What is Flexible PCB Coverlay?
Flexible PCB coverlay is a thin, insulating material that is laminated onto the surface of a flexible printed circuit board. Its primary purpose is to protect the exposed copper traces and pads from damage, corrosion, and short-circuiting. Coverlay also provides electrical insulation, mechanical support, and enhances the overall durability of the flexible PCB.
Key Properties of Flexible PCB Coverlay
To effectively serve its purpose, flexible PCB coverlay must possess specific properties that ensure optimal performance. These properties include:
-
Electrical Insulation: Coverlay materials must have excellent dielectric properties to prevent current leakage and short-circuiting between conductive elements.
-
Flexibility: The coverlay must be able to withstand repeated bending and flexing without cracking, delaminating, or losing its protective properties.
-
Adhesion: A strong bond between the coverlay and the flexible PCB surface is essential to maintain the integrity of the assembly and prevent delamination under stress.
-
Chemical Resistance: Coverlay materials should be resistant to common chemicals, solvents, and environmental factors to ensure long-term reliability.
-
Thermal Stability: The coverlay must be able to withstand the temperature ranges encountered during the manufacturing process and in the end-use application.
Types of Flexible PCB Coverlay Materials
Several materials are commonly used for flexible PCB coverlay, each with its unique set of properties and advantages. The choice of material depends on the specific requirements of the application, such as temperature range, flexibility, and cost. Some of the most popular flexible PCB coverlay materials include:
1. Polyimide (PI)
Polyimide is the most widely used coverlay material for flexible PCBs due to its excellent thermal stability, mechanical strength, and electrical insulation properties. It offers high resistance to chemicals, solvents, and moisture, making it suitable for demanding applications. Polyimide coverlay is available in various thicknesses and can be customized with additives to enhance specific properties.
2. Polyester (PET)
Polyester coverlay is a cost-effective alternative to polyimide, offering good electrical insulation and flexibility. It is commonly used in less demanding applications where high-temperature resistance is not a critical requirement. PET coverlay is available in clear and opaque versions and can be easily printed or laser-marked for identification purposes.
3. Flexible Solder mask (FSM)
Flexible solder mask is a photoimageable coverlay material that combines the functions of a traditional solder mask and a coverlay. FSM is applied using a photolithographic process, allowing for precise patterning and selective exposure of pads and openings. This material offers excellent electrical insulation, solderability, and resistance to harsh environments.
Coverlay Application Techniques
The process of applying coverlay to a flexible PCB involves several techniques, each with its advantages and limitations. The choice of application method depends on factors such as the coverlay material, the desired features, and the production volume. The most common coverlay application techniques include:
1. Lamination
Lamination is the most widely used method for applying coverlay to flexible PCBs. In this process, the coverlay material is placed on top of the flexible PCB, and the assembly is subjected to heat and pressure using a lamination press. The heat activates the adhesive on the coverlay, causing it to bond firmly to the PCB surface. Lamination ensures a uniform and reliable bond between the coverlay and the PCB.
2. Screen Printing
Screen printing is a cost-effective method for applying coverlay to flexible PCBs, particularly for low-volume production or prototyping. In this process, a screen with the desired coverlay pattern is used to deposit the coverlay material onto the PCB surface. The printed coverlay is then cured using heat or UV light to achieve a strong bond. Screen printing allows for selective application of coverlay and can accommodate complex patterns.
3. Photoimaging
Photoimaging is a precise and versatile method for applying coverlay to flexible PCBs. This process involves using a photoimageable coverlay material, such as flexible solder mask (FSM), which is exposed to UV light through a photomask. The exposed areas of the coverlay material undergo a chemical change, allowing them to be developed and removed, while the unexposed areas remain on the PCB surface. Photoimaging enables the creation of fine features, such as small openings and pads, with high accuracy.
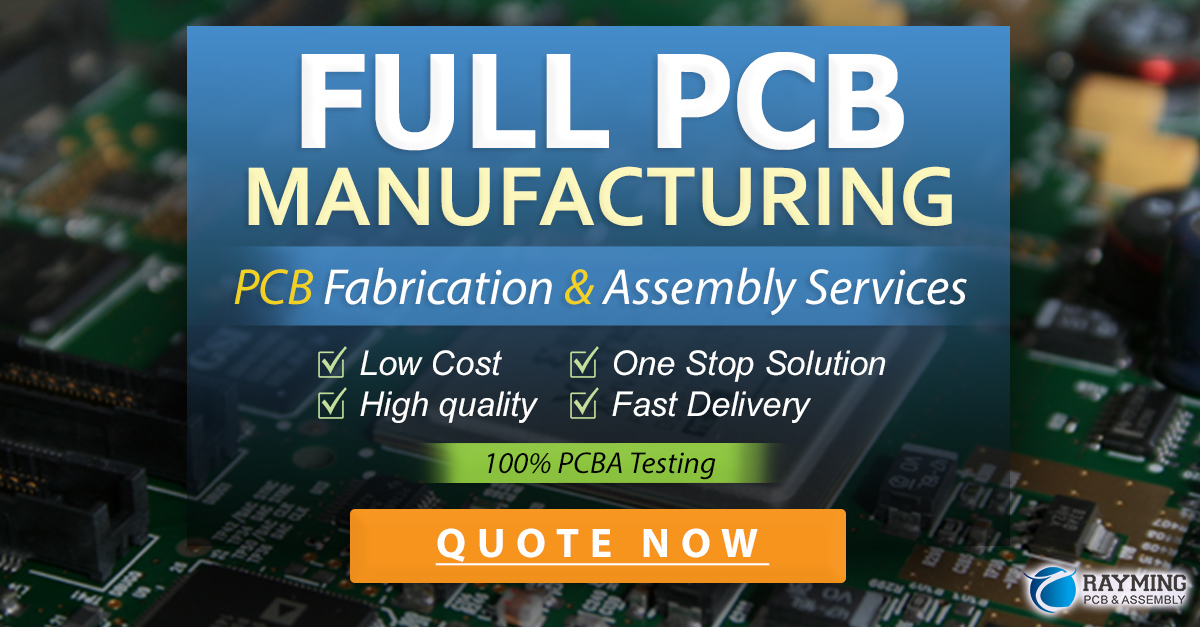
Design Considerations for Flexible PCB Coverlay
When designing a flexible PCB with coverlay, several factors must be considered to ensure optimal performance and reliability. These considerations include:
1. Coverlay Thickness
The thickness of the coverlay material should be selected based on the specific requirements of the application. Thicker coverlays provide better mechanical protection and insulation but may reduce flexibility and increase the overall thickness of the assembly. Thinner coverlays offer improved flexibility but may compromise on protection and durability. A balance must be struck between these factors to achieve the desired performance.
2. Adhesive Selection
The choice of adhesive used to bond the coverlay to the flexible PCB is crucial for ensuring a reliable and long-lasting assembly. The adhesive must be compatible with both the coverlay material and the PCB Substrate, and it should provide strong adhesion under the expected operating conditions. Factors such as temperature range, chemical resistance, and flexibility should be considered when selecting an adhesive.
3. Coverlay Openings and Features
Coverlay openings and features, such as access holes, vias, and exposed pads, must be carefully designed to ensure proper functionality and reliability. The size and placement of these features should take into account the limitations of the coverlay application process and the requirements of the end-use application. Adequate clearance must be provided around the openings to prevent damage to the coverlay material during assembly and use.
4. Bend Radius and Flexibility
The bend radius and flexibility of the coverlay material should be compatible with the intended application. The coverlay must be able to withstand the expected bending and flexing without cracking, delaminating, or losing its protective properties. The design of the flexible PCB should take into account the minimum bend radius specified for the selected coverlay material to ensure long-term reliability.
Applications of Flexible PCB Coverlay
Flexible PCB coverlay finds applications in a wide range of industries and products, where the benefits of flexibility, lightweight, and compact design are highly valued. Some of the most common applications include:
-
Wearable Electronics: Flexible PCBs with coverlay are extensively used in wearable devices, such as smartwatches, fitness trackers, and medical monitoring systems, where conformity to the human body and durability are essential.
-
Medical Devices: Coverlay-protected flexible PCBs are employed in various medical devices, including implantable electronics, diagnostic equipment, and patient monitoring systems, where reliability and biocompatibility are critical.
-
Automotive Electronics: Flexible PCBs with coverlay are used in automotive applications, such as instrument clusters, sensors, and infotainment systems, where space constraints and harsh environmental conditions are common.
-
Consumer Electronics: Coverlay-protected flexible PCBs are found in a wide range of consumer electronics, including smartphones, tablets, cameras, and gaming devices, where compact design and reliability are paramount.
-
Aerospace and Defense: Flexible PCBs with coverlay are used in aerospace and defense applications, such as avionics, surveillance systems, and military equipment, where weight reduction, high reliability, and resistance to extreme conditions are essential.
Advantages of Flexible PCB Coverlay
The use of coverlay in flexible PCBs offers several advantages that contribute to the overall performance and reliability of the end product. These advantages include:
-
Enhanced Protection: Coverlay provides a robust barrier against mechanical damage, environmental factors, and chemical exposure, ensuring the long-term reliability of the flexible PCB.
-
Improved Insulation: The dielectric properties of coverlay materials offer excellent electrical insulation, preventing short-circuits and current leakage between conductive elements.
-
Increased Durability: Coverlay-protected flexible PCBs can withstand repeated bending and flexing without compromising the integrity of the assembly, making them suitable for applications where high flexibility is required.
-
Compact Design: The use of coverlay enables the creation of compact and lightweight flexible PCB assemblies, which is crucial for applications where space and weight are limited.
-
Cost-Effective: Coverlay application techniques, such as lamination and screen printing, are cost-effective methods for protecting flexible PCBs, especially in high-volume production.
Challenges and Limitations
Despite the numerous advantages of flexible PCB coverlay, there are some challenges and limitations that must be considered:
-
Material Selection: Choosing the appropriate coverlay material for a specific application can be challenging, as each material has its own set of properties and limitations. Factors such as temperature range, chemical resistance, and flexibility must be carefully evaluated to ensure optimal performance.
-
Adhesion Issues: Achieving strong and reliable adhesion between the coverlay and the flexible PCB can be challenging, particularly in applications where high flexibility and harsh environmental conditions are encountered. Proper surface preparation and adhesive selection are crucial for ensuring a robust bond.
-
Limited Reworkability: Once the coverlay is applied to the flexible PCB, it can be difficult to rework or repair the assembly without damaging the coverlay material. This limitation highlights the importance of careful design and quality control during the manufacturing process.
-
Increased Thickness: The addition of coverlay to a flexible PCB increases the overall thickness of the assembly, which may be a concern in applications where ultra-thin profiles are required. Careful selection of coverlay thickness and material can help mitigate this issue.
Future Trends and Developments
As the demand for flexible electronics continues to grow, the development of advanced coverlay materials and application techniques is expected to drive innovation in the field of flexible PCBs. Some of the future trends and developments include:
-
High-Performance Materials: The development of new coverlay materials with enhanced properties, such as higher temperature resistance, improved flexibility, and better chemical resistance, will enable the use of flexible PCBs in increasingly demanding applications.
-
Eco-Friendly Solutions: The push towards sustainable and eco-friendly electronics will drive the development of biodegradable and recyclable coverlay materials, reducing the environmental impact of flexible PCBs.
-
Additive Manufacturing: The integration of additive manufacturing techniques, such as 3D printing, with coverlay application processes may enable the creation of complex and customized coverlay patterns, opening up new possibilities for flexible PCB design.
-
Sensor Integration: The incorporation of sensors and other electronic components into the coverlay material itself may lead to the development of smart coverlays that can monitor the health and performance of the flexible PCB in real-time.
Frequently Asked Questions (FAQ)
-
What is the purpose of coverlay in flexible PCBs?
Coverlay serves as a protective and insulating layer on the surface of flexible PCBs, shielding the exposed copper traces and pads from damage, corrosion, and short-circuiting. It also provides mechanical support and enhances the overall durability of the assembly. -
What are the most common materials used for flexible PCB coverlay?
The most common materials used for flexible PCB coverlay include polyimide (PI), polyester (PET), and flexible solder mask (FSM). Each material has its own set of properties and advantages, and the choice depends on the specific requirements of the application. -
How is coverlay applied to flexible PCBs?
Coverlay can be applied to flexible PCBs using various techniques, such as lamination, screen printing, and photoimaging. Lamination involves bonding the coverlay to the PCB surface using heat and pressure, while screen printing uses a patterned screen to deposit the coverlay material. Photoimaging employs a photoimageable coverlay material that is selectively exposed and developed to create the desired pattern. -
What factors should be considered when designing a flexible PCB with coverlay?
When designing a flexible PCB with coverlay, several factors must be considered, including coverlay thickness, adhesive selection, coverlay openings and features, and bend radius and flexibility. These factors should be carefully evaluated to ensure optimal performance and reliability of the end product. -
What are the future trends and developments in flexible PCB coverlay?
Future trends and developments in flexible PCB coverlay include the development of high-performance materials with enhanced properties, eco-friendly solutions, the integration of additive manufacturing techniques, and the incorporation of sensors and other electronic components into the coverlay material itself. These advancements are expected to drive innovation and expand the applications of flexible PCBs in various industries.
Conclusion
Flexible PCB coverlay plays a crucial role in protecting and enhancing the performance of flexible printed circuit boards. By providing electrical insulation, mechanical support, and environmental protection, coverlay ensures the long-term reliability and durability of flexible PCBs in a wide range of applications.
The selection of appropriate coverlay materials and application techniques is essential for achieving optimal results. Designers must carefully consider factors such as material properties, thickness, adhesive compatibility, and feature requirements to create reliable and high-performance flexible PCB assemblies.
As the demand for flexible electronics continues to grow, the development of advanced coverlay materials and application methods will drive innovation in the field of flexible PCBs. The integration of new technologies, such as additive manufacturing and sensor integration, will open up new possibilities for the design and functionality of flexible PCBs.
By understanding the intricacies of flexible PCB coverlay and staying up-to-date with the latest trends and developments, engineers and manufacturers can leverage the full potential of this essential component in creating cutting-edge flexible electronics for a wide range of industries and applications.
Leave a Reply