What is Coverlay Adhesive Squeezeout?
Coverlay adhesive squeezeout is a phenomenon that occurs during the manufacturing process of flexible printed circuits (FPCs). It refers to the excess adhesive material that is pushed out from under the coverlay film when it is laminated onto the FPC substrate. This squeezeout can cause various issues in the final product, such as contamination, reduced flexibility, and potential short circuits.
Causes of Coverlay Adhesive Squeezeout
Several factors can contribute to the occurrence of coverlay adhesive squeezeout:
- Excessive adhesive application: Applying too much adhesive during the lamination process can lead to squeezeout.
- Improper lamination pressure: If the lamination pressure is too high, it can force the adhesive out from under the coverlay film.
- Uneven substrate surface: An uneven or rough FPC substrate surface can cause adhesive to be displaced during lamination, resulting in squeezeout.
- Incorrect adhesive viscosity: Using an adhesive with an incorrect viscosity can make it more prone to squeezeout.
Impact of Coverlay Adhesive Squeezeout on FPC Performance
Coverlay adhesive squeezeout can have several negative effects on the performance and reliability of flexible printed circuits:
Contamination
Squeezeout adhesive can contaminate other areas of the FPC, such as conductors or solder pads. This contamination can lead to poor solderability, reduced electrical performance, and potential short circuits.
Reduced Flexibility
Excess adhesive on the surface of the FPC can harden and create a rigid layer, reducing the overall flexibility of the circuit. This can be particularly problematic for applications that require a high degree of flexibility, such as wearable electronics or dynamic flex applications.
Dimensional Instability
Adhesive squeezeout can alter the thickness and dimensions of the FPC, leading to dimensional instability. This can cause issues during assembly or when integrating the FPC into the final product.
Aesthetic Concerns
In some cases, coverlay adhesive squeezeout can be visible on the surface of the FPC, creating an unsightly appearance. This can be a concern for applications where aesthetics are important, such as consumer electronics.
Preventing Coverlay Adhesive Squeezeout
To minimize the occurrence of coverlay adhesive squeezeout, several preventive measures can be taken during the FPC manufacturing process:
Optimizing Adhesive Application
Ensuring that the correct amount of adhesive is applied to the FPC substrate is crucial in preventing squeezeout. This can be achieved through:
- Using precise dispensing equipment
- Implementing process controls to monitor adhesive application
- Regularly maintaining and calibrating dispensing equipment
Proper Lamination Process Control
Controlling the lamination process parameters can help reduce the risk of adhesive squeezeout:
- Adjusting lamination pressure to the optimal level
- Ensuring even pressure distribution across the FPC surface
- Monitoring and controlling lamination temperature
Substrate Surface Preparation
Proper preparation of the FPC substrate surface can help minimize adhesive squeezeout:
- Cleaning the substrate to remove contaminants
- Ensuring a smooth and even substrate surface
- Using surface treatments to improve adhesion
Adhesive Selection
Choosing the right adhesive for the specific application can help reduce the likelihood of squeezeout:
- Selecting an adhesive with the appropriate viscosity
- Considering the adhesive’s flow properties and cure characteristics
- Evaluating the compatibility of the adhesive with the coverlay material and substrate
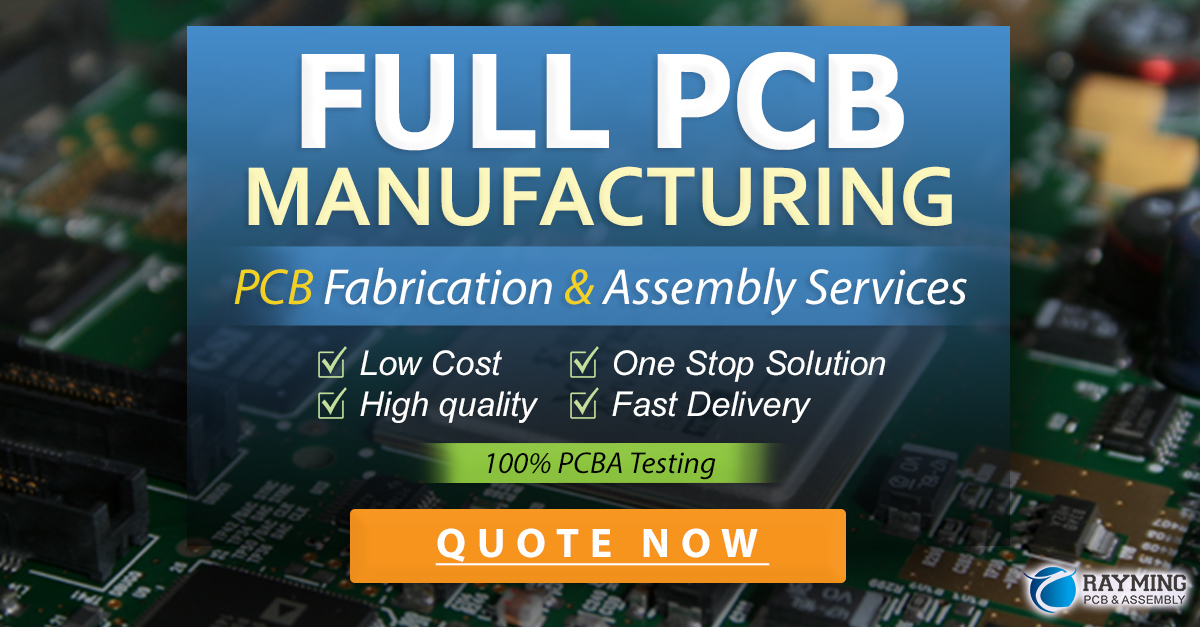
Detecting and Addressing Coverlay Adhesive Squeezeout
Despite preventive measures, coverlay adhesive squeezeout may still occur. Detecting and addressing squeezeout is essential to ensure the quality and reliability of the final FPC product.
Visual Inspection
Visual inspection is the most common method for detecting coverlay adhesive squeezeout. Inspectors should look for:
- Visible adhesive on the surface of the FPC
- Uneven or excessive adhesive around the edges of the coverlay
- Contamination of conductors or solder pads
Automated Optical Inspection (AOI)
Automated optical inspection systems can be used to detect coverlay adhesive squeezeout more efficiently and consistently than manual visual inspection. AOI systems use high-resolution cameras and image processing algorithms to identify squeezeout and other defects.
Addressing Squeezeout
When coverlay adhesive squeezeout is detected, several actions can be taken to address the issue:
- Cleaning: In some cases, the excess adhesive can be removed using solvents or mechanical cleaning methods. However, care must be taken not to damage the FPC or coverlay during the cleaning process.
- Rework: If the squeezeout is severe or cleaning is not feasible, the affected FPC may need to be reworked. This can involve removing the coverlay, cleaning the substrate, and reapplying the coverlay with the proper amount of adhesive.
- Scrap: In extreme cases where the squeezeout cannot be effectively addressed through cleaning or rework, the affected FPC may need to be scrapped and replaced.
Best Practices for Managing Coverlay Adhesive Squeezeout
To effectively manage coverlay adhesive squeezeout in FPC manufacturing, consider implementing the following best practices:
- Establish process controls: Implement process controls to monitor and maintain optimal parameters for adhesive application, lamination, and substrate preparation.
- Regularly maintain equipment: Ensure that dispensing equipment, lamination presses, and other machinery are regularly maintained and calibrated to prevent squeezeout-related issues.
- Train personnel: Provide training to personnel involved in FPC manufacturing to ensure they understand the causes, impacts, and prevention of coverlay adhesive squeezeout.
- Implement quality control measures: Establish quality control measures, such as visual inspection and AOI, to detect and address squeezeout promptly.
- Continuously improve processes: Regularly review and analyze squeezeout-related data to identify opportunities for process improvements and implement corrective actions.
Frequently Asked Questions (FAQ)
1. What is the difference between coverlay and solder mask in FPCs?
Coverlay and solder mask serve different purposes in flexible printed circuits:
- Coverlay is a protective insulating layer that is laminated onto the FPC substrate to protect the conductors and provide electrical insulation. It is typically made of polyimide or other flexible materials.
- Solder mask is a thin, heat-resistant coating applied to the FPC to protect the conductors from oxidation and prevent solder bridging during assembly. It also defines the areas where solder should be applied.
2. Can coverlay adhesive squeezeout cause short circuits in FPCs?
Yes, coverlay adhesive squeezeout can potentially cause short circuits in FPCs. If the excess adhesive contaminates adjacent conductors or solder pads, it can create an unintended electrical connection, leading to a short circuit.
3. How can the viscosity of the adhesive affect Coverlay squeezeout?
The viscosity of the adhesive can significantly impact the occurrence of coverlay squeezeout. An adhesive with a low viscosity may be more prone to squeezeout, as it can flow more easily under pressure during lamination. Conversely, an adhesive with a high viscosity may be less likely to squeeze out but may not provide adequate adhesion. Selecting an adhesive with the appropriate viscosity for the specific application is essential.
4. What are some common cleaning methods for removing coverlay adhesive squeezeout?
Common cleaning methods for removing coverlay adhesive squeezeout include:
- Solvent cleaning: Using solvents, such as isopropyl alcohol or acetone, to dissolve and remove the excess adhesive.
- Mechanical cleaning: Using tools, such as brushes or scrapers, to physically remove the squeezeout.
- Plasma cleaning: Using a plasma treatment to etch away the excess adhesive without damaging the FPC or coverlay.
5. How can automated optical inspection (AOI) help in detecting coverlay adhesive squeezeout?
Automated optical inspection (AOI) systems can help detect coverlay adhesive squeezeout more efficiently and consistently than manual visual inspection. AOI systems use high-resolution cameras and advanced image processing algorithms to identify squeezeout and other defects on the surface of the FPC. This allows manufacturers to quickly detect and address squeezeout issues, improving the overall quality and reliability of the final product.
Conclusion
Coverlay adhesive squeezeout is a common issue in the manufacturing of flexible printed circuits that can lead to various problems, such as contamination, reduced flexibility, and potential short circuits. By understanding the causes and impacts of squeezeout, implementing preventive measures, and establishing effective detection and addressing methods, manufacturers can minimize the occurrence of this issue and ensure the production of high-quality FPCs.
Implementing best practices, such as establishing process controls, regularly maintaining equipment, training personnel, and continuously improving processes, can help manage coverlay adhesive squeezeout effectively. As the demand for flexible electronics continues to grow, it is crucial for FPC manufacturers to prioritize the management of squeezeout to meet the increasing quality and reliability requirements of various industries.
Leave a Reply