Introduction to Copper Panels and Their Importance
Copper panels have become an essential component in various industries, including electronics, telecommunications, and construction. These panels are widely used due to their excellent electrical conductivity, thermal conductivity, and corrosion resistance properties. The distribution of copper on a panel plays a crucial role in determining its performance and reliability. In this article, we will explore the various aspects of copper distribution on a panel, including its manufacturing process, testing methods, and applications.
What is a Copper Panel?
A copper panel, also known as a copper clad laminate (CCL), is a composite material consisting of a layer of copper foil bonded to a dielectric substrate, such as fiberglass or epoxy resin. The copper layer is typically used for electrical connections and heat dissipation, while the substrate provides mechanical support and electrical insulation. Copper panels are available in various thicknesses, sizes, and configurations to suit different applications.
The Importance of Copper Distribution on a Panel
The distribution of copper on a panel is a critical factor in determining its electrical and thermal performance. A uniform and consistent copper distribution ensures optimal current carrying capacity, signal integrity, and heat dissipation. Any irregularities or defects in the copper layer can lead to issues such as high resistance, signal loss, and localized heating, which can compromise the reliability and longevity of the panel.
Manufacturing Process of Copper Panels
Substrate Preparation
The first step in manufacturing a copper panel is preparing the substrate material. The most common substrate materials used are fiberglass and epoxy resin. Fiberglass substrates are made by weaving glass fibers into a fabric and impregnating it with a resin. Epoxy resin substrates, on the other hand, are made by mixing epoxy resin with a hardener and curing it under controlled conditions.
Copper Foil Production
Copper foil used in copper panels is typically produced through an electrodeposition process. In this process, a thin layer of copper is deposited onto a rotating drum or a continuous belt from an electrolytic solution containing copper ions. The thickness of the copper foil can be controlled by adjusting the current density and the duration of the deposition process. The resulting copper foil is then cleaned, dried, and wound into rolls for further processing.
Bonding Copper Foil to Substrate
The copper foil is bonded to the prepared substrate using a lamination process. In this process, the copper foil and the substrate are stacked together and subjected to high temperature and pressure in a lamination press. The heat and pressure activate the adhesive properties of the substrate, causing it to bond with the copper foil. The lamination process ensures a strong and uniform bond between the copper layer and the substrate.
Patterning and Etching
After the lamination process, the copper panel undergoes patterning and etching to create the desired electrical circuits. The patterning process involves applying a photoresist layer onto the copper surface and exposing it to UV light through a photomask. The exposed areas of the photoresist become soluble and are removed during the development process, leaving a pattern of exposed copper. The exposed copper is then etched away using a chemical solution, leaving only the desired copper traces on the substrate.
Surface Finishing
The final step in the manufacturing process is surface finishing. This step involves applying a protective coating onto the copper surface to prevent oxidation and improve solderability. The most common surface finishes used are:
- Hot Air Solder Leveling (HASL): A thin layer of solder is applied onto the copper surface and leveled using hot air.
- Electroless Nickel Immersion Gold (ENIG): A layer of nickel is deposited onto the copper surface, followed by a thin layer of gold.
- Organic Solderability Preservative (OSP): A thin layer of organic compounds is applied onto the copper surface to prevent oxidation.
Testing Methods for Copper Distribution on a Panel
Visual Inspection
Visual inspection is the most basic method for testing copper distribution on a panel. This method involves examining the copper surface for any visible defects, such as pinholes, scratches, or discoloration. Visual inspection can be performed using the naked eye or with the aid of a microscope for higher magnification.
Thickness Measurement
The thickness of the copper layer is a critical parameter that affects the electrical and thermal performance of the panel. Thickness measurement can be performed using various methods, such as:
- Micrometer: A mechanical device that measures the thickness of the panel by applying a constant pressure between two anvils.
- X-ray Fluorescence (XRF): A non-destructive method that measures the thickness of the copper layer by analyzing the characteristic X-rays emitted by the copper atoms when excited by a primary X-ray source.
- Scanning Electron Microscope (SEM): A high-resolution imaging technique that can measure the thickness of the copper layer by analyzing the cross-section of the panel.
Method | Advantages | Disadvantages |
---|---|---|
Micrometer | Simple and inexpensive | Limited accuracy and precision |
XRF | Non-destructive and fast | Requires calibration standards |
SEM | High resolution and accuracy | Destructive and time-consuming |
Electrical Conductivity Test
The electrical conductivity of the copper layer is a critical parameter that affects the signal integrity and power handling capacity of the panel. Electrical conductivity can be tested using various methods, such as:
- Four-Point Probe: A method that measures the sheet resistance of the copper layer by applying a current through two outer probes and measuring the voltage drop across two inner probes.
- Eddy Current Testing: A non-destructive method that measures the electrical conductivity of the copper layer by inducing eddy currents in the copper and measuring the resulting magnetic field.
Adhesion Test
The adhesion between the copper layer and the substrate is essential for the mechanical and thermal stability of the panel. Adhesion can be tested using various methods, such as:
- Peel Test: A method that measures the force required to peel the copper layer from the substrate at a specific angle and speed.
- Tape Test: A qualitative method that involves applying a pressure-sensitive tape onto the copper surface and peeling it off to check for any copper residue on the tape.
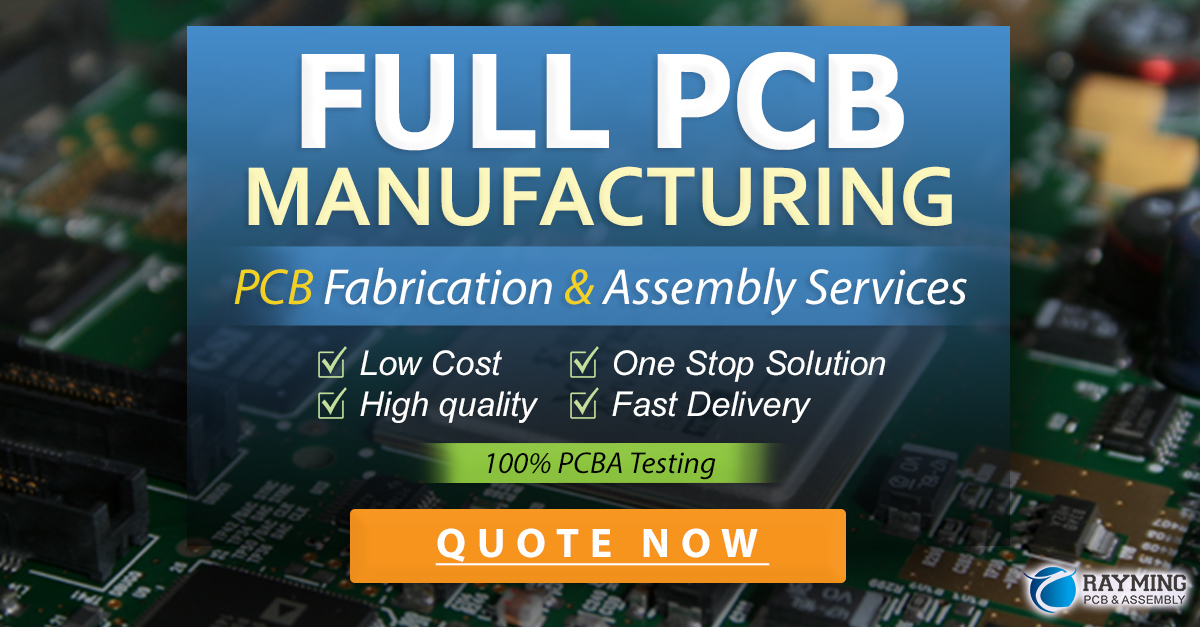
Applications of Copper Panels
Printed Circuit Boards (PCBs)
Copper panels are widely used in the manufacturing of printed circuit boards (PCBs). PCBs are the backbone of modern electronic devices, providing mechanical support and electrical connections for various components. The copper layer on the panel is etched into the desired circuit pattern, allowing for the flow of electrical signals between components.
High-Frequency Applications
Copper panels are also used in high-frequency applications, such as radar systems, wireless communications, and satellite technology. In these applications, the copper layer is designed to have specific geometric patterns and dimensions to achieve the desired electrical performance, such as impedance matching and signal propagation.
Power Electronics
Copper panels are used in power electronic devices, such as inverters, converters, and motor drives. In these applications, the copper layer is designed to have a high current carrying capacity and low electrical resistance to minimize power losses and heat generation. The copper layer is often combined with a heat sink or a cooling system to dissipate the generated heat effectively.
FAQ
What factors affect the copper distribution on a panel?
Several factors can affect the copper distribution on a panel, including:
- Manufacturing process parameters, such as lamination temperature, pressure, and duration.
- Copper foil quality, such as surface roughness, purity, and thickness uniformity.
- Substrate material properties, such as surface energy, thermal expansion coefficient, and moisture absorption.
- Etching process parameters, such as etchant concentration, temperature, and agitation.
How can I ensure a uniform copper distribution on a panel?
To ensure a uniform copper distribution on a panel, you can:
- Use high-quality copper foil with consistent thickness and surface properties.
- Optimize the lamination process parameters to achieve a strong and uniform bond between the copper and the substrate.
- Control the etching process parameters to minimize undercut and overetch.
- Implement strict quality control measures, such as visual inspection, thickness measurement, and electrical conductivity testing.
Can copper panels be recycled?
Yes, copper panels can be recycled. Copper is a valuable material that can be recovered and reused multiple times without losing its properties. The recycling process typically involves separating the copper from the substrate using mechanical or chemical methods and then melting and refining the copper for reuse in new applications.
What are the benefits of using copper panels in electronics?
Copper panels offer several benefits in electronic applications, including:
- High electrical conductivity, which allows for efficient signal transmission and power distribution.
- Excellent thermal conductivity, which helps in dissipating heat generated by electronic components.
- Good corrosion resistance, which ensures the long-term reliability of the electronic device.
- Ease of manufacturing, as copper can be readily etched and patterned using standard PCB fabrication processes.
How does the thickness of the copper layer affect the performance of the panel?
The thickness of the copper layer affects several performance aspects of the panel, such as:
- Current carrying capacity: Thicker copper layers can carry higher currents without overheating or experiencing voltage drops.
- Signal integrity: Thicker copper layers have lower electrical resistance and inductance, which helps in maintaining signal integrity, especially at high frequencies.
- Thermal management: Thicker copper layers have higher thermal conductivity, which helps in dissipating heat more effectively.
- Mechanical strength: Thicker copper layers provide better mechanical support and stability to the panel, especially in applications with high mechanical stress or vibration.
Conclusion
Copper distribution on a panel is a critical factor that determines its electrical, thermal, and mechanical performance. The manufacturing process of copper panels involves several steps, including substrate preparation, copper foil production, bonding, patterning, etching, and surface finishing. Various testing methods, such as visual inspection, thickness measurement, electrical conductivity test, and adhesion test, are used to ensure the quality and reliability of the copper distribution on the panel.
Copper panels find widespread applications in various industries, including electronics, telecommunications, and power systems. They are used in the manufacturing of printed circuit boards, high-frequency devices, and power electronic modules. The benefits of using copper panels include high electrical and thermal conductivity, good corrosion resistance, and ease of manufacturing.
As the demand for high-performance electronic devices continues to grow, the importance of copper distribution on a panel will only increase. Manufacturers and designers must pay close attention to the quality and consistency of the copper layer to ensure the optimal performance and reliability of their products. With the advancements in materials science and manufacturing technologies, we can expect to see further improvements in the copper distribution on panels, enabling the development of even more advanced and sophisticated electronic devices in the future.
Leave a Reply