Differences and ensure proper signal propagation. Use serpentine routing or length matching techniques to equalize the trace lengths if necessary.
Control Trace Geometry
Pay close attention to the trace geometry when designing differential traces without a reference plane. The trace width, spacing, and thickness play a significant role in determining the differential impedance.
Use impedance calculation tools or field solvers to determine the appropriate trace dimensions for your target impedance. Keep in mind that the absence of a reference plane may require adjustments to the trace geometry compared to standard calculations.
Maintain consistent trace width and spacing along the length of the differential pair. Avoid abrupt changes in trace geometry, as they can introduce impedance discontinuities.
Use Differential Vias
When transitioning differential traces between layers, use differential vias to maintain signal integrity. Differential vias are pairs of vias that carry the differential signals between layers while maintaining the differential impedance.
Ensure that the differential vias are properly spaced and sized to match the impedance of the differential traces. Avoid stubs or unused via pads, as they can introduce impedance discontinuities.
Provide Shielding
In the absence of a reference plane, providing shielding for the differential traces can help in reducing external influences and improving signal integrity. Shielding can be achieved through various techniques, such as:
- Coplanar shielding: Place ground traces or planes adjacent to the differential traces on the same layer to provide shielding and reduce coupling to nearby conductors.
- Microstrip shielding: If possible, route the differential traces on an outer layer and place a ground plane on the adjacent layer to provide shielding.
- Stripline shielding: If the differential traces are routed on an inner layer, consider using ground planes on the layers above and below the traces to create a stripline-like environment.
Shielding helps in confining the electromagnetic fields and reduces the impact of external factors on the differential impedance.
Minimize Discontinuities
Avoid introducing discontinuities along the differential trace path. Discontinuities can occur due to vias, layer transitions, or changes in trace geometry. Each discontinuity introduces impedance mismatches and can affect signal quality.
Minimize the number of vias and layer transitions in the differential trace route. If unavoidable, ensure proper impedance matching and provide adequate clearance around the discontinuities.
Perform Simulations and Measurements
Given the challenges of designing differential traces without a reference plane, it is important to perform simulations and measurements to validate the design.
Use electromagnetic simulation tools to model the differential traces and analyze their impedance profile. Simulations can help in identifying impedance variations and discontinuities.
Perform measurements on prototypes or test coupons to verify the actual differential impedance. Time-domain reflectometry (TDR) and vector network analyzer (VNA) measurements can provide insights into the impedance characteristics and help in identifying any issues.
Based on the simulation and measurement results, make necessary adjustments to the design to optimize the differential impedance and signal integrity.
Frequently Asked Questions (FAQ)
-
Q: Why is differential trace impedance important in high-speed PCB design?
A: Differential trace impedance is crucial in high-speed PCB design because it ensures proper signal propagation and minimizes signal integrity issues. Maintaining a consistent and controlled differential impedance helps in reducing reflections, minimizing crosstalk, and improving noise immunity. -
Q: What challenges arise when designing differential traces without a reference plane?
A: Designing differential traces without a reference plane presents challenges such as the lack of a controlled impedance environment, increased sensitivity to trace geometry, reduced coupling between differential traces, increased susceptibility to external influences, and limited applicability of standard impedance calculation methods. -
Q: How can I minimize the impact of external influences on differential traces without a reference plane?
A: To minimize the impact of external influences on differential traces without a reference plane, you can follow guidelines such as minimizing trace length, maintaining symmetry, controlling trace geometry, using differential vias, providing shielding, and minimizing discontinuities along the trace path. -
Q: What techniques can be used to provide shielding for differential traces without a reference plane?
A: Techniques for providing shielding for differential traces without a reference plane include coplanar shielding (placing ground traces or planes adjacent to the differential traces), microstrip shielding (routing differential traces on an outer layer with a ground plane on the adjacent layer), and stripline shielding (routing differential traces on an inner layer with ground planes above and below). -
Q: How can I validate the differential impedance of traces without a reference plane?
A: To validate the differential impedance of traces without a reference plane, you can perform electromagnetic simulations using specialized tools to model the traces and analyze their impedance profile. Additionally, performing measurements on prototypes or test coupons using time-domain reflectometry (TDR) or vector network analyzer (VNA) can provide insights into the actual impedance characteristics.
Conclusion
Designing differential traces without a reference plane presents unique challenges in terms of maintaining a consistent and controlled differential impedance. The absence of a reference plane creates an uncontrolled impedance environment, increases sensitivity to trace geometry, reduces coupling between differential traces, and makes the traces more susceptible to external influences.
To mitigate these challenges and ensure good signal integrity, designers can follow guidelines such as minimizing trace length, maintaining symmetry, controlling trace geometry, using differential vias, providing shielding, and minimizing discontinuities. Performing simulations and measurements is also crucial to validate the differential impedance and make necessary adjustments to the design.
By carefully considering these factors and applying appropriate design techniques, it is possible to successfully design differential traces without a reference plane while maintaining acceptable signal integrity and performance. However, it is important to recognize the limitations and trade-offs involved in such designs and to thoroughly validate the impedance characteristics through simulations and measurements.
As high-speed digital systems continue to push the boundaries of PCB design, understanding and effectively managing differential trace impedance without a reference plane becomes increasingly important. By staying informed about the challenges and best practices, designers can navigate these complex design scenarios and ensure reliable and robust differential signaling in their PCB layouts.
Leave a Reply